
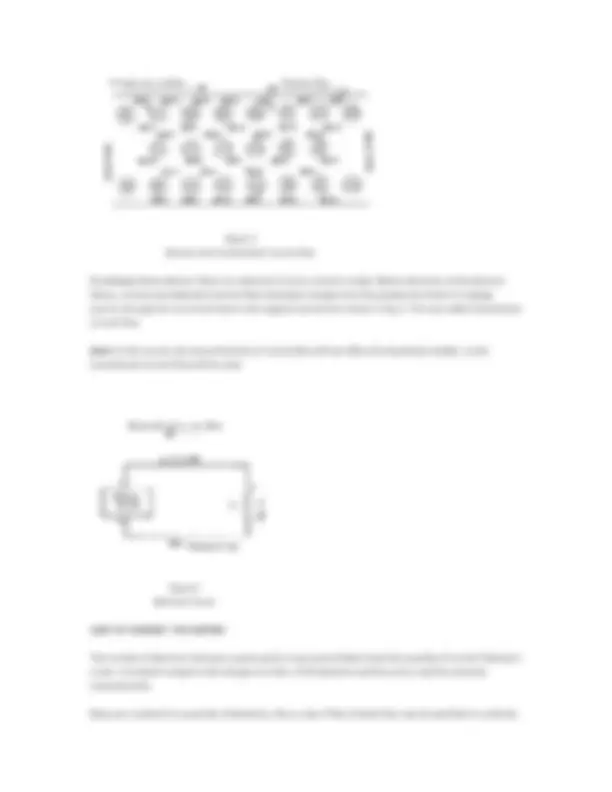
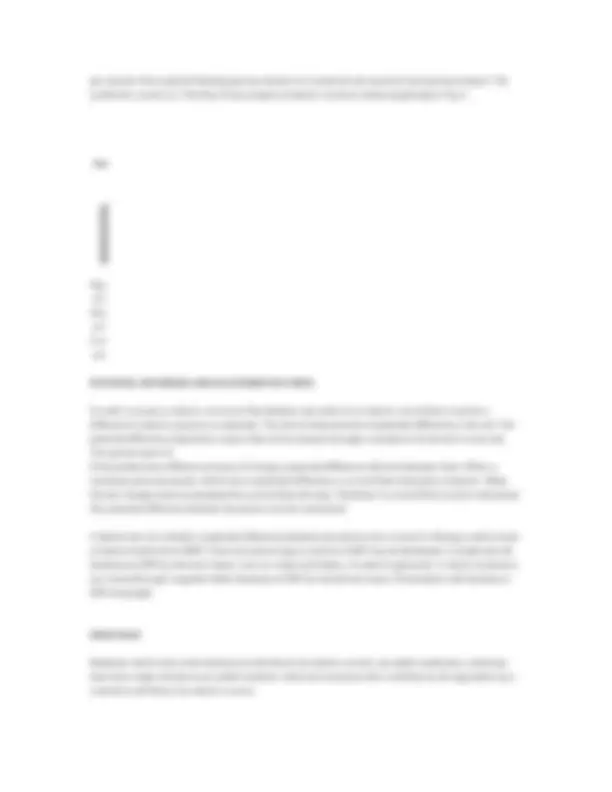

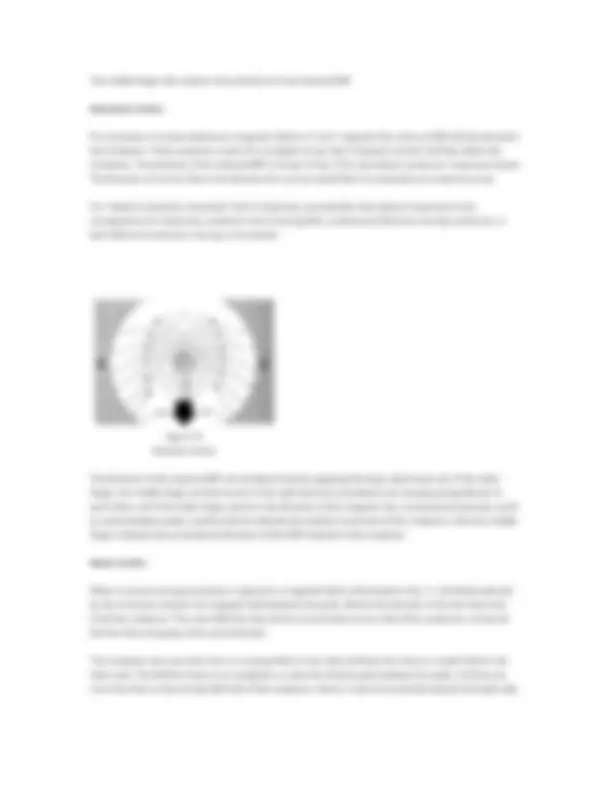
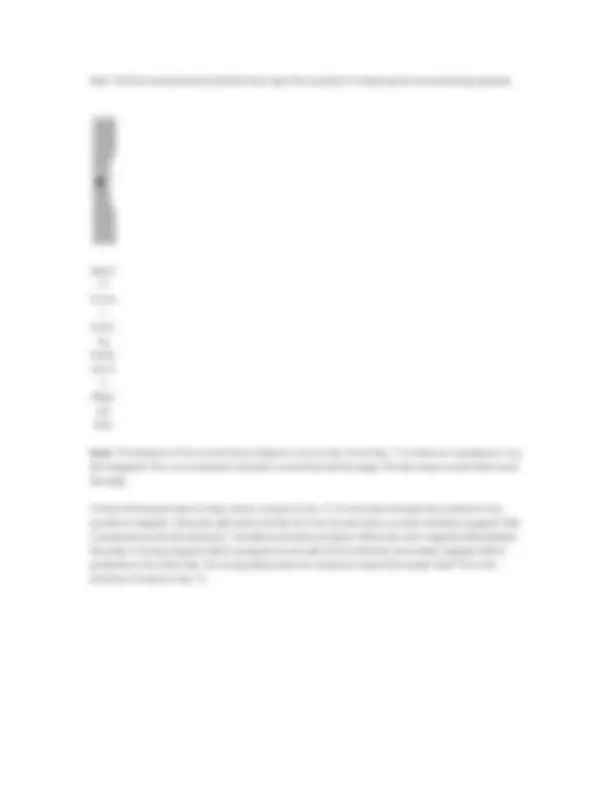
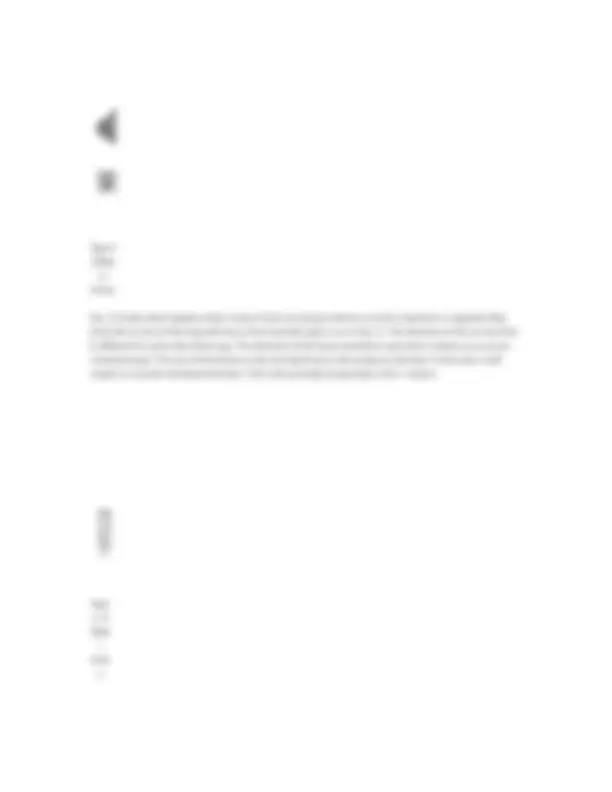
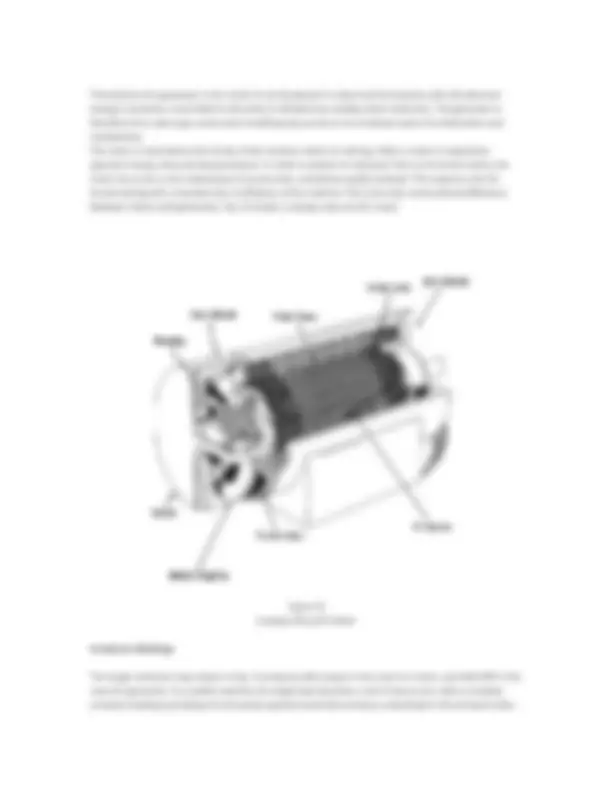
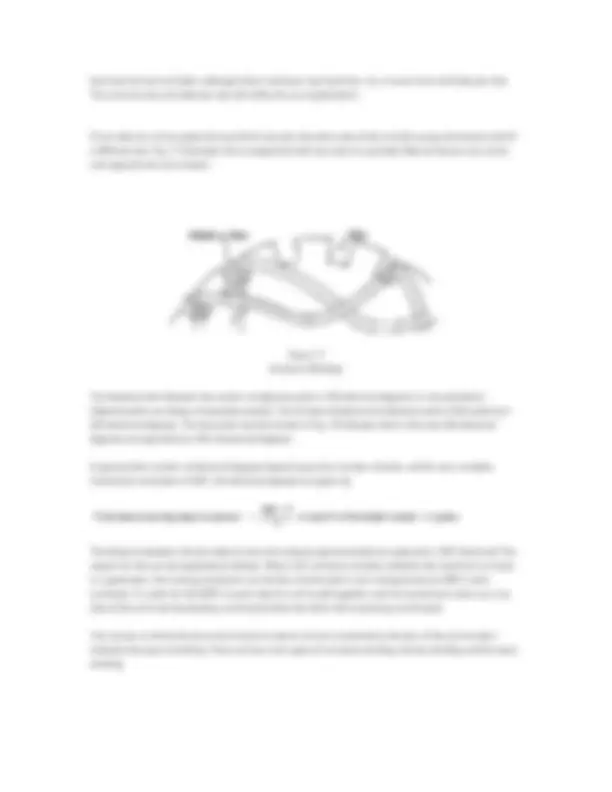
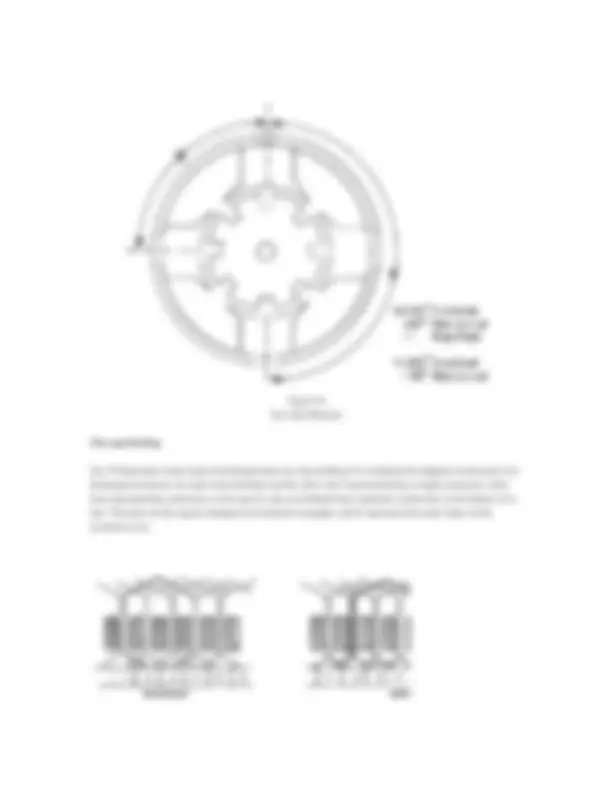
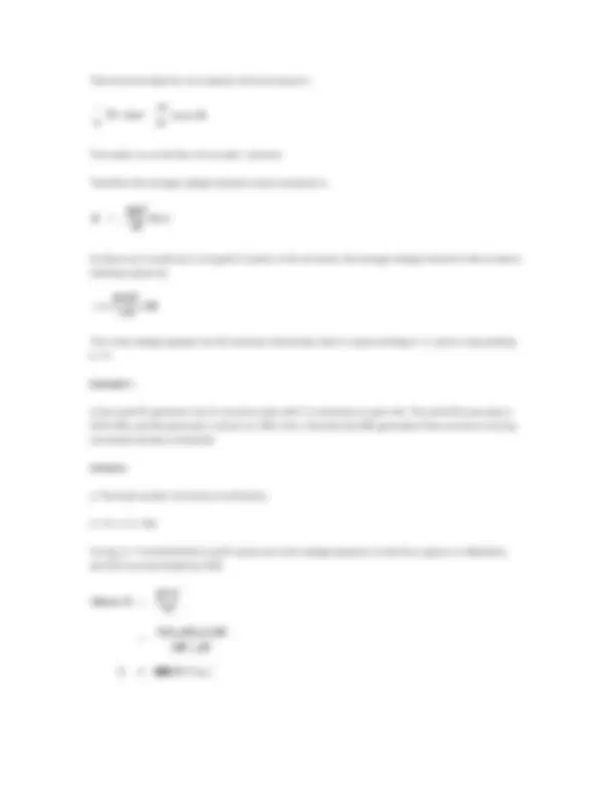
