
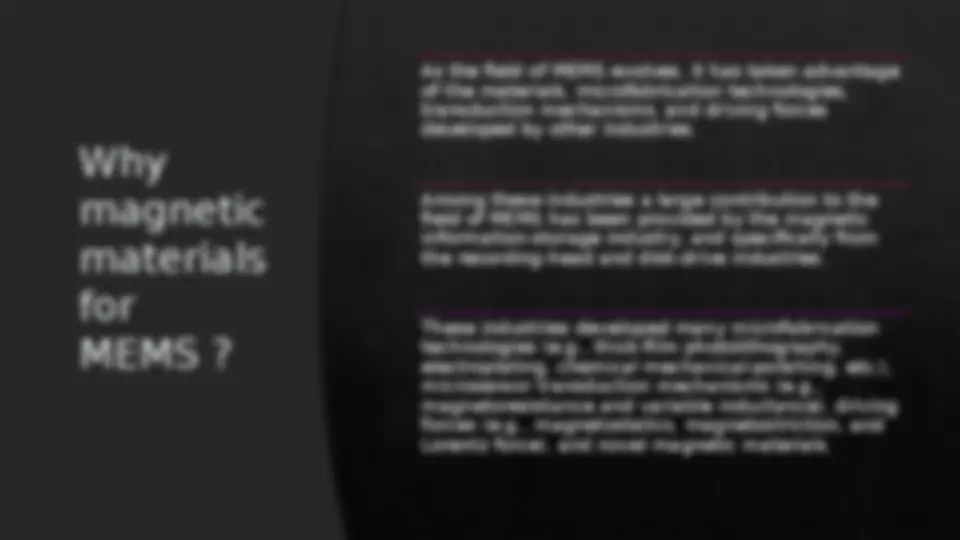
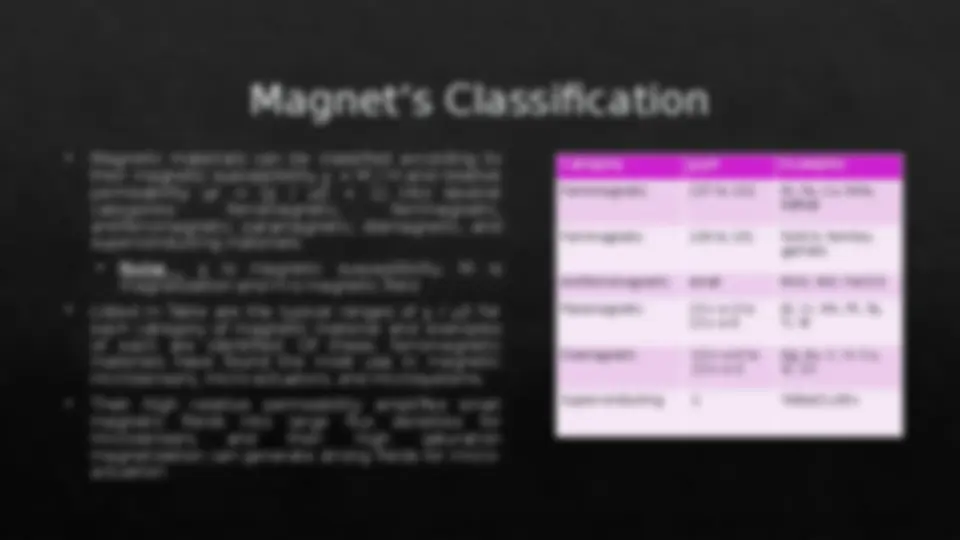
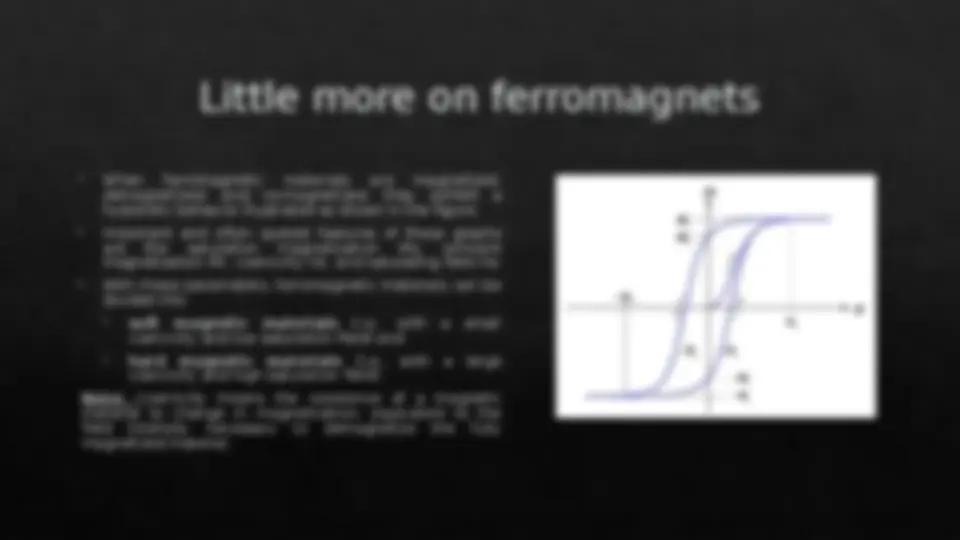
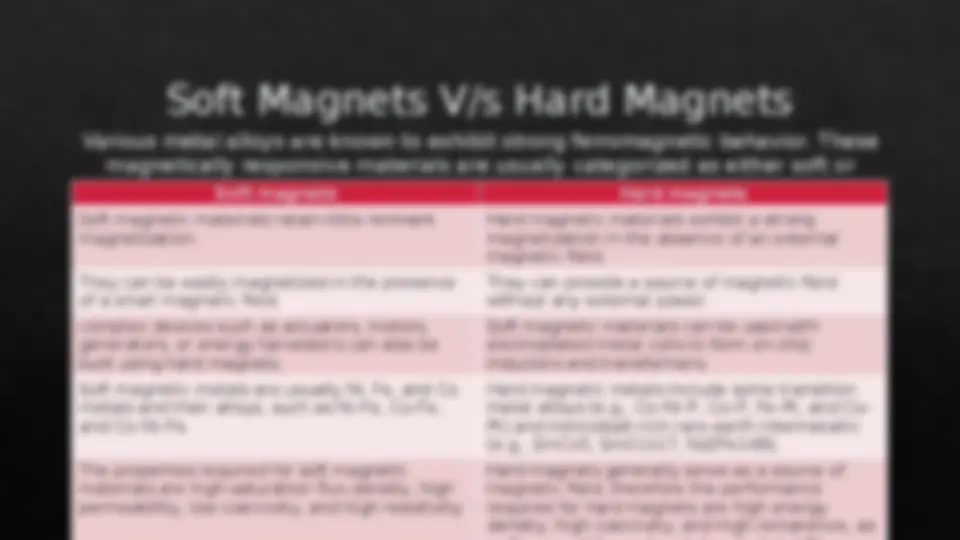
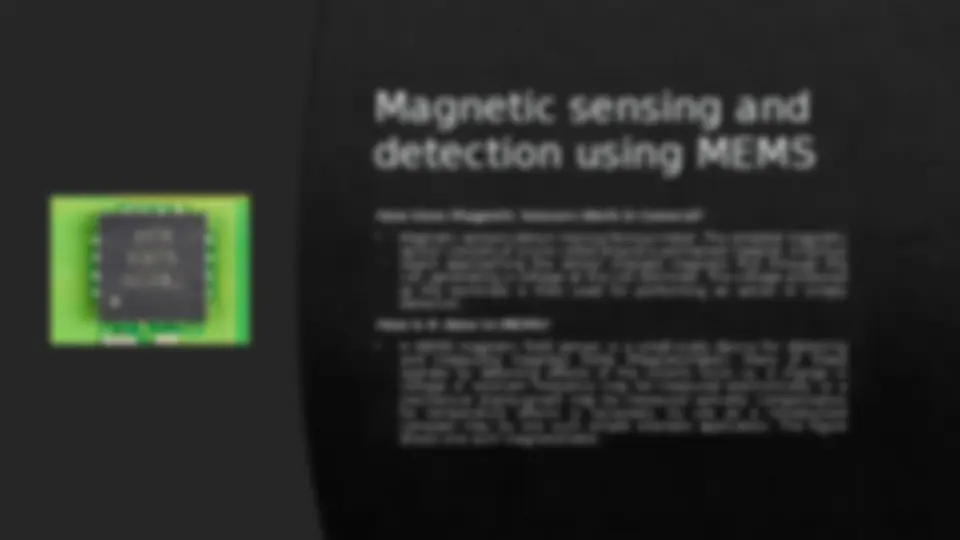
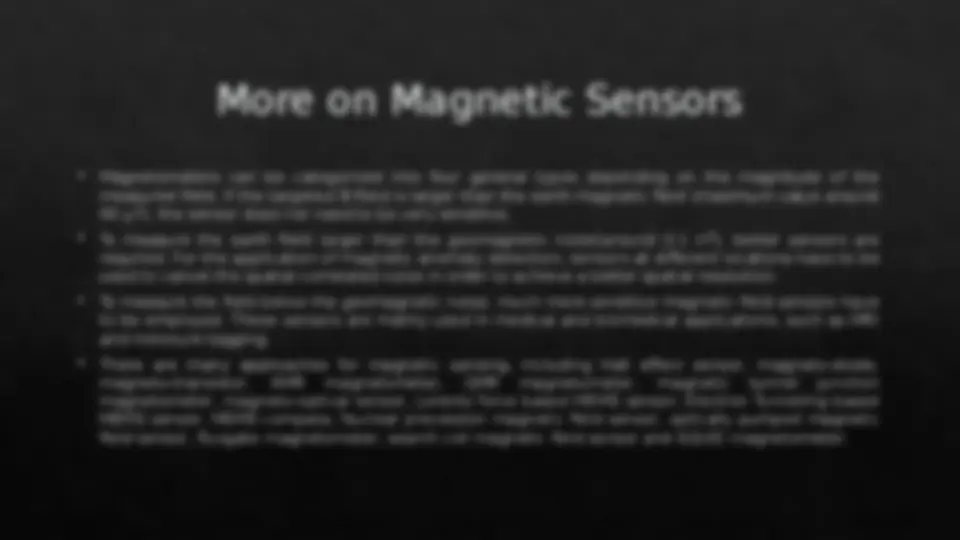
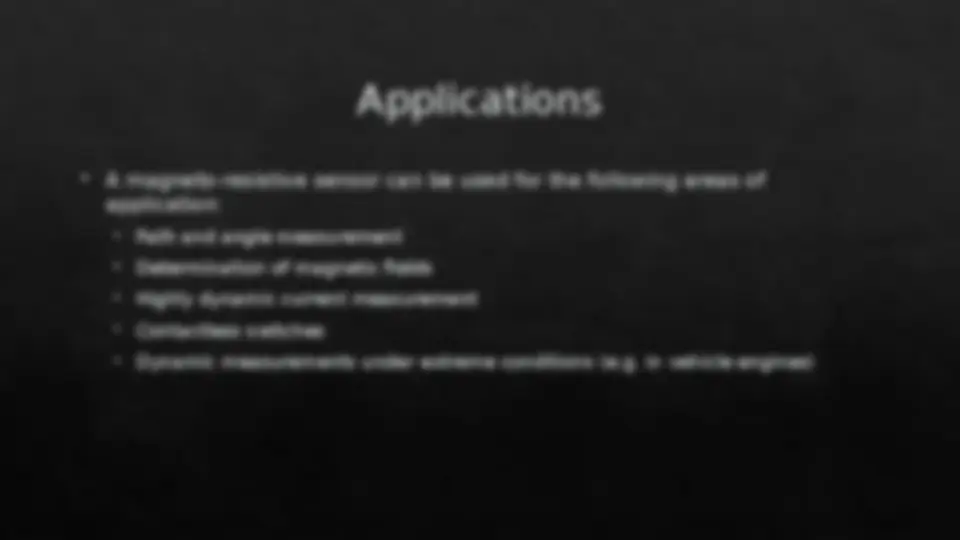
