
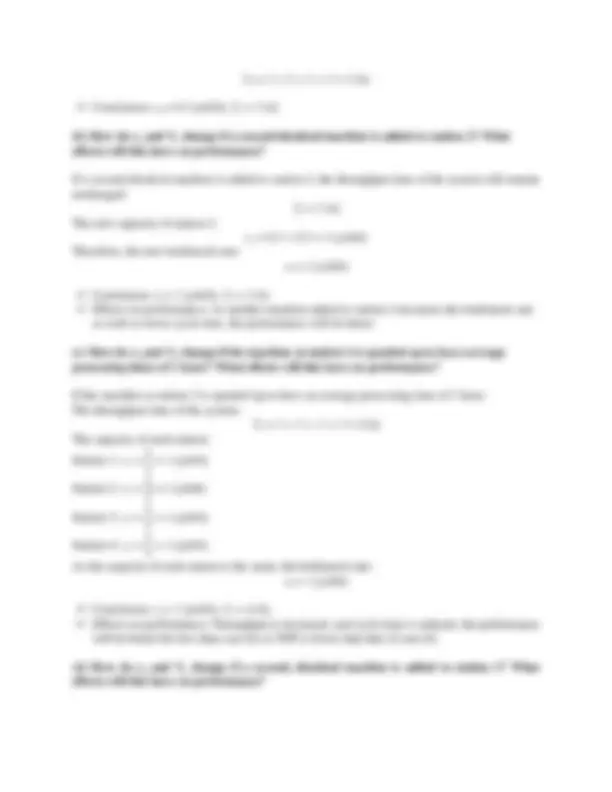
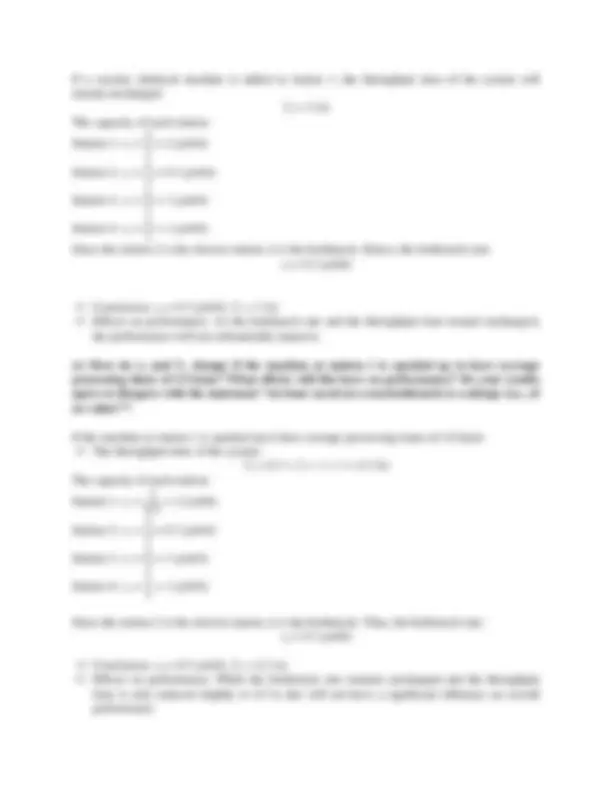
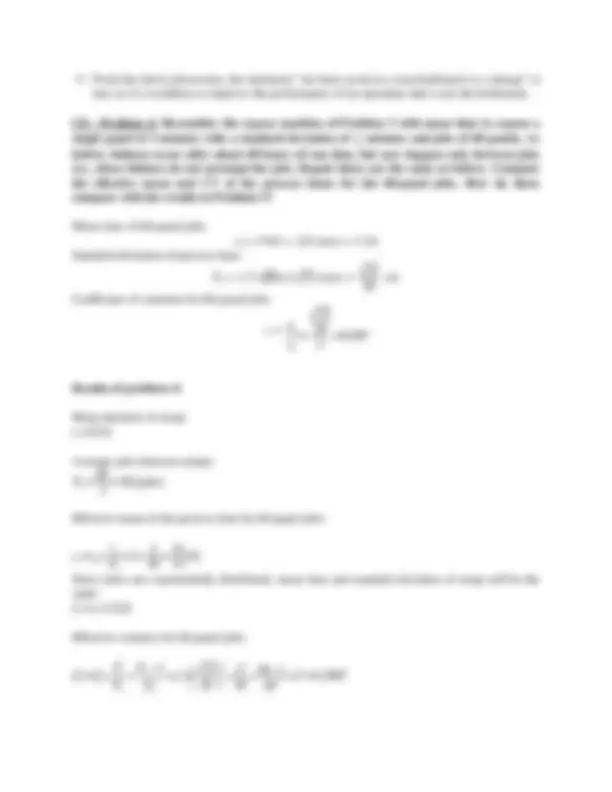
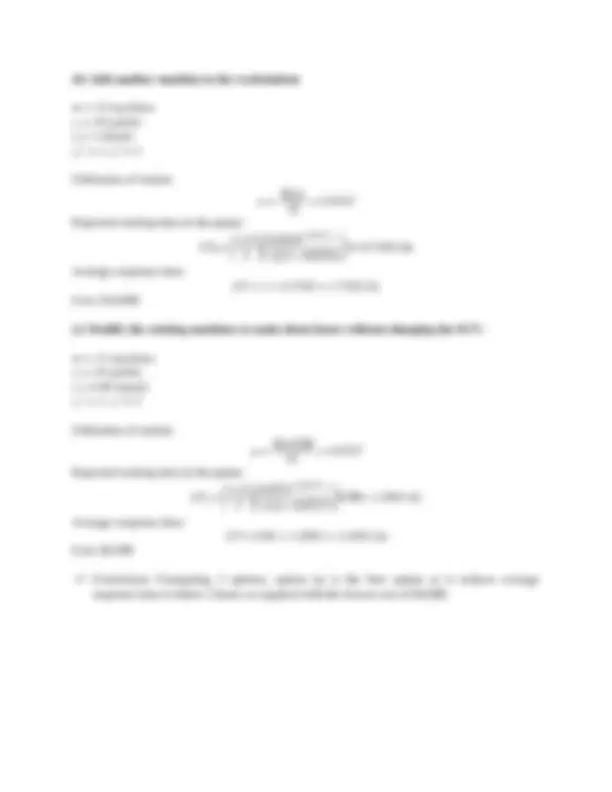
Study with the several resources on Docsity
Earn points by helping other students or get them with a premium plan
Prepare for your exams
Study with the several resources on Docsity
Earn points to download
Earn points by helping other students or get them with a premium plan
Community
Ask the community for help and clear up your study doubts
Discover the best universities in your country according to Docsity users
Free resources
Download our free guides on studying techniques, anxiety management strategies, and thesis advice from Docsity tutors
Questions and Answers for Problem 3 & 5 of Chapter 7 and Problem 4 & 9 of Chapter 8 in Factory Physics Textbook
Typology: Exercises
1 / 8
This page cannot be seen from the preview
Don't miss anything!
On special offer
Full Name: Thi Huong Giang Cao Student ID: 7959979 HW
C7 – Problem 3: A powder metal (PM) manufacturing line produces bushings in three steps, compaction, sinter-harden, and rough/finish turn, which are accomplished at three single-machine stations with average processing times of 12, 10, and 6 minutes, respectively. However, while compaction and sinter-harden are dedicated to the bushing line, the rough/finish turn station also processes bearings from another line; the average processing times for bearings are 14 minutes.
(a) If the production volumes of bushings and bearings are the same, what is the bottleneck of the PM line?
Since the first 2 stations are dedicated to only the bushing line, the cycle times of the compaction and sinter-harden stations: t 1 = 12 (min) t 2 = 10 (min) Bearing time: tb = 14 (min) As the third station also processes bearings from another line, cycle time of the rough/finish turn station: t 3 = 6 + 14 = 20 (min) Conclusion: As the rough/finish turn station has the longest processing time, it is the bottleneck of the PM line.
