
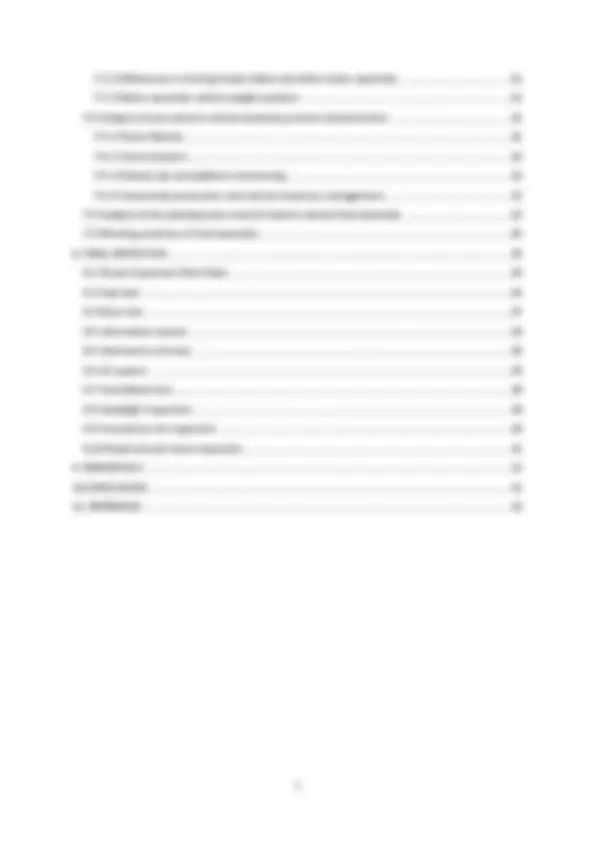
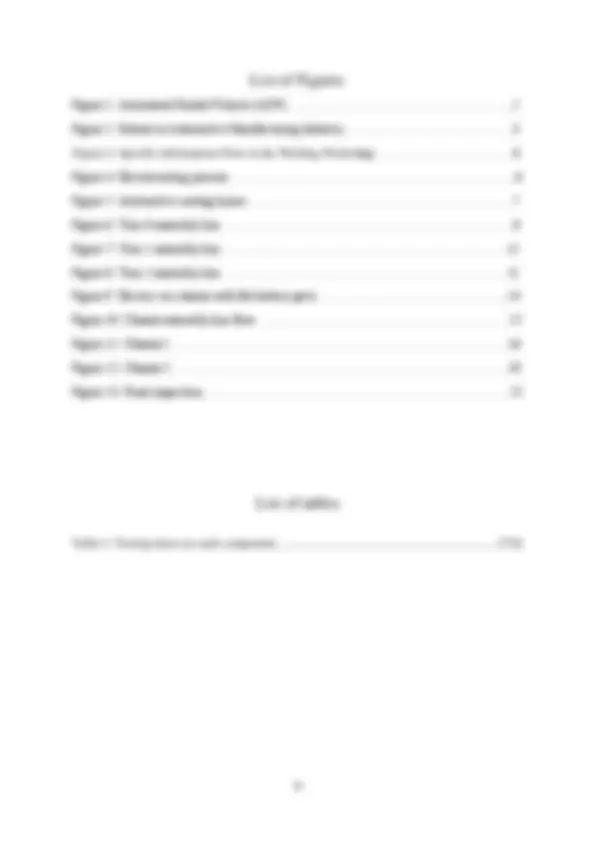

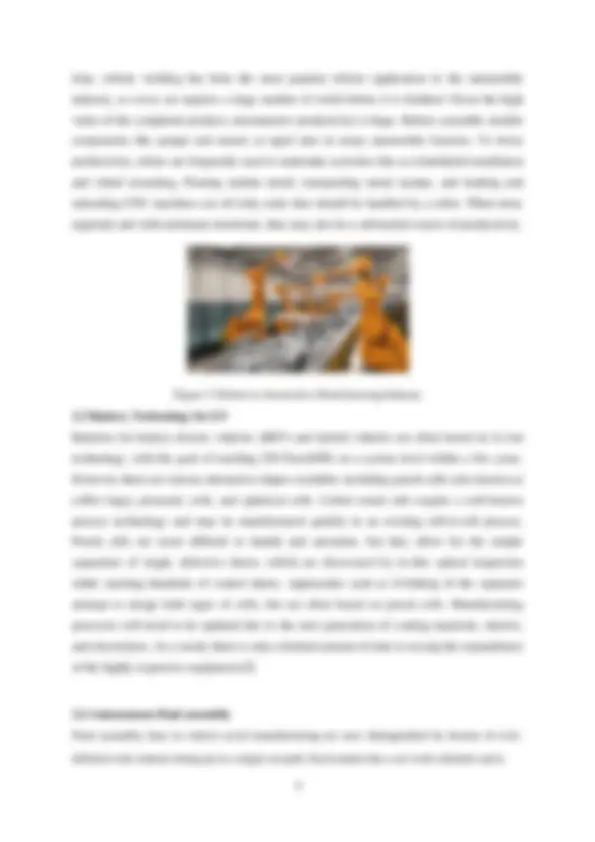
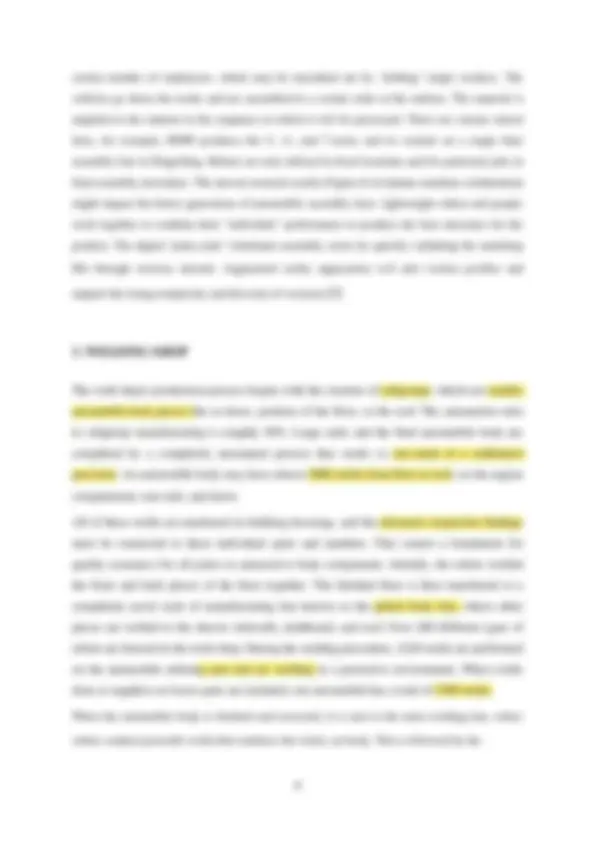
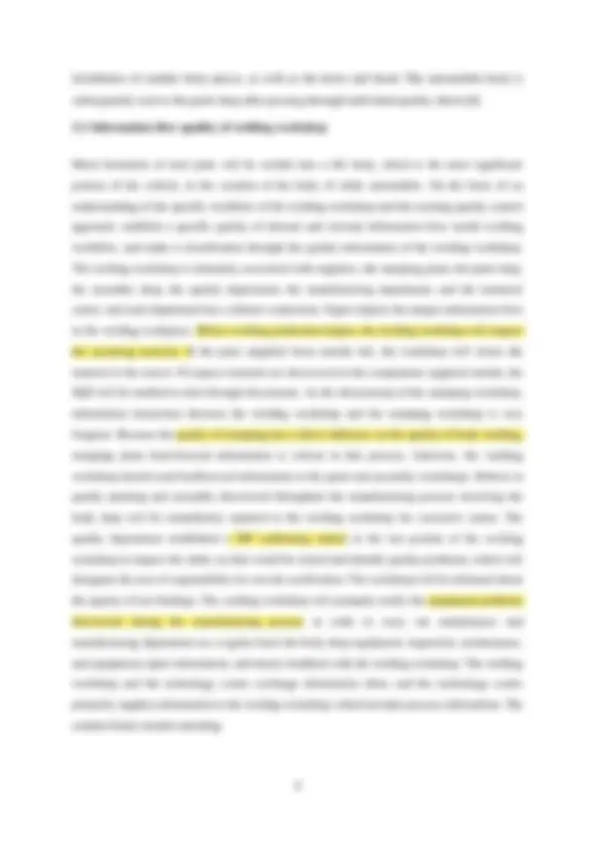
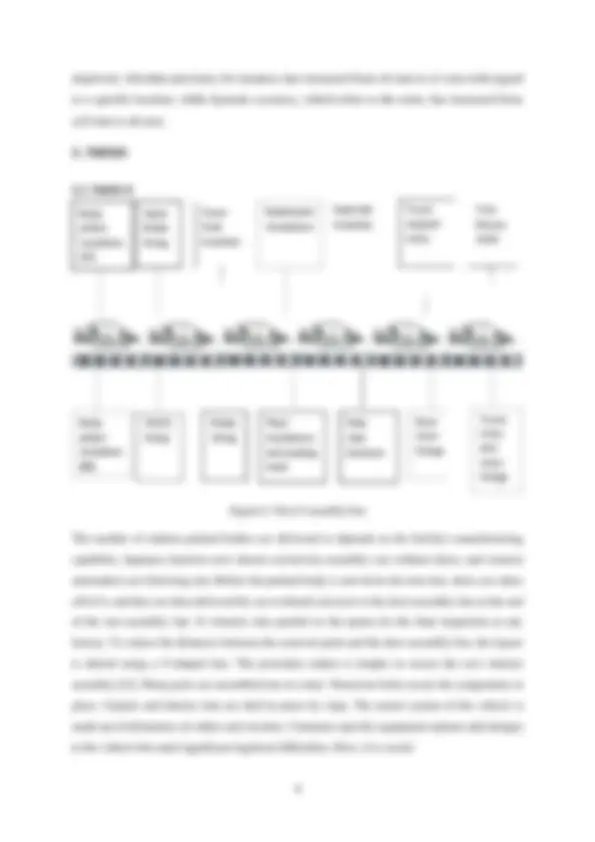
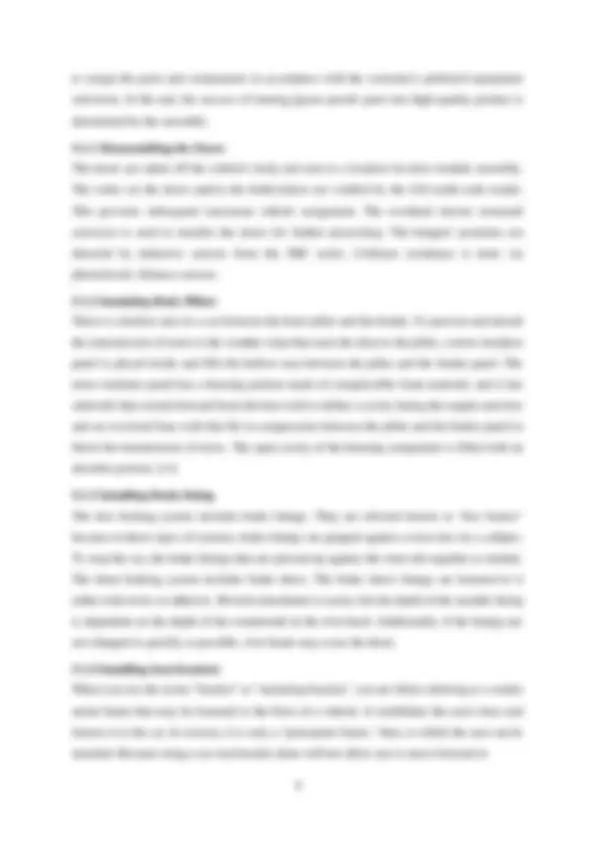
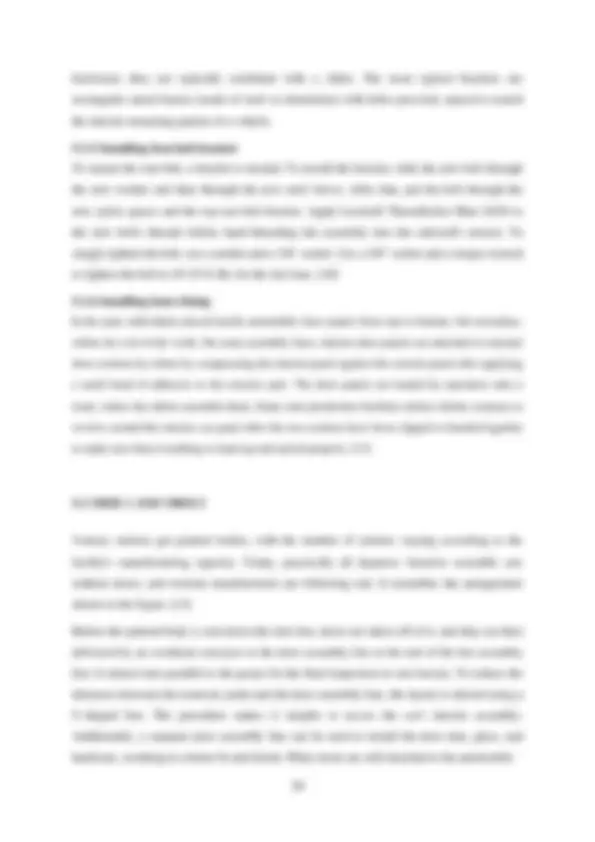
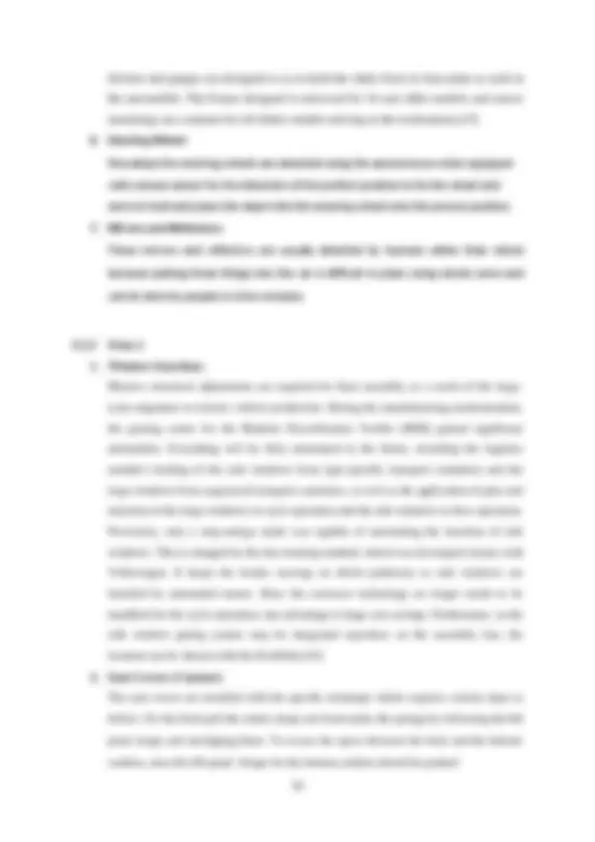
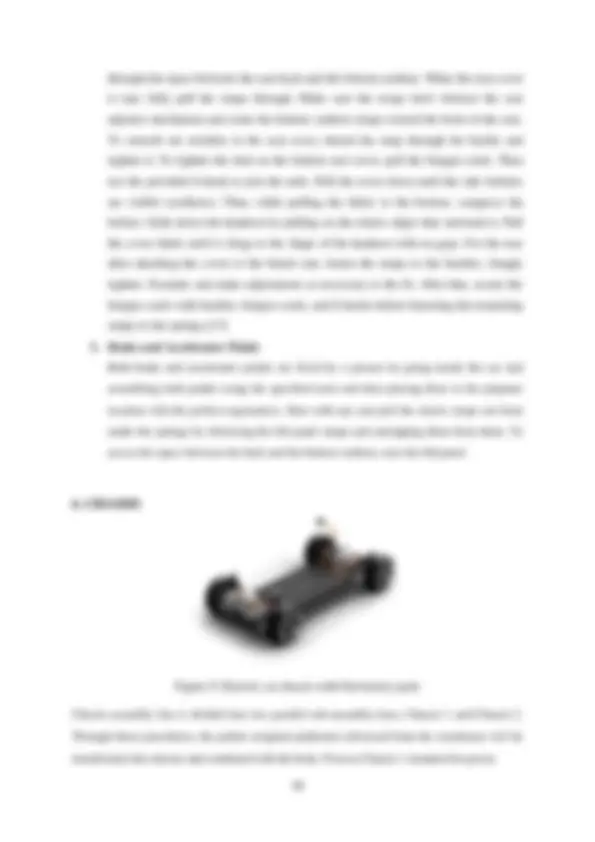