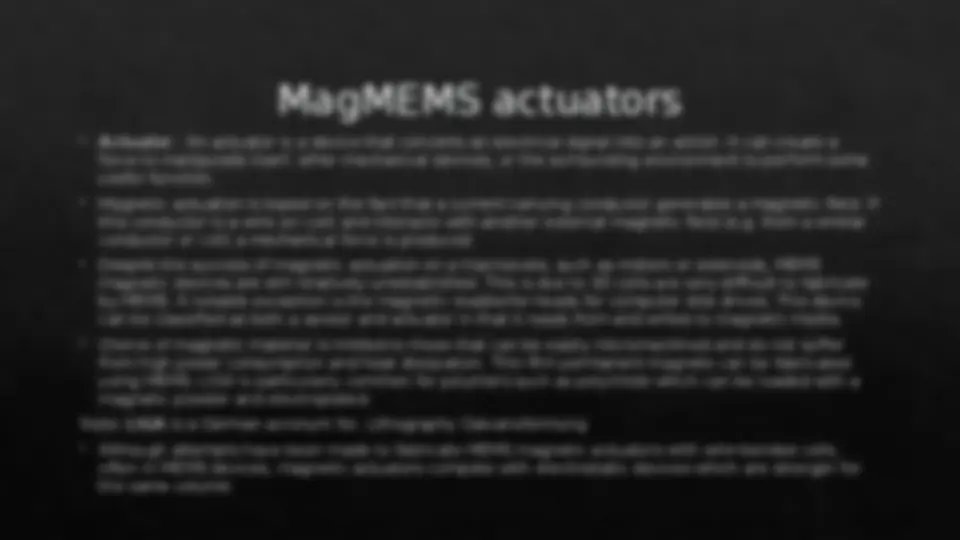
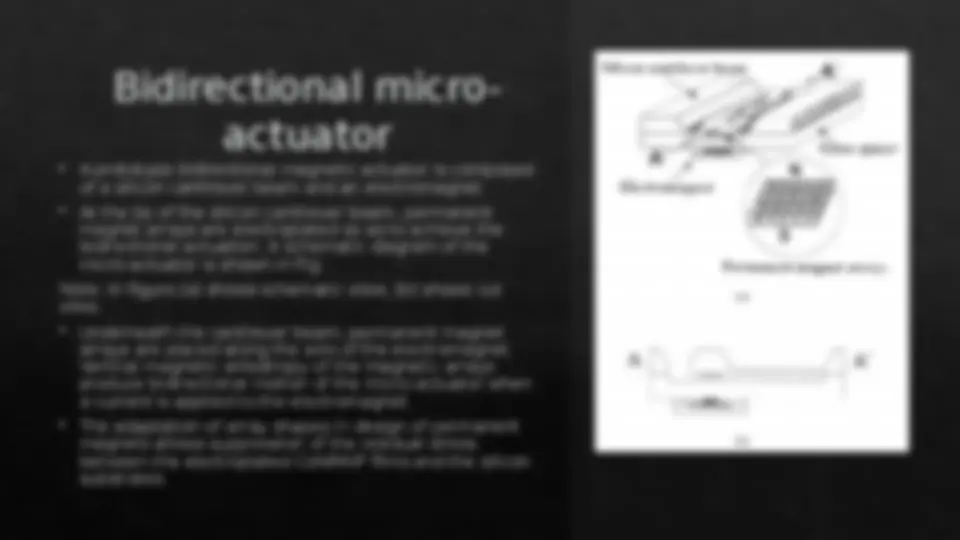
Study with the several resources on Docsity
Earn points by helping other students or get them with a premium plan
Prepare for your exams
Study with the several resources on Docsity
Earn points to download
Earn points by helping other students or get them with a premium plan
Community
Ask the community for help and clear up your study doubts
Discover the best universities in your country according to Docsity users
Free resources
Download our free guides on studying techniques, anxiety management strategies, and thesis advice from Docsity tutors
This presentation gives types of magnetic materials in MEMS and more information on the same.
Typology: Assignments
1 / 17
This page cannot be seen from the preview
Don't miss anything!
