
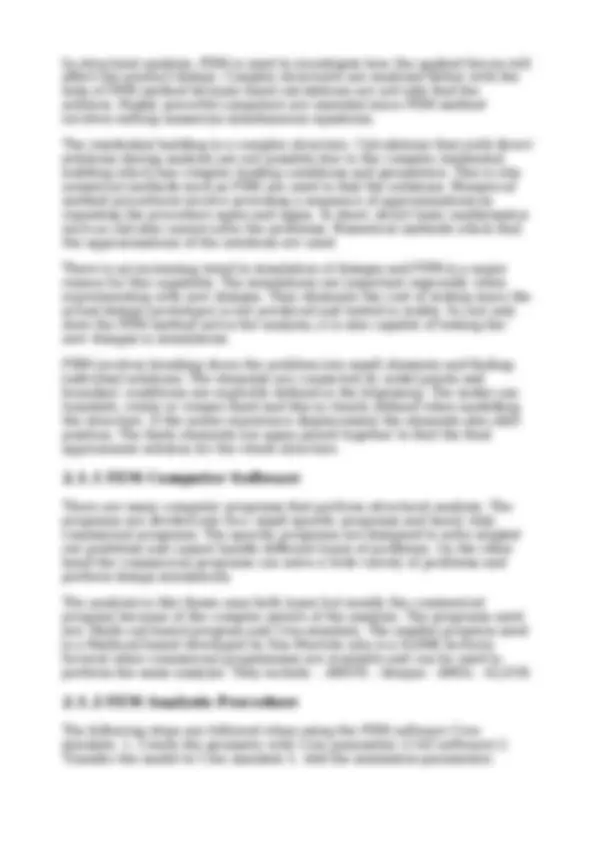
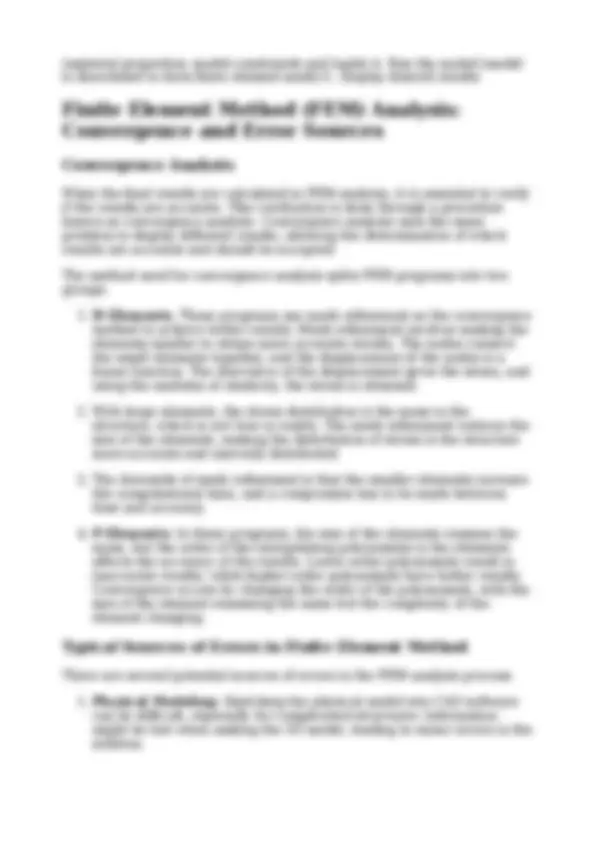
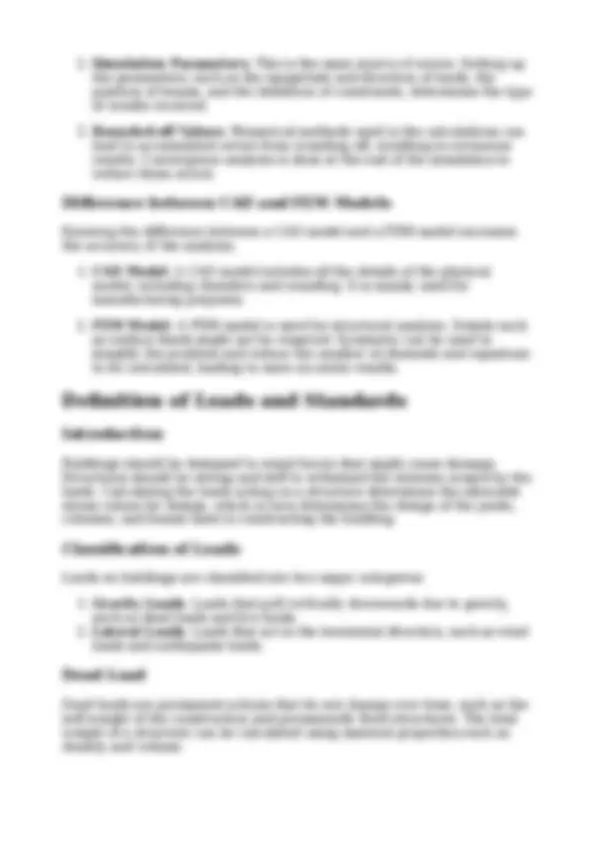
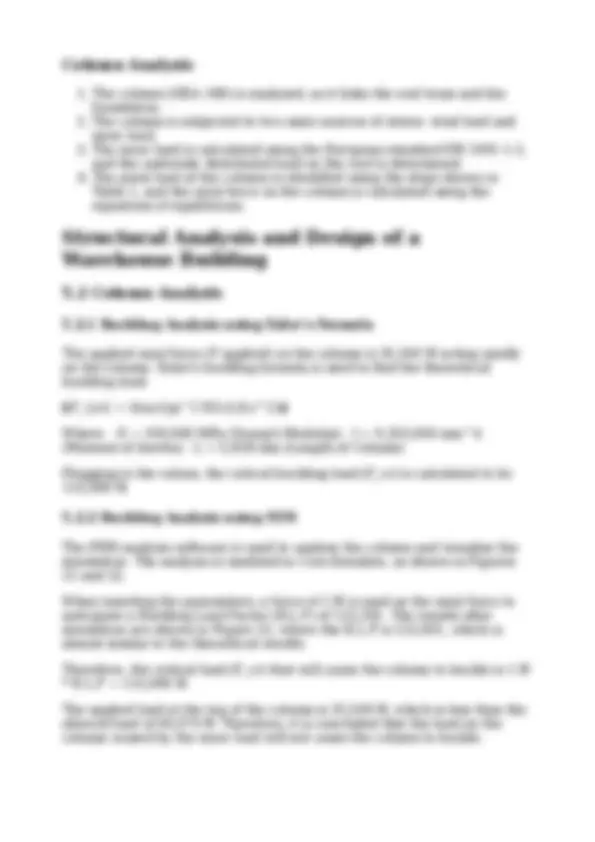
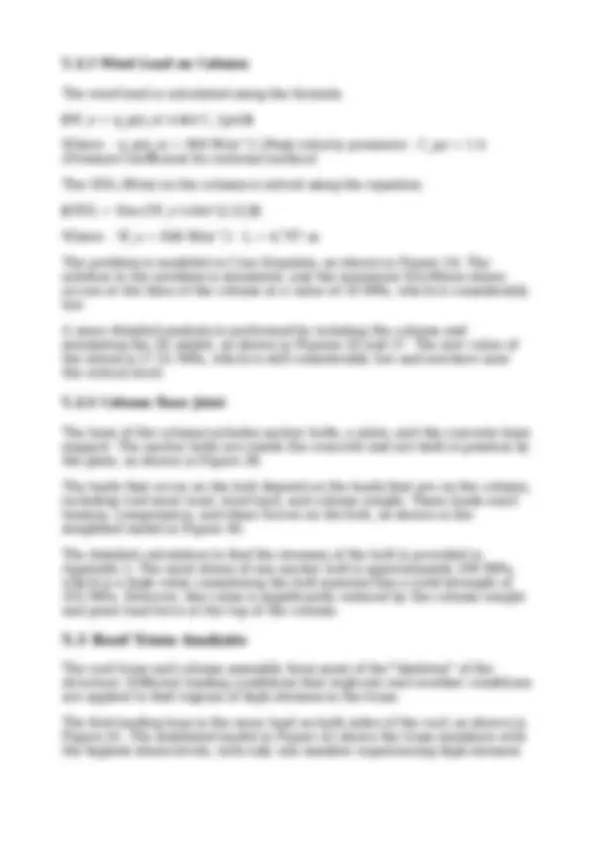
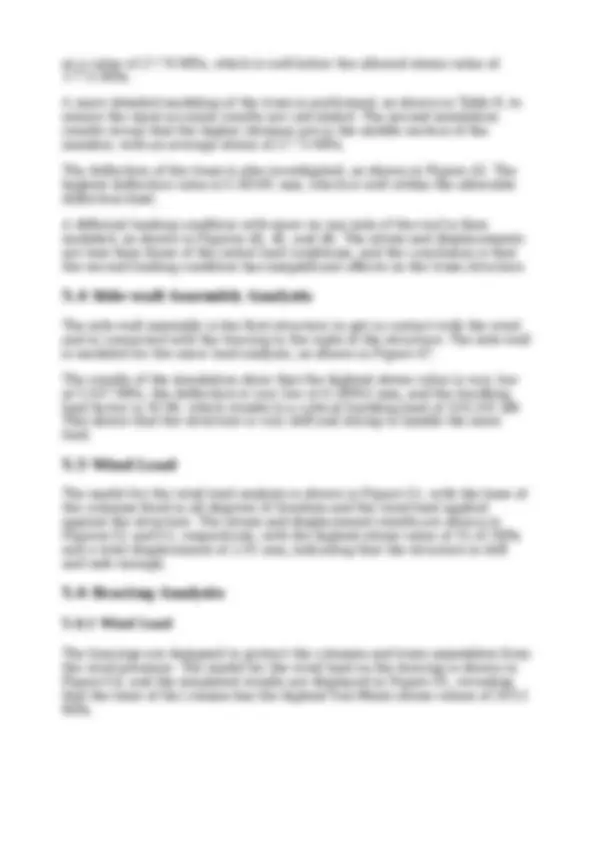
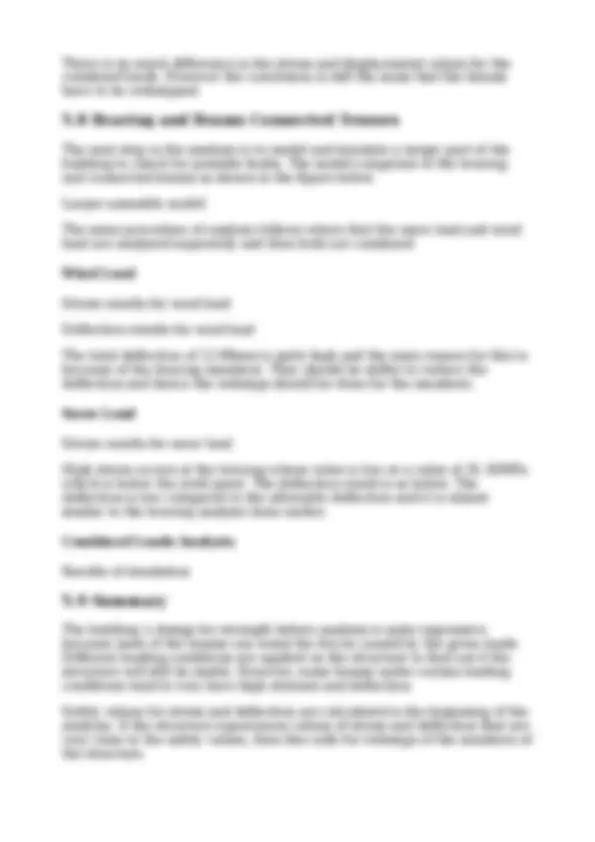
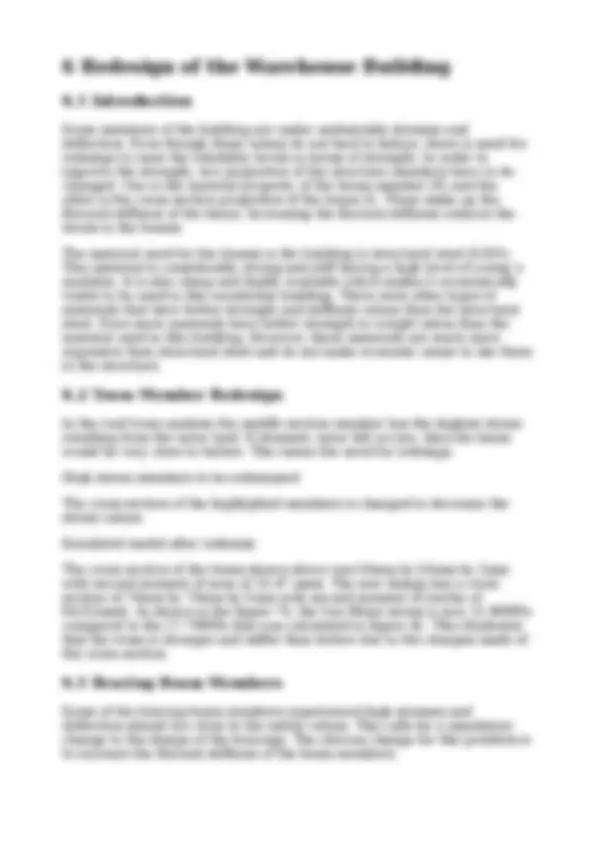
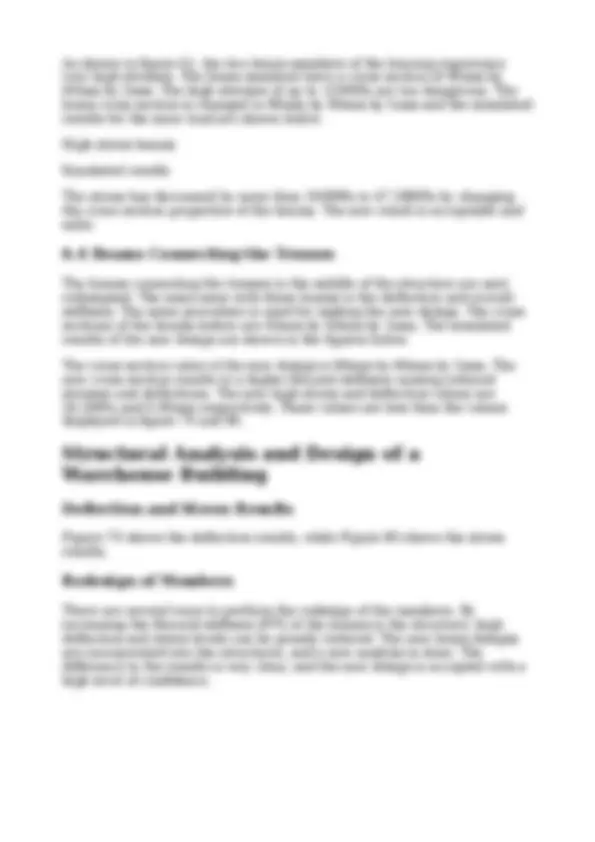
