
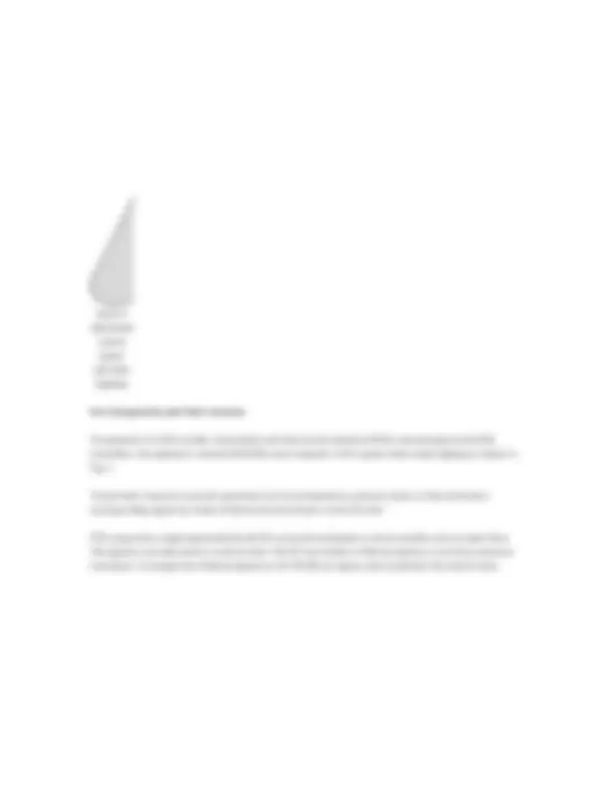
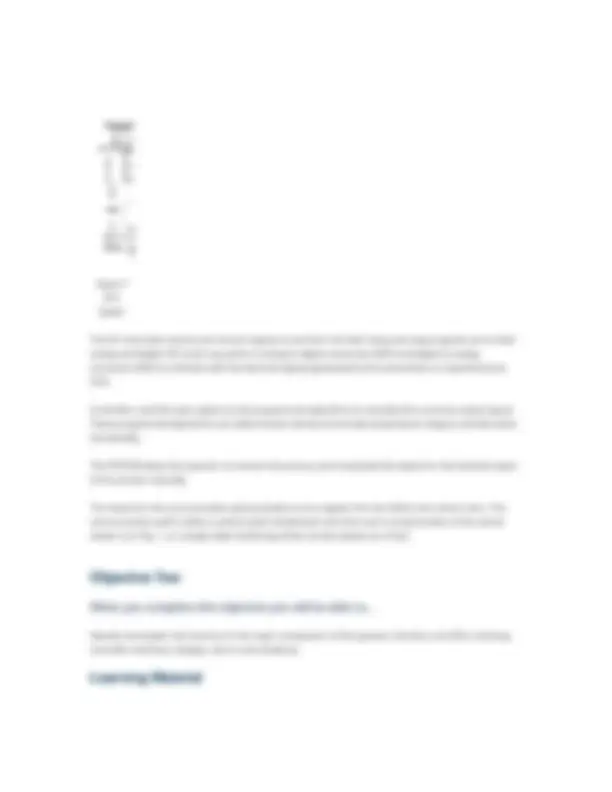
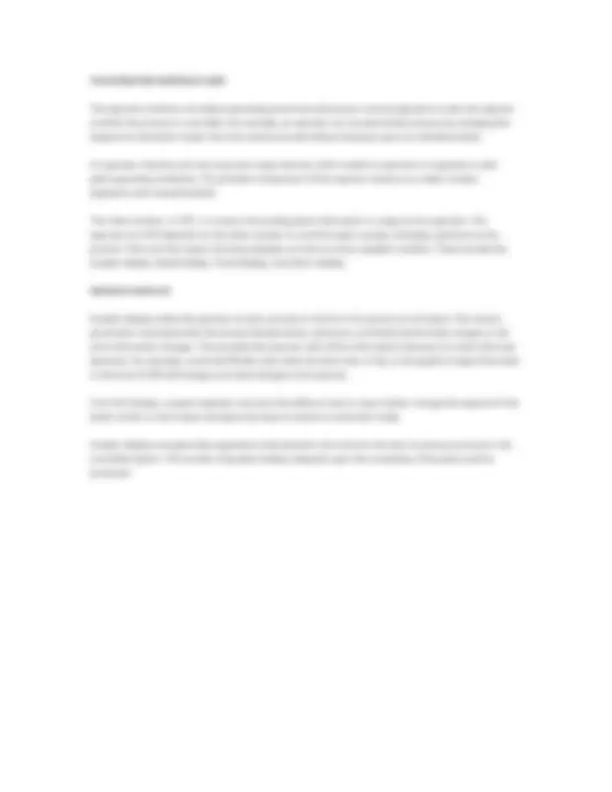
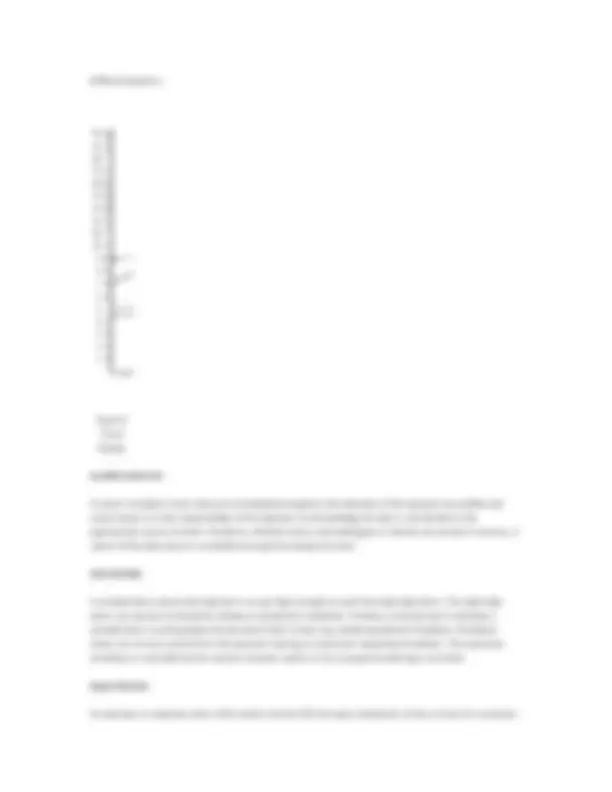
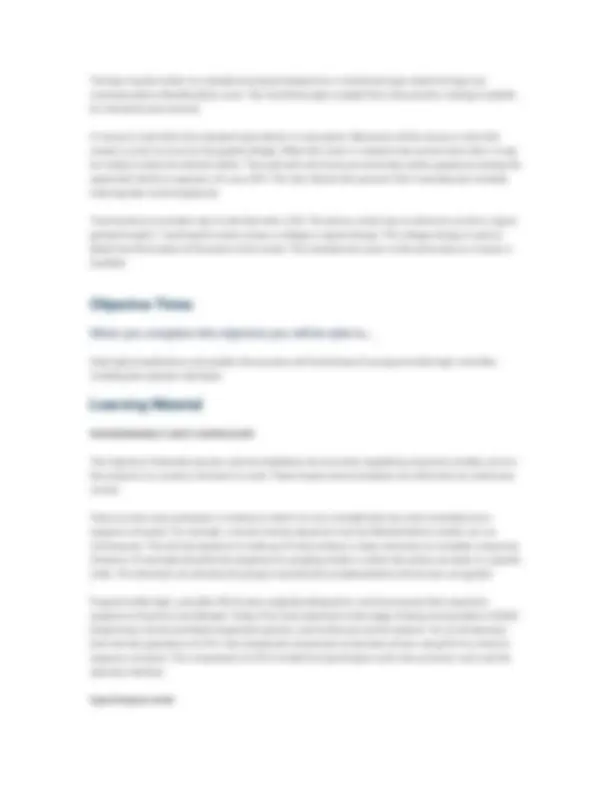
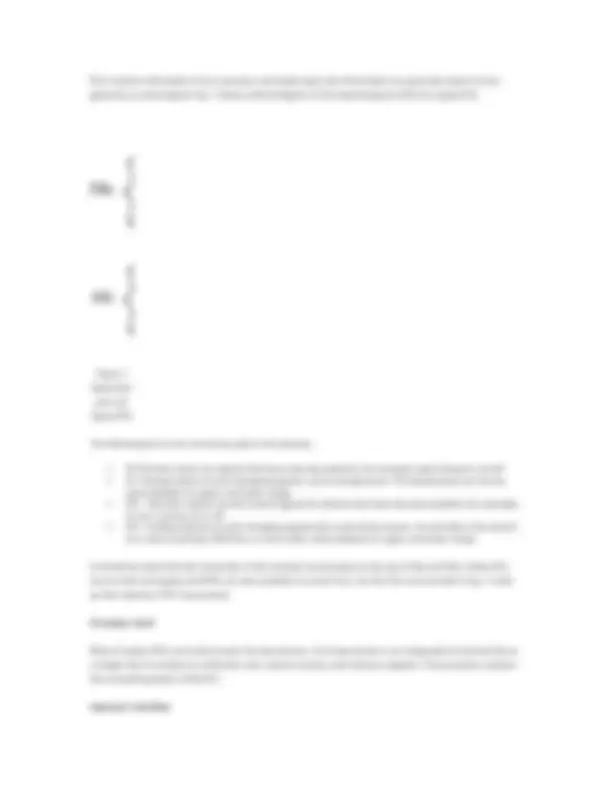
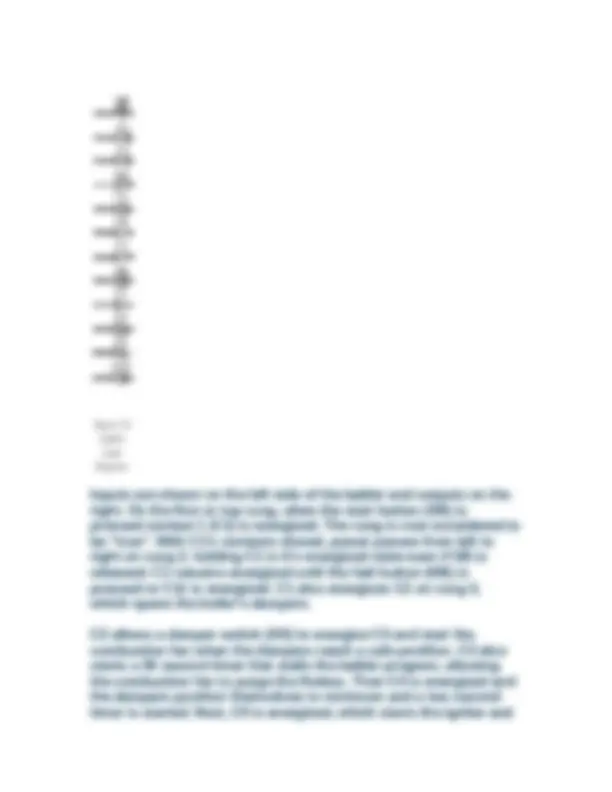