Briefing MEMSBriefing MEMS (^) MEMS stand for Micro Electronic Mechanical Systems (^) Micro mechatronics and microsystems constitute the technology of microscopic devices, particularly those with moving parts. (^) MEMS are made up of components between 1 and 100 micrometers in size (i.e., 0.001 to 0.1 mm), and MEMS devices generally range in size from 20 micrometers to a millimeter (i.e., 0.02 to 1.0 mm), although components arranged in arrays (e.g., digital micromirror devices) can be more than 1000 mm2. (^) They usually consist of a central unit that processes data (an integrated circuit chip such as microprocessor) and several components that interact with the surroundings (such as microsensors). (^) MEMS stand for Micro Electronic Mechanical Systems (^) Micro mechatronics and microsystems constitute the technology of microscopic devices, particularly those with moving parts. (^) MEMS are made up of components between 1 and 100 micrometers in size (i.e., 0.001 to 0.1 mm), and MEMS devices generally range in size from 20 micrometers to a millimeter (i.e., 0.02 to 1.0 mm), although components arranged in arrays (e.g., digital micromirror devices) can be more than 1000 mm2. (^) They usually consist of a central unit that processes data (an integrated circuit chip such as microprocessor) and several components that interact with the surroundings (such as microsensors).
Magnet’s ClassificationMagnet’s Classification (^) Magnetic materials can be classified according to their magnetic susceptibility χ = M / H and relative permeability μr = (χ / μ0 + 1) into several r = (χ / μr = (χ / μ0 + 1) into several 0 + 1) into several categories: ferromagnetic, ferrimagnetic, antiferromagnetic, paramagnetic, diamagnetic, and superconducting materials. (^) Note: χ is magnetic susceptibility, M is magnetization and H is magnetic field (^) Listed in Table are the typical ranges of χ / μr = (χ / μ0 + 1) into several 0 for each category of magnetic material and examples of each are identified. Of these, ferromagnetic materials have found the most use in magnetic microsensors, micro-actuators, and microsystems. (^) Their high relative permeability amplifies small magnetic fields into large flux densities for microsensors and their high saturation magnetization can generate strong fields for micro- actuation. (^) Magnetic materials can be classified according to their magnetic susceptibility χ = M / H and relative permeability μr = (χ / μ0 + 1) into several r = (χ / μr = (χ / μ0 + 1) into several 0 + 1) into several categories: ferromagnetic, ferrimagnetic, antiferromagnetic, paramagnetic, diamagnetic, and superconducting materials. (^) Note: χ is magnetic susceptibility, M is magnetization and H is magnetic field (^) Listed in Table are the typical ranges of χ / μr = (χ / μ0 + 1) into several 0 for each category of magnetic material and examples of each are identified. Of these, ferromagnetic materials have found the most use in magnetic microsensors, micro-actuators, and microsystems. (^) Their high relative permeability amplifies small magnetic fields into large flux densities for microsensors and their high saturation magnetization can generate strong fields for micro- actuation. Category χ/μ0 Examples Ferromagnetic 107 to 102 Ni, Fe, Co, NiFe, NdFeB Ferrimagnetic 104 to 101 Fe3O4, ferrites, garnets Antiferromagnetic small MnO, NiO, FeCO Paramagnetic 10 x e-3 to 10 x e- Al, Cr, Mn, Pt, Ta, Ti, W Diamagnetic -10 x e-6 to -10 x e- Ag, Au, C, H, Cu, Si, Zn Superconducting -1 YbBa2Cu3Ox
Little more on ferromagnetsLittle more on ferromagnets (^) When ferromagnetic materials are magnetized, demagnetized, and re-magnetized, they exhibit a hysteretic behavior illustrated as shown in the figure. (^) Important and often quoted features of these graphs are the saturation magnetization M s, remnant magnetization M r, coercivity H c, and saturating field H s. (^) With these parameters, ferromagnetic materials can be divided into (^) soft magnetic materials (i.e., with a small coercivity and low saturation field) and (^) hard magnetic materials (i.e., with a large coercivity and high saturation field). Note: Coercivity means the resistance of a magnetic material to change in magnetization, equivalent to the field intensity necessary to demagnetize the fully magnetized material. (^) When ferromagnetic materials are magnetized, demagnetized, and re-magnetized, they exhibit a hysteretic behavior illustrated as shown in the figure. (^) Important and often quoted features of these graphs are the saturation magnetization M s, remnant magnetization M r, coercivity H c, and saturating field H s. (^) With these parameters, ferromagnetic materials can be divided into (^) soft magnetic materials (i.e., with a small coercivity and low saturation field) and (^) hard magnetic materials (i.e., with a large coercivity and high saturation field). Note: Coercivity means the resistance of a magnetic material to change in magnetization, equivalent to the field intensity necessary to demagnetize the fully magnetized material.