(b) If the volume of bearings is 1/2 that of bushings, what is the bottleneck of the PM line?
If the volume of bearings is 1/2 that of bushings, the bearing time also decreases to half, so:
tb =
= 7 (min)
Now, the cycle time of each station: t 1 = 12 (min) t 2 = 10 (min) t 3 = 6 + 7 = 13 (min) Conclusion: As the rough/finish turn station has the longest processing time, it is still the bottleneck of the PM line.
(c) If the volume of bearings is 1/3 that of bushings, what is the bottleneck of the PM line?
If the volume of bearings is 1/3 that of bushings, the bearing time also decreases to one-third, so:
tb =
= 4.67 (min)
Now, the cycle time of each station: t 1 = 12 (min) t 2 = 10 (min) t 3 = 6 + 4.67 = 10.67 (min) Conclusion: As the compaction station is the slowest station, it is now the bottleneck of the PM line. (d) If you had to pick one process for the bottleneck, which one would it be?
If the third station is dedicated to only the bushing line, the cycle time of each station: t 1 = 12 (min) t 2 = 10 (min) t 3 = 6 (min) Conclusion: If I had to pick one process for the bottleneck, it would be the first station (compaction) station as it is the slowest station among the three stations.
C7 – Problem 5: Consider a four-station line in which all stations consist of single machines. Station 2 has average processing times of 2 hours per job, while the remaining stations have average processing times of 1 hour per job. Answer the following, under the assumption that process times are deterministic (as in the best case)
The average processing time of each station: Station 1: t 1 = 1 (h) Station 2: t 2 = 2 (h) Station 3: t 3 = 1 (h) Station 4: t 4 = 1 (h)
(a) What are rb and To for this line?
