
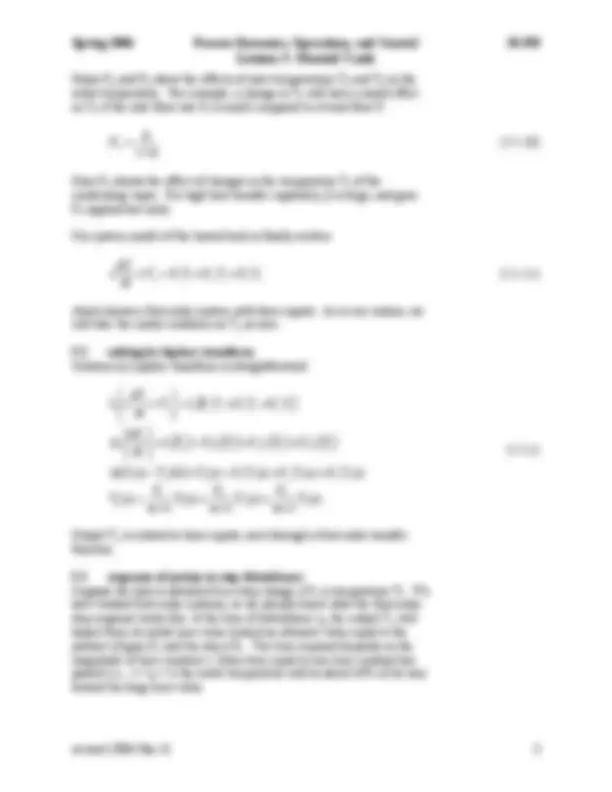
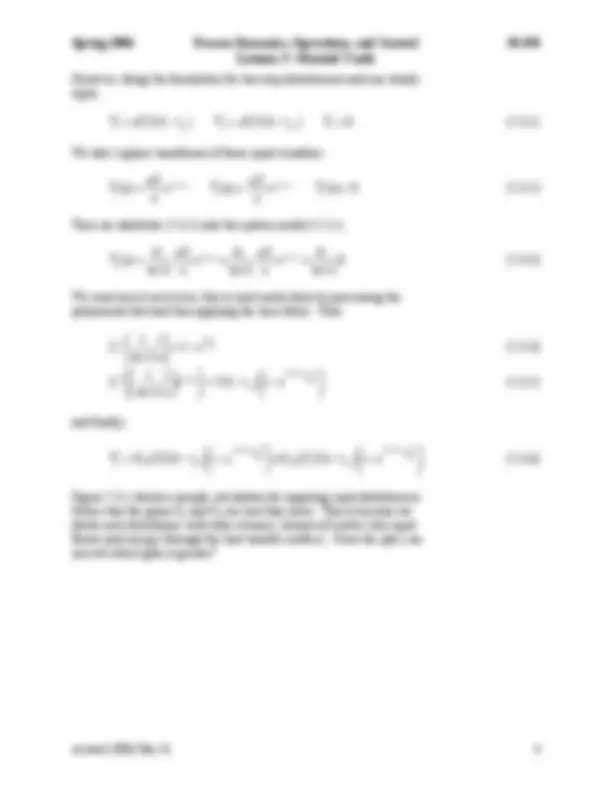
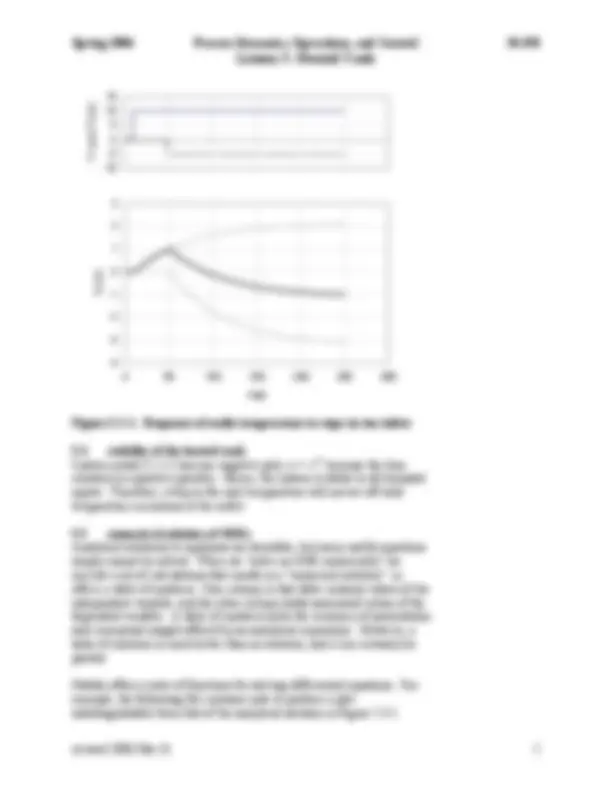
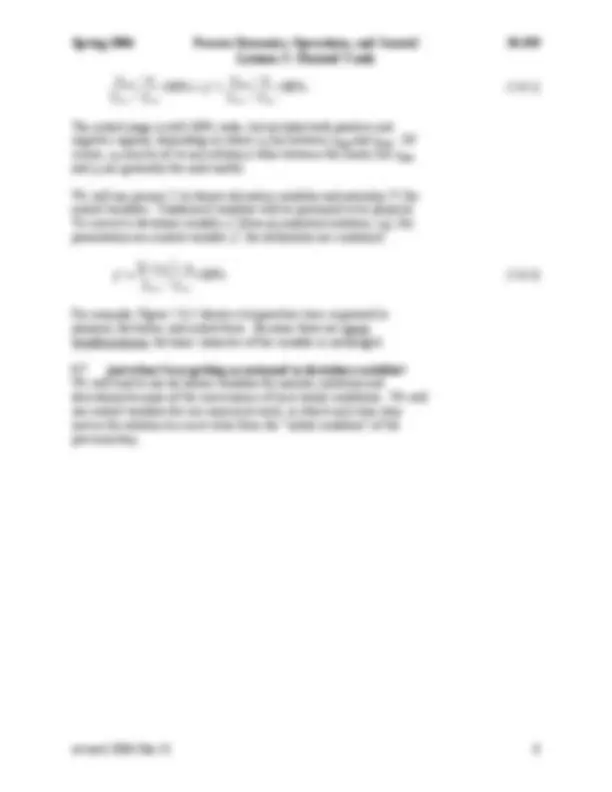
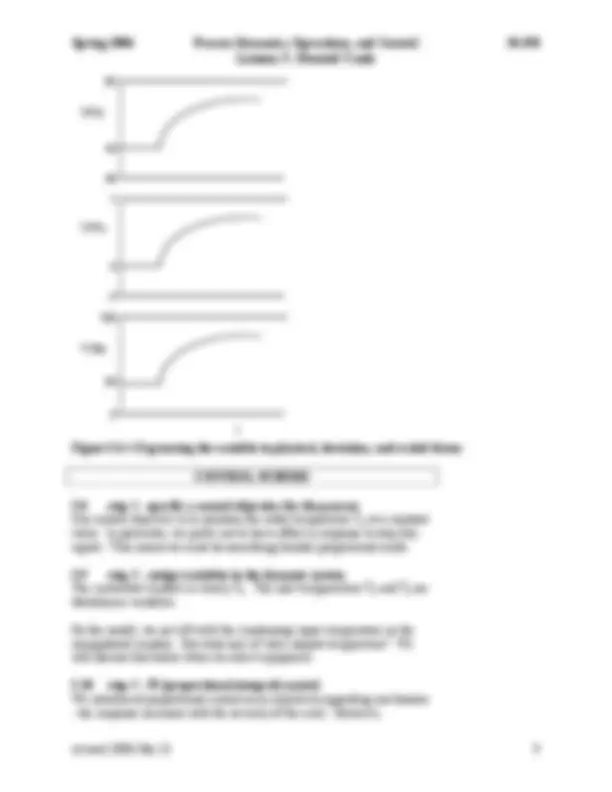
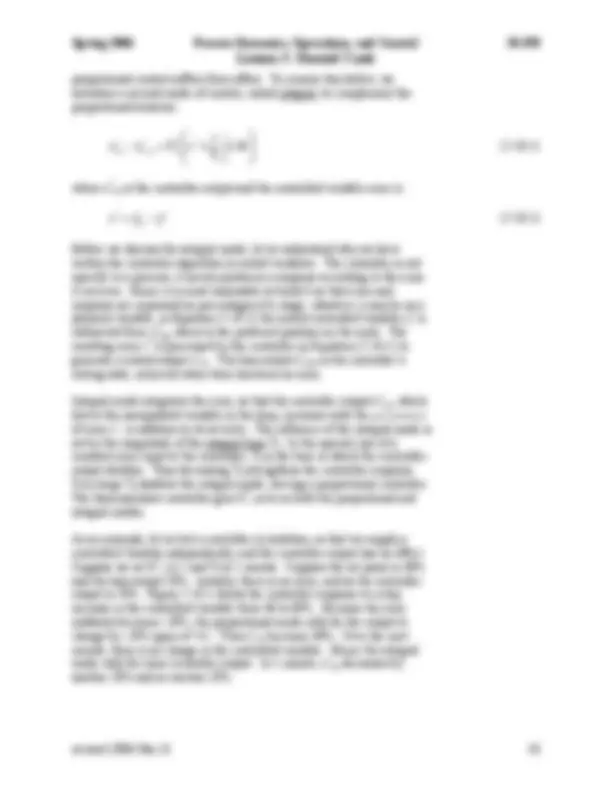
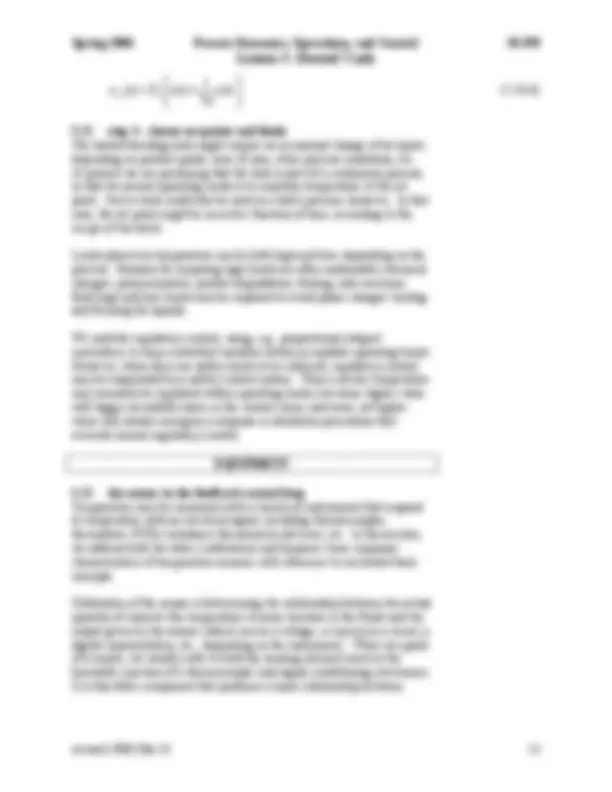
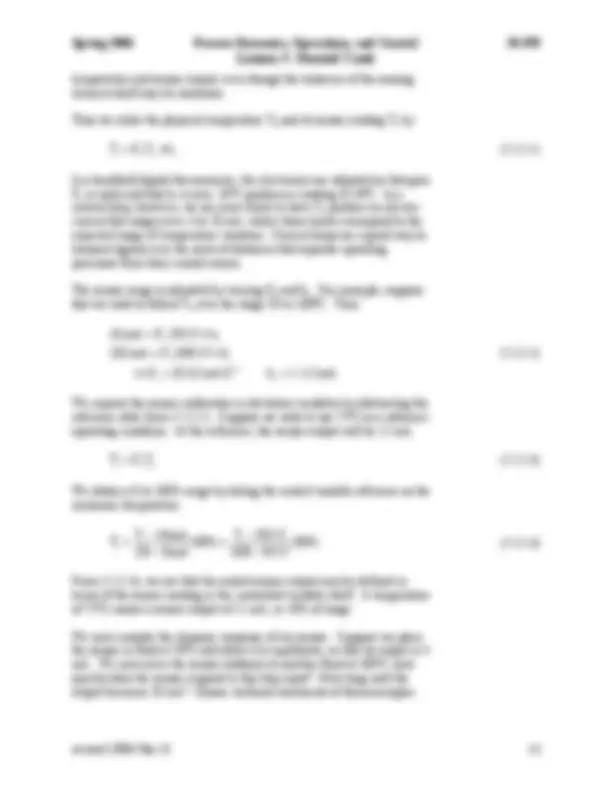
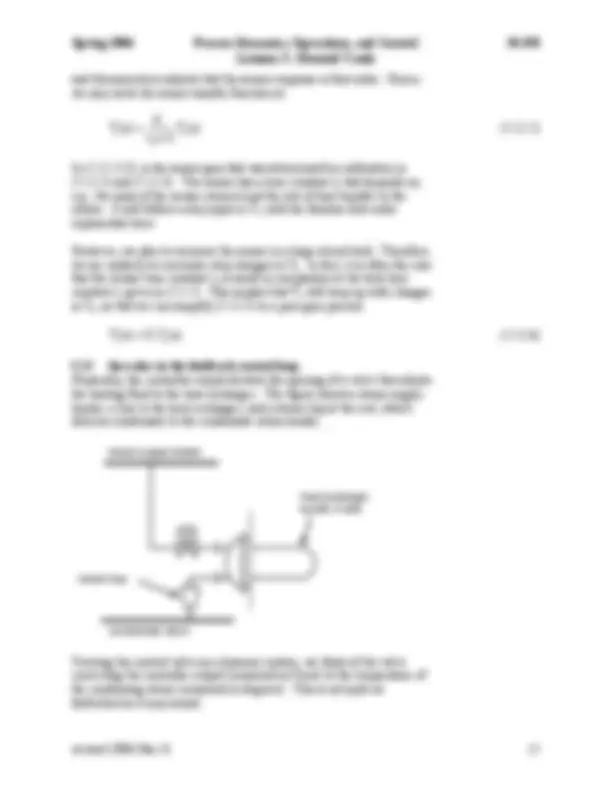
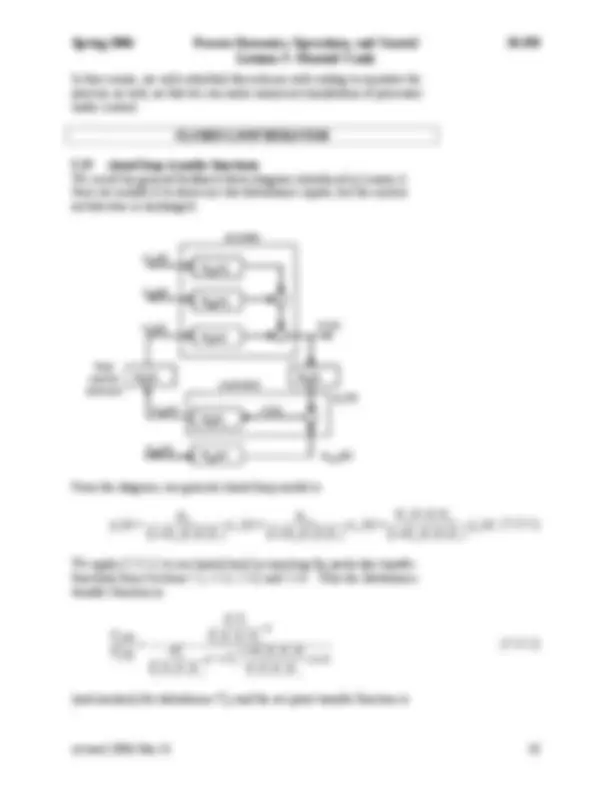
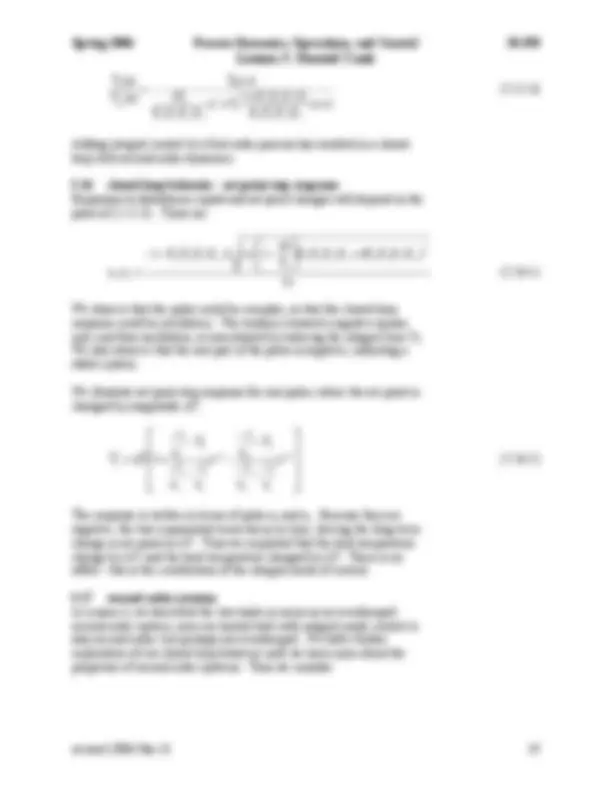
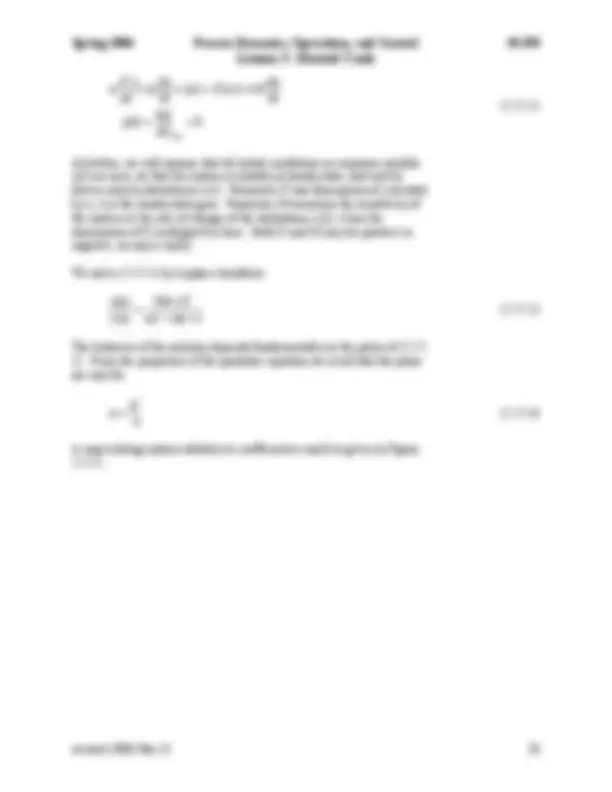
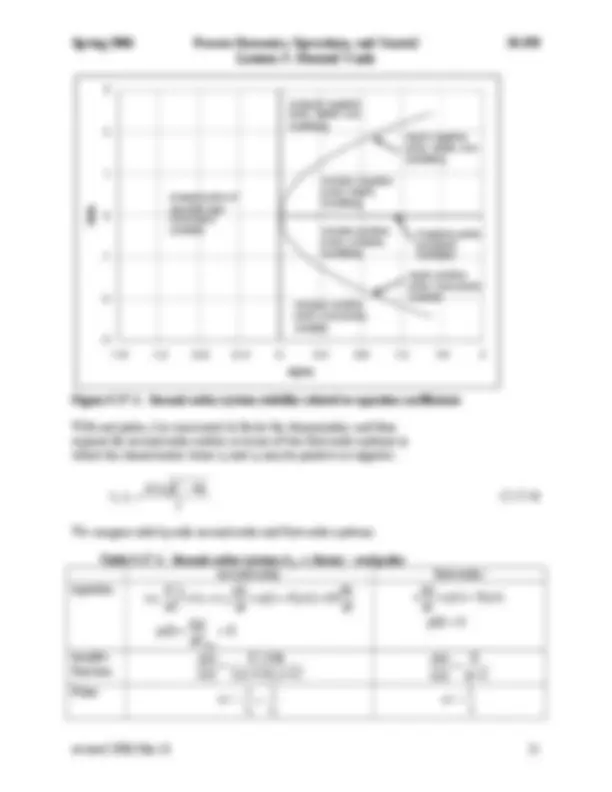
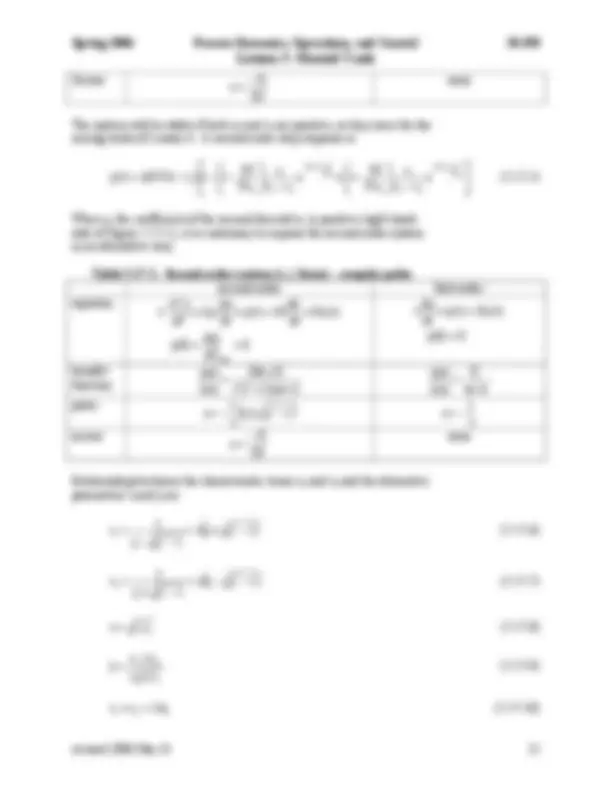
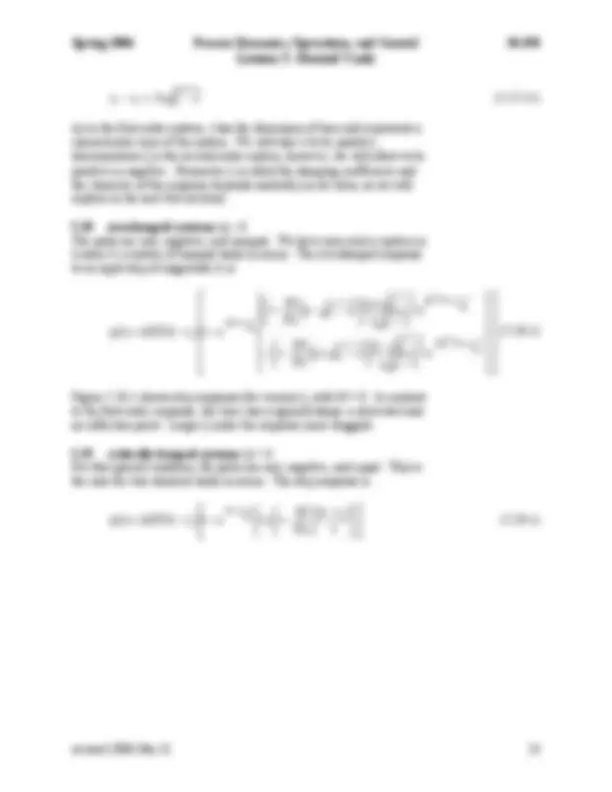
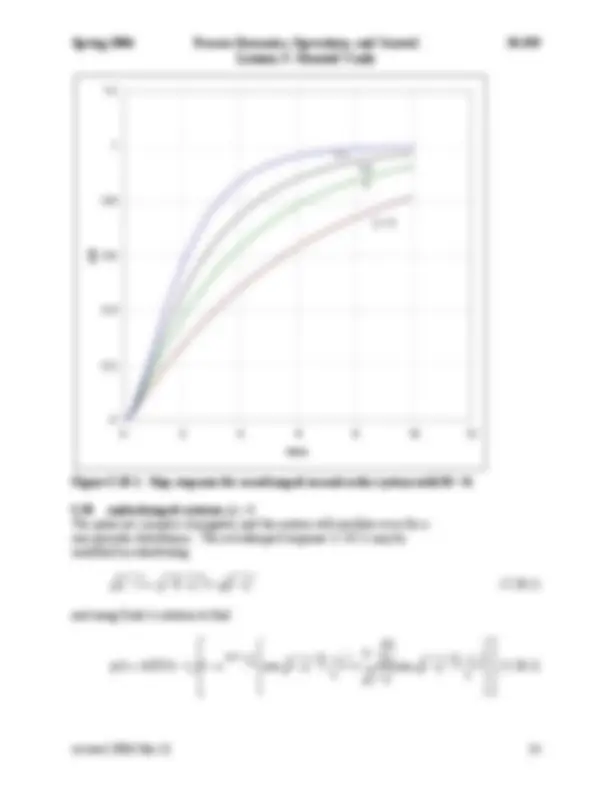
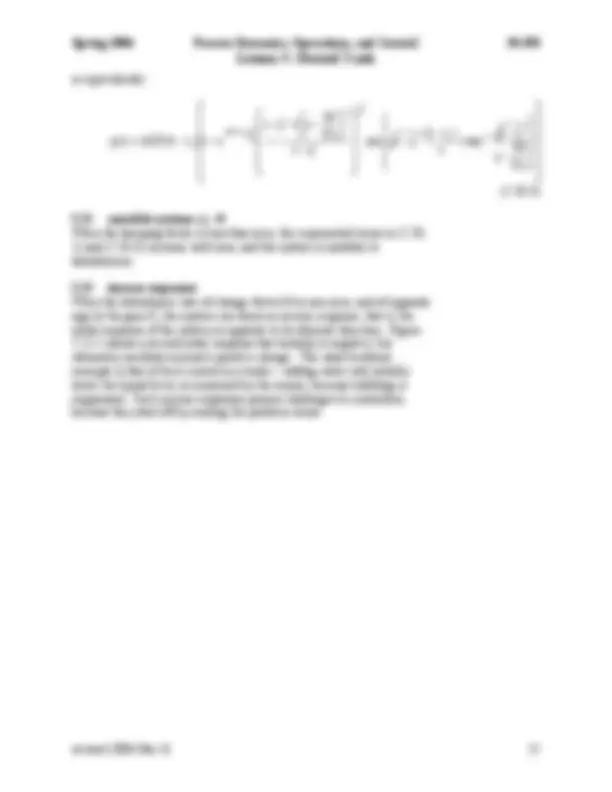
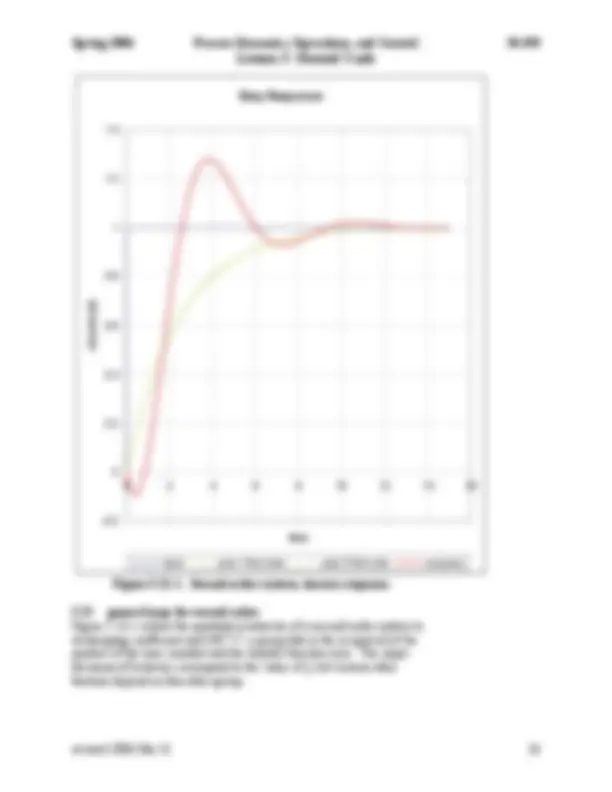
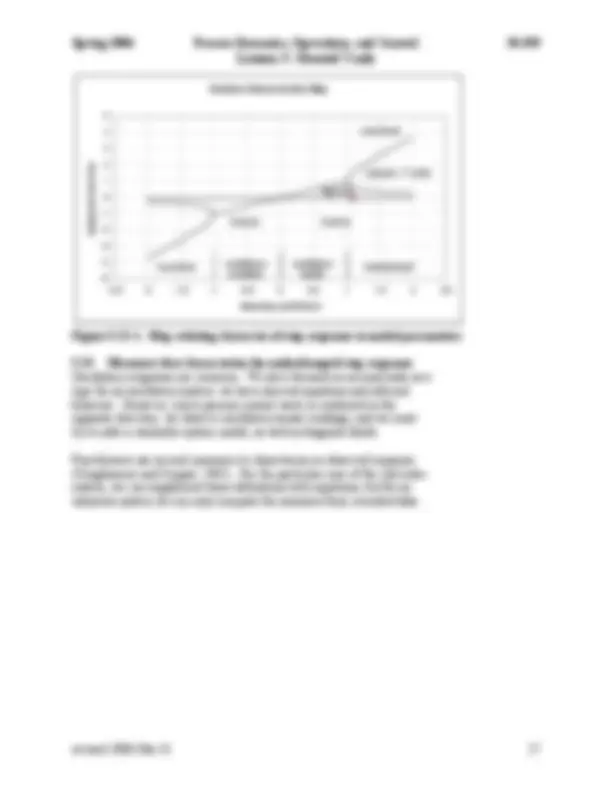
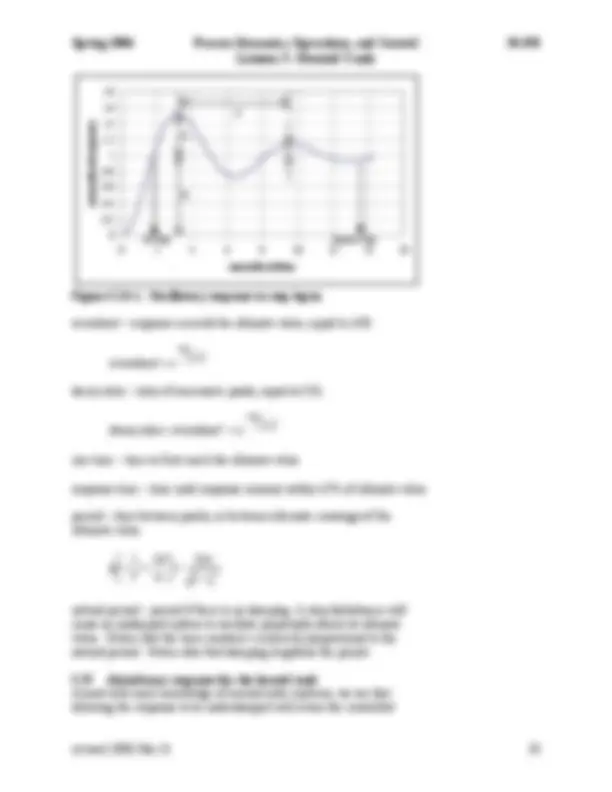
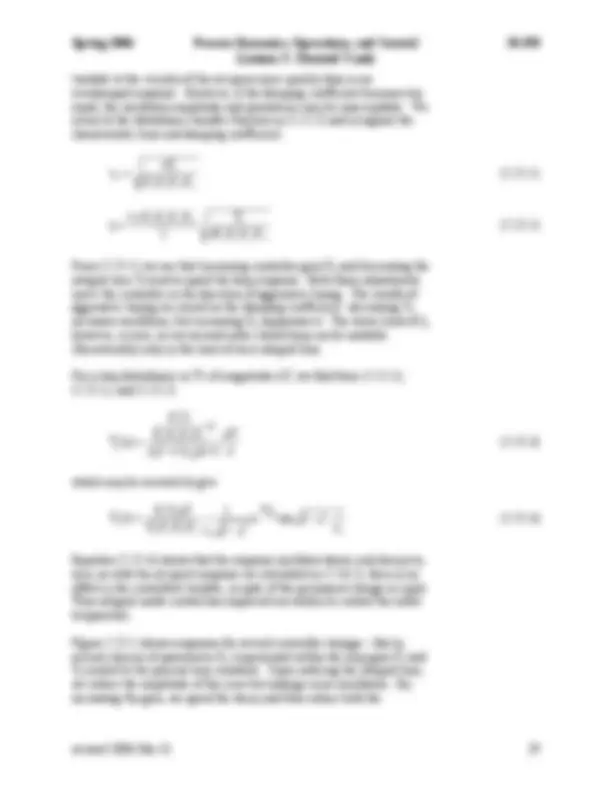
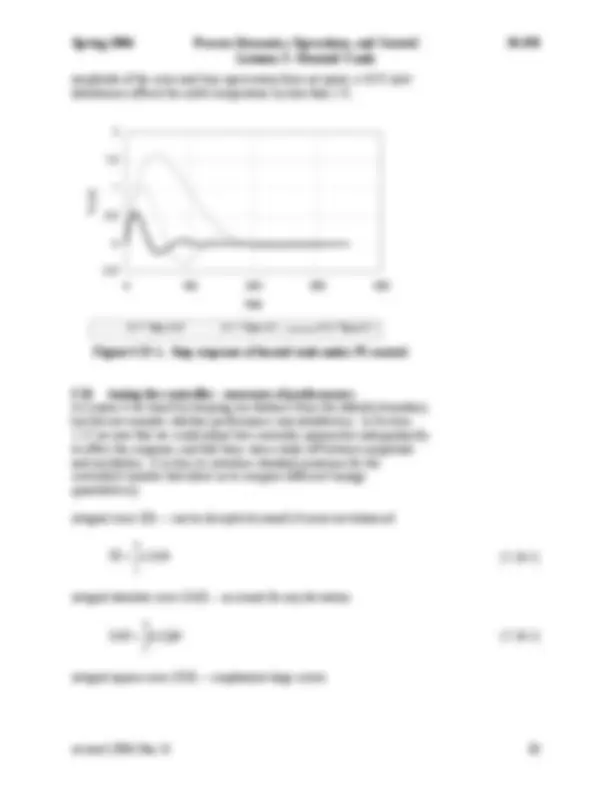