(^) Although soft magnetic materials can be used to realize high-force actuators and sensitive magnetometers, hard magnetic or permanent magnetic materials would be more appropriate in some cases. (^) For example, hard magnetic materials with a high remnant magnetization M r can be conveniently used in bi-directional (push-pull) micro-actuators. (^) In addition, micro-actuators driven by off-chip coils could be activated with lower fields and hence lower power levels if a hard-magnetic material is used instead of a soft magnetic material. However, except for a few instances hard magnetic materials have not been used extensively in MEMS. (^) The primary reason for this has been the lack of readily available and reliable deposition and micromachining processes. Various hard magnetic materials can be prepared by metallurgical processes (e.g., sintering, pressure bonding, injection molding, casting, extruding, and calendaring), vacuum processes (e.g., evaporation, sputtering, MBE, CVD), and electrochemical processes (e.g., electroless deposition and electrodeposition). (^) Originally, most hard magnetic materials have been based on cobalt alloys because its hcp structure has a high crystal anisotropy. Thus far Co-based alloys with P, As, Sb, Bi, W, Cr, Mo, Pd, Pt, Ni, Fe, Cu, Mn, O and H have been deposited. Elements alloyed into Co tend to become concentrated at the grain boundaries. The result is isolated magnetic Co particles surrounded by non-magnetic or weakly magnetic boundaries (^) Such formations create microscopic energy barriers that increase the coercivity H c of the film, thereby making it magnetically harder. (^) Although soft magnetic materials can be used to realize high-force actuators and sensitive magnetometers, hard magnetic or permanent magnetic materials would be more appropriate in some cases. (^) For example, hard magnetic materials with a high remnant magnetization M r can be conveniently used in bi-directional (push-pull) micro-actuators. (^) In addition, micro-actuators driven by off-chip coils could be activated with lower fields and hence lower power levels if a hard-magnetic material is used instead of a soft magnetic material. However, except for a few instances hard magnetic materials have not been used extensively in MEMS. (^) The primary reason for this has been the lack of readily available and reliable deposition and micromachining processes. Various hard magnetic materials can be prepared by metallurgical processes (e.g., sintering, pressure bonding, injection molding, casting, extruding, and calendaring), vacuum processes (e.g., evaporation, sputtering, MBE, CVD), and electrochemical processes (e.g., electroless deposition and electrodeposition). (^) Originally, most hard magnetic materials have been based on cobalt alloys because its hcp structure has a high crystal anisotropy. Thus far Co-based alloys with P, As, Sb, Bi, W, Cr, Mo, Pd, Pt, Ni, Fe, Cu, Mn, O and H have been deposited. Elements alloyed into Co tend to become concentrated at the grain boundaries. The result is isolated magnetic Co particles surrounded by non-magnetic or weakly magnetic boundaries (^) Such formations create microscopic energy barriers that increase the coercivity H c of the film, thereby making it magnetically harder. Hard Magnetic Materials in MEMS Hard Magnetic Materials in MEMS
Soft Magnets V/s Hard MagnetsSoft Magnets V/s Hard Magnets Various metal alloys are known to exhibit strong ferromagnetic behavior. These magnetically responsive materials are usually categorized as either soft or hard magnets. Various metal alloys are known to exhibit strong ferromagnetic behavior. These magnetically responsive materials are usually categorized as either soft or Soft magnets^ hard magnets. Hard magnets Soft magnetic materials retain little remnant magnetization. Hard magnetic materials exhibit a strong magnetization in the absence of an external magnetic field. They can be easily magnetized in the presence of a small magnetic field. They can provide a source of magnetic field without any external power. complex devices such as actuators, motors, generators, or energy harvesters can also be built using hard magnets. Soft