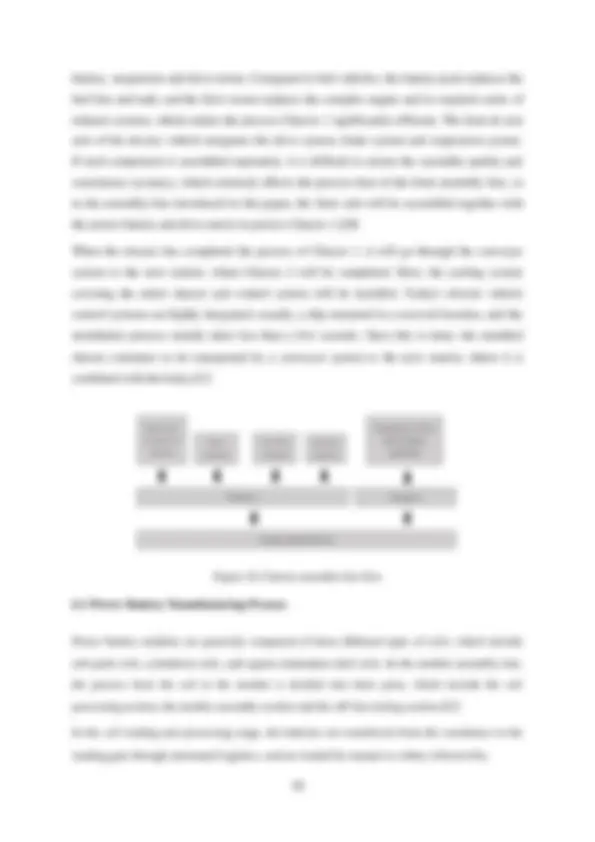
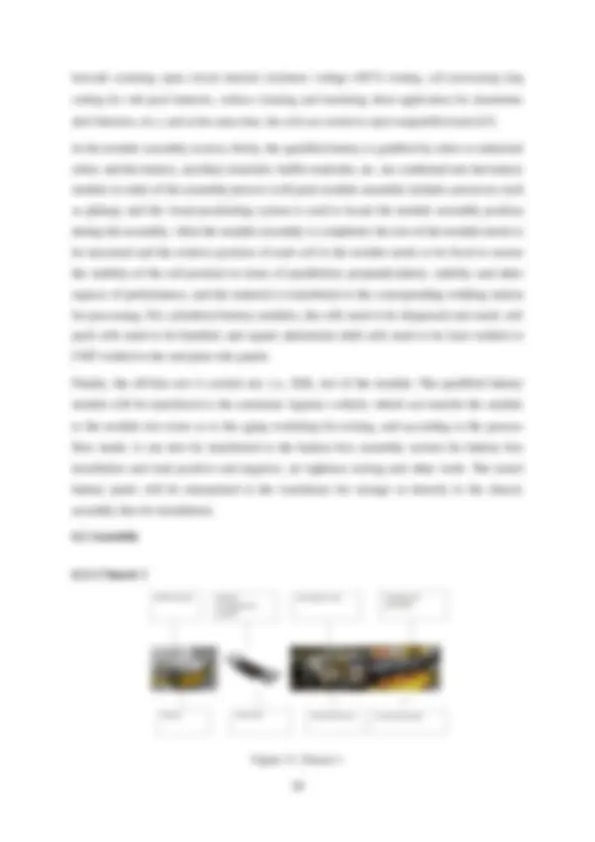
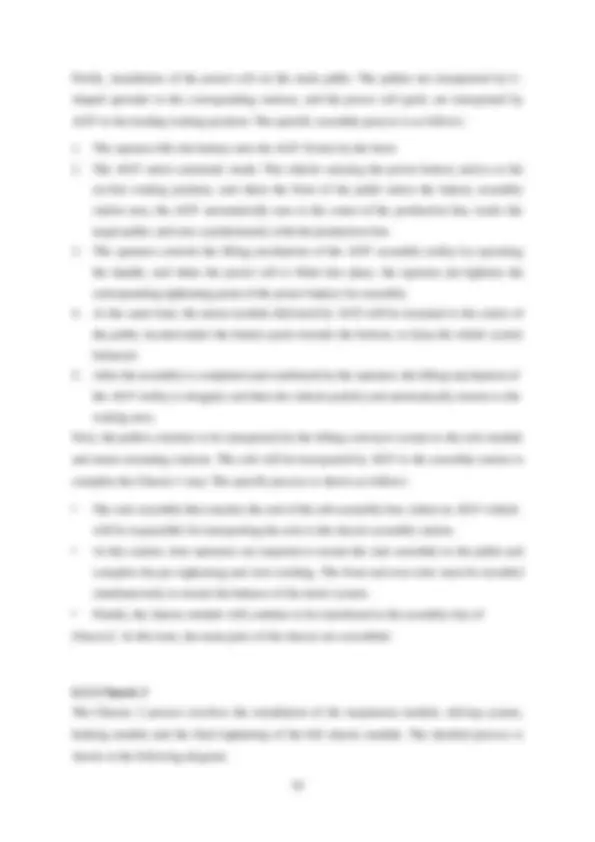
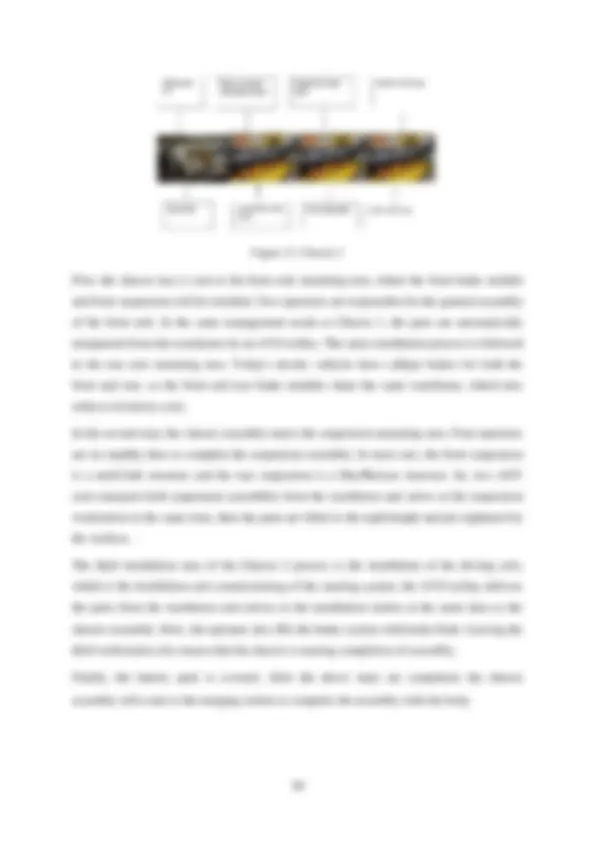
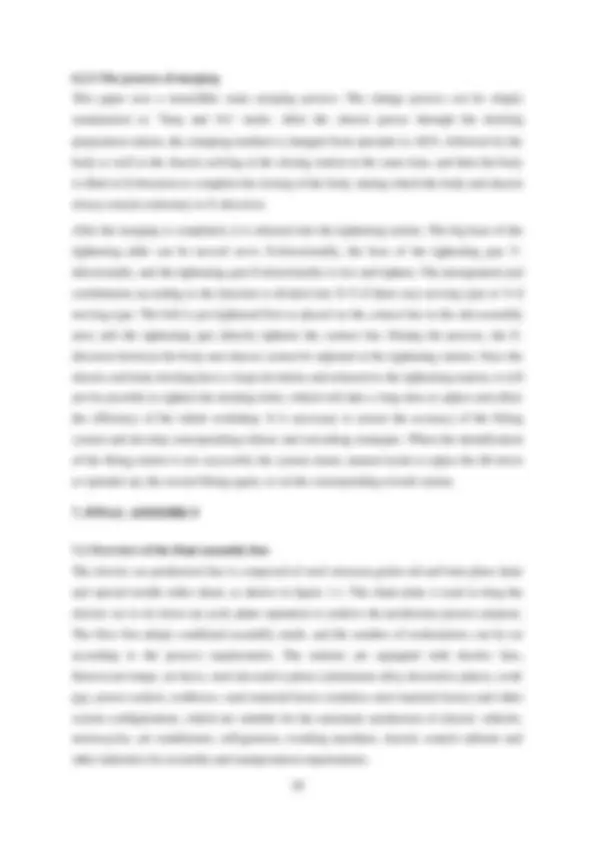
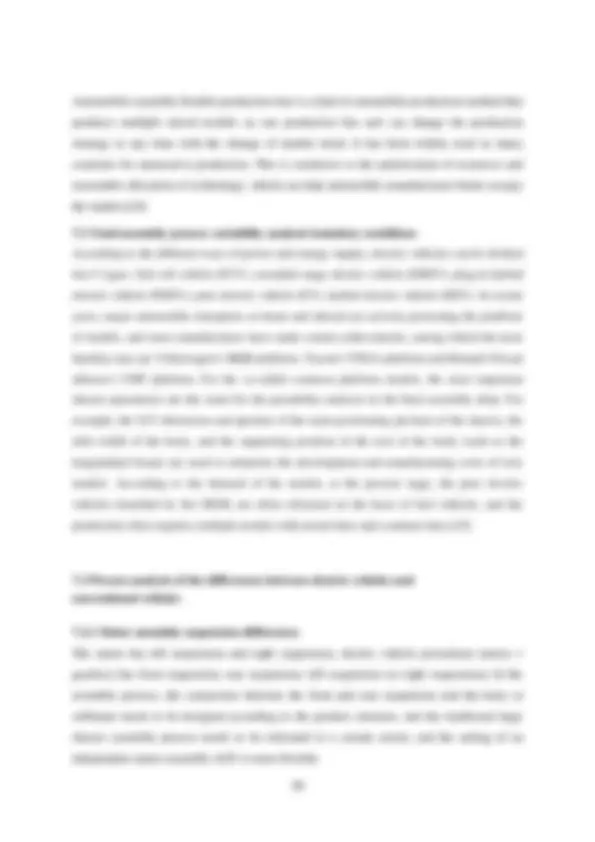
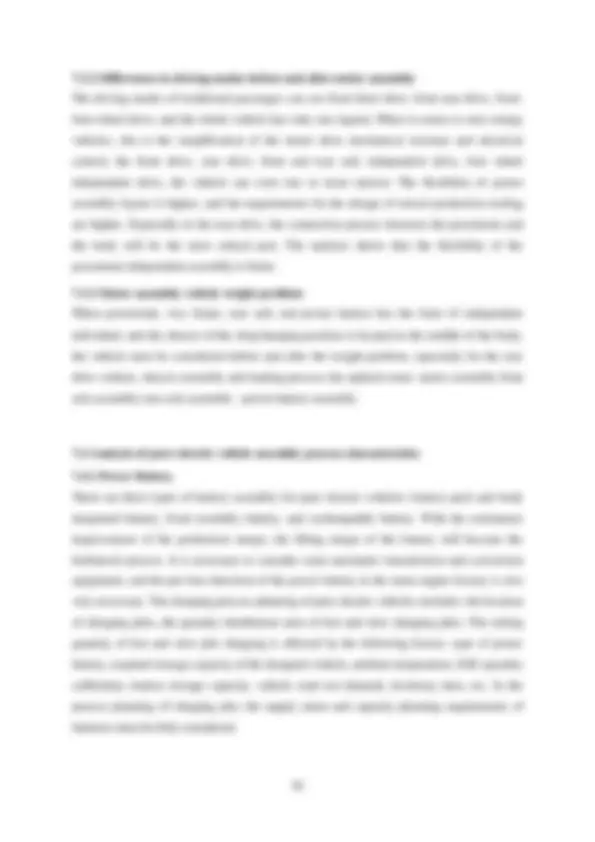
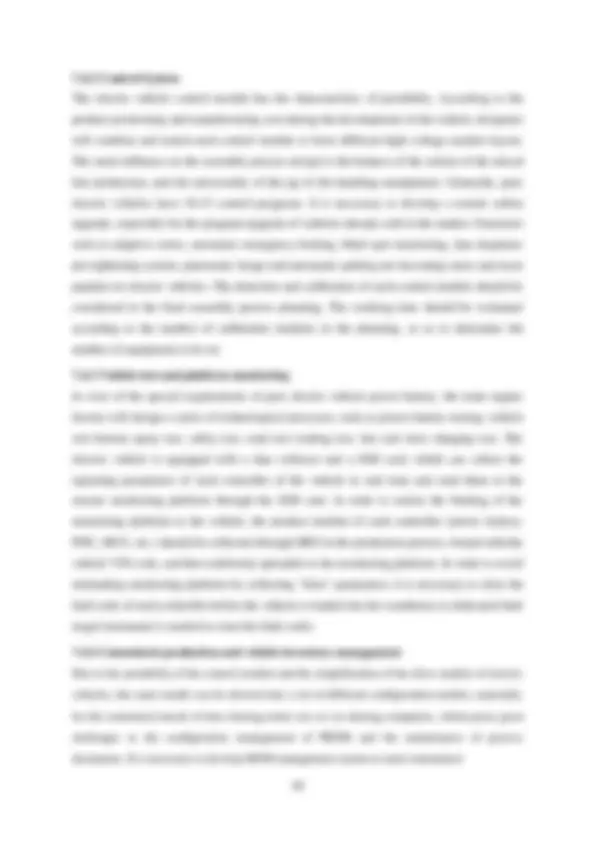
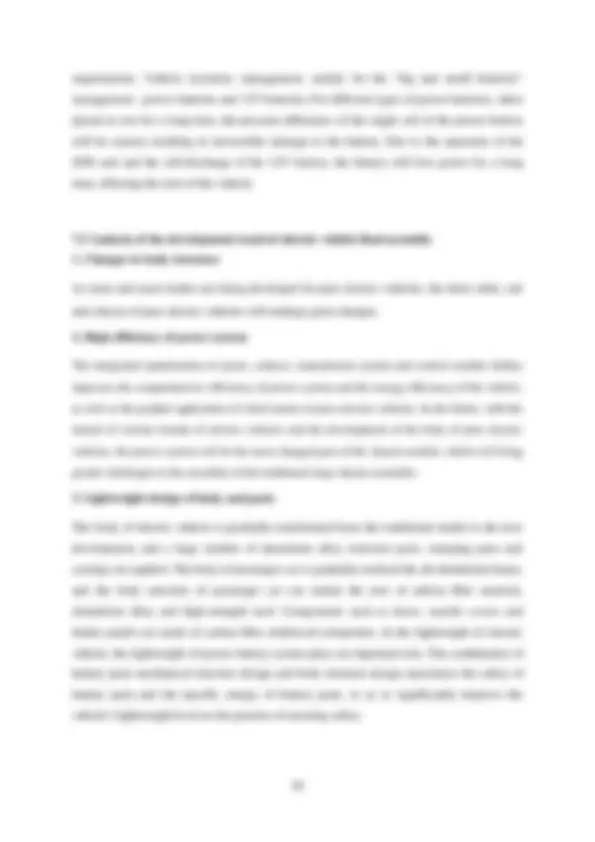