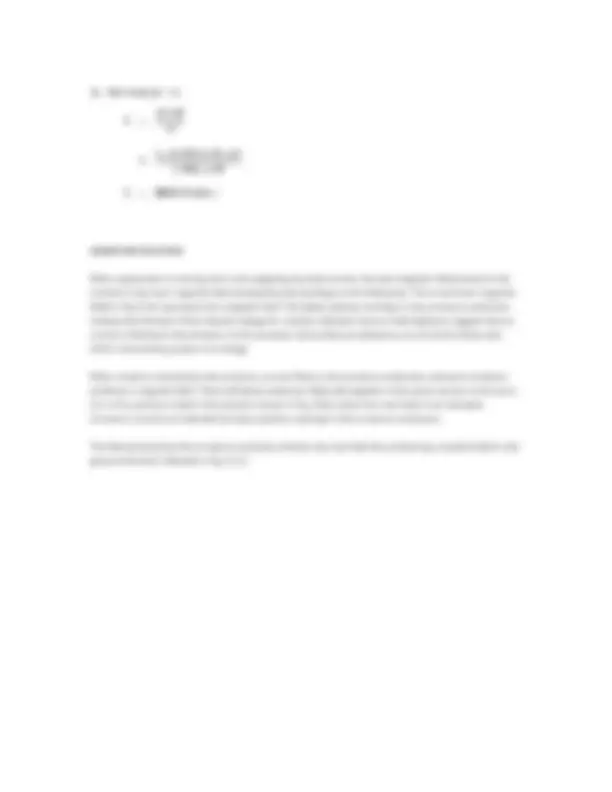
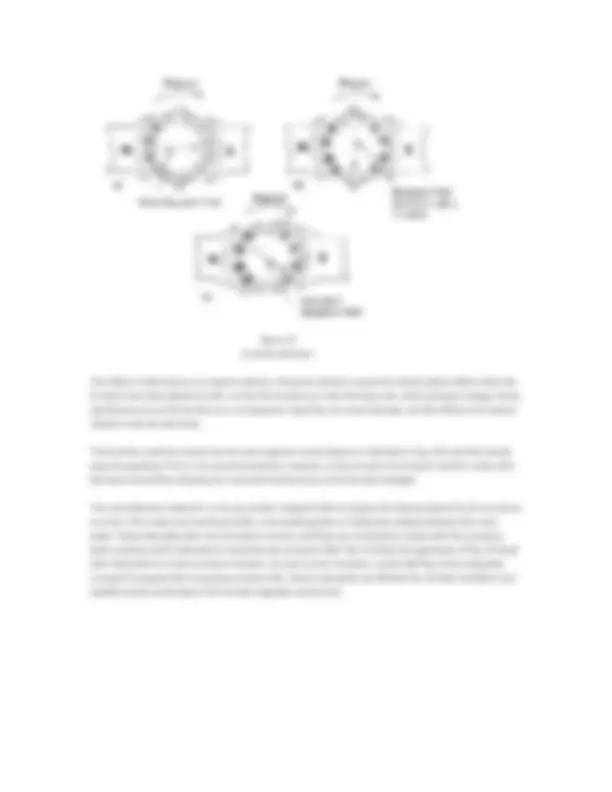
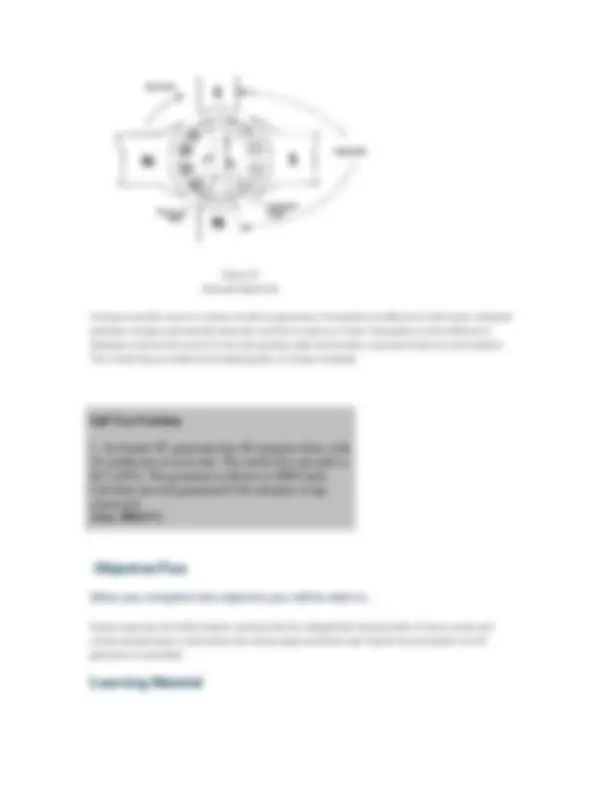
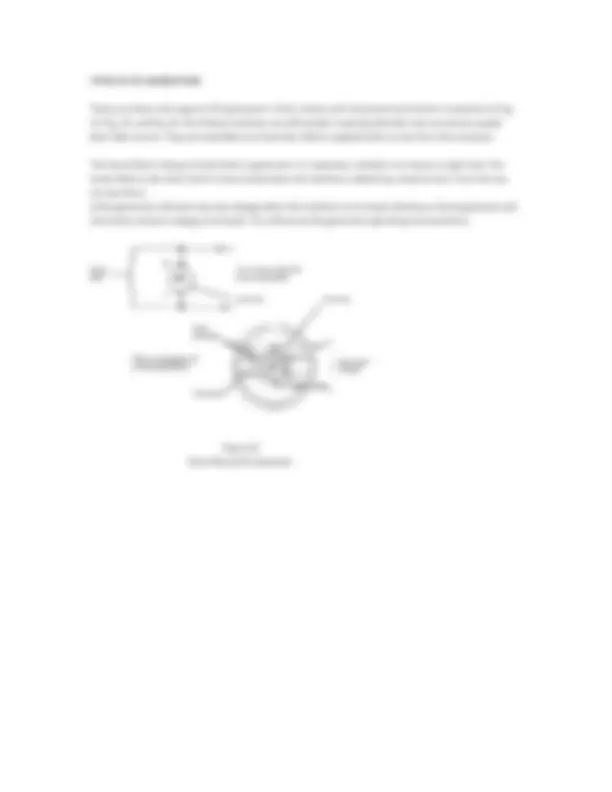
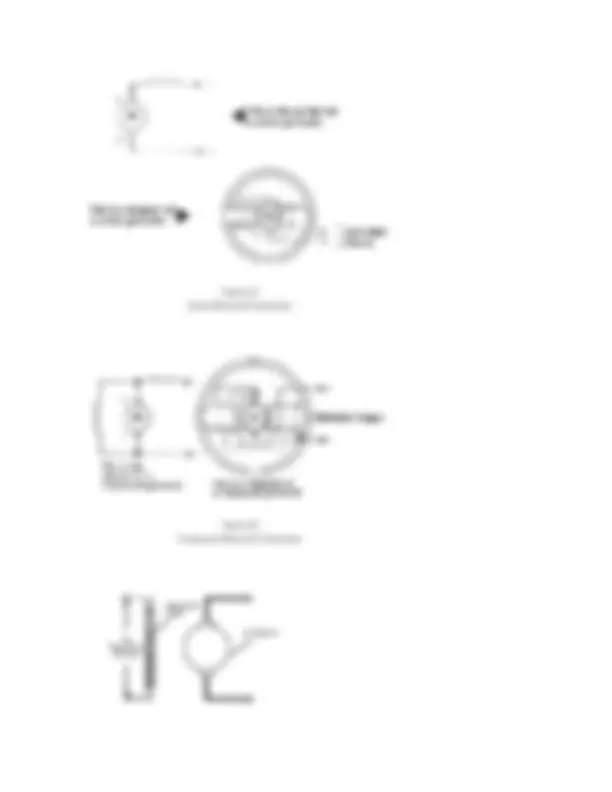
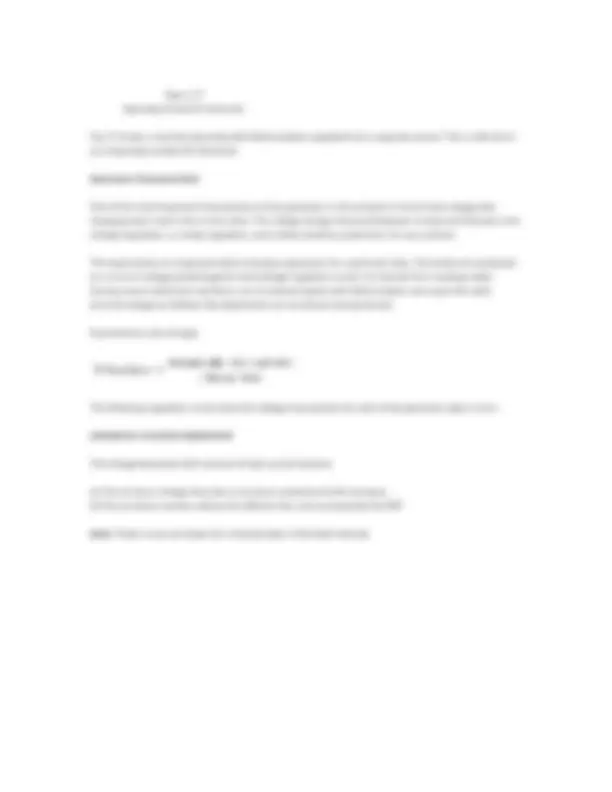
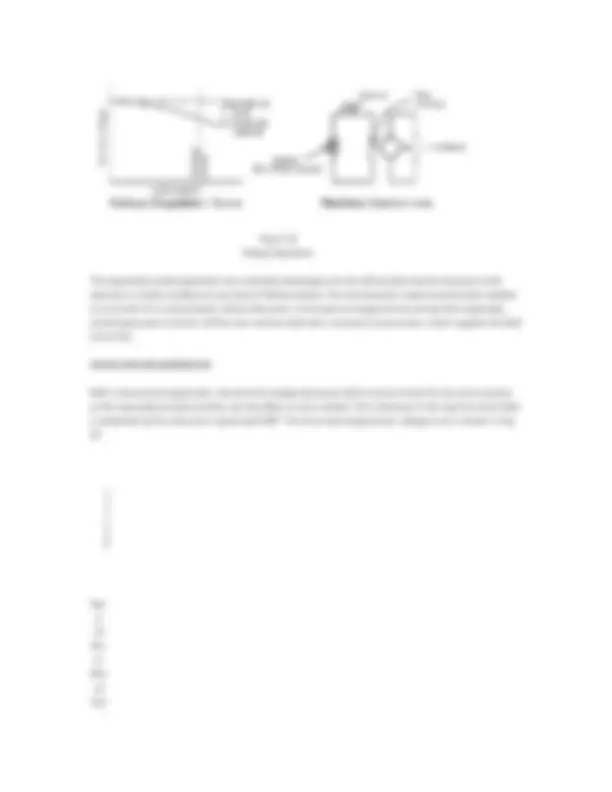
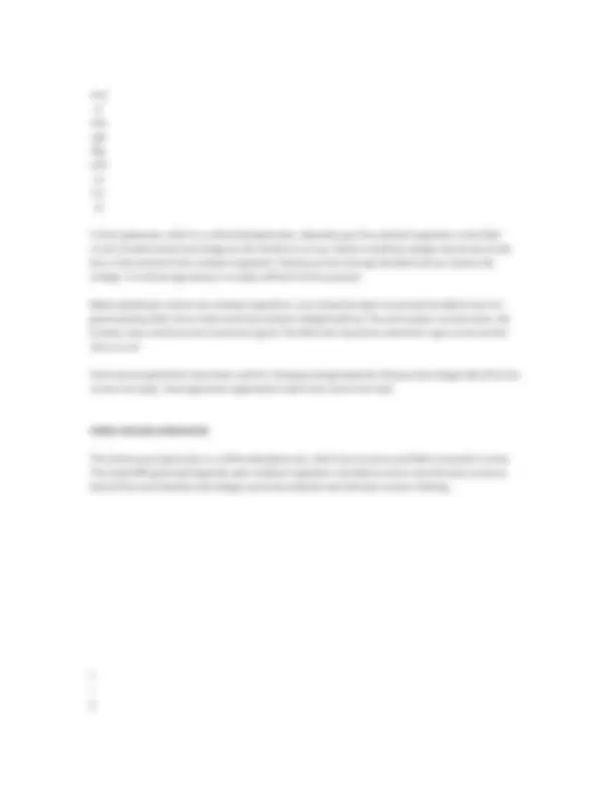
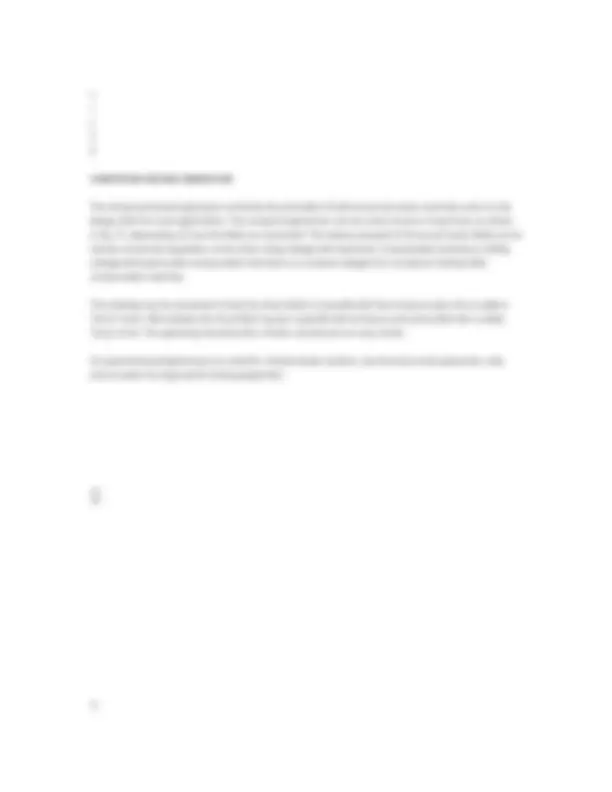
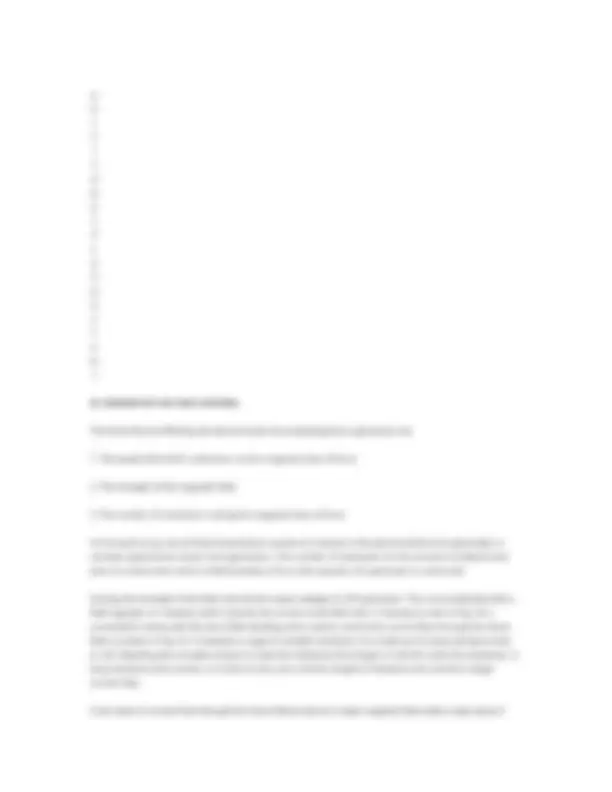