magnetic materials can be used with electroplated metal coils to form on-chip inductors and transformers. Soft magnetic metals are usually Ni, Fe, and Co metals and their alloys, such as Ni–Fe, Co–Fe, and Co–Ni–Fe. Hard magnetic metals include some transition metal alloys (e.g., Co–Ni–P, Co–P, Fe–Pt, and Co– Pt) and iron/cobalt-rich rare-earth intermetallic (e.g., SmCo5, Sm2Co17, Nd2Fe14B). The properties required for soft magnetic materials are high-saturation flux density, high permeability, low coercivity, and high resistivity. Hard magnets generally serve as a source of magnetic field, therefore the performance required for hard magnets are high energy density, high coercivity, and high remanence, as
More on Magnetic SensorsMore on Magnetic Sensors (^) Magnetometers can be categorized into four general types depending on the magnitude of the measured field. If the targeted B-field is larger than the earth magnetic field (maximum value around 60 μT), the sensor does not need to be very sensitive. (^) To measure the earth field larger than the geomagnetic noise(around 0.1 nT), better sensors are required. For the application of magnetic anomaly detection, sensors at different locations have to be used to cancel the spatial-correlated noise in order to achieve a better spatial resolution. (^) To measure the field below the geomagnetic noise, much more sensitive magnetic field sensors have to be employed. These sensors are mainly used in medical and biomedical applications, such as MRI and molecule tagging. (^) There are many approaches for magnetic sensing, including Hall effect sensor, magneto-diode, magneto-transistor, AMR magnetometer, GMR magnetometer, magnetic tunnel junction magnetometer, magneto-optical sensor, Lorentz force based MEMS sensor, Electron Tunneling based MEMS sensor, MEMS compass, Nuclear precession magnetic field sensor, optically pumped magnetic field sensor, fluxgate magnetometer, search coil magnetic field sensor and SQUID magnetometer. (^) Magnetometers can be categorized into four general types depending on the magnitude of the measured field. If the targeted B-field is larger than the earth magnetic field (maximum value around 60 μT), the sensor does not need to be very sensitive. (^) To measure the earth field larger than the geomagnetic noise(around 0.1 nT), better sensors are required. For the application of magnetic anomaly detection, sensors at different locations have to be used to cancel the spatial-correlated noise in order to achieve a better spatial resolution. (^) To measure the field below the geomagnetic noise, much more sensitive magnetic field sensors have to be employed. These sensors are mainly used in medical and biomedical applications, such as MRI and molecule tagging. (^) There are many approaches for magnetic sensing, including Hall effect sensor, magneto-diode, magneto-transistor, AMR magnetometer, GMR magnetometer, magnetic tunnel junction magnetometer, magneto-optical sensor, Lorentz force based MEMS sensor, Electron Tunneling based MEMS sensor, MEMS compass, Nuclear precession magnetic field sensor, optically pumped magnetic field sensor, fluxgate magnetometer, search coil magnetic field sensor and SQUID magnetometer.
Magneto-resistive sensor Magneto-resistive sensor
(^) A magneto-resistive sensor uses the fact that the electrical resistance in a ferromagnetic thin film alloy is changed through an external magnetic field. “Ferrum” is Latin and stands for “iron”. Generally, mixed alloys are used, for example iron and nickel. These sensors are exceptionally small, and due to their special material, they are robust and consume very little energy. They are especially useful in areas where there is no continuous energy supply.
(^) A magneto-resistive sensor uses the fact that the electrical resistance in a ferromagnetic thin film alloy is changed through an external magnetic field. “Ferrum” is Latin and stands for “iron”. Generally, mixed alloys are used, for example iron and nickel. These sensors are exceptionally small, and due to their special material, they are robust and consume very little energy. They are especially useful in areas where there is no continuous energy supply.