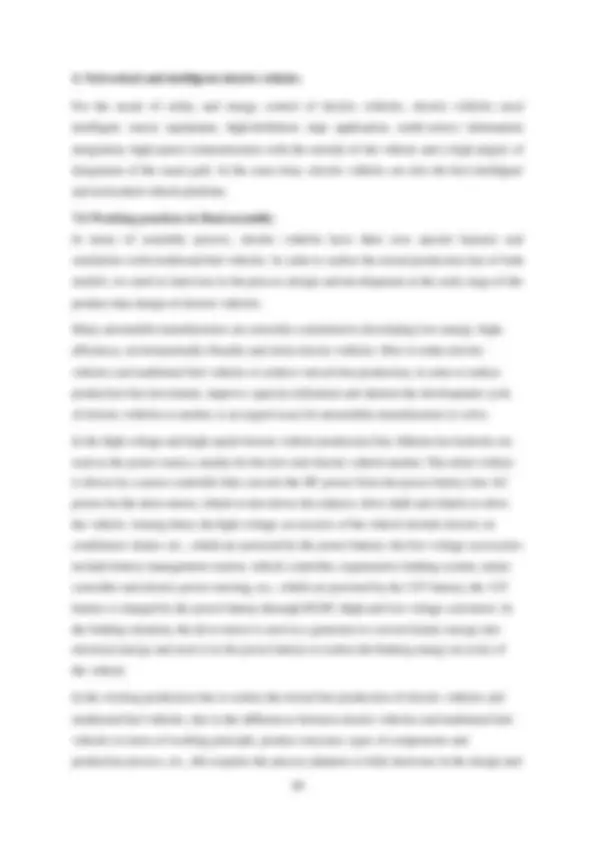
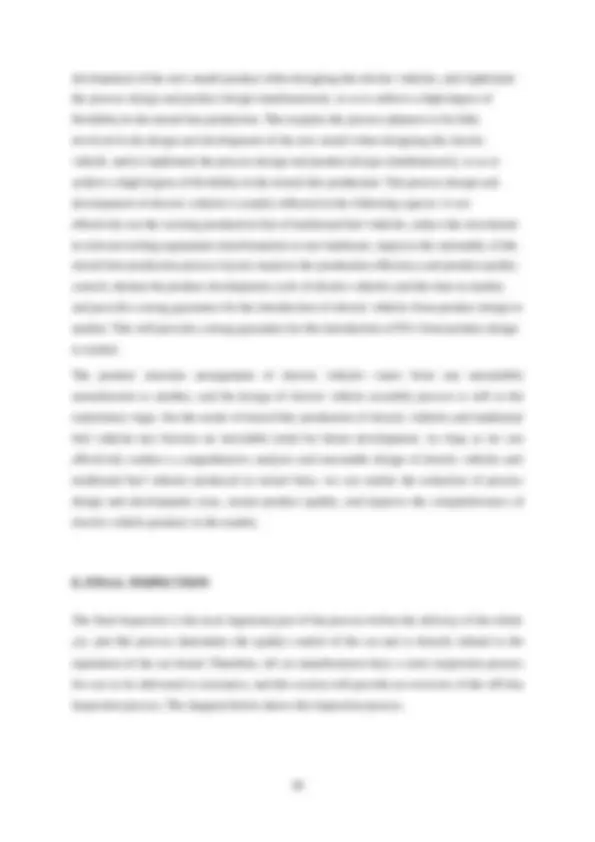
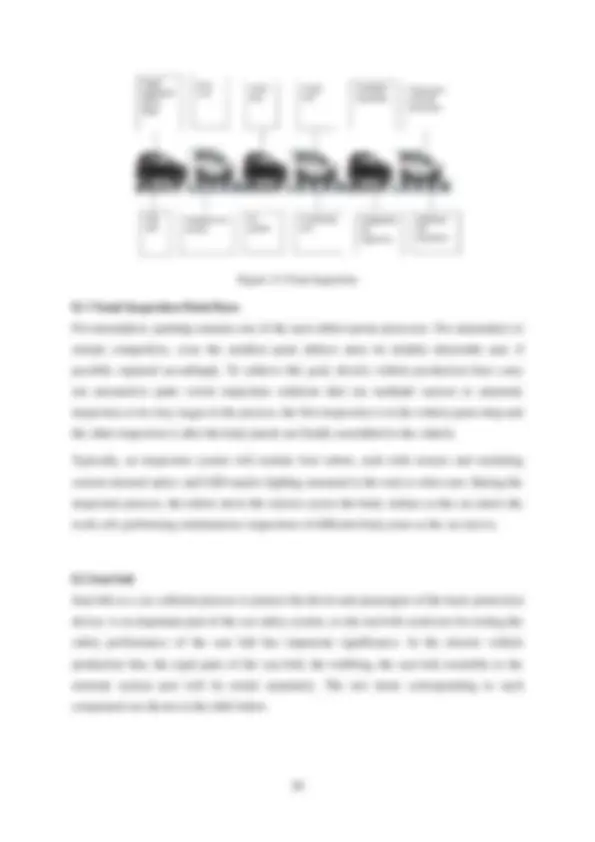
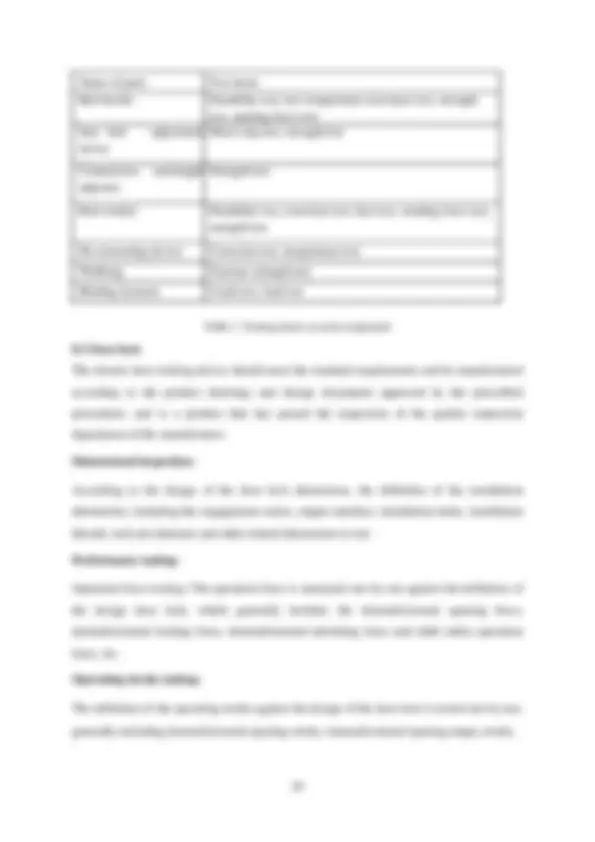
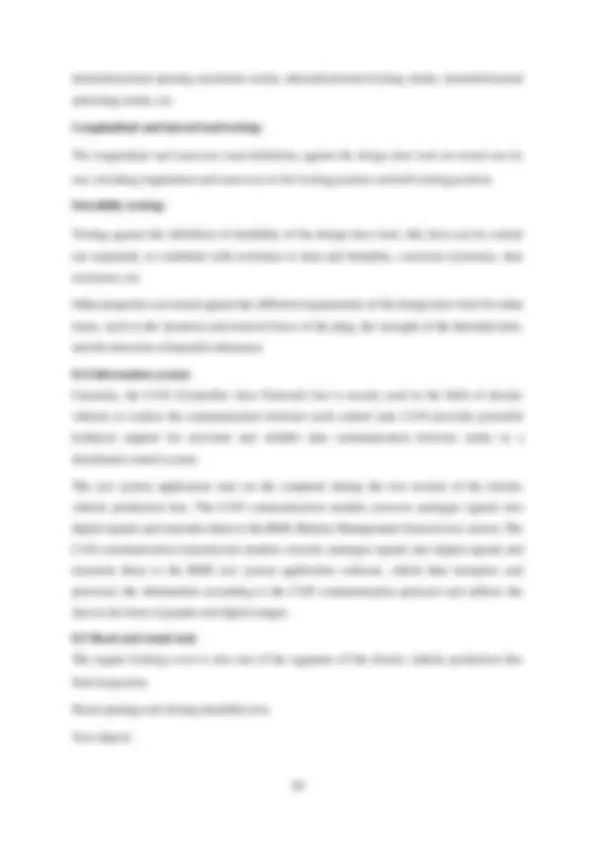
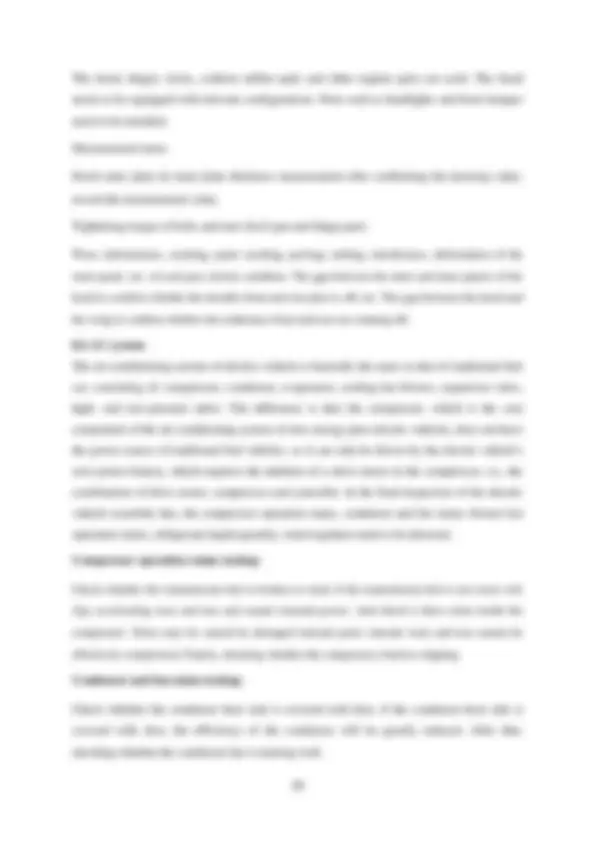
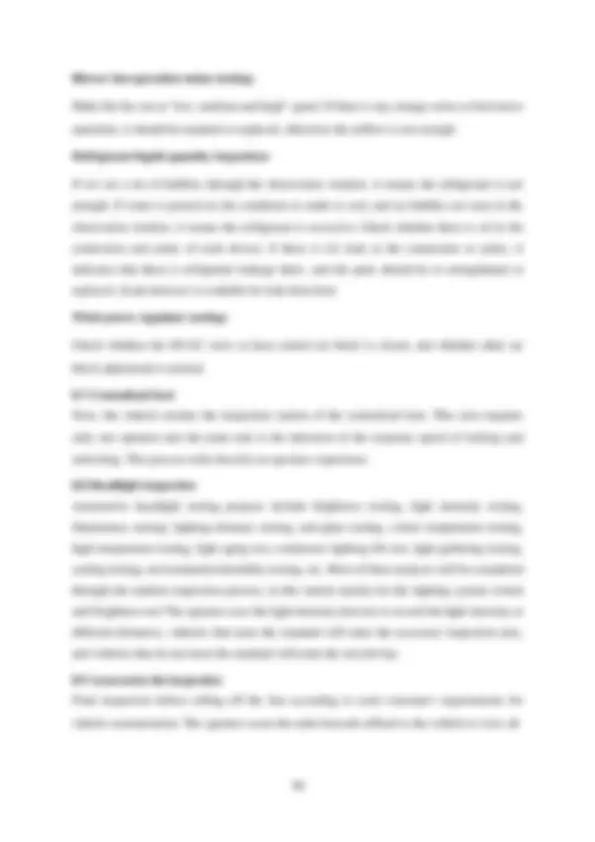
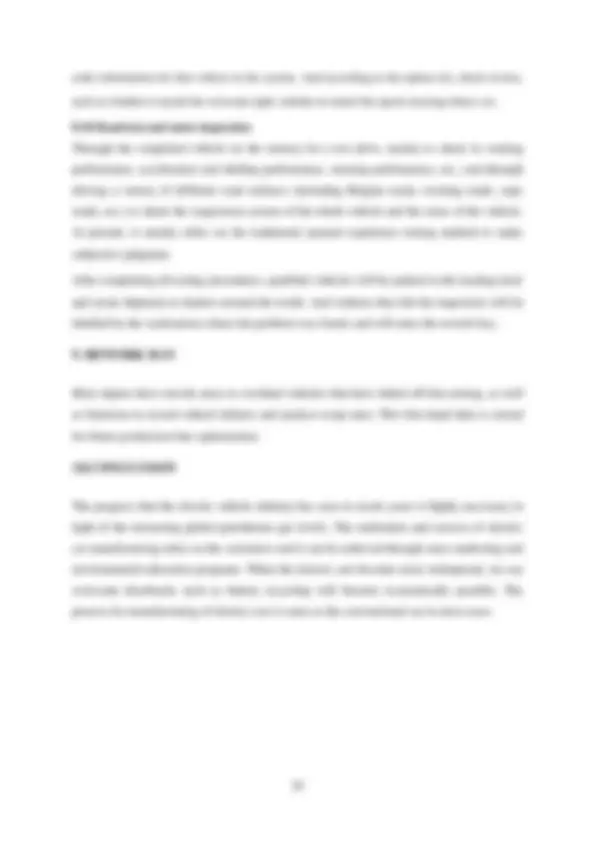
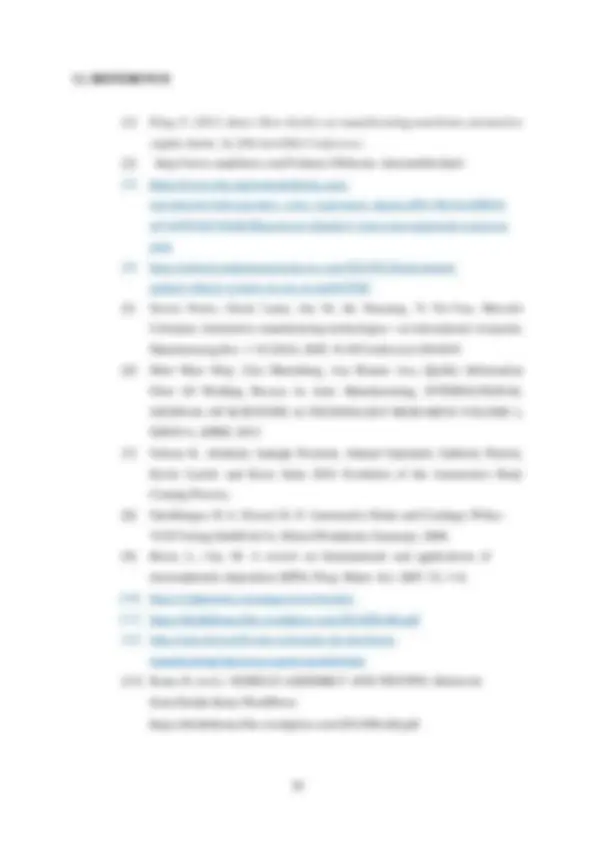
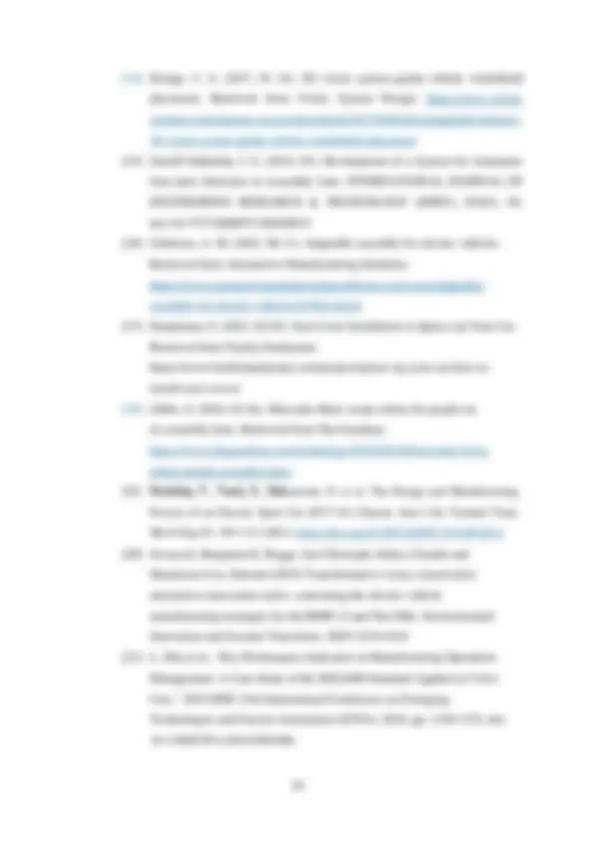