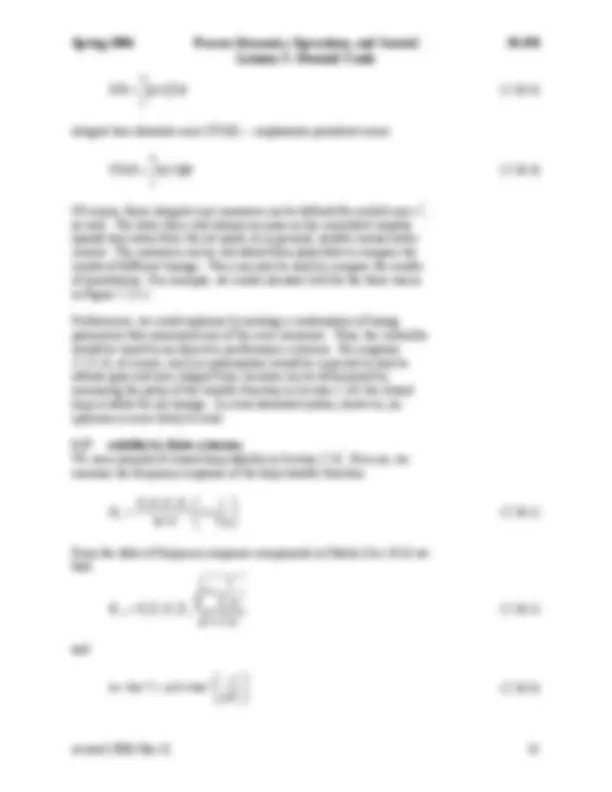
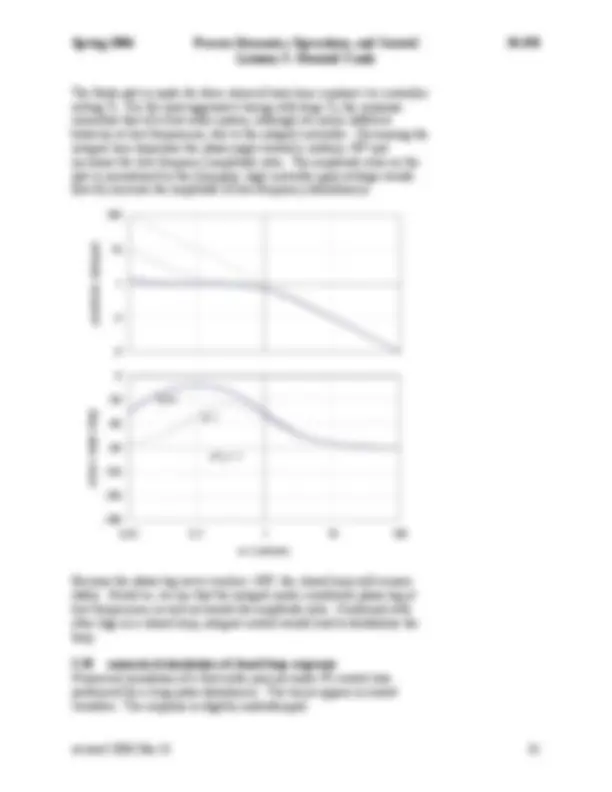

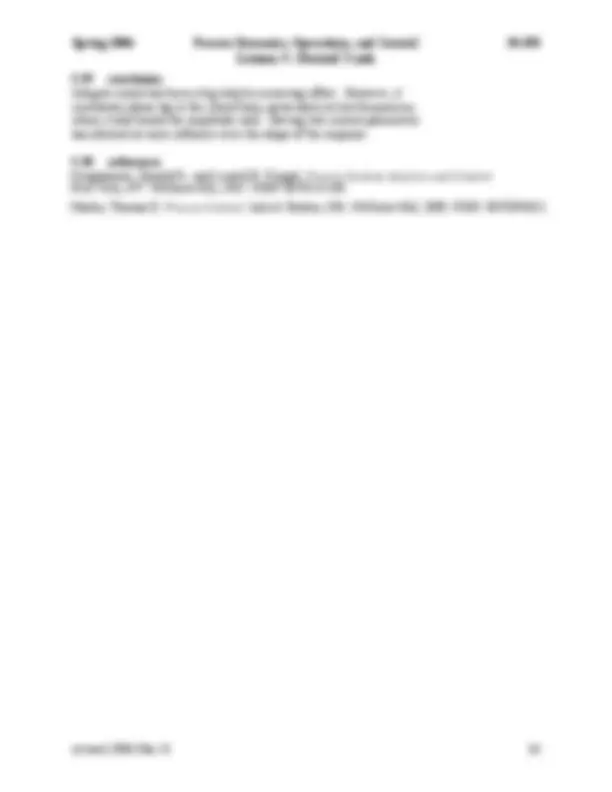
Study with the several resources on Docsity
Earn points by helping other students or get them with a premium plan
Prepare for your exams
Study with the several resources on Docsity
Earn points to download
Earn points by helping other students or get them with a premium plan
Community
Ask the community for help and clear up your study doubts
Discover the best universities in your country according to Docsity users
Free resources
Download our free guides on studying techniques, anxiety management strategies, and thesis advice from Docsity tutors
heat transfer and mass balance chemical process control
Typology: Study Guides, Projects, Research
1 / 34
This page cannot be seen from the preview
Don't miss anything!
