
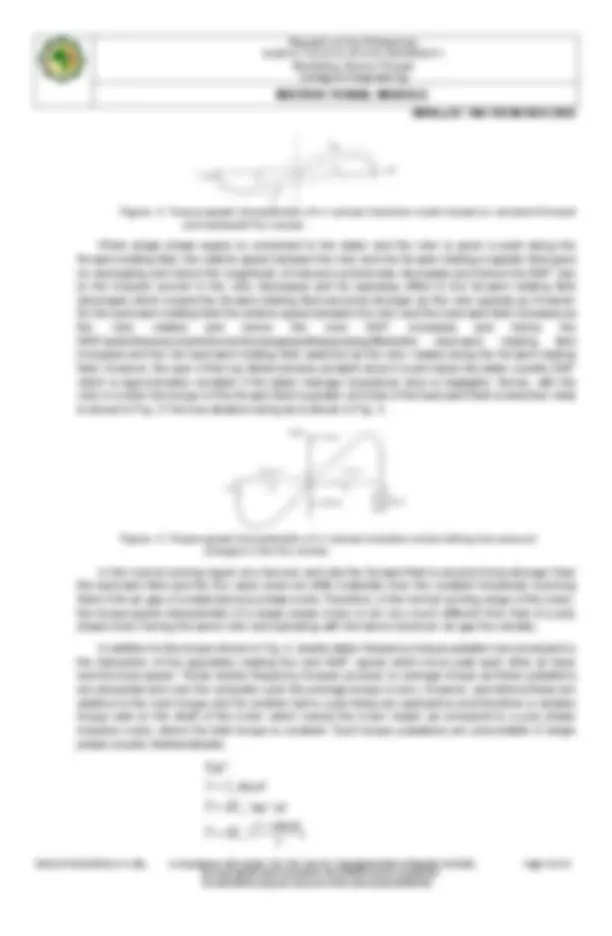
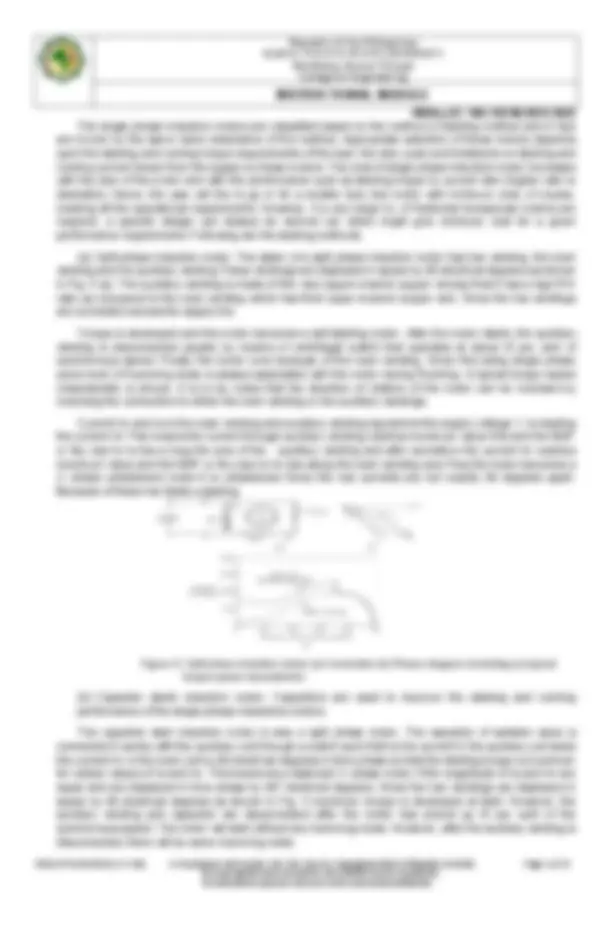
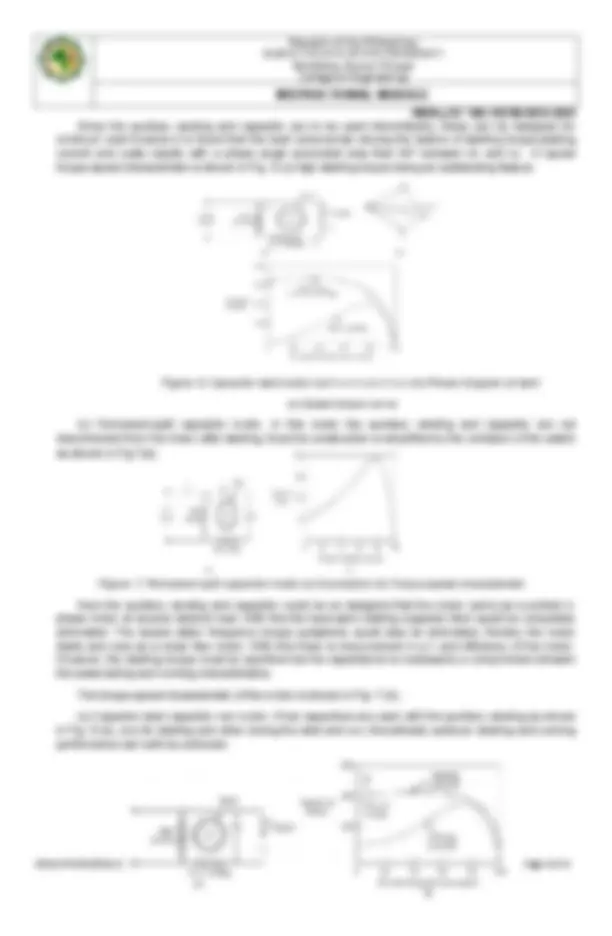
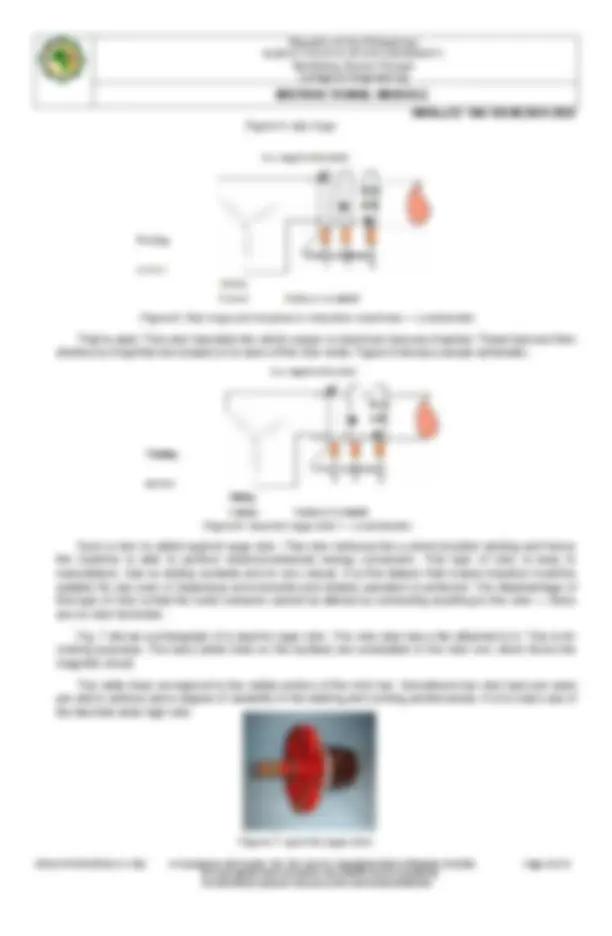
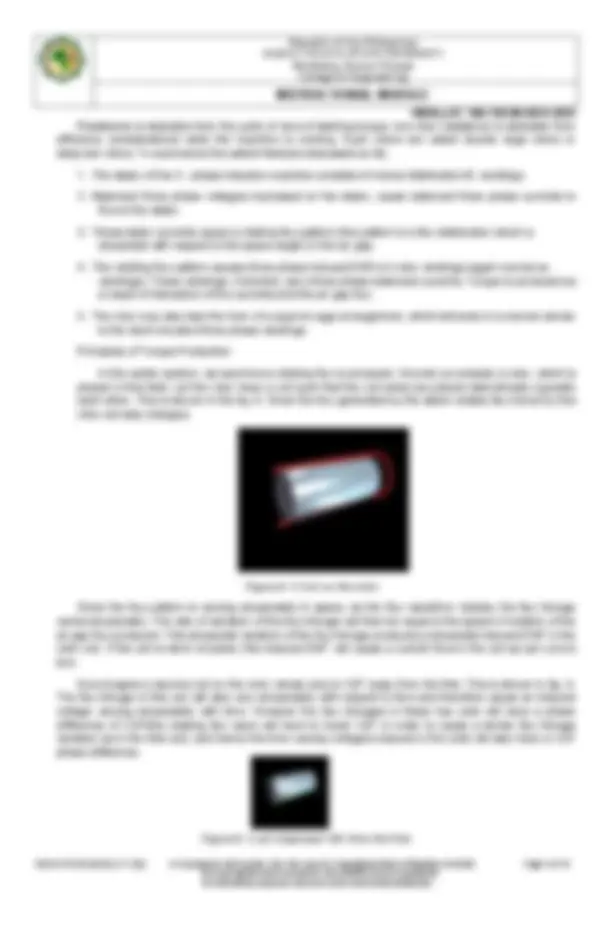
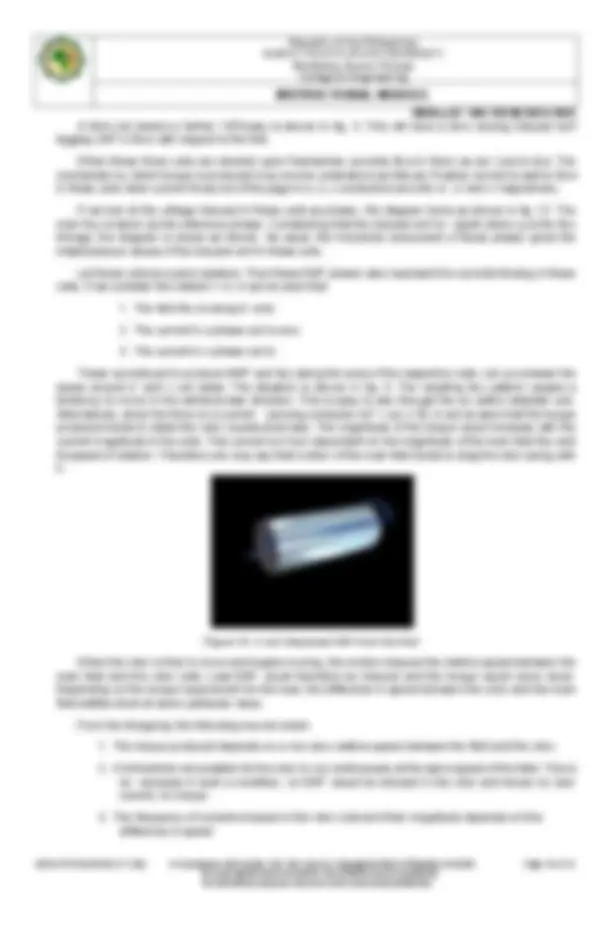
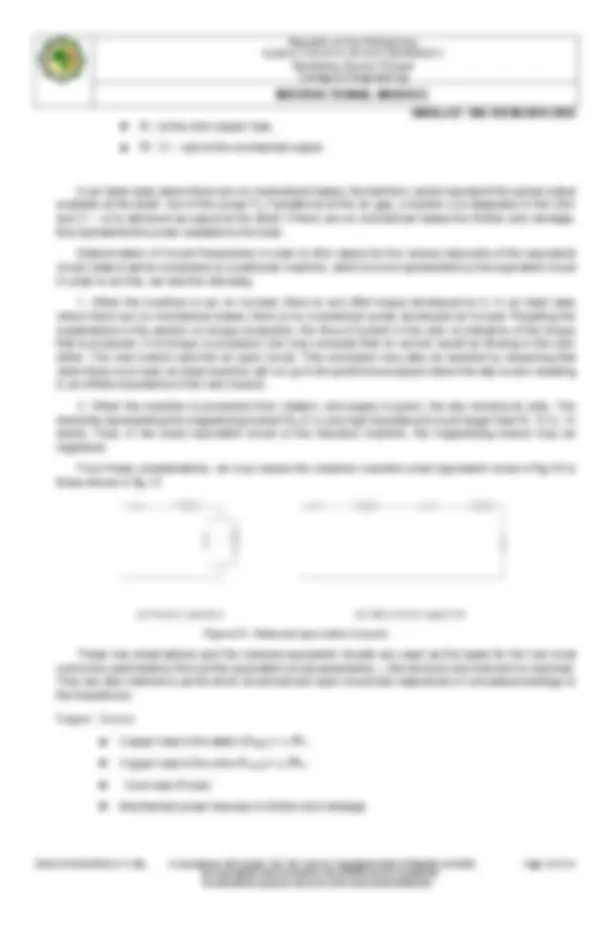
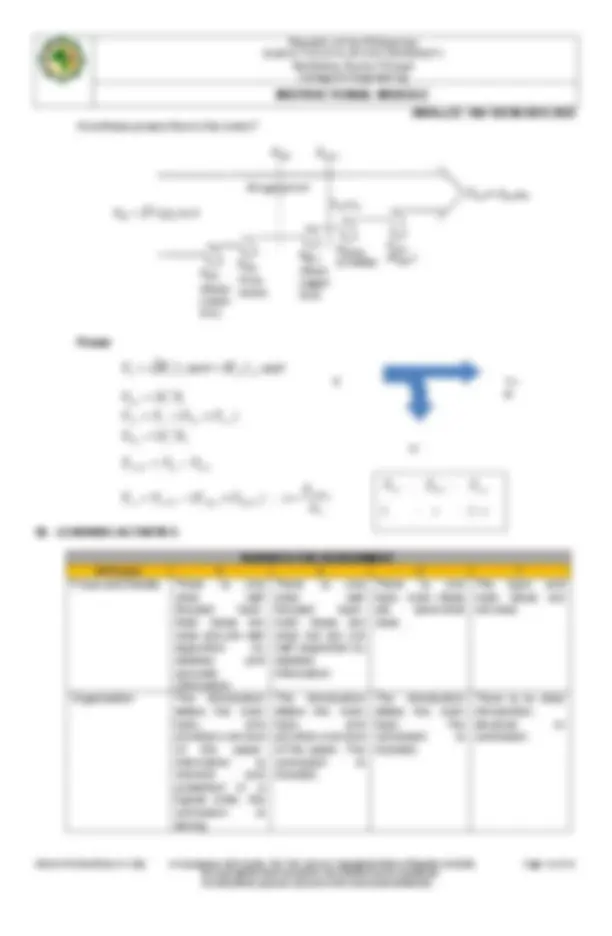
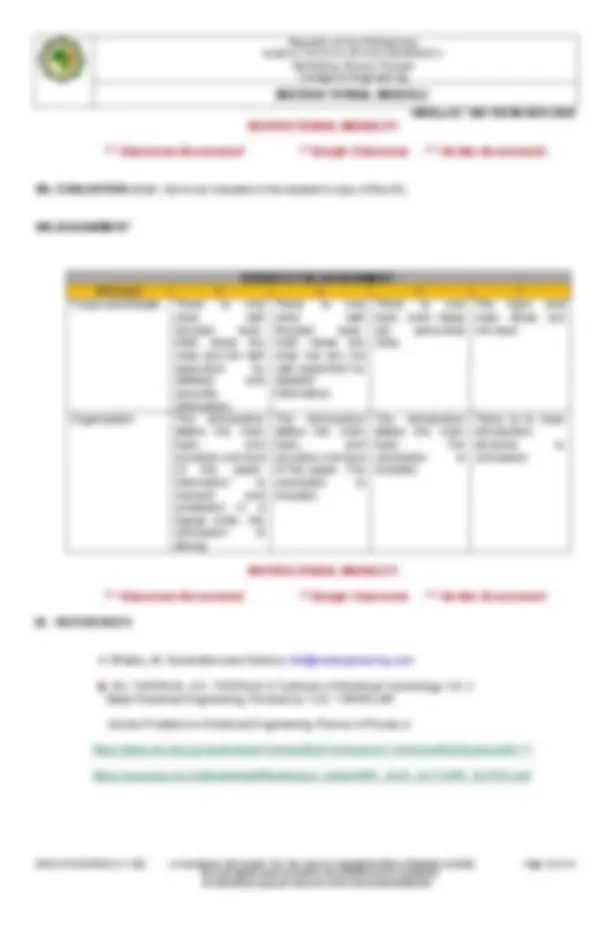
Study with the several resources on Docsity
Earn points by helping other students or get them with a premium plan
Prepare for your exams
Study with the several resources on Docsity
Earn points to download
Earn points by helping other students or get them with a premium plan
Community
Ask the community for help and clear up your study doubts
Discover the best universities in your country according to Docsity users
Free resources
Download our free guides on studying techniques, anxiety management strategies, and thesis advice from Docsity tutors
This instructional module provides a comprehensive overview of single-phase and three-phase induction motors, covering their characteristics, operating principles, and methods for speed control. It delves into the differences between single-phase and three-phase motors, explaining the need for special starting arrangements in single-phase motors. The module also explores various types of single-phase motors, including split-phase, capacitor-start, and shaded-pole motors, highlighting their advantages and disadvantages. Additionally, it discusses the concept of slip and its role in torque production, providing a detailed explanation of the equivalent circuit of an induction machine.
Typology: Study notes
1 / 15
This page cannot be seen from the preview
Don't miss anything!