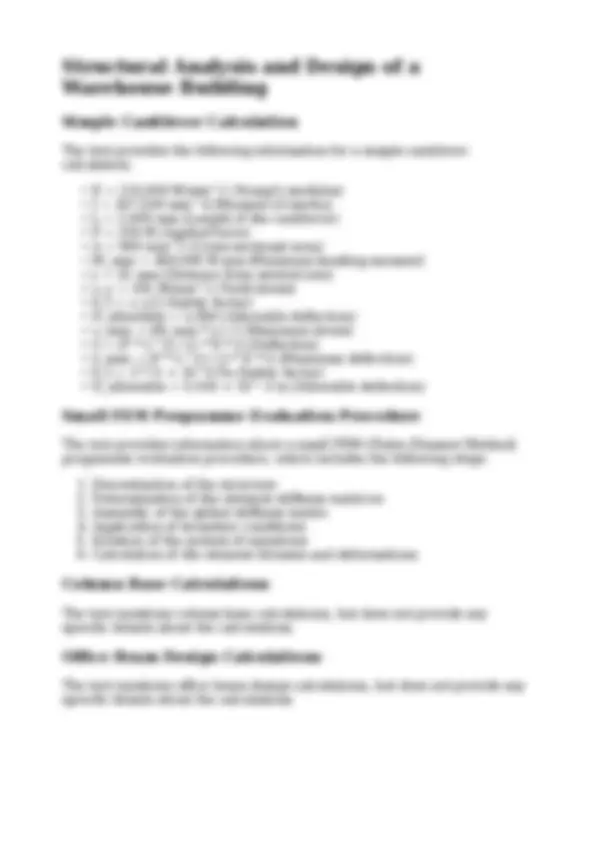
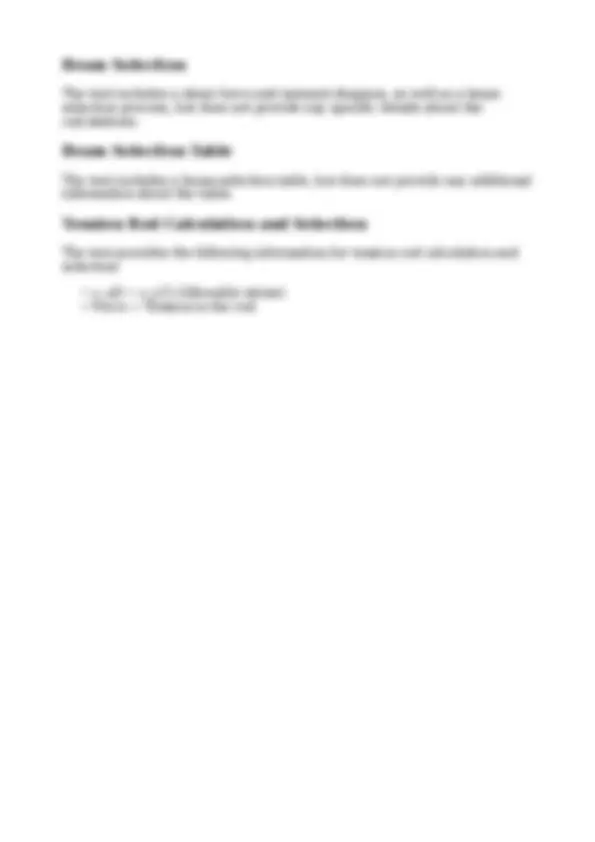
Study with the several resources on Docsity
Earn points by helping other students or get them with a premium plan
Prepare for your exams
Study with the several resources on Docsity
Earn points to download
Earn points by helping other students or get them with a premium plan
Community
Ask the community for help and clear up your study doubts
Discover the best universities in your country according to Docsity users
Free resources
Download our free guides on studying techniques, anxiety management strategies, and thesis advice from Docsity tutors
A comprehensive guide to finite element method (fem) analysis in structural engineering. It covers key concepts, applications, and practical examples, including convergence analysis, error sources, load classification, and buckling analysis. The document also explores the use of fem software for structural analysis and provides insights into the redesign of warehouse buildings based on fem results.