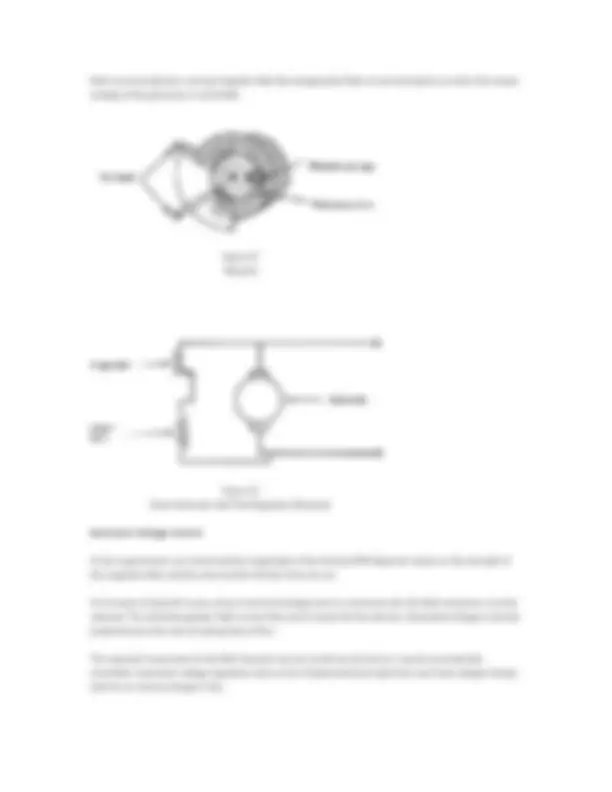
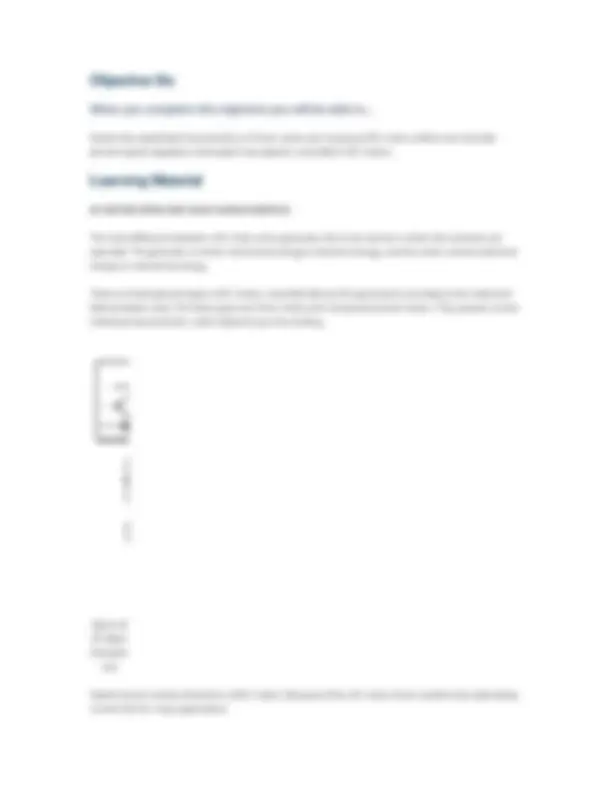
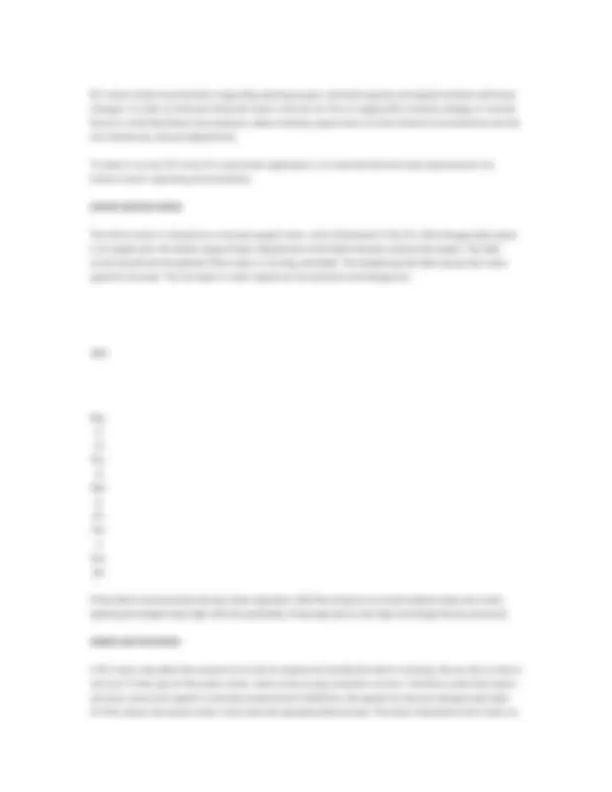
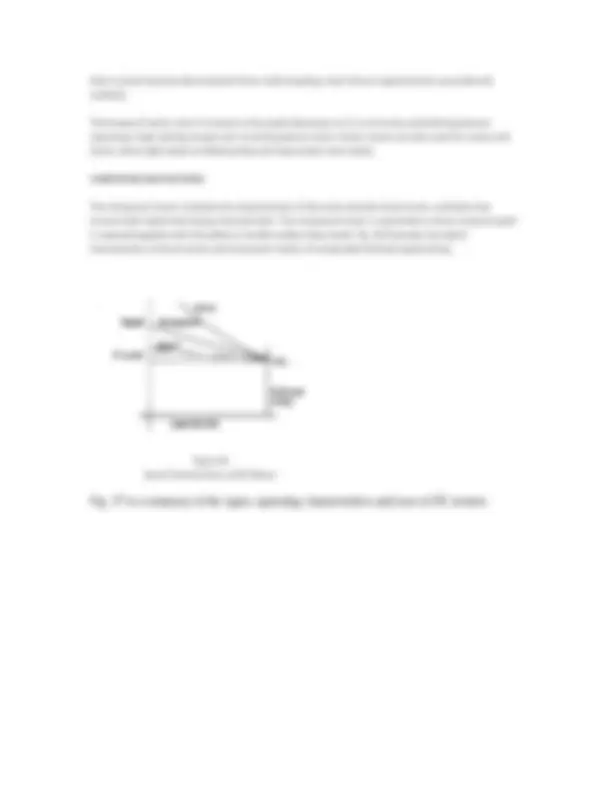
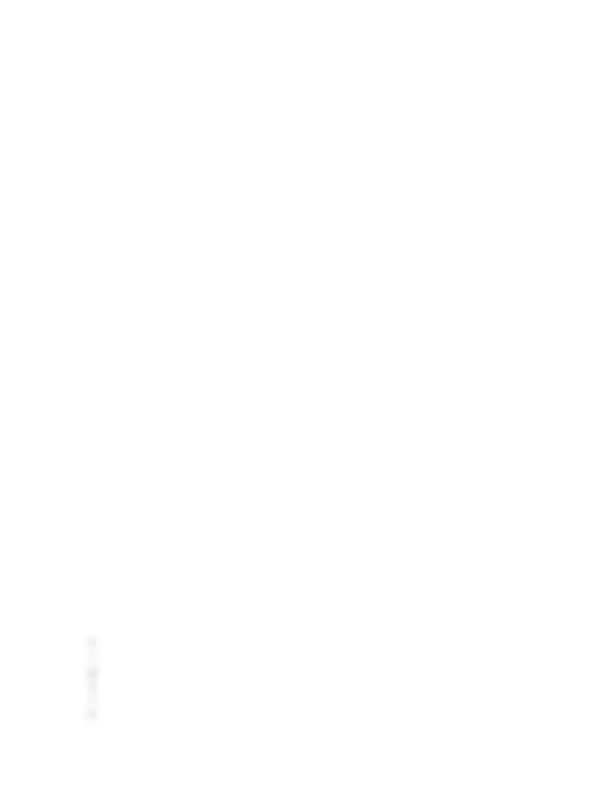
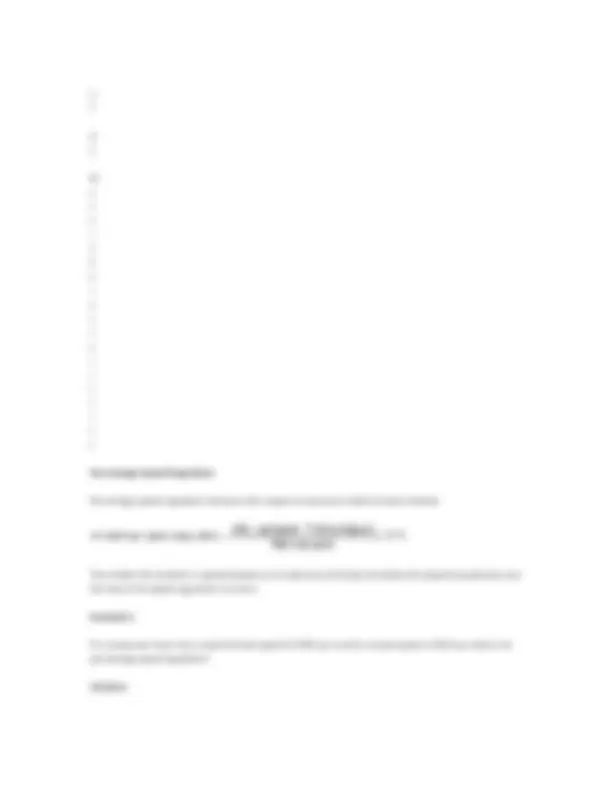
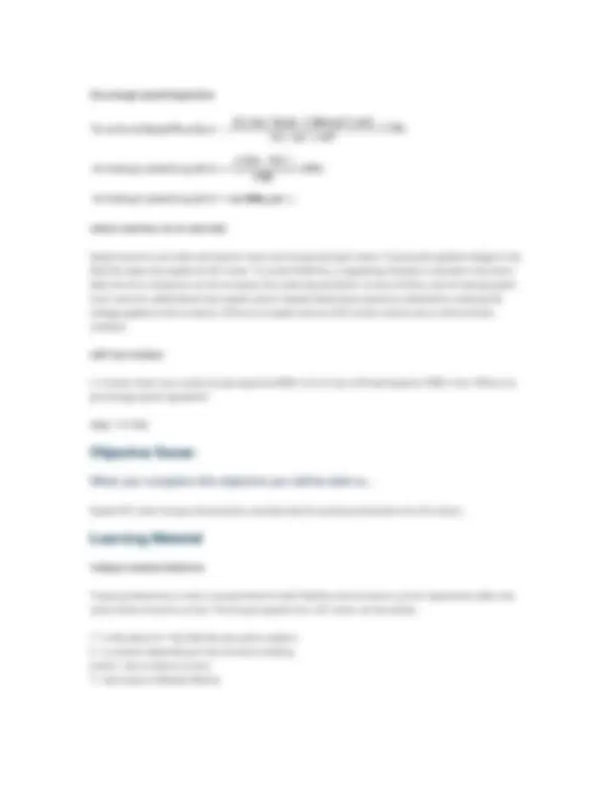
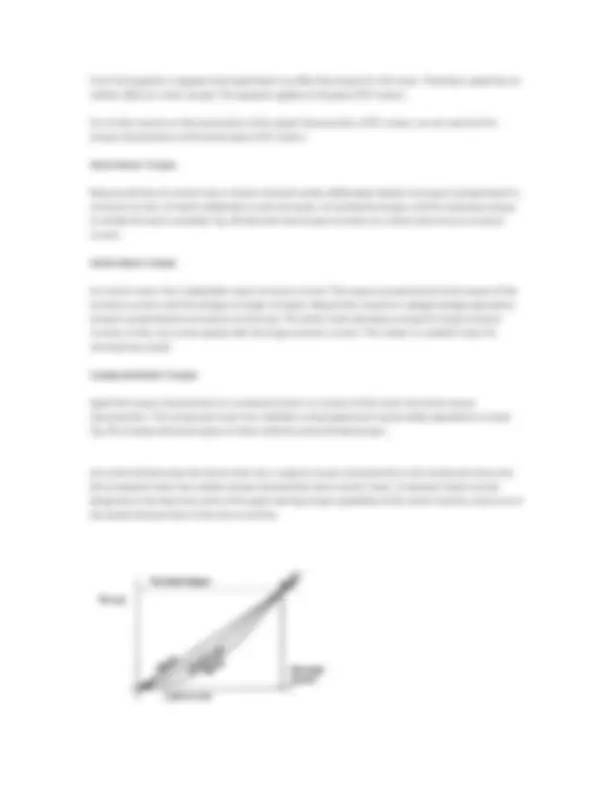
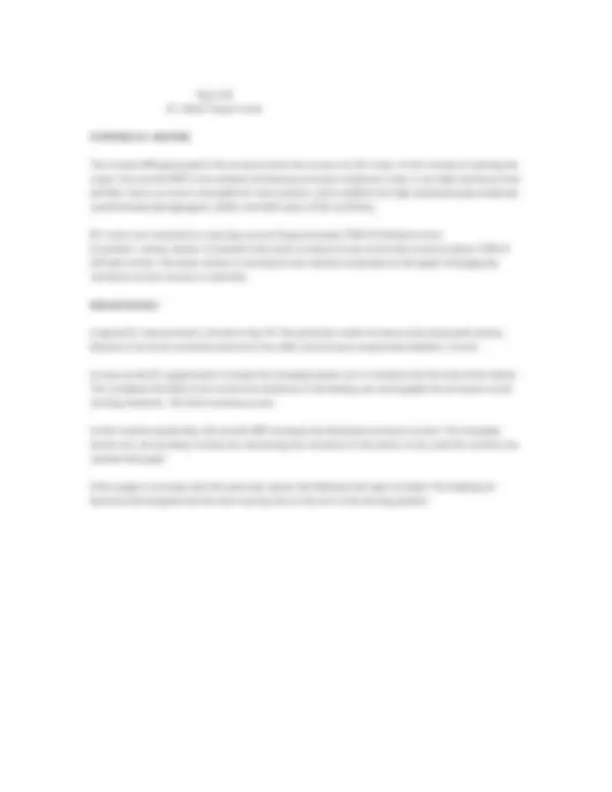
