
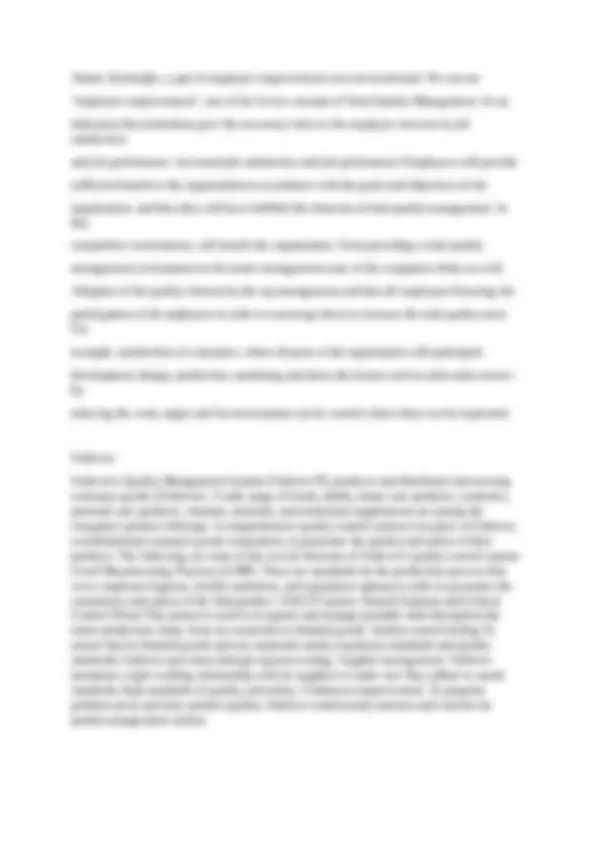
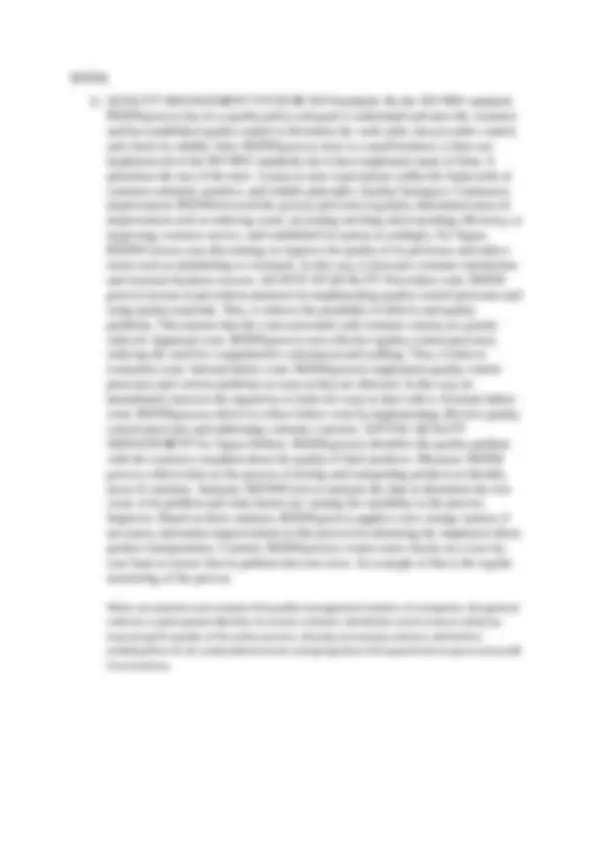
Study with the several resources on Docsity
Earn points by helping other students or get them with a premium plan
Prepare for your exams
Study with the several resources on Docsity
Earn points to download
Earn points by helping other students or get them with a premium plan
Community
Ask the community for help and clear up your study doubts
Discover the best universities in your country according to Docsity users
Free resources
Download our free guides on studying techniques, anxiety management strategies, and thesis advice from Docsity tutors
about marketing lecture note Introduction to Marketing: This section covers the basic definition of marketing, its role in business, and the importance of understanding customer needs and wants. Marketing Mix: The marketing mix consists of four key elements, also known as the 4Ps: Product, Price, Place, and Promotion. This section explains each component and how they work together to create a marketing strategy. Market Segmentation and Targeting: Here, students learn about dividing the market into distinct groups based on characteristics such as demographics, psychographics, and behavior. Targeting involves selecting specific segments to focus marketing efforts on. Consumer Behavior: This topic explores the psychological, social, and cultural factors that influence consumers' purchasing decisions. It covers concepts like perception, motivation, learning, and the decision-making process. Marketing Research: Students learn about the importance of gathering and analyzing data to make
Typology: Summaries
1 / 4
This page cannot be seen from the preview
Don't miss anything!
Quality management Quality control is very important. Quality control is the process of production, management, and continuous improvement of a product or service according to certain standards. It aims to increase customer satisfaction, improve production efficiency and ensure a competitive advantage for the business. Quality control includes the following key components:
that as company they are keen about the dresses that chefs used, they must have gloves and long shelves shirt in and something to cover their head in order to reduce the chance any unwanted issue to emerge. Ahmet Zeytinoğlu kindly provide us with the information that after they have done the service they provide the consumer with the they survey to fill out. In this survey the customer is asked to answer about the overall taste of the food and quality and the freshness of the food. Ahmet bey disclosed that. Turkey’s average satisfaction rate in the food industry is fluctuating around 60-65 percentage, however. According to the manager they have 80 percentage. Afterwards the manager also noted that they always try to finds way to enhance their current performance and to find the reasons why there is a 20-percentage gap. And if an issue is detected they will go back to the process phase to resolve the issue. Businesses are responsible for the costs they have to bear in order to produce quality products. They should take into account. Because ensuring the success of the enterprises in the competition, strong in the market Having advantages such as being in a position with the existence of Quality Cost System can be provided. Businesses applying the Quality Cost System to other businesses they will have the opportunity to stay in the market and have a larger market share we can say (Yumuk and Inan, 2005:178). with systematically measured quality costs both the revenue stream is accelerated and customer satisfaction is increased, making it stand out from the competition passable. (Salık, 2014:23) For quality management