NUEVA VIZCAYA STATE UNIVERSITY Bambang, Nueva Vizcaya College of Engineering
IM No.:EE 106 -1SEM-202 4 -202 5 NVSU-FR-ICD-05-00 (111120) In Accordance with Section 185, Fair Use of a Copyrighted Work of Republic Act 8293, Page 1 of 15 the copy righted works included in this material may be reproduced
Bachelor of Science in Mechanical Engineering
DC and AC Machinery YEAR LEVEL 3 TIME FRAME 15Hrs WK^ NO.^ 12-15 IM NO. 05 I. UNIT TITLE/CHAPTER TITLE Chapter 5. Induction Motor II. LESSON TITLE Induction Motor III. LESSON OVERVIEW Single phase induction motor; Three Phase Induction Motor; Testing and Speed control of Induction machines; IV. DESIRED LEARNING OUTCOMES
NUEVA VIZCAYA STATE UNIVERSITY Bambang, Nueva Vizcaya College of Engineering
IM No.:EE 106 -1SEM-202 4 -202 5 NVSU-FR-ICD-05-00 (111120) In Accordance with Section 185, Fair Use of a Copyrighted Work of Republic Act 8293, Page 2 of 15 the copy righted works included in this material may be reproduced around the air gap and constant in time with respect to an observer moving with the MMF. The stator winding of the single phase motor is disposed in slots around the inner periphery ofalaminatedringsimilartothe3-phasemotor. Figure: 1 Elementary single phase induction mo to r An induction motor with a cage rotor and single phase stator winding is shown schematically in Fig.1. The actual stator winding as mentioned earlier is distributed in slots so as to produce an approximately sinusoidal space distribution of MMF. Principle of Operation Suppose the rotor is at rest and 1-phase supply is given to stator winding. The current flowing in the stator winding gives rise to an MMF whose axis is along the winding and it is a pulsating MMF, stationary in space and varying in magnitude, as a function of time, varying from positive maxi- mum to zero to negative maximum and this pulsating MMF induces currents in the short-circuited rotor of the motor which gives rise to an MMF. The currents in the rotor are induced due to transformer action and the direction of the currents is such that the MMF so developed opposes the stator MMF. The axis of the rotor MMF is same as that of the stator MMF. Since the torque developed is proportional to sine of the angle between the two MMF and since the angle is zero, the net torque acting on the rotor is zero and hence the rotor remains stationary. For analytical purposes a pulsating field can be resolved into two revolving fields of constant magnitude and rotating in opposite directions as shown in Fig. 2 and each field has a magnitude equal to half the maximum length of the original pulsating phasor. Figure: 2. Representation of the pulsating field by space phasors These component waves rotate in opposite direction at synchronous speed. The forward (anticlockwise) and backward-rotating (clockwise) MMF waves f and b are shown in Fig. 2 .. In case of 3- phase induction motor there is only one forward rotating magnetic field and hence torque is developed and the motor is self-starting. However, in single phase induction motor each of this component MMF waves produces induction motor action but the corresponding torques are in opposite direction. With the rotor at rest the forward and backward field produce equal torques but opposite in direction and hence no net torque is developed on the motor and the motor remains stationary. If the forward and backward air gap fields remained equal when the rotor is revolving, each of the component fields would produce a torque-speed characteristic similar to that of a Poly phase induction motor with negligible leakage impedance as shown by the dashed curves f And b in Fig. 3 The resultant torque-speed characteristic which is the algebraic sum of the two component curves shows that i f the motor were started by auxiliary means it would produce torque in what- ever direction it was started
NUEVA VIZCAYA STATE UNIVERSITY Bambang, Nueva Vizcaya College of Engineering
IM No.:EE 106 -1SEM-202 4 -202 5 NVSU-FR-ICD-05-00 (111120) In Accordance with Section 185, Fair Use of a Copyrighted Work of Republic Act 8293, Page 4 of 15 the copy righted works included in this material may be reproduced The single phase induction motors are classified based on the method of starting method and in fact are known by the same name descriptive of the method. Appropriate selection of these motors depends upon the starting and running torque requirements of the load, the duty cycle and limitations on starting and running current drawn from the supply by these motors. The cost of single phase induction motor increases with the size of the motor and with the performance such as starting torque to current ratio (higher ratio is desirable), hence, the user will like to go in for a smaller size (hp) motor with minimum cost, of course, meeting all the operational requirements. However, if a very large no. of fractional horsepower motors are