To calculate the capacity of each station:
Capacity = Number of machines Processing time So, the capacity of each station:
Station 1: r 1 =
= 1 (job/h)
Station 2: r 2 =
= 0.5 (job/h)
Station 3: r 3 =
= 1 (job/h)
Station 4: r 4 =
= 1 (job/h)
Since the bottleneck rate of the production line is equal to the lowest capacity among all the stations: rb = 0.5 (job/h) As throughput time is equal to sum of processing times of all stations:
If a second, identical machine is added to station 1, the throughput time of the system will remain unchanged: To = 5 (h) The capacity of each station:
Station 1: r 1 =
= 2 (job/h)
Station 2: r 2 =
= 0.5 (job/h)
Station 3: r 3 =
= 1 (job/h)
Station 4: r 4 =
= 1 (job/h)
Since the station 2 is the slowest station, it is the bottleneck. Hence, the bottleneck rate: rb = 0.5 (job/h)
Conclusion: rb = 0.5 (job/h), To = 5 (h) Effects on performance: As the bottleneck rate and the throughput time remain unchanged, the performance will not substantially improve.
(e) How do rb and To change if the machine at station 1 is speeded up to have average processing times of 1/2 hour? What effects will this have on performance? Do your results agree or disagree with the statement “An hour saved at a non-bottleneck is a mirage (i.e., of no value)”?
If the machine at station 1 is speeded up to have average processing times of 1/2 hour: The throughput time of the system: To = 0.5 + 2 + 1 + 1 = 4.5 (h) The capacity of each station:
Station 1: r 1 =
= 2 (job/h)
Station 2: r 2 =
= 0.5 (job/h)
Station 3: r 3 =
= 1 (job/h)
Station 4: r 4 =
= 1 (job/h)
Since the station 2 is the slowest station, it is the bottleneck. Thus, the bottleneck rate: rb = 0.5 (job/h)
Conclusion: rb = (0.5 job/h), To = 4.5 (h) Effects on performance: While the bottleneck rate remains unchanged and the throughput time is only reduced slightly to 4.5 h, this will not have a significant influence on overall performance.
From the above discussion, the statement “An hour saved at a non-bottleneck is a mirage” is true as it is worthless to improve the performance of an operation that is not the bottleneck.
C8 – Problem 4: Reconsider the expose machine of Problem 3 with mean time to expose a single panel of 2 minutes with a standard deviation of (^) 121 minutes and jobs of 60 panels. As
before, failures occur after about 60 hours of run time, but now happen only between jobs (i.e., these failures do not preempt the job). Repair times are the same as before. Compute the effective mean and CV of the process times for the 60-panel jobs. How do these compare with the results in Problem 3?
Mean time of 60-panel jobs: t 0 = 2*60 = 120 (min) = 2 (h) Standard deviation of process time:
(h)
Coefficient of variation for 60-panel jobs:
co = ∂ 0 t 0
Results of problem 4:
Mean duration of setup: ts = 2 ( h )
Average jobs between setups:
Ns =
= 30 ( jobs )
Effective mean of the process time for 60-panel jobs:
te = t 0 +
ts Ns
( h )
Since times are exponentially distributed, mean time and standard deviation of setup will be the same: ∂s = ts = 2 ( h )
Effective variance for 60-panel jobs:
∂e^2 = ∂ 02 +
∂s^2 N (^) s
Ns − 1 N^2 s^
∗ t^2 s^ =( √^15 20 )
2
2 30
To calculate the expected waiting time in the queue:
ca^2 + ce^2
u √^2 ( m^ +^1 )−^1
te with u =
r (^) a t (^) e m
To calculate the average response time: CT = CTq + te
Current situation:
m = 11 machines ra = 10 (job/h) te = 1 (h/job) ca^2 = 1, ce^2 = 5
Utilization of station:
u =
Expected waiting time in the queue:
1 = 2.0692 (h)
Average response time:
CT = 1 + 2.0692 = 3.0692 (h)
(a) Perform more preventive maintenance:
m = 11 machines ra = 10 (job/h) te = 1 (h/job) ca^2 = 1, ce^2 = 1
Utilization of station:
u =
Expected waiting time in the queue:
1 = 0.6897 (h)
Average response time:
CT = 1 + 0.6897 = 1.6897 (h) Cost: $8,
(b) Add another machine to the workstation:
m = 12 machines ra = 10 (job/h) te = 1 (h/job) ca^2 = 1, ce^2 = 5
Utilization of station:
u =
Expected waiting time in the queue:
1 = 0.7102 (h)
Average response time: CT = 1 + 0.7102 = 1.7102 (h) Cost: $10,
(c) Modify the existing machines to make them faster without changing the SCV:
m = 11 machines ra = 10 (job/h) te = 0.96 (h/job) ca^2 = 1, ce^2 = 5
Utilization of station:
u =
Expected waiting time in the queue:
0.96= 1.2095 (h)
Average response time: CT = 0.96 + 1.2095 = 2.1695 (h) Cost: $8,
Conclusion: Comparing 3 options, option (a) is the best option as it reduces average response time to below 2 hours as required with the lowest cost of $8,000.