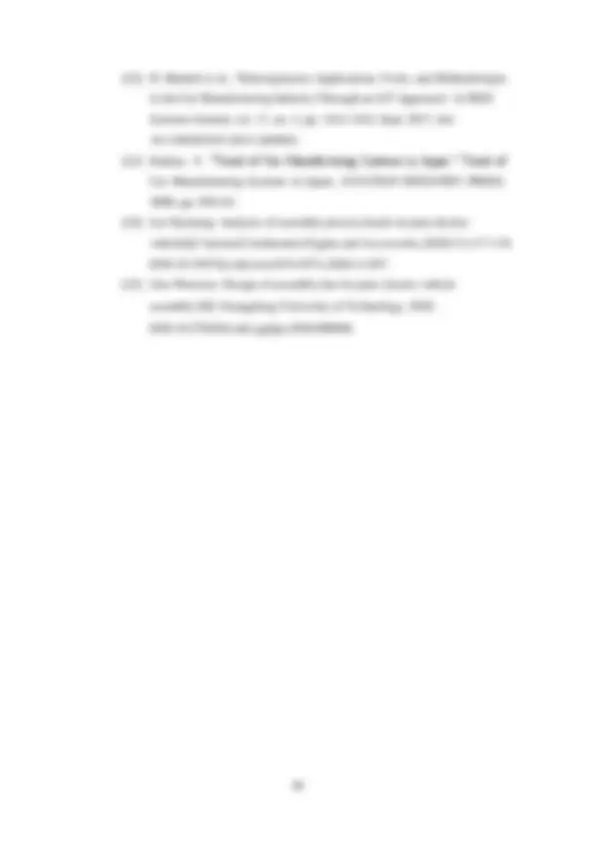
Study with the several resources on Docsity
Earn points by helping other students or get them with a premium plan
Prepare for your exams
Study with the several resources on Docsity
Earn points to download
Earn points by helping other students or get them with a premium plan
Community
Ask the community for help and clear up your study doubts
Discover the best universities in your country according to Docsity users
Free resources
Download our free guides on studying techniques, anxiety management strategies, and thesis advice from Docsity tutors
This document delves into the complexities of electric vehicle assembly, highlighting the unique challenges and opportunities presented by this emerging technology. It explores the differences between traditional fuel vehicle assembly and electric vehicle assembly, focusing on key aspects like battery technology, motor assembly, and the integration of intelligent systems. The document also examines the development trends in electric vehicle assembly, including the shift towards mixed-line production and the increasing importance of automation and intelligent systems.