5.0 context and direction From Lesson 3 to Lesson 4, we increased the dynamic order of the process, introduced the Laplace transform and block diagram tools, took more account of equipment, and discovered how control can produce instability. Now we change the process: our system models have previously depended on material balances, but now we will write the energy balance. We will also introduce the integral mode of control in the algorithm.
5.1 a heated tank We consider a tank that blends and heats two inlet streams. The heating medium is a condensing vapor at temperature T (^) c in a heat exchanger of surface area A.
F 1 T (^1)
F 2 T (^2)
F T (^) o T (^) c
V
A
F 1 T (^1)
F 2 T (^2)
F T (^) o T (^) c
V
A
For the present, we continue to assume constant mass in an overflow tank. Writing the material balance,
ρF 1 +ρF 2 =ρ F (5.1-1)
This is not yet the time for complications: we will approximate the physical properties of the liquid (density, heat capacity, etc.) as constants. We will also simplify the problem by assuming that the flow rates remain constant in time. The energy balance is
dt
d ρ (^) p o− ref =ρ 1 p 1 − ref +ρ 2 p 2 − ref + c− o −ρ p o− ref (5.1-2)
where the overall heat transfer coefficient is U and the thermodynamic reference is Tref. We identify a steady-state operating reference condition with all variables at their desired values.
dt
d ρ p or− ref = =ρ 1 p 1 r− ref +ρ 2 p 2 r− ref + cr− or −ρ p or− ref
(5.1-3)
We subtract (5.1-3) from (5.1-2), define deviation variables, and rearrange to standard form.
' c p
' 2 p
' 2 p 1 p
' 1 p o
' o p
p (^) T FC UA
dt
dT FC UA
ρ +
ρ +
ρ
ρ +
ρ
ρ (5.1-4)
To make some sense of the equation coefficients, define the tank residence time
τ (^) R = (5.1-5)
and a ratio of the capability for heat transfer to the capability for enthalpy removal by flow.
FC p
ρ
β = (5.1-6)
β thus indicates the importance of heat transfer in the mixing of the fluids. We now use (5.1-5) and (5.1-6) to define the dynamic parameters: time constant and gains.
τ τ = 1
Thus the dynamic response of the tank temperature to disturbances is faster as heat transfer capability (β) becomes more significant. For no heat transfer (β = 0) the time constant is equal to the residence time.
1 1 (5.1-8)
2 2 (5.1-9)
However, doing the formalities for two step disturbances and one steady input,
T 1 ' = ΔT 1 U ( t−td 1 ) T 2 '=ΔT 2 U( t−td 2 ) Tc'= 0 (5.3-1)
We take Laplace transforms of these input variables:
e T(s) 0 s
e T(s) s
T 1 ' (s)^1 td^1 s 2 '^2 td^2 s c' =
Then we substitute (5.3-2) into the system model (5.2-1).
s 1
e s
s 1
e s
s 1
To ' (s)^11 td^1 s^22 td^2 s^3 τ +
τ +
τ +
We must invert each term; this is most easily done by processing the polynomial first and then applying the time delay. Thus
− (^) = − − τ ⎭
τ +
1 t 1 e s
s 1
( ) (^) ⎟ ⎠
τ +
τ − − −(t−t ) d 1
(^1) etd 1 s Ut t 1 e d^1 s
s 1
and finally
( ) ( ) (^) ⎟ ⎠
= Δ − − τ
− − τ − − (tt ) 2 2 d 2
(tt ) 1 1 d 1
o
d 1 d 2 T K TUt t 1 e K TUt t 1 e (5.3-6)
Figure 5.3-1 shows a sample calculation for opposing input disturbances. Notice that the gains K 1 and K 2 are less than unity. This is because we dilute each disturbance with other streams: streams of matter (two input flows) and energy (through the heat transfer surface). From the plot, can you tell which gain is greater?
0
1
2
3
0 50 100 150 200 250 300 t (s)
T'o (K)
0
5
10
15
T'1 and T'2 (K)^0 50 100 150 200 250
Figure 5.3-1: Response of outlet temperature to steps in two inlets
5.4 stability of the heated tank System model (5.2-1) has one negative pole, s = -τ-1, because the time constant is a positive quantity. Hence, the system is stable to all bounded inputs. Therefore, a blip in the inlet temperature will not set off wild temperature excursions at the outlet.
5.5 numerical solution of ODEs Analytical solutions to equations are desirable, but many useful equations simply cannot be solved. When we “solve an ODE numerically” we execute a set of calculations that results in a “numerical solution”: in effect, a table of numbers. One column in that table contains values of the independent variable, and the other column holds associated values of the dependent variable. A table of numbers lacks the economy of presentation and conceptual insight offered by an analytical expression. However, a table of numbers is much better than no solution, and it can certainly be plotted.
Matlab offers a suite of functions for solving differential equations. For example, the following file contains code to produce a plot indistinguishable from that of the analytical solution in Figure 5.3-1.
hold off % turn off the plot hold
end % heated_tank
% define the differential equation in a subfunction function dTodt = hot_tank(t,To,tau,K1,K2,K3,T1,T2,Tc) dTodt = (K1T1 + K2T2 + K3*Tc - To)/tau ; end
The Matlab function ode45 is one of several routines available for integrating ordinary differential equations. The output arguments are a column vector for time t and another for temperature deviation To. The input argument @hot_tank directs ode45 to the subfunction in which the equation is defined. Notice the way in which hot_tank is written: the equation is arranged to calculate the derivative of output variable To as a function of To and the input variables. ode45 calls hot_tank repeatedly as it marches through the time interval denoted by the row vector tspan.
5.6 scaled variables versus deviation variables We introduced deviation variables so that any non-zero variable - positive or negative - would be seen as a departure from the ideal reference condition. Deviation variables also allowed us to define and use transfer functions in expressing our system models through Laplace transforms.
We must, however, finally read real instruments and control real processes. For these purposes, it is common to represent sensor readings, controller outputs, and valve-stem positions on a scale of 0 to 100. Such scaled variables obscure actual values, but immediately reveal context. That is, a visitor to a control room would not know the significance of a particular tank level reading of 2.6 m, but could interpret 96% easily. An everyday example of a sensor that presents a scaled variable is the fuel gauge in an automobile.
To scale physical variable y, for example, we identify the range in which we expect it to vary: from y (^) min to y (^) max. We then subtract some bias value from y and divide the difference by the range:
y y
y y y max min
If the bias value yb is set to the minimum y (^) min , then y^ varies between 0 and 100%. This is the typical control room presentation. If instead the bias value is set to the reference value yr, then y^ varies from
y y
y y 100 % y y y
y y max min
min r −
The scaled range is still 100% wide, but includes both positive and negative regions, depending on where yr lies between y (^) min and y (^) max. Of course, yb may be set to any arbitrary value between the limits, but y (^) min and yr are generally the most useful.
We will use primes (′) to denote deviation variables and asterisks () for scaled variables. Unadorned variables will be presumed to be physical. To convert a deviation variable y′ (from an analytical solution, e.g.) for presentation as a scaled variable y^ , the definitions are combined:
y y
y y y y max min
r b
'
−
For example, Figure 5.6-1 shows a temperature trace expressed in physical, deviation, and scaled form. Because these are linear transformations, the basic character of the variable is unchanged.
5.7 just when I was getting accustomed to deviation variables! We will tend to use deviation variables for analytic solutions and derivations because of the convenience of zero initial conditions. We will use scaled variables for our numerical work, in which each time step moves the solution to a new value from the “initial condition” of the previous step.
proportional control suffers from offset. To counter this defect, we introduce a second mode of control, called integral, to complement the proportional behavior.
− = ε + ∫ε
t
0
I
c
co,b
co (^) T dt
x x K (5.10-1)
where x*co is the controller output and the controlled variable error is
sp ε* =y −y (5.10-2)
Before we discuss the integral mode, let us understand why we have written the controller algorithm in scaled variables. The controller is not specific to a process; it merely produces a response according to the error it receives. Hence it is most reasonable to build it so that error and response are expressed as percentages of a range; whatever y may be as a physical variable, in Equation (5.10-2) the scaled controlled variable y^ is subtracted from ysp , which is the preferred position on the scale. The resulting error ε^ is processed by the controller in Equation (5.10-1) to generate a scaled output xco. The bias output x*co,b is the controller’s resting state, achieved when there has been no error.
Integral mode integrates the error, so that the controller output xco , which drives the manipulated variable in the loop, increases with the persistence of error ε^ , in addition to its severity. The influence of the integral mode is set by the magnitude of the integral time T (^) I. In the special case of a constant error input to the controller, TI is the time in which the controller output doubles. Thus decreasing TI strengthens the controller response. Very large TI disables the integral mode, leaving a proportional controller. The dimensionless controller gain K*c acts on both the proportional and integral modes.
As an example, let us test a controller in isolation, so that we supply a controlled variable independently, and the controller output has no effect. Suppose we set Kc to 1 and TI to 1 minute. Suppose the set point is 40% and the bias output 50%. Initially, there is no error, and so the controller output is 50%. Figure 5.10-1 shows the controller response to a step increase in the controlled variable from 40 to 60%. Because the error suddenly becomes -20%, the proportional mode calls for the output to change by -20% (gain of +1). Thus xco becomes 30%. Over the next minute, there is no change in the controlled variable. Hence the integral mode calls for more controller output. In 1 minute, x*co decreases by another 20% and so reaches 10%.
At one minute, we contrive to return the controlled variable to set point, so that the error is again zero. The proportional mode then ceases to call for output. However, the integral mode still remembers the earlier error, and so the output returns to 30%, not the original 50%. We will see later that when the controller is placed in a feedback loop, not isolated as we have used it here, the integral mode acts to eliminate offset.
60
40
50
10
y*^ (%)
x *co(%)
ε*^ (%) 0
t
30
60
40
50
10
y*^ (%)
x *co(%)
ε*^ (%) 0
t
30
Figure 5.10-1: response of isolated PI controller to an input pulse
For our analytical work, we will want to express the controller algorithm in deviation variables. We proceed by substituting from definition (5.6-1) into the algorithm (5.10-1) and (5.10-2).
= ε + ε(s) Ts
x (s) K (s) I
c
' co (5.10-6)
5.11 step 4 - choose set points and limits The heated blending tank might require an occasional change of set point, depending on product grade, time of year, other process conditions, etc. At present we are presuming that the tank is part of a continuous process, so that its normal operating mode is to maintain temperature at the set point. Such a tank could also be used in a batch process, however. In this case, the set point might be an active function of time, according to the recipe of the batch.
Limits placed on temperature can be both high and low, depending on the process. Reasons for imposing high limits are often undesirable chemical changes: polymerization, product degradation, fouling, side reactions. Both high and low limits may be imposed to avoid phase changes: boiling and freezing for liquids.
We institute regulatory control, using, e.g., proportional-integral controllers, to keep controlled variables within acceptable operating limits. However, when there are safety limits to be enforced, regulatory control may be superseded by a safety control system. Thus a reactor temperature may normally be regulated within operating limits, but some higher value will trigger an audible alarm in the control room, and some yet higher value will initiate emergency response or shutdown procedures that override normal regulatory control.
5.12 the sensor in the feedback control loop Temperature may be measured with a variety of instruments that respond to temperature with an electrical signal, including thermocouples, thermistors, RTDs (resistance thermometry devices), etc. In this section, we address both the static (calibration) and dynamic (time response) characteristics of temperature sensors, with reference to our heated tank example.