ApplicationsApplications (^) A magneto-resistive sensor can be used for the following areas of application:
(^) A magneto-resistive sensor can be used for the following areas of application:
MagMEMS actuatorsMagMEMS actuators (^) Actuator : An actuator is a device that converts an electrical signal into an action. It can create a force to manipulate itself, other mechanical devices, or the surrounding environment to perform some useful function. (^) Magnetic actuation is based on the fact that a current-carrying conductor generates a magnetic field. If this conductor is a wire (or coil) and interacts with another external magnetic field (e.g. from a similar conductor or coil) a mechanical force is produced. (^) Despite the success of magnetic actuation on a macroscale, such as motors or solenoids, MEMS magnetic devices are still relatively unestablished. This is due to 3D coils are very difficult to fabricate by MEMS. A notable exception is the magnetic read/write heads for computer disk drives. This device can be classified as both a sensor and actuator in that it reads from and writes to magnetic media. (^) Choice of magnetic material is limited to those that can be easily micromachined and do not suffer from high power consumption and heat dissipation. Thin film permanent magnets can be fabricated using MEMS; LIGA is particularly common for polymers such as polyimide which can be loaded with a magnetic powder and electroplated. Note: LIGA is a German acronym for, Lithography Galvanoformung (^) Although attempts have been made to fabricate MEMS magnetic actuators with wire-bonded coils, often in MEMS devices, magnetic actuators compete with electrostatic devices which are stronger for the same volume. (^) Actuator : An actuator is a device that converts an electrical signal into an action. It can create a force to manipulate itself, other mechanical devices, or the surrounding environment to perform some useful function. (^) Magnetic actuation is based on the fact that a current-carrying conductor generates a magnetic field. If this conductor is a wire (or coil) and interacts with another external magnetic field (e.g. from a similar conductor or coil) a mechanical force is produced. (^) Despite the success of magnetic actuation on a macroscale, such as motors or solenoids, MEMS magnetic devices are still relatively unestablished. This is due to 3D coils are very difficult to fabricate by MEMS. A notable exception is the magnetic read/write heads for computer disk drives. This device can be classified as both a sensor and actuator in that it reads from and writes to magnetic media. (^) Choice of magnetic material is limited to those that can be easily micromachined and do not suffer from high power consumption and heat dissipation. Thin film permanent magnets can be fabricated using MEMS; LIGA is particularly common for polymers such as polyimide which can be loaded with a magnetic powder and electroplated. Note: LIGA is a German acronym for, Lithography Galvanoformung (^) Although attempts have been made to fabricate MEMS magnetic actuators with wire-bonded coils, often in MEMS devices, magnetic actuators compete with electrostatic devices which are stronger for the same volume.
(^) Various array shapes were investigated to understand the geometric effects on the magnetic properties. In designing the arrays, geometric aspect ratio was used as a measure of the geometric effect of magnetic properties, which is proportional to demagnetizing factor in those arrays. (^) Aspect ratio is defined by the ratio between the longest dimension and the shortest dimension in an individual cell, where the number is calculated as width divided by thickness in those arrays. Various geometries were investigated to understand the effect of array shape on the magnetic properties of permanent magnet components electroplated on the silicon substrate. (^) Figure shows the designed schematic geometry of magnet arrays. To prevent the deformation over the cantilever beam due to the electroplated magnets in beam structure, an island shape of silicon overhang was adopted at the tip of cantilever beam. (^) A commercially available surface mountable planar inductor (Coil-craft, LPO2506OB-105, 1000 μH) was modified and integrated on the glass spacer as electromagnet. The electromagnet consists of a circular ferrite core (diameter 2 mm) and a copper coil (number of turns 185). The saturation current is 100 mA and its dc resistance is 14.2 Ω. (^) Various array shapes were investigated to understand the geometric effects on the magnetic properties. In designing the arrays, geometric aspect ratio was used as a measure of the geometric effect of magnetic properties, which is proportional to demagnetizing factor in those arrays. (^) Aspect ratio is defined by the ratio between the longest dimension and the shortest dimension in an individual cell, where the number is calculated as width divided by thickness in those arrays. Various geometries were investigated to understand the effect of array shape on the magnetic properties of permanent magnet components electroplated on the silicon substrate. (^) Figure shows the designed schematic geometry of magnet arrays. To prevent the deformation over the cantilever beam due to the electroplated magnets in beam structure, an island shape of silicon overhang was adopted at the tip of cantilever beam. (^) A commercially available surface mountable planar inductor (Coil-craft, LPO2506OB-105, 1000 μH) was modified and integrated on the glass spacer as electromagnet. The electromagnet consists of a circular ferrite core (diameter 2 mm) and a copper coil (number of turns 185). The saturation current is 100 mA and its dc resistance is 14.2 Ω.