
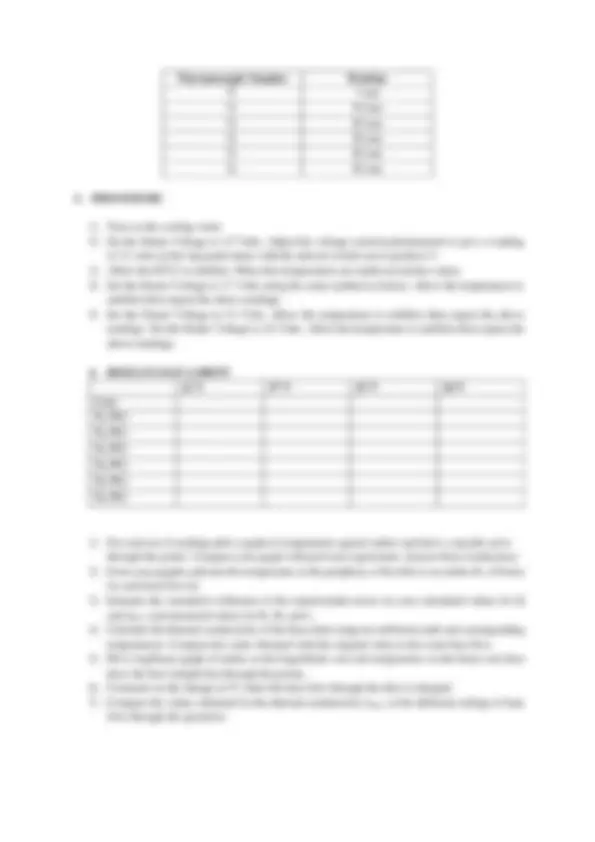
Study with the several resources on Docsity
Earn points by helping other students or get them with a premium plan
Prepare for your exams
Study with the several resources on Docsity
Earn points to download
Earn points by helping other students or get them with a premium plan
Community
Ask the community for help and clear up your study doubts
Discover the best universities in your country according to Docsity users
Free resources
Download our free guides on studying techniques, anxiety management strategies, and thesis advice from Docsity tutors
laboratory documents of heat transfer
Typology: Schemes and Mind Maps
1 / 3
This page cannot be seen from the preview
Don't miss anything!
Experiment 3: Radial Heat Conduction
Nomenclature for Experiment 3
Name Symbol SI unit
Inner radius of disk Ri m Outer radius of disk Ro m Radius from center of the disk to thermocouple Ra ( i.e. R 1 ) m Thickness of disk (distance) x m Voltage of heating element V V Current of heating element I A Electrical power to heating element Q W Heat transfer rate per unit time(heat flow) Q W Measured temperature Ta ( i.e. T 1 ) ⁰C Thermal conductivity K W/(m⁰C) Flow rate of cooling water Fw l/min Time T sec
To measure the temperature distribution for steady state conduction of energy through the wall of a cylinder (radial energy flow) and demonstrate the effect of a change in heat flow. To understand the use of the Fourier Rate Equation in determining the rate of heat flow for steady-state conduction of energy through the wall of a cylinder (radial energy flow). To determine the constant of proportionality (the thermal conductivity k) of the disk material.
When the inner and outer surfaces of a thick walled cylinder are each at a different uniform temperature, heat flows radially through the cylinder wall. The disk can be considered to be constructed as a series of successive layers. From continuity considerations the radial heat flow through each of the successive layers in the wall must be constant if the flow is steady but since the area of the successive layers increases with radius, the temperature gradient must decrease with radius.
Fig.1 Horizontal Cross Section of the Heated Disk
2.1.a Heated Disk The disk is manufactured from brass 3.2 mm thick and 110 mm diameter with a central copper core 14 mm diameter. The thermal conductivity of the Brass disk is approximately 125 W/m°C at the typical operating temperatures in the experiment set. 2.1.b Cooling Coil The periphery of the disk is cooled by cold water flowing through a copper tube which is attached to the circumference of the disk. 2.1.c Thermocouples Six type K thermocouples are positioned at different radii in the heated disk to indicate the temperature gradient from the central heated core to the cooled periphery of the disk. Each thermocouple is located in a hole with the thermocouple bead on the centerline of the disk. The thermocouples are positioned on a tangent to the central heated core to minimize the disturbance to the heat flow between the thermocouples. Thermocouple positions are listed below: