
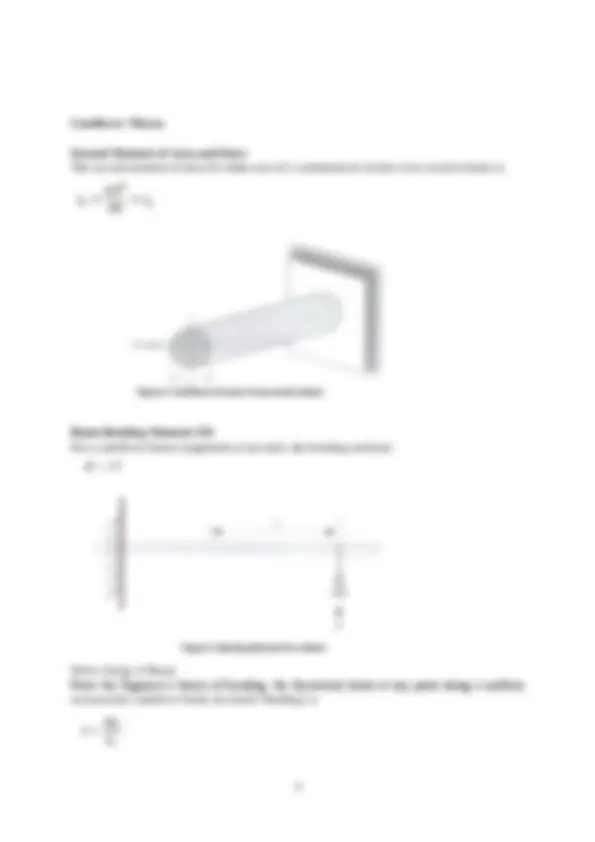
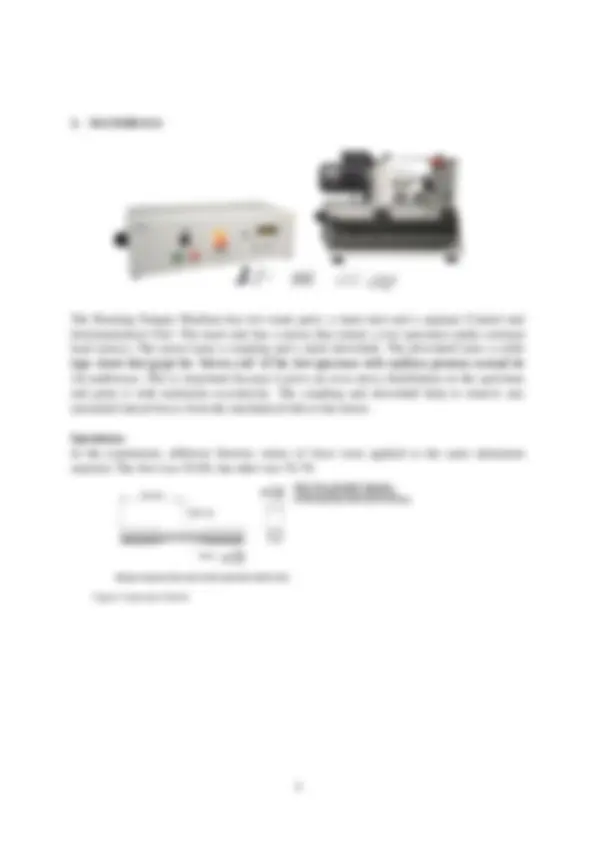
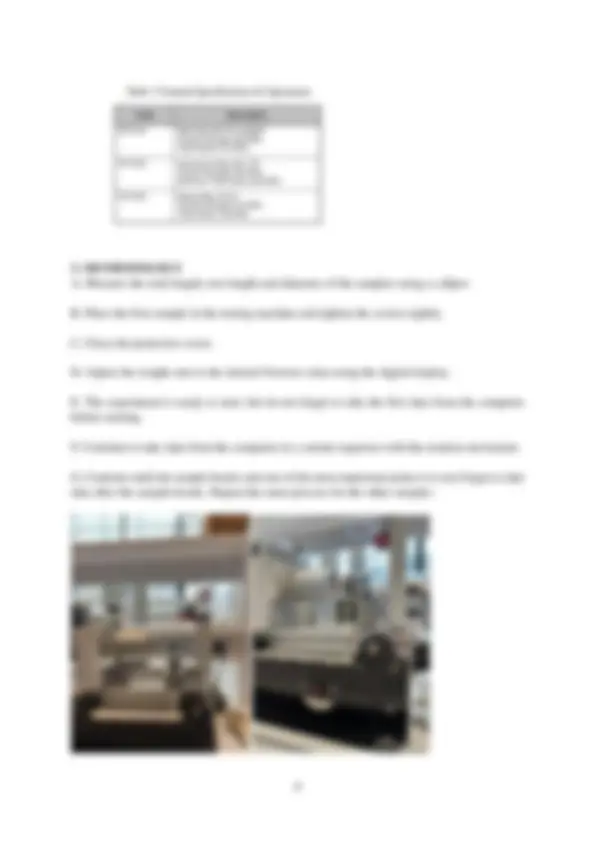
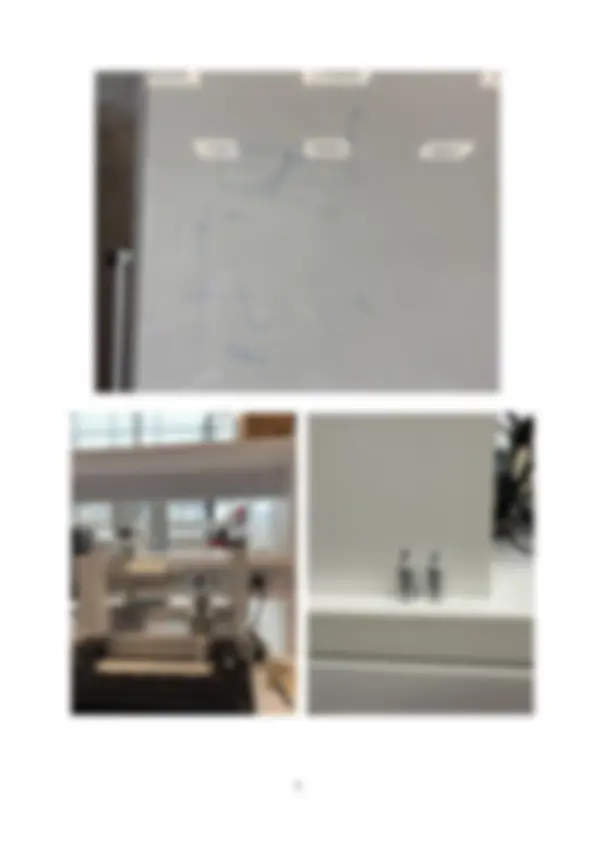
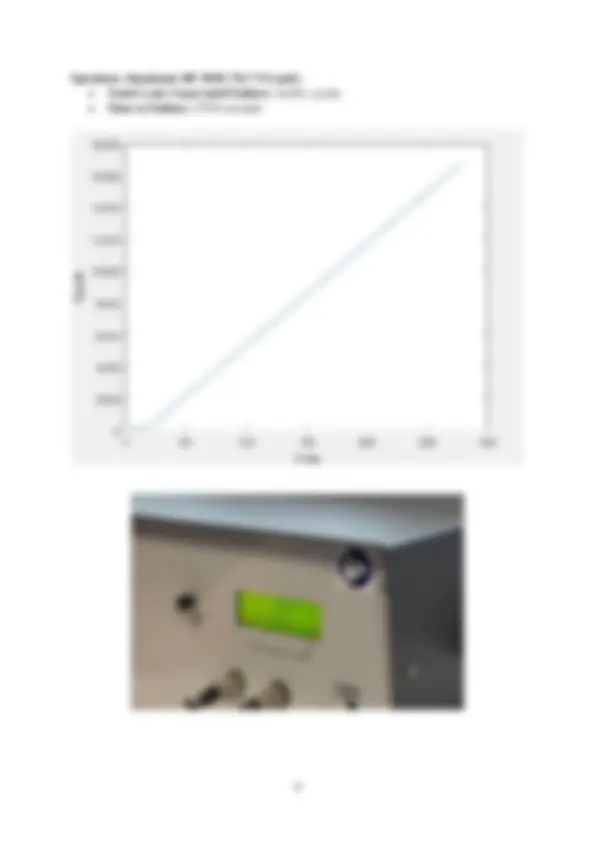
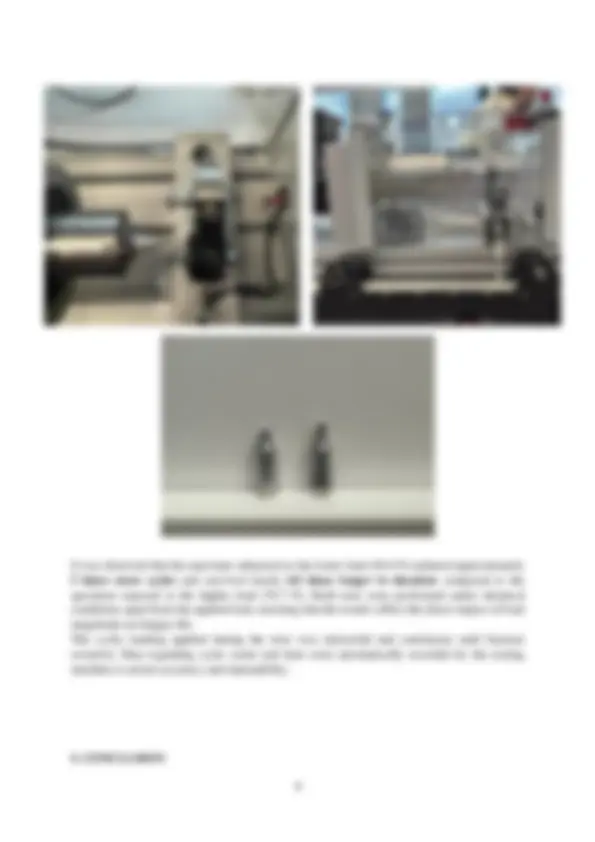
Study with the several resources on Docsity
Earn points by helping other students or get them with a premium plan
Prepare for your exams
Study with the several resources on Docsity
Earn points to download
Earn points by helping other students or get them with a premium plan
Community
Ask the community for help and clear up your study doubts
Discover the best universities in your country according to Docsity users
Free resources
Download our free guides on studying techniques, anxiety management strategies, and thesis advice from Docsity tutors
Fatigue test results and graphs under different forces applied to aluminum samples.
