
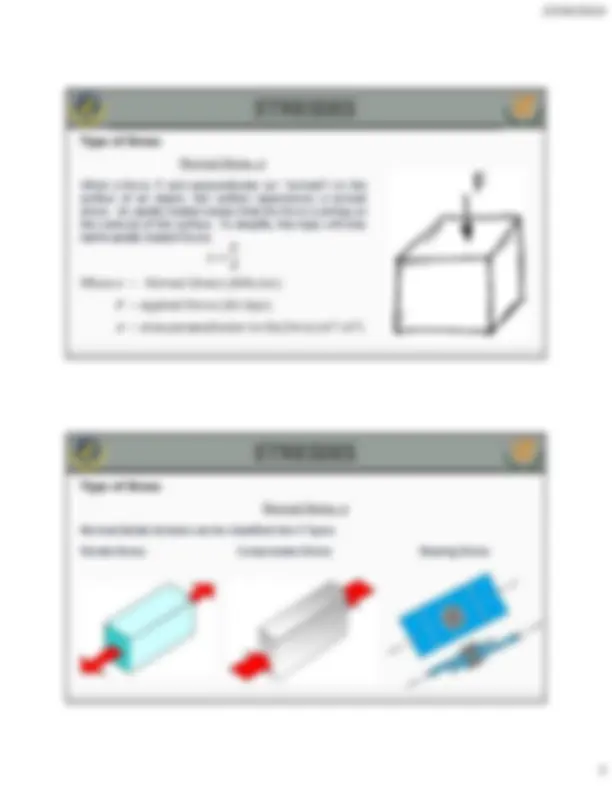
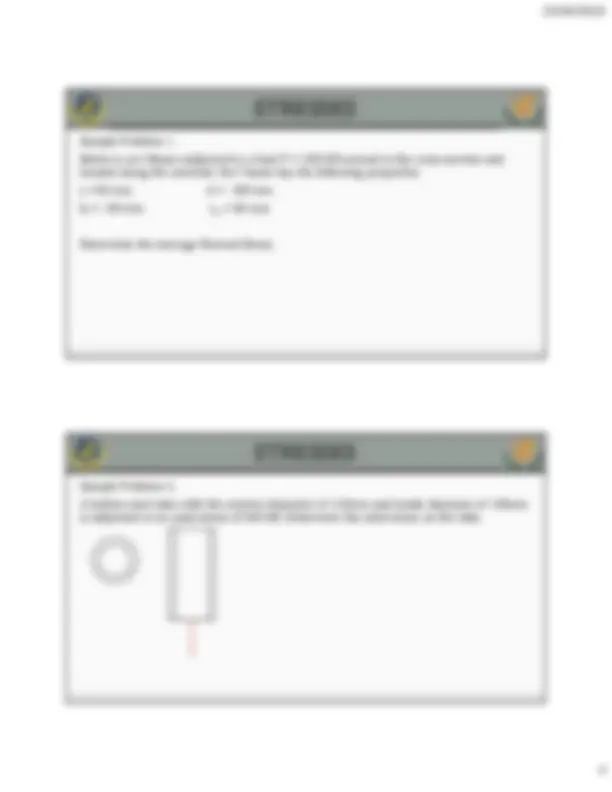
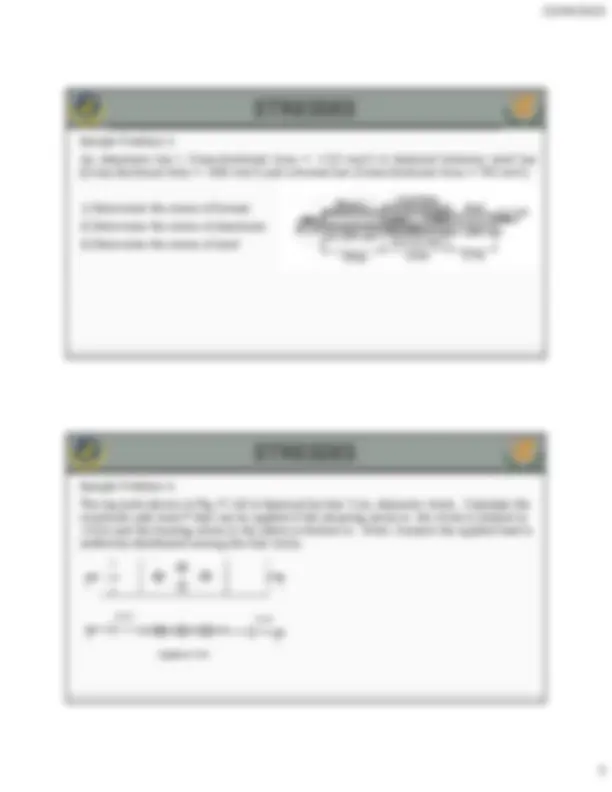
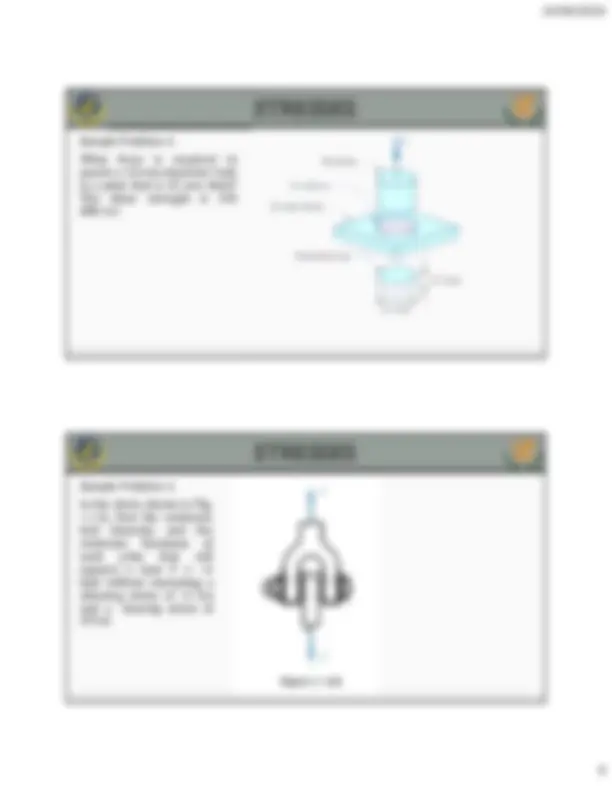
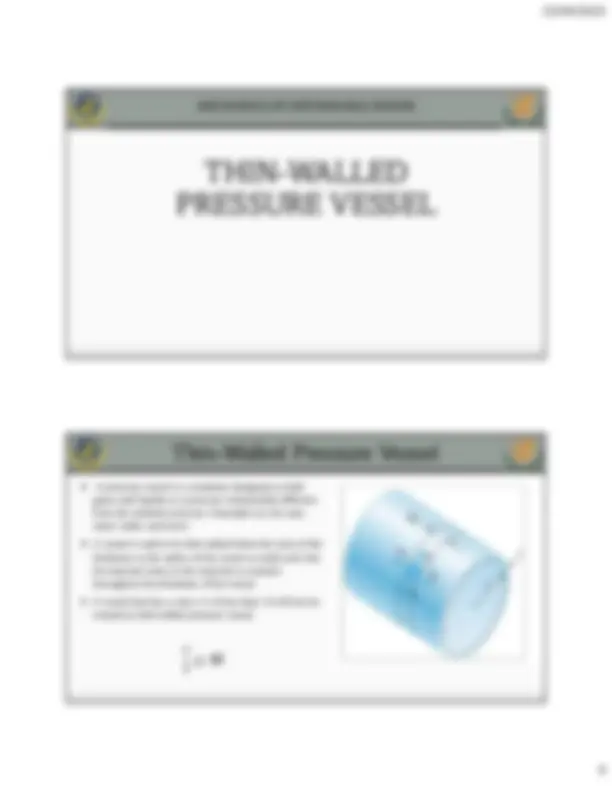
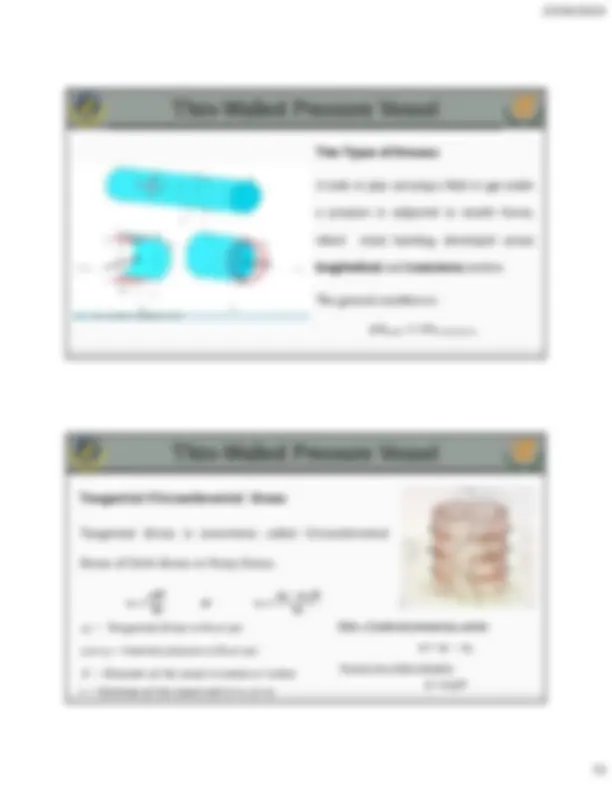
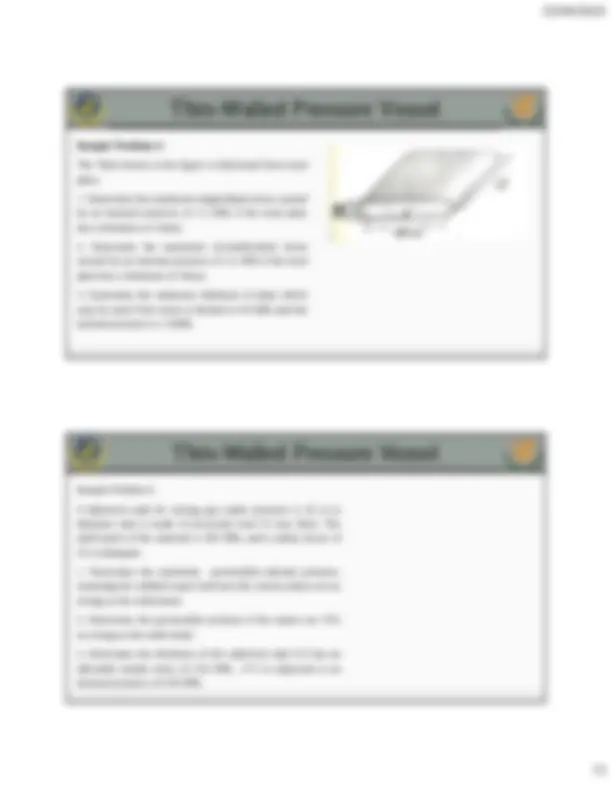
Study with the several resources on Docsity
Earn points by helping other students or get them with a premium plan
Prepare for your exams
Study with the several resources on Docsity
Earn points to download
Earn points by helping other students or get them with a premium plan
Community
Ask the community for help and clear up your study doubts
Discover the best universities in your country according to Docsity users
Free resources
Download our free guides on studying techniques, anxiety management strategies, and thesis advice from Docsity tutors
An in-depth exploration of the mechanics of deformable bodies, focusing on the concepts of stresses and thin-walled pressure vessels. It covers the development of internal forces, types of stresses (normal and shear), and the analysis of thin-walled pressure vessels subjected to internal pressure. Several sample problems to illustrate the application of the principles discussed. It serves as a comprehensive resource for students and professionals studying the mechanics of materials, particularly in the areas of stress analysis and pressure vessel design.
Typology: Exercises
1 / 13
This page cannot be seen from the preview
Don't miss anything!