Calibration of the sensor is determining the relationship between the actual quantity of interest (the temperature at some location in the fluid) and the output given by the sensor (which can be a voltage, a current in a circuit, a digital representation, etc., depending on the instrument). When we speak of a sensor, we usually refer to both the sensing element (such as the bimetallic junction of a thermocouple) and signal conditioning electronics. It is this latter component that produces a linear relationship between
temperature and sensor output, even though the behavior of the sensing element itself may be nonlinear.
Thus we relate the physical temperature To and its sensor reading Ts by
Ts = KsTo+b s (5.12-1)
In a handheld digital thermometer, the electronics are adjusted so that gain Ks is unity and bias bs is zero: 26ºC produces a reading of 26ºC. In a control loop, however, we are more likely to have To produce an electric current that ranges over 4 to 20 mA, where these limits correspond to the expected range of temperature variation. Current loops are a good way to transmit signals over the sorts of distances that separate operating processes from their control rooms.
The sensor range is adjusted by varying Ks and bs. For example, suppose that we wish to follow To over the range 50 to 100ºC. Then
( ) ( ) ( ) ( ) K ( 0. 32 ) mAK b ( 12 ) mA
20 mA K 100 C b
4 mA K 50 C b
s
1 s
s s
s s
−
D
D
(5.12-2)
We express the sensor calibration in deviation variables by subtracting the reference state from (5.12-1). Suppose we wish to use 75ºC as a reference operating condition. At the reference, the sensor output will be 12 mA.
' s o
' Ts = KT (5.12-3)
We obtain a 0 to 100% range by taking the scaled variable reference as the minimum temperature.
( ) ( )
( ) ( )
20 4 mA
T 4 mA Ts * s o D
D
−
From (5.12-4), we see that the scaled sensor output may be defined in terms of the sensor reading or the controlled variable itself. A temperature of 75ºC causes a sensor output of 12 mA, or 50% of range.
We now consider the dynamic response of our sensor. Suppose we place the sensor in fluid at 50ºC and allow it to equilibrate, so that its output is 4 mA. We now move the sensor suddenly to another fluid at 100ºC; how quickly does the sensor respond to this step input? How long until the output becomes 20 mA? Classic textbook treatments of thermocouples
Thus the flow admitted by the valve is the flow that is able to condense at a temperature high enough to transfer that heat of condensation to the liquid in the tank. In short, we open the valve to supply more heat.
Let us not become lost among momentum equation, vapor pressure relationship, empirical flow resistance relationships, etc., which we invoked above. Our purpose is to describe the action of the controller upon the condensing temperature, and so we need a gain (from steady- state relationships) and dynamic description (from the rate processes). Will a simple first-order description be sufficient?
x (s ) s 1
T (s) 'co v
' v c τ +
We will address this question more thoroughly in Lesson 6. For the present, while not dismissing our skepticism, we will accept (5.13-1). That is, we presume that over some range of operating conditions, at least, the change in condensing temperature is directly proportional to a change in controller output. The underlined phrase is a key one: our linear (i.e., constant gain) model is an approximation, and part of our engineering job is to determine how far our model can be trusted.
Regarding dynamic response, the first-order response of Tc to xco is also an approximation. In Lesson 4 we used this description of our valve, and we saw that our second-order process combined with the valve to produce a third-order closed loop. In this lesson, however, we have other topics to explore, so we will presume that the characteristic time τv for changing the condensing temperature is much smaller than the mixing tank time constant τ, so that
Tc ' (s)= Kvx'co(s ) (5.13-2)
We have said, then, that we expect the dynamic response of the closed loop to depend primarily on the dynamic characteristics of the process, and very little on the characteristics of sensor (Section 5.12) and valve (Section 5.13).
5.14 numerical controller calculations In Lessons 3 and 4, we have expressed controller behavior in mathematical terms and predicted the closed loop behavior by solving process and controller equations simultaneously. We posit “step disturbance” and then make a plot of what the equations say. This dynamic system representation is useful if it can help us manage real equipment.
We understand that our process is actually a tank, but what does the controller look like? For many years, the controller was a physical box that manipulated air flow with bellows and dampers; its output was an air pressure that positioned a valve stem. Coughanowr and Koppel (chap.22) describe such mechanisms.
Now, the controller is most often a program that runs on a microprocessor. The program input is numbers that represent physical signals from the sensor. The algorithm (5.10-1) is computed numerically. The output numbers are fed to a transducer that makes physical adjustments to a valve.
Whereas our analytical solutions represent continuous connection between controller and process, the computer program controller samples the process values at intervals. Marlin (chap.11) discusses the effect of sampling frequency on controller performance.
A very simple controller program outline is given below:
initialization set up arrays to hold variables set controller parameters (Kc*, TI)
loop for automatic control interrogate sensor to determine controlled variable at t_now use comparator to determine set point and calculate error use controller algorithm to calculate controller output at t_now administer controller output to process update monitor plot with values at t_now wait for time interval Δt to pass set new value of t_now and return to beginning of loop
s 1 KKKK
s T KKKK
Ts 1 T (s)
T(s)
s c v 3
s c v 3 I
2 s c v 3
I
I ' sp
' o
τ
Adding integral control to a first order process has resulted in a closed loop with second-order dynamics.
5.16 closed-loop behavior - set point step response Responses to disturbance inputs and set point changes will depend on the poles of (5.15-3). These are
( )
τ
⎛ (^) τ − − ± + − = 2
s,s
2 s c v 3 s c v 3 I
s c v 3 1 2 (5.16-1)
We observe that the poles could be complex, so that the closed loop response could be oscillatory. The tendency toward a negative square root, and thus oscillation, is exacerbated by reducing the integral time TI. We also observe that the real part of the poles is negative, indicating a stable system.
We illustrate set point step response for real poles, where the set point is changed by magnitude ΔT:
= Δ + st
2 1
I st 2
2 1
I ' 1 o (^1) e 2
s
s
s
e
s
s
s
The response is written in terms of poles s 1 and s 2. Because they are negative, the two exponential terms decay in time, leaving the long-term change in set point as ΔT. Thus we requested that the tank temperature change by ΔT, and the tank temperature changed by ΔT. There is no offset - this is the contribution of the integral mode of control.
5.17 second order systems In Lesson 4, we described the two tanks in series as an overdamped second-order system; now our heated tank with integral-mode control is also second order, but perhaps not overdamped. We defer further exploration of our closed loop behavior until we learn more about the properties of second-order systems. Thus we consider
dt
dy y( 0 )
dt
dx y(t) Kx(t) M dt
dy dt
d y
t 0
2
2
α +β + = +
=
As before, we will assume that all initial conditions on response variable y(t) are zero, so that the system is initially at steady state, and will be driven only by disturbance x(t). Parameter K has dimensions of y divided by x; it is the steady-state gain. Parameter M measures the sensitivity of the system to the rate of change of the disturbance x(t); it has the dimensions of K multiplied by time. Both K and M may be positive or negative, as may α and β.
We solve (5.17-1) by Laplace transform.
s s 1
Ms K x(s)
y( s) α^2 +β +
The behavior of the solution depends fundamentally on the poles of (5.17- 2). From the properties of the quadratic equation we recall that the poles are real for
β^2 α < (5.17-3)
A map relating system stability to coefficients α and β is given in Figure 5.17-1.