required, a specific design can always be worked out which might give minimum cost for a given performance requirements. Following are the starting methods. (a) Split-phase induction motor. The stator of a split phase induction motor has two winding, the main winding and the auxiliary winding.These windings are displaced in space by 90 electrical degrees as shown in Fig. 5 (a). The auxiliary winding is made of thin wire (super enamel copper wire)so that it has a high R/X ratio as compared to the main winding which has thick super enamel copper wire. Since the two windings are connected across the supply the Torque is developed and the motor becomes a self-starting motor. After the motor starts, the auxiliary winding is disconnected usually by means of centrifugal switch that operates at about t5 per cent of synchronous speed. Finally the motor runs because of the main winding. Since this being single phase some level of humming noise is always associated with the motor during Running. A typical torque speed characteristic is shown. It is to be noted that the direction of rotation of the motor can be reversed by reversing the connection to either the main winding or the auxiliary windings. Current Im and Ia in the main winding and auxiliary winding lag behind the supply voltage V, Ia leading the current Im This means the current through auxiliary winding reaches maximum value first and the MMF or flux due to Ia lies a long the axis of the auxiliary winding and after sometime the current Im reaches maximum value and the MMF or flux due to Im lies along the main winding axis.Thus the motor becomes a 2- phase unbalanced motor.It is unbalanced Since the two currents are not exactly 90 degrees apart. Because of these two fields a starting Figure: 5. Split phase induction motor (a) Connection (b) Phasor diagram at starting (c) typical torque-speed characteristic. (b) Capacitor starts induction motor: Capacitors are used to improve the starting and running performance of the single phase inductions motors. The capacitor start induction motor is also a split phase motor. The capacitor of suitable value is connected in series with the auxiliary coil through a switch such that Ia the current in the auxiliary coil leads the current Im in the main coil by 90 electrical degrees in time phase so that the starting torque is maximum for certain values of Ia and Im. This becomes a balanced 2- phase motor if the magnitude of Ia and Im are equal and are displaced in time phase by 90 ° electrical degrees. Since the two windings are displaced in space by 90 electrical degrees as shown in Fig. 5 maximum torque is developed at start. However, the auxiliary winding and capacitor are disconnected after the motor has picked up t5 per cent of the synchronous speed. The motor will start without any humming noise. However, after the auxiliary winding is disconnected, there will be some humming noise.
NUEVA VIZCAYA STATE UNIVERSITY Bambang, Nueva Vizcaya College of Engineering
IM No.:EE 106 -1SEM-202 4 -202 5 NVSU-FR-ICD-05-00 (111120) In Accordance with Section 185, Fair Use of a Copyrighted Work of Republic Act 8293, Page 5 of 15 the copy righted works included in this material may be reproduced Since the auxiliary winding and capacitor are to be used intermittently, these can be designed for minimum cost.However,it is found that the best compromise among the factors of starting torque,starting current and costs results with a phase angle somewhat less than 90 ° between Im and Ia. A typical torque-speed characteristic is shown in Fig. 6 (c) high starting torque being an outstanding feature. Figure: 6. Capacitor start motor (a) C o n n e c t i o n (b) Phasor diagram at start (c) Speed torque curve. (c) Permanent-split capacitor motor. In this motor the auxiliary winding and capacitor are not disconnected from the motor after starting, thus the construction is simplified by the omission of the switch
Figure: 7. Permanent split capacitor motor (a) Connection (b) Torque-speed characteristic Here the auxiliary winding and capacitor could be so designed that the motor works as a perfect 2- phase motor at anyone desired load. With this the backward rotating magnetic field would be completely eliminated. The double stator frequency torque pulsations would also be eliminated, thereby the motor starts and runs as a noise free motor. With this there is improvement in p.f. and efficiency of the motor. However, the starting torque must be sacrificed as the capacitance is necessarily a compromise between the bests tarting and running characteristics. The torque-speed characteristic of the motor is shown in Fig. 7 (b). (c) Capacitor start capacitor rum motor. If two capacitors are used with the auxiliary winding as shown in Fig. 8 (a), one for starting and other during the start and run, theoretically optimum starting and running performance can both be achieved.