Rigid Bodies- do not deform (stretch, compress, or bend) when subjected to load. Deformable Bodies - any body that changes its shape and/or volume while being acted upon by any kind of external force.
Development of Internal Forces In strength of materials, we make an additional investigation of the internal distribution of the forces. This is done by passing an exploratory section through the body, exposing the internal forces acting on the section that are necessary to maintain equilibrium of either segment. In general, the internal forces reduce to a resultant force and moment, which are resolved into components that are normal (perpendicular) and tangent to the section.
Development of Internal Forces N Axial Force,P. This component measures the resistance to pulling or pushing action perpendicular to the section. Vx,Vz Shear forces, v. These are components of the total resistance to sliding the portion to one side of the section. My Torque, T. This component measures the resistance to twisting the member. Mx, Mz Bending Moment, M. Measures the resistance to bending the member about the y and z axes.
Sample Problem 1. Below is an I-Beam subjected to a load P = 300 kN normal to the cross-section and located along the centroid, the I beam has the following properties tf =50 mm d = 300 mm bf = 100 mm tw = 60 mm Determine the average Normal Stress.
Sample Problem 2. A hollow steel tube with the exterior diameter of 120mm and inside diameter of 100mm is subjected to an axial stress of 400 kN. Determine the axial stress on the tube.
Sample Problem 3. An aluminum bar ( Cross-Sectional Area = 1125 mm^2 ) is fastened between steel bar (Cross-Sectional Area = 1000 mm^2 ) and a bronze bar (Cross-Sectional Area = 750 mm^2 ).
Sample Problem 4. The lap joint shown in Fig. P-126 is fastened by four ¾-in.-diameter rivets. Calculate the maximum safe load P that can be applied if the shearing stress in the rivets is limited to 14 ksi and the bearing stress in the plates is limited to 18 ksi. Assume the applied load is uniformly distributed among the four rivets.
Sample Problem 1. The lap joint shown below is fastened by four rivets of 3/4-in. diameter. Find the maximum load P that can be applied if the working stresses are 14 ksi for shear in the rivet and 18 ksi for bearing in the plate. Assume that the applied load is distributed evenly among the four rivets, and neglect friction between the plates.
Sample Problem 2. Referring to Fig. P-121, compute the maximum force P that can be applied by the machine operator, if the shearing stress in the pin at B and the axial stress in the control rod at C are limited to 4000 psi and 5000 psi, respectively. The diameters are 0.25 inch for the pin, and 0.5 inch for the control rod. Assume single shear for the pin at B.
Sample Problem 3. What force is required to punch a 20-mm-diameter hole in a plate that is 25 mm thick? The shear strength is 350 MN/m^2.
Sample Problem 4. In the clevis shown in Fig. 1-11b, find the minimum bolt diameter and the minimum thickness of each yoke that will support a load P = 14 kips without exceeding a shearing stress of 12 ksi and a bearing stress of 20 ksi.