Typology: Study Guides, Projects, Research
1 / 39
This page cannot be seen from the preview
Don't miss anything!
Automotive industry is undergoing a radical transformation. New technological, social, environmental and geopolitical challenges are redefining the characteristics of a saturated market. On considering environment, Electric cars are promising technology for achieving a sustainable transport sector in future, mainly due to their low emissions. Here we are going to see the manufacturing of the Electric car, the two major difference in electric car being battery back instead of fuel tank and Electric motor instead of IC Engine. This report covers various technologies used in Electric car manufacturing, process flow of battery pack assembling, trims and Chassis. After assembling, final inspections carried out in cars are included.
iv
2.1 Automated Guided Vehicles (AGVs) An automated guided vehicle (AGV) is a portable robot that navigates by following lengthy lines or cables on the floor, or by using radio waves, vision cameras, magnets, or lasers. They are most commonly employed in industrial applications to move heavy goods across a huge industrial structure, such as a factory or warehouse. AGVs are used to supply raw materials, transport work-in-process, and move finished items in Stamping Plants, Power Train (Engine and Transmission) Plants, and Assembly Plants. AGVs are also utilised to deliver specialty tooling that has to be updated. Automated material transport technologies are especially well suited to the automobile industry. AGV systems may be immediately linked to production planning processes via digital interfaces, ensuring that they always know when which components are required in which area of production. The applications of AGV systems used by automotive companies are various, ranging from the transport of whole cars and major components, such as transport front end modules, fascias, instrument panels, and seats, through the assembly line to chassis marriage - where the chassis is synchronised with the car body - and line replenishment of parts and sub-assemblies.[4]
Figure 1: Automated Guided Vehicle (AGV)
2.2 Robots Plants that manufacture automobiles use robots for a wide range of tasks, such as painting, welding, assembling, and material handling. A car plant is filled with robots, but their functions vary depending on where they are located. A robot can inspect parts, move materials, and spray paint on cars, allowing people to concentrate on more specialized work. On massive production lines, collaborative robots are developed to collaborate with other robots. Handling and welding robots must work together to ensure that such assembly lines run smoothly. For a long
time, robotic welding has been the most popular robotic application in the automobile industry, as every car requires a large number of welds before it is finished. Given the high value of the completed product, automation's productivity is huge. Robots assemble smaller components like pumps and motors at rapid rates in many automobile factories. To boost productivity, robots are frequently used to undertake activities like as windshield installation and wheel mounting. Pouring molten metal, transporting metal stamps, and loading and unloading CNC machines are all risky tasks that should be handled by a robot. When done regularly and with minimum downtime, they may also be a substantial source of productivity.
Figure 3: Robots in Automotive Manufacturing Industry 2.3 Battery Technology for EV Batteries for battery electric vehicles (BEV) and hybrid vehicles are often based on Li-ion technology, with the goal of reaching 250 Euro/kWh on a system level within a few years. However, there are various alternative shapes available, including pouch cells (also known as coffee bags), prismatic cells, and spherical cells. Coiled round cells require a well-known process technology and may be manufactured quickly in an existing roll-to-roll process. Pouch cells are more difficult to handle and automate, but they allow for the simple separation of single, defective sheets, which are discovered by in-line optical inspection while stacking hundreds of coated sheets. Approaches such as Z-folding of the separator attempt to merge both types of cells, but are often based on pouch cells. Manufacturing processes will need to be updated due to the next generation of coating materials, slurries, and electrolytes. As a result, there is only a limited amount of time to recoup the expenditures of the highly expensive equipment.[5]
2.4 Autonomous final assembly Final assembly lines in vehicle serial manufacturing are now distinguished by dozens of well-
defined work stations lining up in a single set path. Each station has a set work schedule and a
installation of smaller body pieces, as well as the doors and hood. The automobile body is subsequently sent to the paint shop after passing through individual quality check.[6]
3.1 Information flow quality of welding workshop
Metal formation of steel plate will be welded into a full body, which is the most significant portion of the vehicle, in the creation of the body of white automobile. On the basis of an understanding of the specific workflow of the welding workshop and the existing quality control approach, establish a specific quality of internal and external information flow model welding workflow, and make a classification through the quality information of the welding workshop. The welding workshop is intimately associated with suppliers, the stamping plant, the paint shop, the assembly shop, the quality department, the manufacturing department, and the technical centre, and each department has a distinct connection. Figure depicts the unique information flow in the welding workplace. Before welding production begins, the welding workshop will inspect the incoming material. If the parts supplied from outside fail, the workshop will return the material to the source. If suspect elements are discovered in the components supplied outside, the SQE will be notified to deal through discussions. As the downstream of the stamping workshop, information interaction between the welding workshop and the stamping workshop is very frequent. Because the quality of stamping has a direct influence on the quality of body welding, stamping plant feed-forward information is critical in this process. Likewise, the welding workshop should send feedforward information to the paint and assembly workshops. Defects in quality painting and assembly discovered throughout the manufacturing process involving the body shop will be immediately reported to the welding workshop for corrective action. The quality department established a SIP confirming station in the last portion of the welding workshop to inspect the white car that would be stored and identify quality problems, which will designate the area of responsibility for rework rectification. The workshop will be informed about the quality of test findings. The welding workshop will promptly notify the equipment problems discovered during the manufacturing process in order to carry out maintenance and manufacturing department on a regular basis the body shop equipment, inspection, maintenance, and equipment repair information, and timely feedback with the welding workshop. The welding workshop and the technology centre exchange information often, and the technology centre primarily supplies information to the welding workshop, which includes process information. The combat fixture models matching
guideline check with the operational requirements and other information, on the other hand, are not very complete and should be improved.[6]
Figure 3: Specific Information Flow in the Welding Workshop
4.1 Electric Car Coating Process There are five key phases in modern car painting techniques. These are a few of them [7]:
Figure 4: Electrocoating process
improved. Absolute precision, for instance, has increased from ±4 mm to ±1 mm with regard to a specific location, while dynamic accuracy, which refers to the route, has increased from ±25 mm to ±6 mm.