Typology: Summaries
1 / 19
This page cannot be seen from the preview
Don't miss anything!
The objective of the thesis is to improve the design of a warehouse building. Structural analysis is important as the reliability of the structure is investigated. Can the building withstand the loading conditions? That is the question asked during most of the analysis. The structural analysis is essential since it identifies the critical parts that need special attention. Furthermore, the analysis helps to understand the design of the structure in more detail. Every part of the structure has a purpose and this should be identified before any adjustments are made.
The structure to be analysed is a warehouse building used to store farming equipment and products. The building experiences a lot of stresses in different parts due to various loading conditions. It is not practical to analyse the building as a whole. For more detailed information, the structure is broken down to different smaller parts for easier examination. Also, different parts of the building serve more important roles than others. In this thesis the roof truss, column support and joints are assumed to be the most crucial parts.
Loads act on a structure in many directions. Sometimes the load acts alone and sometimes simultaneously. Worst case loading conditions which result into the highest stresses are used to analyse the building. Parts of the structure that experience high Von-Mises stresses or high buckling are isolated for further analysis.
Engineering principles mainly used in this analysis derives knowledge from the following topics: - Statics - Strength of materials - Machine elements - Material selection - Finite element method for mechanical engineers
The new designs are later introduced to the analysis to check if the high stresses are reduced. Redesigning the members is an important part of the analysis. In addition to the redesign, a new office structure is designed from a concept idea to a real structure. The new structure is an office for the warehouse manager.
The method of analysis used is highly crucial since the results almost entirely depend on the procedure used to examine the structure. It is for that reason that finite element method (FEM) is used for this entire analysis.
This method is a convenient and faster way to carry out the structural analysis. Individual drawings of the structures to be analysed are modelled in the software to replicate the real structure. The forces and constraints are also modelled in the software.
Modelling involves replicating the drawing in the computer software. The most important information in the models include: beam cross section properties, forces and constraints (boundary conditions) of the structure. However, caution is exercised during this process since inaccurate modelling of the structures in the software can lead to accumulated errors.
The next step is to simulate the model to find out the results. Results show the Von-Mises stresses, buckling and displacements of the model. The regions with red indicate high stresses or displacements while the blue ones show low stresses or displacements.
The process of analysis is not straight forward even with the help of highly advanced computer software. The two main challenges anticipated are maintaining high accuracy and consistency in the procedures. If not careful, very bizarre results and conclusions are obtained. A familiar saying used when using computer software "garbage in garbage out" should be always remembered. It is highly important that the level of accuracy remains at a high level throughout the thesis. As mentioned before, accumulated errors lead to inaccurate results and wrong designs.
There are many situations that can lead to wrong data being used for the analysis. For example during modelling some details might be omitted from the drawings which affect the final results. Simple strength of materials calculations help to improve the accuracy levels. The results should be reasonable to increase the confidence levels. The method of solving problems should be the same throughout the analysis because it is then easier to compare results and designs. Avoiding errors and having a good consistency is important during this thesis work.
2 THE FINITE ELEMENT METHOD
Physical problems exist in different categories of engineering for example; solid and fluid mechanics, electronics, dynamics and thermodynamics. Numerical analysis is a technique used by engineers to solve differential equations which best describe the physical models. Finite element method (FEM) is an example of a numerical technique that is used to solve the physical problems. FEM analysis can be used in many fields. Some of the fields include: - Structural analysis (stress, strain, buckling and modal) - Temperature analysis - Magnetic and electrical analysis - Crush simulations - Connected problems (wind load on a building causing deflections)
(material properties, model constraints and loads) 4. Run the model (model is discretized to form finite element mesh) 5. Display desired results
Finite Element Method (FEM) Analysis:
Convergence and Error Sources
When the final results are calculated in FEM analysis, it is essential to verify if the results are accurate. This verification is done through a procedure known as convergence analysis. Convergence analysis uses the same problem to display different results, allowing the determination of which results are accurate and should be accepted.
The method used for convergence analysis splits FEM programs into two groups:
H-Elements : These programs use mesh refinement as the convergence method to achieve better results. Mesh refinement involves making the elements smaller to obtain more accurate results. The nodes connect the small elements together, and the displacement of the nodes is a linear function. The derivative of the displacement gives the strain, and using the modulus of elasticity, the stress is obtained.
With large elements, the stress distribution is the same in the structure, which is not true in reality. The mesh refinement reduces the size of the elements, making the distribution of stress in the structure more accurate and unevenly distributed.
The downside of mesh refinement is that the smaller elements increase the computational time, and a compromise has to be made between time and accuracy.
P-Elements : In these programs, the size of the elements remains the same, but the order of the interpolating polynomials in the elements affects the accuracy of the results. Lower-order polynomials result in inaccurate results, while higher-order polynomials have better results. Convergence occurs by changing the order of the polynomials, with the size of the element remaining the same but the complexity of the element changing.