Two Types of Stresses A tank or pipe carrying a fluid or gas under a pressure is subjected to tensile forces, which resist bursting, developed across longitudinal and transverse section. The general condition is : 𝑝𝐴௧ = 𝜎𝐴௦௦௧
Tangential/Circumferential Stress Tangential Stress is sometimes called Circumferential Stress of Girth Stress or Hoop Stress. 𝜎௧ − 𝑇𝑎𝑛𝑔𝑒𝑛𝑡𝑖𝑎𝑙 𝑆𝑡𝑟𝑒𝑠𝑠 𝑖𝑛 𝑃𝑎 𝑜𝑟 𝑝𝑠𝑖 𝑝 𝑜𝑟 𝑝 − 𝐼𝑛𝑡𝑒𝑟𝑛𝑎𝑙 𝑝𝑟𝑒𝑠𝑠𝑢𝑟𝑒 𝑖𝑛 𝑃𝑎 𝑜𝑟 𝑝𝑠𝑖 𝐷 − 𝐷𝑖𝑎𝑚𝑒𝑡𝑒𝑟 𝑜𝑓 𝑡ℎ𝑒 𝑣𝑒𝑠𝑠𝑒𝑙 𝑖𝑛 𝑚𝑒𝑡𝑒𝑟𝑠 𝑜𝑟 𝑖𝑛𝑐ℎ𝑒𝑠 𝑡 − 𝑡ℎ𝑖𝑐𝑘𝑛𝑒𝑠𝑠 𝑜𝑓 𝑡ℎ𝑒 𝑣𝑒𝑠𝑠𝑒𝑙 𝑤𝑎𝑙𝑙 𝑖𝑛 𝑚. 𝑜𝑟 𝑖𝑛. 𝑁𝑜𝑡𝑒 ∶ 𝑖𝑓 𝑒𝑥𝑡𝑒𝑟𝑛𝑎𝑙 𝑝𝑟𝑒𝑠𝑠𝑢𝑟𝑒, 𝑝 𝑒𝑥𝑖𝑠𝑡𝑠 𝒑 = 𝒑𝒊 − 𝒑𝒐 Pressure for a fluid of depth,h 𝒑 = 𝝆 𝒈 𝒉 𝝈𝒕 = 𝒑𝑫 𝟐𝒕 𝒐𝒓 𝝈𝒕 = (𝒑𝒊 − 𝒑𝒐)𝑫 𝟐𝒕
Longitudinal Stress Consider the free body diagram in the transverse section of the tank, the force, F, acting at the rear end of the tank must be equal to the total longitudinal stress on the wall PT=σl Awall. Since it is compared to D, the area of the wall is closed to π D t. 𝝈୪ = 𝒑 𝑫 4𝒕 𝝈𝒍= (𝒑𝒊 − 𝒑𝒐)𝑫 𝟒𝒕 𝝈𝒕 = 𝟐𝝈𝒍 𝜎 − 𝐿𝑜𝑛𝑔𝑖𝑡𝑢𝑑𝑖𝑛𝑎𝑙 𝑆𝑡𝑟𝑒𝑠𝑠 𝑖𝑛 𝑃𝑎 𝑜𝑟 𝑝𝑠𝑖 𝑝 𝑜𝑟 𝑝 − 𝐼𝑛𝑡𝑒𝑟𝑛𝑎𝑙 𝑝𝑟𝑒𝑠𝑠𝑢𝑟𝑒 𝑖𝑛 𝑃𝑎 𝑜𝑟 𝑝𝑠𝑖 𝐷 − 𝐷𝑖𝑎𝑚𝑒𝑡𝑒𝑟 𝑜𝑓 𝑡ℎ𝑒 𝑣𝑒𝑠𝑠𝑒𝑙 𝑖𝑛 𝑚𝑒𝑡𝑒𝑟𝑠 𝑜𝑟 𝑖𝑛𝑐ℎ𝑒𝑠 𝑡 − 𝑡ℎ𝑖𝑐𝑘𝑛𝑒𝑠𝑠 𝑜𝑓 𝑡ℎ𝑒 𝑣𝑒𝑠𝑠𝑒𝑙 𝑤𝑎𝑙𝑙 𝑖𝑛 𝑚. 𝑜𝑟 𝑖𝑛. 𝑁𝑜𝑡𝑒 ∶ 𝑖𝑓 𝑒𝑥𝑡𝑒𝑟𝑛𝑎𝑙 𝑝𝑟𝑒𝑠𝑠𝑢𝑟𝑒, 𝑝 𝑒𝑥𝑖𝑠𝑡𝑠 𝒑 = 𝒑𝒊 − 𝒑𝐨 Pressure for a fluid of depth,h 𝒑 = 𝝆 𝒈 𝒉
Sample Problem 1 From CE Board May 2011 - A water tank 3m in diameter ang 6 m in height is made from steel having a thickness of 12mm. When the tank is filled with water, determine the circumferential stress.
Sample Problem 4 The Tank shown in the figure is fabricated from steel plate,
Sample Problem 5 A Spherical tank for storing gas under pressure is 25 m in diameter and is made of structural steel 15 mm thick. The yield point of the material is 250 MPa, and a safety factor of 2.5 is adequate.