Body Hand pillars Brake insulation lining (LS)
Front Seat brackets
Dashboard insulations
Seat belt brackets
Trunk support trims
Trim fixture locks
Body pillars insulation (RS)
Clutch lining
Brake Floor Rear lining insulations seat and sealing brackets track
Figure 6: Trim 0 assembly line
Door inner linings
Trunk trims and inner linings
The number of stations painted bodies are delivered to depends on the facility's manufacturing capability. Japanese factories now almost exclusively assemble cars without doors, and western automakers are following suit. Before the painted body is sent down the trim line, doors are taken off of it, and they are then delivered by an overhead conveyor to the door assembly line at the end of the last assembly line. It virtually runs parallel to the queue for the final inspection at one factory. To reduce the distances between the removal point and the door assembly line, the layout is altered using a U-shaped line. The procedure makes it simpler to access the car's interior assembly [12]. Many parts are assembled one at a time. Numerous bolts secure the components in place. Carpets and interior trim are held in place by clips. The neural system of the vehicle is made up of kilometres of cables and circuitry. Customer-specific equipment options add intrigue to the vehicle but entail significant logistical difficulties. Here, it is crucial
to assign the parts and components in accordance with the customer's preferred equipment selections. In the end, the success of turning jigsaw puzzle parts into high-quality product is determined by the assembly.
5.1.1 Disassembling the Doors The doors are taken off the vehicle's body and sent to a location for door module assembly. The codes on the doors and/or the build-tickets are verified by the O2I multi-code reader. This prevents subsequent inaccurate vehicle assignment. The overhead electric monorail conveyor is used to transfer the doors for further processing. The hangers' positions are detected by inductive sensors from the IMC series. Collision avoidance is done via photoelectric distance sensors.
5.1.2 Insulating Body Pillars There is a hollow area in a car between the front pillar and the fender. To prevent and absorb the transmission of noise to the weather strip that seals the door to the pillar, a noise insulator panel is placed inside and fills the hollow area between the pillar and the fender panel. The noise insulator panel has a housing portion made of compressible foam material, and it has sidewalls that extend forward from the base wall to define a cavity facing the engine and tires and an oversized base wall that fits in compression between the pillar and the fender panel to block the transmission of noise. The open cavity of the housing component is filled with an absorber portion. [11]
5.1.3 Installing Brake lining The disc braking system includes brake linings. They are referred known as "disc brakes" because in these types of systems, brake linings are gripped against a rotor disc by a calliper. To stop the car, the brake linings that are pressed up against the rotor rub together as needed. The drum braking system includes brake shoes. The brake shoe's linings are fastened to it either with rivets or adhesive. Riveted attachment is easier, but the depth of the useable lining is dependent on the depth of the countersink in the rivet head. Additionally, if the linings are not changed as quickly as possible, rivet heads may score the drum.
5.1.4 Installing Seat brackets When you use the terms "bracket" or "mounting bracket," you are likely referring to a sturdy metal frame that may be fastened to the floor of a vehicle. It establishes the seat's base and fastens it to the car. In essence, it is only a "permanent frame," then, to which the seat can be attached. Because using a car seat bracket alone will not allow you to move forward or
body, there is a very high probability that the assembly line will sustain damage when it is repeatedly opened and closed at various stations for interior assembly activities. Additionally, hanging the door trim component makes it more difficult. The aisle might be made smaller by taking the doors off. Never more than one step separates the production employees from the components they are installing. When doors are still attached to the automobile body, there is a very high probability that the assembly line will sustain damage when it is repeatedly opened and closed at various stations for interior assembly activities. Additionally, hanging the door trim component makes it more difficult. The aisle might be made smaller by taking the doors off. Never more than one step separates the production employees from the components they are installing.[13]
Figure 7: Trim 1 assembly line
Figure 8: Trim 2 assembly Line
5.2.2 Trim 1
1. Door liners installation: A robot removes an inside door trim liner from a magazine, places it beneath a stationary applicator of hot adhesive, and fastens it to the door. The rapid measuring technique enables speedy determination of the door's exact location.[13] 2. Installation of the cockpit: Each cockpit is already preassembled. From above, the cockpit is lowered into the body. To seal the junction, a robot applies the sealant beforehand. Additionally, the sides of the cockpit are automatically bolted to the body [13]. The stations of the system for automatic cockpit installation are shown in the figure.[14] 3. Rear Light Assembling: The plastic housing, reflectors and front lenses are typically made by tier-one lighting companies, while motors, ballast and necessary wiring and other parts come from a network of tier-two and tier-three suppliers within each major region. Typically, tier- one lighting firms produce the plastic housing, reflectors, and front lenses, while tier- two and tier-three suppliers in each major region provide the motors, ballasts, and associated wiring. These lights are attached using robotic arms or by a person who used a pneumatic drill to tighten the bolts. 4. Preparing and fitting windshields: The windshields are loaded onto pallets automatically (or manually) and centered. To fasten the trim frame to the outer border of the windshield with a particular attachment, a robot installs the necessary number of clips. A robot also uses glue and primer at stations further down the line. The procedure is constantly monitored to make sure that the glue is metered and applied in accordance with the robot's pace of movement. To ensure that the windshields are properly installed into each opening, a robot with an integrated vision system (sensing system based on the principle of laser- light intersection) fits them into place.[13] 5. Seat Installation: A system is developed using the proximity inductive sensors (metal detectors), programmable logic controller, and pneumatic cylinders to automatically detect the slider model to be given for assembling. The output is displayed using indication lamps which indicate the presence of particular model depending on sensor input. The jigs,
through the space between the seat back and the bottom cushion. When the seat cover is taut, fully pull the straps through. Make sure the straps don't obstruct the seat adjuster mechanism and route the bottom cushion straps toward the front of the seat. To smooth out wrinkles in the seat cover, thread the strap through the buckle and tighten it. To tighten the skirt on the bottom seat cover, pull the bungee cords. Then use the provided S-hook to join the ends. Pull the cover down until the side bolsters are visible (cushions). Then, while pulling the fabric to the bottom, compress the bolster. Slide down the headrest by pulling on the elastic edges that surround it. Pull the cover fabric until it clings to the shape of the headrest with no gaps. For the rear after attaching the cover to the bench seat, fasten the straps to the buckles. Snugly tighten. Examine and make adjustments as necessary to the fit. After that, secure the bungee cords with buckles, bungee cords, and S-hooks before fastening the remaining straps to the springs.[17]
3. Brake and Accelerator Pedal: Both brake and accelerator pedals are fixed by a person by going inside the car and assembling both pedals using the specified tools and then placing them in the pinpoint location with the perfect ergonomics. Start with any seat pull the elastic straps out from under the springs by following the bib panel straps and unclipping them from them. To access the space between the back and the bottom cushion, raise the bib panel.
Figure 9: Electric car chassis with flat battery pack
Chassis assembly line is divided into two parallel sub-assembly lines, Chassis 1 and Chassis 2. Through these procedures, the pallets (original platforms) delivered from the warehouse will be transformed into chassis and combined with the body. Process Chassis 1 mounted for power
battery, suspension and drive motor. Compared to fuel vehicles, the battery pack replaces the fuel line and tank, and the drive motor replaces the complex engine and its required series of exhaust systems, which makes the process Chassis 1 significantly efficient. The front & rear axle of the electric vehicle integrates the drive system, brake system and suspension system. If each component is assembled separately, it is difficult to ensure the assembly quality and consistency accuracy, which seriously affects the process beat of the final assembly line, so in the assembly line introduced in this paper, the front axle will be assembled together with the power battery and drive motor in process Chassis 1.[20]
When the chassis has completed the process of Chassis 1, it will go through the conveyor system to the next station, where Chassis 2 will be completed. Here, the cooling system covering the entire chassis and control system will be installed. Today's electric vehicle control systems are highly integrated, usually a chip mounted in a reserved location, and the installation process usually takes less than a few seconds. Once this is done, the moulded chassis continues to be transported by a conveyor system to the next station, where it is combined with the body.[21]
Figure 10: Chassis assembly line flow
6.1 Power Battery Manufacturing Process
Power battery modules are generally composed of three different types of cells, which include soft pack cells, cylindrical cells, and square aluminium shell cells. In the module assembly line, the process from the cell to the module is divided into three parts, which include the cell processing section, the module assembly section and the off-line testing section.[22]
In the cell loading and processing stage, the batteries are transferred from the warehouse to the
loading gate through automated logistics, and are loaded by manual or robots, followed by