Typology: Study Guides, Projects, Research
1 / 11
This page cannot be seen from the preview
Don't miss anything!
Fatigue testing is a specialised form of mechanical testing that is performed by applying cyclic loading to a coupon or structure. These tests are used either to generate fatigue life and crack growth data, identify critical locations or demonstrate the safety of a structure that may be susceptible to fatigue. Fatigue tests are used on a range of components from coupons through to full size test articles such as automobiles and aircraft. Fatigue tests on coupons are typically conducted using servo hydraulic test machines which are capable of applying large variable amplitude cyclic loads. Constant amplitude testing can also be applied by simpler oscillating machines. The fatigue life of a coupon is the number of cycles it takes to break the coupon. This data can be used for creating stress-life or strain-life curves. The rate of crack growth in a coupon can also be measured, either during the test or afterward using fractography. Testing of coupons can also be carried out inside environmental chambers where the temperature, humidity and environment that may affect the rate of crack growth can be controlled. 1.1. Theory Notation
Rotating Cantilever The Rotating Fatigue Machine clamps the specimen as a cantilever (figure 1). The load on its free end creates tension on the upper half of the specimen and compression on the lower half. However, because it rotates, it has alternate compressive and tensile stress on any given part along the unsupported length of the test specimen. Figure 2 shows a cross section through the specimen as it rotates. Any fixed point on the unsupported length of the specimen moves through one cycle of compression and tension. In each cycle, the stress at that point moves from zero stress point to maximum tension (+σ), back through zero stress and to a maximum compression (-σ) point. It then moves back to zero stress and repeats the cycle. As the stress fully reverses (from positive to negative or vice versa), this is called reversal. Each cycle has two reversals. Stress ( 𝛔 ) This is the force applied to a material over a known area. Compressive stress is where the material is compressed. It has a negative value. Tensile Stress is where the material stretched. It has a positive value.
The Rotating Fatigue Machine has two main parts: a main unit and a separate Control and Instrumentation Unit. The main unit has a motor that rotates a test specimen under constant load (stress). The motor turns a coupling and a short driveshaft. The driveshaft turns a collet type chuck that grips the ‘driven end’ of the test specimen with uniform pressure around its circumference. This is important because it gives an even stress distribution on the specimen and grips it with minimum eccentricity. The coupling and driveshaft help to remove any unwanted lateral forces from the mechanical link to the motor. Specimens In the experiment, different Newton values of force were applied to the same aluminum material. The first was 59.8N, the other was 76.7N.
A. Measure the total length, test length and diameter of the samples using a caliper. B. Place the first sample in the testing machine and tighten the screws tightly. C. Close the protective cover. D. Adjust the weight arm to the desired Newton value using the digital display. E. The experiment is ready to start, but do not forget to take the first data from the computer before starting. F. Continue to take data from the computer in a certain sequence with the rotation movement. G. Continue until the sample breaks and one of the most important points is to not forget to take data after the sample breaks. Repeat the same process for the other samples.
It was observed that the specimen subjected to the lower load (56.9 N) endured approximately 5 times more cycles and survived nearly 4.8 times longer in duration compared to the specimen exposed to the higher load (76.7 N). Both tests were performed under identical conditions apart from the applied load, ensuring that the results reflect the direct impact of load magnitude on fatigue life. The cyclic loading applied during the tests was sinusoidal and continuous until fracture occurred. Data regarding cycle count and time were automatically recorded by the testing machine to ensure accuracy and repeatability. 5. CONCLUSION
The fatigue test results clearly demonstrate the inverse relationship between applied load and fatigue life in aluminum specimens. As the applied load increased from 56.9 N to 76.7 N - a 34.8% increase in force - the number of cycles to failure dropped by approximately 80.3% , and the time to failure decreased by 79.2%. This significant reduction highlights the material’s sensitivity to increased stress levels under cyclic loading conditions. These findings are consistent with fatigue theory, where higher stress levels accelerate crack initiation and propagation, leading to earlier failure. The aluminum specimens, being identical in material properties and geometry, confirm that the load magnitude is the primary factor influencing fatigue life in this experiment. In practical engineering applications, this emphasizes the importance of minimizing cyclic stress levels in aluminum components to ensure longer service life. The data also reinforce the need for conservative load design, especially in structures and components expected to experience repeated loading during their operational lifespan.