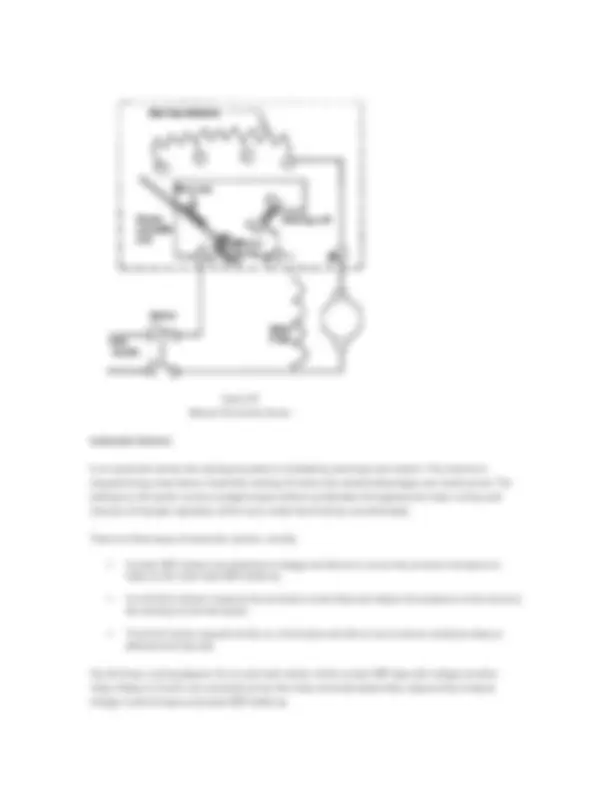
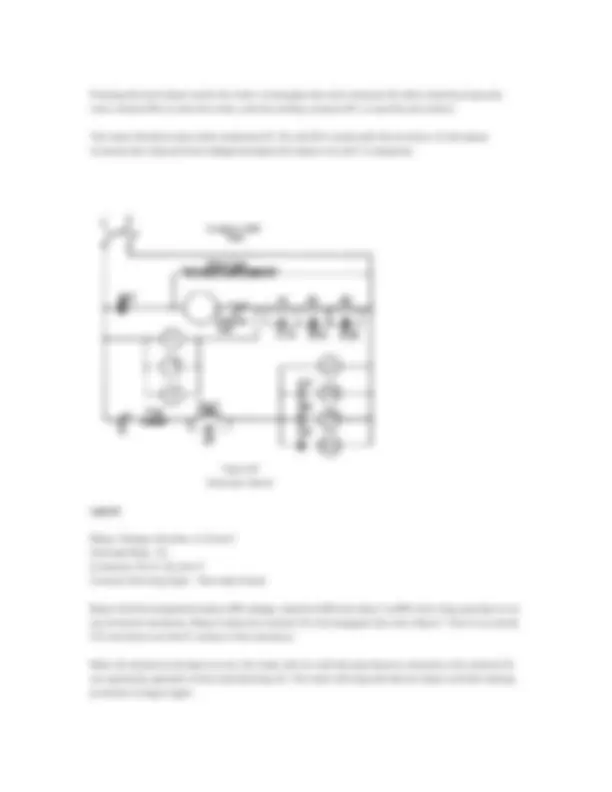
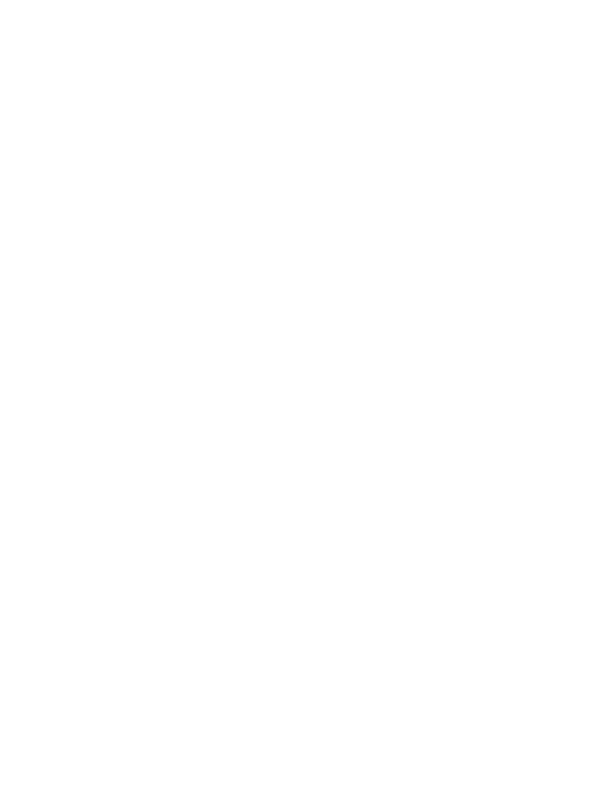
Study with the several resources on Docsity
Earn points by helping other students or get them with a premium plan
Prepare for your exams
Study with the several resources on Docsity
Earn points to download
Earn points by helping other students or get them with a premium plan
Community
Ask the community for help and clear up your study doubts
Discover the best universities in your country according to Docsity users
Free resources
Download our free guides on studying techniques, anxiety management strategies, and thesis advice from Docsity tutors
A comprehensive overview of dc machines, covering fundamental concepts like electromagnetic induction, generator action, and motor action. It delves into the design and operating principles of dc generators and motors, explaining the roles of key components like armature, brushes, windings, and poles. The document also explores back emf, armature reaction, torque, and speed control mechanisms in dc motors. It is a valuable resource for students and professionals seeking a thorough understanding of dc machines.