NUEVA VIZCAYA STATE UNIVERSITY Bambang, Nueva Vizcaya College of Engineering
IM No.:EE 106 -1SEM-202 4 -202 5 NVSU-FR-ICD-05-00 (111120) In Accordance with Section 185, Fair Use of a Copyrighted Work of Republic Act 8293, Page 7 of 15 the copy righted works included in this material may be reproduced In actual practice, the three coils form three windings distributed over several slots. These windings may be connected in star or delta and three terminations are brought out. These are conventional three phase windings which are discussed in greater detail in the chapters on alternators. Such windings are present n the stator as well as rotor Figure 1. stator of an induction machine A photograph of the stator of an induction machine is shown in fig. 1. A close up of the windings is shown in fig. 2.the several turns that makeup a coil are seen in this picture. The three terminations are connected to rings on which three brushes make a sliding contact. As the rotor rotates the brushes slip over the rings and provide means of connecting stationary external circuit elements to the rotating windings. A schematic of these arrangements is shown in fig. 8. A photograph of a wound rotor for an induction machine is shown in fig. 3 Fig. 4 shows a close up of the slip ring portion. Brushes are not shown in this picture. Induction machines, which have these kinds of windings and terminals that are brought out, are called slip ring machines. The reader may note that in order that torque is produced current must flow in the rotor. To achieve that, the stationary brush terminals must either be shorted, or connected to a circuit allowing current flow. Sometimes a star connected resistor bank is connected so that the developed starting torque is higher. There are also other forms of power electronic circuitry that may be connected to the rotor terminals to achieve various functions. The popularity of the induction machine however, stems from another variety of rotor. F igure2: Coils in the stator Figure 3: A wound rotor with slip rings
NUEVA VIZCAYA STATE UNIVERSITY Bambang, Nueva Vizcaya College of Engineering
IM No.:EE 106 -1SEM-202 4 -202 5 NVSU-FR-ICD-05-00 (111120) In Accordance with Section 185, Fair Use of a Copyrighted Work of Republic Act 8293, Page 8 of 15 the copy righted works included in this material may be reproduced Figure 4: slip rings Figure 5: Slip rings and brushes in induction machines — a schematic That is used. This rotor has slots into which copper or aluminum bars are inserted. These bars are then shorted by rings that are brazed on to each of the rotor ends. Figure 9 shows a simple schematic. Figure 6: Squirrel cage rotor — a schematic Such a rotor is called squirrel cage rotor. This rotor behaves like a short-circuited winding and hence the machine is able to perform electromechanical energy conversion. This type of rotor is easy to manufacture, has no sliding contacts and is very robust. It is this feature that makes induction machine suitable for use even in hazardous environments and reliable operation is achieved. The disadvantage of this type of rotor is that the motor behavior cannot be altered by connecting anything to the rotor — there are no rotor terminals. Fig. 7 shows a photograph of a squirrel cage rotor. The rotor also has a fan attached to it. This is for cooling purposes. The bars (white lines on the surface) are embedded in the rotor iron which forms the magnetic circuit. The white lines correspond to the visible portion of the rotor bar. Sometimes two rotor bars are used per slot to achieve some degree of variability in the starting and running performances. It is to make use of the fact that while high rotor Figure 7: squirrel cage rotor
NUEVA VIZCAYA STATE UNIVERSITY Bambang, Nueva Vizcaya College of Engineering
IM No.:EE 106 -1SEM-202 4 -202 5 NVSU-FR-ICD-05-00 (111120) In Accordance with Section 185, Fair Use of a Copyrighted Work of Republic Act 8293, Page 10 of 15 the copy righted works included in this material may be reproduced A third coil placed a further 120 °away is shown in fig. 3. This will have a time varying induced emf lagging 240 ° in time with respect to the first. When these three coils are shorted upon themselves currents flow in them as per Lenz’s law. The mechanism by which torque is produced may now be understood as follows. Positive current is said to flow in these coils when current flows out of the page in a, b, c conductors and into a′ , b′ and c′ respectively. If we look at the voltage induced in these coils as phasor, the diagram looks as shown in fig. 12. The main flux is taken as the reference phasor. Considering that the induced emf is −dψ/dt where ψ is the flux linkage, the diagram is drawn as shown. As usual, the horizontal component of these phasor gives the instantaneous values of the induced emf in these coils. Let these coils be purely resistive. Then these EMF phasor also represent the currents flowing in these coils. If we consider the instant t = 0, it can be seen that
NUEVA VIZCAYA STATE UNIVERSITY Bambang, Nueva Vizcaya College of Engineering