There are several potential sources of errors in the FEM analysis process:
Physical Modeling : Sketching the physical model into CAD software can be difficult, especially for complicated structures. Information might be lost when making the 3D model, leading to minor errors in the solution.
Simulation Parameters : This is the main source of errors. Setting up the parameters, such as the magnitude and direction of loads, the position of beams, and the definition of constraints, determines the type of results received.
Rounded-off Values : Numerical methods used in the calculations can lead to accumulated errors from rounding off, resulting in erroneous results. Convergence analysis is done at the end of the simulation to reduce these errors.
Knowing the difference between a CAD model and a FEM model increases the accuracy of the analysis:
CAD Model : A CAD model includes all the details of the physical model, including chamfers and rounding. It is mainly used for manufacturing purposes.
FEM Model : A FEM model is used for structural analysis. Details such as surface finish might not be required. Symmetry can be used to simplify the problem and reduce the number of elements and equations to be calculated, leading to more accurate results.
Definition of Loads and Standards
Buildings should be designed to resist forces that might cause damage. Structures should be strong and stiff to withstand the stresses caused by the loads. Calculating the loads acting on a structure determines the allowable stress values for design, which in turn determines the design of the joints, columns, and beams used in constructing the building.
Loads on buildings are classified into two major categories:
Gravity Loads : Loads that pull vertically downwards due to gravity, such as dead loads and live loads. Lateral Loads : Loads that act in the horizontal direction, such as wind loads and earthquake loads.
Dead loads are permanent actions that do not change over time, such as the self-weight of the construction and permanently fixed structures. The total weight of a structure can be calculated using material properties such as density and volume.
To convert a line load to a point load, the equation used is: Line load (kN/m) * Length / 2 = Point load (kN)
Table 1 demonstrates the step-by-step process of converting a line load to a point load, including the use of free body diagrams and equations of equilibrium.
The text then provides two simple demonstrations of the Finite Element Method (FEM) analysis procedure:
Cantilever Beam
The physical problem is a cantilever beam made of structural steel (S355) with a point force at one end. Hand calculations are performed to determine the maximum stress, deflection, allowable deflection, and allowed stress. The beam is then modeled in Creo-Parametric and analyzed using Creo- Simulate (the FEM software). The results from the FEM analysis are compared to the hand calculations, showing good agreement. The FEM software provides additional advantages, such as displaying stress and displacement results for all sections of the cantilever and easier modification of the cross-section dimensions.
Simple Truss Analysis
A simple truss structure with five elements and four nodes is analyzed using a dedicated 2D FEM software. The truss is also idealized as beam members and analyzed using Creo- Simulate. The results from the two approaches are compared, showing very similar stress values for the truss elements.
The text then describes the analysis of a warehouse building, focusing on the "skeleton" part, which includes the truss-column assembly, beams, bracings, and joints.
The building is modeled in a CAD software, and the analysis starts by simplifying the structure to a 2D view, followed by a 3D analysis. The elements are joined by nodes, and each element has defined geometric properties. Constraints and loads are applied to the model, and the simulation is run. Convergence analysis is performed to estimate the errors in the simulation, and the results are critically reviewed.
The column (HEA-180) is analyzed, as it links the roof truss and the foundation. The column is subjected to two main sources of stress: wind load and snow load. The snow load is calculated using the European standard EN 1991-1-3, and the uniformly distributed load on the roof is determined. The point load at the column is identified using the steps shown in Table 1, and the axial force on the column is calculated using the equations of equilibrium.
Structural Analysis and Design of a
Warehouse Building
5.2.1 Buckling Analysis using Euler's Formula
The applied axial force (P applied) on the column is 35,500 N acting axially on the column. Euler's buckling formula is used to find the theoretical buckling load:
$P_{cr} = \frac{\pi^2 EI}{(2L)^2}$
Where: - E = 200,000 MPa (Young's Modulus) - I = 9,250,000 mm^ (Moment of Inertia) - L = 5,838 mm (Length of Column)
Plugging in the values, the critical buckling load (P_cr) is calculated to be 133,900 N.
5.2.2 Buckling Analysis using FEM
The FEM analysis software is used to analyze the column and visualize the simulation. The analysis is modeled in Creo-Simulate, as shown in Figures 31 and 32.
When inserting the parameters, a force of 1 N is used as the axial force to anticipate a Buckling Load Factor (B.L.F) of 133,392. The results after simulation are shown in Figure 33, where the B.L.F is 133,661, which is almost similar to the theoretical results.
Therefore, the critical load (P_cr) that will cause the column to buckle is 1 N
The applied load at the top of the column is 35,500 N, which is less than the allowed load of 66,970 N. Therefore, it is concluded that the load on the column caused by the snow load will not cause the column to buckle.
at a value of 27.76 MPa, which is well below the allowed stress value of 177.5 MPa.