Typology: Summaries
1 / 40
This page cannot be seen from the preview
Don't miss anything!
Explain basic concepts in the production of electricity and the design, characteristics and operation of DC generators and motors.
You will specifically be able to complete the following tasks:
Explain the production of electron flow in a circuit and define circuit voltage, amperage and resistance.
All matter is composed of tiny particles called molecules. A molecule is the smallest identifiable particle of a substance. Each molecule is made up of smaller particles called atoms the building blocks of all matter. Electricity can be explained by the nature of atoms and the manner in which they behave when subjected to various forces and conditions. Fig. 1 portrays the structure of an atom. The center consists of an arrangement of protons carrying a positive charge. Arranged in circles, or shells, around the protons are negative charges called electrons. Figure 1
The Atom In Fig. 1 the outer ring has only one electron spinning in orbit. This valence or free electron is loosely attracted to the mass of protons and is easily freed from the atom. A battery or generator can force an electron to move, allowing an electron from an adjacent atom to rush in and take its place. Such a movement of electrons along a conductor is called an electric current. The movement of electrons cannot be maintained unless there is a continuous, unbroken path from the current-producing device to the current-consuming device or load. A light bulb, an appliance, or an electric motor are examples of electrical loads. Not all substances possess a valence electron in the outer ring of their structure that can be made to flow. Such substances do not have electron movement or current. They are called nonconductors, or insulators and include rubber, glass, plastics, ceramics, and similar materials. Normally the valence electrons wander erratically in all directions as illustrated by the arrows in Fig. 2. Figure 2 Random Drift of Electrons If an electrical supply such as a battery is connected to the ends of a metal conductor such as a copper wire, as shown in Fig. 3, the free valence electrons are attracted by the positive (+) terminal of the voltage supply and will flow out continuously from the negative terminal (-) into the circuit. The movement or drift of electrons along a conductor is known as current flow.
per second. One coulomb flowing past any section of a conductor per second is termed one ampere. The symbol for current is I. The flow of one ampere of electric current is shown graphically in Fig. 5. Figu re 5 Elec tric Curr ent POTENTIAL DIFFERENCE AND ELECTROMOTIVE FORCE In order to cause an electric current to flow between two points in an electric circuit there must be a difference in electric pressure or potential. The unit of measurement of potential difference is the volt. The potential difference required to cause a flow of one ampere through a resistance of one ohm is one volt. The symbol used is E. If two bodies have different amounts of charge a potential difference will exist between them. When a conductor joins two points, which have a potential difference, a current flows along the conductor. When the two charges become equalized the current flow will stop. Therefore if a current flow is to be maintained the potential difference between the points must be maintained. A device that can maintain a potential difference between two points and a current is flowing is said to have an electromotive force (EMF). There are several ways in which an EMF may be developed. A simple wet cell develops an EMF by chemical means, such as a lead acid battery. An electric generator, in which conductors are moved through magnetic fields, develops an EMF by mechanical means. Photovoltaic cells develop an EMF using light. RESISTANCE Materials, which have a low resistance to the flow of an electric current, are called conductors, and those that have a high resistance are called insulators. Electrical resistance then is defined as the opposition by a material to the flow of an electric current.
The practical unit of measurement of resistance is the ohm. A resistance that develops one joule of heat when one ampere flows through it for one second has one ohm of resistance. Resistance depends not only upon the material used for the conductor but also upon its size and temperature: Increase in conductor cross-sectional area will reduce resistance. Increase in conductor length will increase resistance. Increase in conductor temperature will increase resistance in most cases. There are materials whose resistance decreases with increasing temperature, notably, carbon. The symbol for resistance is R. The symbol used for the ohm is the Greek letter omega, written Ω. Ohm's Law is used for calculations as it shows the relationship between voltage, current, and resistance. The law states that in a given circuit, the quantity of current flow is inversely proportional to the resistance for a given voltage, that is, an increase in resistance results in a reduction of current flow, or
Explain electromagnetic induction and how it produces generator action and motor action.
When an electric current flows in a conductor, a circular magnetic field is set up around the conductor. Magnetic field direction and intensity depend upon the direction and intensity of current flow. If conventional current flow is downward in a conductor, as illustrated in Fig. 6, concentric magnetic lines of force travel in a clockwise direction around the conductor. When the direction of current flow is reversed, the lines of force also reverse to an anticlockwise direction. The dot represents the point of an arrow pointed toward the reader to indicate the direction of current flow. An X on the tail of an arrow shows that the current is flowing away from the reader.
Figure 8 Right Hand Rule to Determine Direction Of the Magnetic Field About a Conductor Electromagnetic Induction An electromotive force can be produced in a conductor by moving the conductor through a magnetic field. The voltage developed in the conductor is called induced voltage, or induced electromotive force (EMF). This EMF is induced by moving a conductor in a stationary magnetic field, or by holding the conductor steady and moving the field. Both principles are used in electric generators. The relative directions of motion of the conductor, the magnetic field, and the induced EMF are determined by using Fleming’s right-hand rule (Fig. 9). Figure 9 Fleming’s Right Hand Rule Extend the thumb, forefinger and middle finger of the right-hand mutually at right angles. Point the forefinger in the direction of the magnetic field and the thumb in the direction of motion of the conductor.
The middle finger then points in the direction of the induced EMF. Generator Action If a conductor is moved relative to a magnetic field so it “cut’s” magnetic flux, then an EMF will be induced in the conductor. If the conductor is part of a complete circuit, then “induced currents” will flow within the conductor. The direction of the induced EMF is shown in Fig. 10 for the relative conductor movement shown. The direction of current flow is the direction the current would flow if connected to an external circuit. It is “relative conductor movement” that is important, and whether that relative movement is the consequence of a stationary conductor and a moving field, a stationary field and a moving conductor, or both field and conductor moving, is immaterial. Figure 10 Generator Action The direction of the induced EMF can be determined by applying Fleming's right hand rule. If the index finger, the middle finger and the thumb of the right hand are extended to be mutually perpendicular to each other, and if the index finger points in the direction of the magnetic flux, (conventional direction north to south between poles), and the thumb indicates the relative movement of the conductor, then the middle finger indicates the conventional direction of the EMF induced in the conductor. Motor Action When a current carrying conductor is placed in a magnetic field as illustrated in Fig. 11, the field produced by the conductor distorts the magnetic field between the poles. Notice the direction of the flux lines that circle the conductor. The main field flux lines tend to accumulate on one side of the conductor, so that all the flux lines are gong in the same direction. The conductor has more flux lines or a strong field on one side and fewer flux lines or a weak field on the other side. The field flux lines try to straighten, or take the shortest path between the poles. As there are more flux lines on the strong field side of the conductor, there is more force exerted towards the weak side
Figure 12Mot or Action Fig. 13 shows what happens when a loop of wire carrying an electric current is placed in a magnetic field. Each side or wire of the loop will have a force exerted upon it, as in Fig. 12. The direction of the current flow is different for each side of the loop. The direction of the force exerted on each wire is shown as an arrow marked torque. The sum of the forces or the turning forces is the torque on the loop. In this case, it will rotate in a counter-clockwise direction. This is the principle of operation of D.C. motors. Figur e 13 Moto r Actio n
Fleming's left hand rule is used to indicate the direction the conductor will move due to motor action. It is similar to Fleming’s right hand rule as digits represent the same quantities except that the second finger becomes conventional current direction instead of the induced EMF.