IM No.:EE 106 -1SEM-202 4 -202 5 NVSU-FR-ICD-05-00 (111120) In Accordance with Section 185, Fair Use of a Copyrighted Work of Republic Act 8293, Page 11 of 15 the copy righted works included in this material may be reproduced These are important conclusions. The speed of the main field is known as the synchronous speed, ns. If the actual speed of the rotor is nr then the ratio is known as slip and is frequently expressed as a percentage. Typically induction machines are designed to operate at about less than 4 percent slip at full load. It is instructive to see the situation if the rotor resistance is neglected and is considered to be purely inductive. The phasor diagram of voltages and the currents would then look as shown in fig. 7. At t = 0, one can see that current in a phase coil is at negative maximum, while b and c phases have positive current of 0.5 units. Since main flux at the coil side is close to zero, there is very little torque produced from there. There is a tendency to move due to the b′ and c coil sides, but they are in opposite directions however. Hence there is no net torque on the rotor. This brings up another important conclusion the resistance of the rotor is an important part of torque production in the induction machine. While a high resistance rotor is better suited for torque production, it would also be loss. Equivalent Circuit It is often required to make quantitative predictions about the behavior of the induction machine, under various operating conditions. For this purpose, it is convenient to represent the machine as an equivalent circuit under sinusoidal steady state operating conditions. Since the operation is balanced, a single-phase equivalent circuit is sufficient for most purposes. In order to derive the equivalent circuit, let us consider a machine with an open circuited rotor. Since no current can flow and as a consequence no torque can be produced, the situation is like a transformer open-circuited on the secondary (rotor). The equivalent circuit under this condition can be drawn as shown in fig. 11. Figure 11: Induction machine with the rotor open This is just the normal transformer equivalent circuit (why?). Measurements are generally made on the stator side and the rotor, in most circumstances, is shorted (if required, through some external circuitry). Since most of the electrical interaction is from the stator, it makes sense to refer all parameters to the stator. Let us consider the rotor to be shorted. Let the steady speed attained by the rotor be ωr and the synchronous speed be ωs. The induced voltage on the rotor is now proportional to the slip i.e., slip times the induced voltage under open circuit (why? ). Further, the voltage induced and the current that flows in the rotor is at a frequency equal to slip times the stator excitation frequency (why? ). The equivalent circuit can be made to represent this by shorting the secondary side and is shown in fig. 18. Rr ′ and Xlr ′ refer to the rotor resistance and leakage resistance referred to the stator side (using the square of the turns ratio, as is done in transformer). The secondary side loop is excited by a voltage sE 1 , which is also at a frequency sf 1. This is the reason why the rotor leakage is sXlr ′ now. This is then the per-phase equivalent circuit of the induction machine, also called as exact equivalent circuit. Note that the voltage coming across the magnetizing branch is the applied stator voltage, reduced by the stator impedance drop. Generally the
NUEVA VIZCAYA STATE UNIVERSITY Bambang, Nueva Vizcaya College of Engineering
IM No.:EE 106 -1SEM-202 4 -202 5 NVSU-FR-ICD-05-00 (111120) In Accordance with Section 185, Fair Use of a Copyrighted Work of Republic Act 8293, Page 13 of 15 the copy righted works included in this material may be reproduced Rr ′ is the rotor copper loss. Rr^ ′^ (1^ −^ s)/s^ is^ the^ mechanical^ output. In an ideal case where there are no mechanical losses, the last term would represent the actual output available at the shaft. Out of the power Pg Transferred at the air gap, a fraction s is dissipated in the rotor and (1 − s) is delivered as output at the shaft. If there are no mechanical losses like friction and windage, this represents the power available to the load. Determination of Circuit Parameters In order to find values for the various elements of the equivalent circuit, tests must be conducted on a particular machine, which is to be represented by the equivalent circuit. In order to do this, we note the following.
Copper^ loss^ in^ the^ stator^ (PSCL)^ =^ I 1 2 R 1 Copper loss in the rotor (PRCL) = I 2 2 R 2 Core loss (Pcore) Mechanical power loss due to friction and windage
NUEVA VIZCAYA STATE UNIVERSITY Bambang, Nueva Vizcaya College of Engineering
IM No.:EE 106 -1SEM-202 4 -202 5 NVSU-FR-ICD-05-00 (111120) In Accordance with Section 185, Fair Use of a Copyrighted Work of Republic Act 8293, Page 14 of 15 the copy righted works included in this material may be reproduced How these powers flow in the motor? Power
2 2 2 1 2 1
RCL AG in SCL core SCL
m
Attributes 5 3 2 1 Focus and Details There is one clear, well focused topic. Main ideas are clear and are well supported by detailed and accurate information. There is one clear, well focused topic. main ideas are clear but are not well supported by detailed information. There is one topic. main ideas are somewhat clear. The topic and main ideas are not clear. Organization The introduction states the main topic, and provides overview of the paper. information is relevant and presented in a logical order. the conclusion is strong. The introduction states the main topic, and provides overview of the paper. The conclusion is included. The introduction states the main topic. the conclusion is included. There is no clear introduction, structure or conclusion.
1 : s : 1 - s