A more detailed modeling of the truss is performed, as shown in Table 8, to ensure the most accurate results are calculated. The second simulation results reveal that the higher stresses are in the middle section of the member, with an average stress of 27.73 MPa.
The deflection of the truss is also investigated, as shown in Figure 43. The highest deflection value is 5.58181 mm, which is well within the allowable deflection limit.
A different loading condition with snow on one side of the roof is then modeled, as shown in Figures 44, 45, and 46. The stress and displacements are less than those of the initial load conditions, and the conclusion is that the second loading condition has insignificant effects on the truss structure.
The side-wall assembly is the first structure to get in contact with the wind and is connected with the bracing to the right of the structure. The side-wall is modeled for the snow load analysis, as shown in Figure 47.
The results of the simulation show that the highest stress value is very low at 5.507 MPa, the deflection is very low at 0.28953 mm, and the buckling load factor is 16.96, which results in a critical buckling load of 156.201 kN. This shows that the structure is very stiff and strong to handle the snow load.
The model for the wind load analysis is shown in Figure 51, with the base of the columns fixed in all degrees of freedom and the wind load applied against the structure. The stress and displacement results are shown in Figures 52 and 53, respectively, with the highest stress value of 15.41 MPa and a total displacement of 2.91 mm, indicating that the structure is stiff and safe enough.
5.6.1 Wind Load
The bracings are designed to protect the columns and truss assemblies from the wind pressure. The model for the wind load on the bracing is shown in Figure 54, and the simulated results are displayed in Figure 55, revealing that the base of the column has the highest Von-Mises stress values of 39. MPa.
Structural Analysis and Design of a
Warehouse Building
The following simulation tests if the bracing is strong enough for the snow load. The members of the bracing should be stiff enough to resist the snow load.
The highest stress occurs at the joints of the bracings as shown. The value is 125.3MPa which is less than the safety stress value. Therefore, some of the members might require modification if higher snow loading conditions are anticipated. Snow loads might lead to deflection of the bracings. Therefore, the simulation of the displacements is necessary.
The same members that are under high stress in the figure 57 are the same members with high deflection values. The highest deflection value is 32.1601mm which is less than the safety value but still very close. Clearly, the parts of the bracing need to be redesigned to increase the reliability of the structure.
In some extreme weather conditions, both the snow load and the wind load occur at the same time. This may lead to more stresses and deflections so that is why it is important to imitate the conditions.
There are no major changes to the stress levels of the model and the result values are similar to the snow load results on the bracing. The values for the displacement are shown below.
As shown above the model for the displacement is very different from the one with the snow load or wind load. However, the same bracing member that was under high deflection is still the same. This time around the value of the displacement is 41.99mm. This is a very high value and is not acceptable. The main aim of the bracing is to hold firm against wind forces. Since the bracing is deflecting at high values, this causes the truss members to deflect at higher values as well. The value of the truss deflection is 25mm which is different from the previous models.
The members that have high stresses and deflections are isolated and analysed to investigate even more about the stress distribution.
Model before simulation
Model after simulation showing stress values
Model of both loads before simulation
Model after simulation
Model showing displacement
There is no much difference in the stress and displacement values for the combined loads. However the conclusion is still the same that the beams have to be redesigned.
The next step in the analysis is to model and simulate a larger part of the building to check for possible faults. The model comprises of the bracing and connected beams as shown in the figure below.
The same procedure of analysis follows where first the snow load and wind load are analyzed separately and then both are combined.
Wind Load
The total deflection of 12.88mm is quite high and the main reason for this is because of the bracing members. They should be stiffer to reduce the deflection and hence the redesign should be done for the members.
Snow Load
High stress occurs at the bracing whose value is low at a value of 35.36MPa which is below the yield point. The deflection result is as below. The deflection is low compared to the allowable deflection and it is almost similar to the bracing analysis done earlier.
Combined Loads Analysis
The building´s design for strength before analysis is quite impressive because most of the beams can resist the forces caused by the given loads. Different loading conditions are applied on the structure to find out if the structure will still be stable. However, some beams under certain loading conditions tend to very have high stresses and deflection.
Safety values for stress and deflection are calculated in the beginning of the analysis. If the structure experiences values of stress and deflection that are very close to the safety values, then this calls for redesign of the members of the structure.
Larger assembly model
Stress results for wind load
Deflection results for wind load
Stress results for snow load
Results of simulation
6 Redesign of the Warehouse Building
Some members of the building are under undesirable stresses and deflection. Even though these values do not lead to failure, there is need for redesign to raise the reliability levels in terms of strength. In order to improve the strength, two properties of the structure members have to be changed. One is the material property of the beam member (E) and the other is the cross section properties of the beam (I). These make up the flexural stiffness of the beam. Increasing the flexural stiffness reduces the stress in the beams.
The material used for the beams in the building is structural steel (S355). This material is considerably strong and stiff having a high level of young´s modulus. It is also cheap and highly available which makes it economically viable to be used in this warehouse building. There exist other types of materials that have better strength and stiffness values than the structural steel. Even more materials have better strength to weight ratios than the material used in this building. However, these materials are much more expensive than structural steel and do not make economic sense to use them in the structure.