Describe the design and operating principles of a DC generator or motor, clearly stating the purposes of the armature, brushes, windings and poles.
In an actual machine, the air-gaps or distances between the poles shown in Fig. 8 would be completely unacceptable because air has a high magnetic reluctance. Reluctance is the opposition to the establishment of magnetic flux. Because of the large air gap, a very high force would be needed to establish the necessary magnetic flux. M.M.F. is magnetomotive force, and refers to the ability of a coil to produce flux. M.M.F. corresponds to EMF in an electric circuit, and is considered to be a magnetic pressure. In addition, the flux density in such an air gap would not be uniform. Fig. 14 shows a more practical arrangement for the magnetic circuit of a DC machine. Figure 14 DC Machine
The location of a generator is not critical. It can be placed in a clean and dry location, with the electrical energy it produces, transmitted to the point of utilization by suitably sized conductors. The generator is therefore of an open type construction enabling easy access to its constituent parts for observation and maintenance. The motor is restricted to the vicinity of the machine, which it is driving. Often a motor is required to operate in dusty, dirty and damp locations. In order to protect its vital parts from such environments, the motor has to be a more closed type of construction, sometimes totally enclosed. This requires a fan for forced cooling with a resultant loss in efficiency of the machine. This is the only constructional difference between motors and generators. Fig. 16 shows a cutaway view of a DC motor. Figure 16 Cutaway View of DC Motor Armature Windings The single conductor loop shown in Fig. 13 produces little torque in the case of a motor, and little EMF in the case of a generator. In a usable machine, the single loop becomes a coil of many turns, with a complete armature winding consisting of coils evenly spaced around the armature, and placed in the armature slots.
Each slot has two coil sides, although other machines may have four, six, or even more coil sides per slot. The common two coil sides per slot will suffice for our explanations. If one side of a coil occupies the top half of one slot, the other side of the coil will occupy the bottom half of a different slot. Fig. 17 illustrates this arrangement with two coils in a partially filled armature core, at the end opposite the commutator. Figure 17 Armature Windings The displacement between the centers of adjacent poles is 180 electrical degrees or one pole?pitch. Adjacent poles are always of opposite polarity. The shortest displacement between poles of like polarity is 360 electrical degrees. The four-pole machine shown in Fig. 18 indicates that in this case 360 electrical degrees are equivalent to 180 mechanical degrees. In general the number of electrical degrees depend upon the number of poles, and for one complete mechanical revolution of 360°, the electrical degrees are given by, The distance between the two sides of one coil is always approximately one pole pitch. (180° electrical) The reason for this can be explained as follows. When a DC armature revolves, whether the machine is a motor or a generator, the moving conductors cut the flux of each pole in turn and generate an EMF in each conductor. In order for the EMF’s in each side of a coil to add together and not cancel each other out, one side of the coil must be passing a north pole when the other side is passing a south pole. The manner in which the two ends of each armature coil are connected to the bars of the commutator indicates the type of winding. There are two main types of armature winding, the lap winding and the wave winding.
Figure 19 Lap Winding Figure 20 Wave Winding Fig. 19 shows that the two ends of one coil are attached to adjacent bars on the commutator. The overall effect is that connections to the armature cause the coils to “overlap” each other, hence the name lap winding. The Wave Winding The wave winding is illustrated in Fig. 20. It is identical in every respect to the winding in Fig. 19, except for the connections to the armature. Now the two ends of one coil are connected to armature bars, which are not adjacent to each other. They are placed a distance apart. Fig. 21 shows two coils of a lap winding in relation to a field pole, (shaded rectangle). Even if the width of a brush is less than the width of a commutator bar, the brush will frequently connect two adjacent bars together as the commutator rotates. This means that the coil connected across the two bars is shorting out. If the coil is in the process of having an EMF induced within it, then a current will flow around the circuit completed by the brush. The result is heavy sparking at the brushes. In order to prevent this situation, the brushes are placed so that the coils being “shorted-out” or “commutated” are always coils whose sides are between the poles and are therefore not producing an EMF. This particular position of the brushes is called the neutral axis, and it is the position of minimum sparking at the brushes. Figure 21 Lap Windings
Explain how EMF (Electromotive force), armature reaction, and torque are created and their influence on a DC generator. Given the speed, flux, number of poles, and number of conductors, calculate the EMF created in a DC generator.
Once the armature starts to rotate, whether the machine is a generator or a motor, armature conductors move with respect to the main magnetic field and therefore have a voltage or EMF induced within them. As soon as the armature conductors of either a motor or generator carry current, they become current carrying conductors in a magnetic field and therefore produce a torque. Torque is a twisting or turning force exerted on the loop. The torque produced by the armature conductors in a generator opposes the driving torque applied to the generator shaft by the prime mover. The torque increases with load, requiring increased input from the prime mover in order to overcome this load torque. The voltage E or EMF induced in a conductor moving through a magnetic field is proportional to the amount of flux “cut” per unit time. If a conductor cuts one Weber (useful flux per pole) of flux in one second, then one volt will be induced in the conductor. The voltage induced in an armature conductor is therefore proportional to the flux per pole and inversely proportional to the time taken to cut that flux. Let N = rotational speed of armature in r/min F = flux per pole in webers P = total number of field poles Z = total number of armature conductors b = number of armature paths
When a generator is running, but is not supplying any load current, the only magnetic field present in the machine is the main magnetic field produced by the windings on the field poles. The arrow (main magnetic field) in Fig.22 (a) represents this magnetic field. The lighter polarity markings in the armature conductors indicate the direction of the induced voltage for rotation indicated, but are made lightly to suggest that no current is flowing in the armature. In this situation, the brushes are placed as, so as to short those coils, which momentarily produce no voltage. When a load is connected to the armature, current flows in the armature conductors and each conductor produces a magnetic field. These individual conductor fields add together in the same manner as the turns of a coil to produce a field in the direction shown in Fig. 22(b), where the main field is not indicated. Armature currents are indicated by heavy polarity markings in the armature conductors. The field produced by the armature conductors distorts the main field flux producing a resultant field in the general direction indicated in Fig. 22 (c).
Figure 22 Armature Reaction This effect is referred to as armature reaction. Armature reaction causes the neutral plane within which the brushes have been placed to shift, so that the brushes are now shorting coils, which produce voltage. Heavy sparking occurs at the brushes as a consequence. Sparking can cause damage, and the effects of armature reaction must be overcome. The brushes could be moved into the new magnetic neutral plane as indicated in Fig. 22(c) and this would stop the sparking. This is not a practical solution, however, as the amount of armature reaction varies with the load. It would be necessary to move the brushes every time the load changed. The most effective method is to set up another magnetic field to oppose the field produced by the armature currents. This is done by inserting smaller commutating poles or interpoles midway between the main poles. These interpoles also carry armature current, and they are connected in series with the armature with a polarity, which attempts to neutralize the armature field. Fig. 23 shows the generator of Fig. 22 fitted with interpoles to correct armature reaction. As load current increases, so the field flux of the interpoles increases to oppose the increasing armature flux. Hence interpoles are effective for all load conditions and enable brushes to be kept in the no-load magnetic neutral axis.