In the roof truss analysis the middle section member has the highest stress resulting from the snow load. If dramatic snow fall occurs, then the beam would be very close to failure. This raises the need for redesign.
The cross-section of the highlighted members is changed to decrease the stress values.
The cross section of the beam shown above was 50mm by 50mm by 3mm with second moment of area of 19.47 mm4. The new design has a cross section of 70mm by 70mm by 5mm with second moment of inertia of 84.63mm4. As shown in the figure 76, the Von Mises stress is now 12.89MPa compared to the 27.76MPa that was calculated in figure 42. This illustrates that the truss is stronger and stiffer than before due to the changes made of the cross section.
Some of the bracing beam members experienced high stresses and deflection almost too close to the safety values. This calls for a mandatory change to the design of the bracings. The obvious change for this problem is to increase the flexural stiffness of the beam members.
High stress members to be redesigned
Simulated model after redesign
New Structure (Office) in the Building
After the analysis and redesign of the building, it is concluded that the structure is strong and stiff enough to carry the given loads. The next step is to push the limits of the strength of the building by adding a new structure. The structure to be designed is an office for the warehouse manager. The office is designed to be attached to the side wall of the warehouse, as shown in Figures 81 and 82.
Main Beam Design
The first step in the design is to calculate the loads that will act on the structure. According to the Eurocode standard EN 1991-1-2:2002, this structure falls into category B, which is office areas. The pressure load for this category is 2 to 3 kN/m^2. The highest pressure load, which is 3 kN/ m^2, is chosen as the design load.
The length of the beams supporting the floor of the office from the column HEA 180 is designed to be 3 m, and the width is the distance between them, which is 4.6 m. The next step is to convert the pressure load to a line load on the beam. The line load equals the pressure load multiplied by the perpendicular distance (4.6 m), which results in 13.8 kN/m. Since there are two beams, the line load is divided by two.
Based on the calculations in Appendix 4, the needed section modulus that will be used to choose the beam is 87.46 cm^3. A beam that has a value higher than the calculated section modulus is chosen using the chart in Appendix 4. An I-beam section is preferred because of its good geometrical stiffness properties. Section IPE 160 is chosen to act as the beam at the base.
Tension Rod Design
The beam, which is connected to the column on the side wall, requires an extra support to support the weight. The tension rod is designed to reduce the stress on the beam. The tension rod is connected to the side wall column, as shown in Figure 85.
Calculations to find the exact dimensions required for the rod are in Appendix 5. It is concluded that the rod should be made of steel and have a diameter of approximately 10.00 mm.
Connecting Beams Design
The design proceeds to design middle beams, which connect the two IPE 160 beams. These beams will act as the main office floor support and are
shown in Figure 86. Detailed calculations and selection chart are in Appendix 5.
The needed section modulus for the beam is 30.197 cm^3. A rectangular beam of 100 by 60 by 6 is chosen according to the chart in Appendix 6.
To verify if the new design is strong enough to handle the loads, the new structure has to be analyzed. The analysis also shows the effect of the new design on the already existing structures.
The tension rod and main supporting beam are first analyzed to find out the effects they have on the column. The model in Creo-Simulate program is as shown in Figure 87.
A distributed load is applied on the beam, and the effects are as shown in Figure 88. The highest stress is at the bottom of column HEA 180 with a value of 86.12 MPa. This value is not very high and is therefore accepted since the strength has not reached a value higher than the yield strength.
The connecting middle beams, as shown in Figure 86, are then analyzed to check if they can support the loads. Figures 89 and 90 show the model in Creo-Simulate, and Figure 91 shows the simulated model with the deflection of the middle beams.
The highest stress value is 33.92 MPa, which is below the yield strength of the structural steel used in the building. The values are not close to the yield strength and are therefore acceptable. The highest displacement value in the middle beam is approximately 8 mm. The displacement and stress due to the applied forces on the beams are very low, leading to the conclusion that the middle beams are well designed to support the floor of the office.
The beams with the highest stresses and displacements are analyzed in more detail to achieve a higher level of confidence. The middle beam is modeled in 3D and then analyzed. Figure 92 shows the detailed model, and the middle part of the beam has the highest deflection, with a value of 5. mm.
The final 3D model of the new office design and wall is shown in Figure 93.
The new design does not compromise the strength of the already existing side wall structure. The office design is also strong enough to hold the calculated loads. The side walls, floor, roof, and interior structures will also not destabilize the office structure.
The text includes a shear force and moment diagram, as well as a beam selection process, but does not provide any specific details about the calculations.
The text includes a beam selection table, but does not provide any additional information about the table.
The text provides the following information for tension rod calculation and selection:
σ_all = σ_y/2 (Allowable stress) Force = Tension in the rod