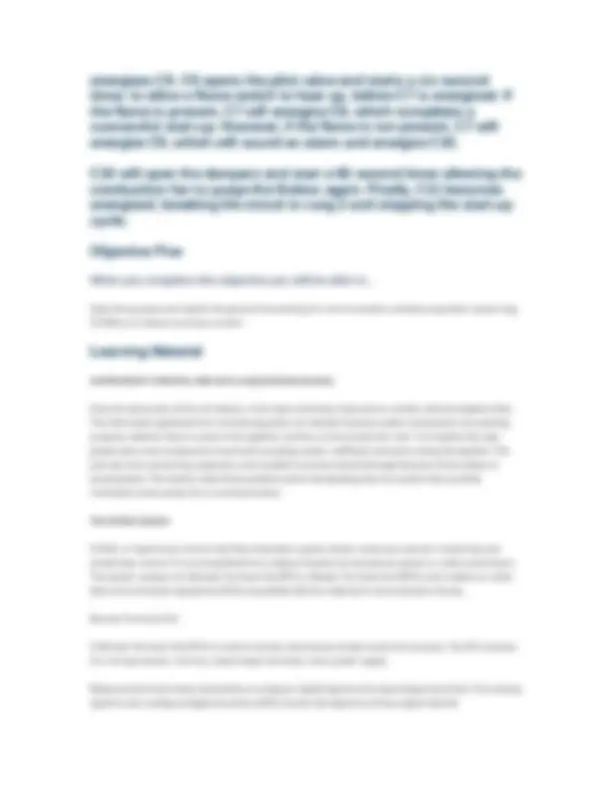
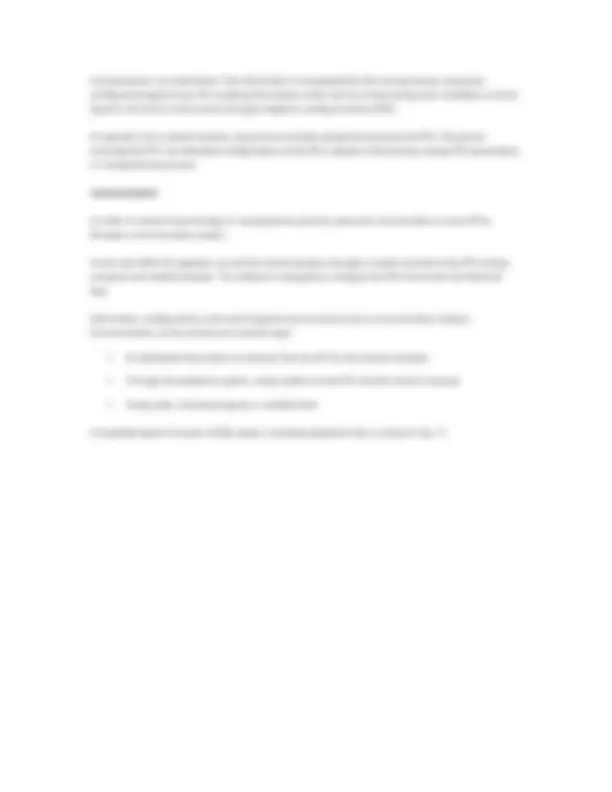
Study with the several resources on Docsity
Earn points by helping other students or get them with a premium plan
Prepare for your exams
Study with the several resources on Docsity
Earn points to download
Earn points by helping other students or get them with a premium plan
Community
Ask the community for help and clear up your study doubts
Discover the best universities in your country according to Docsity users
Free resources
Download our free guides on studying techniques, anxiety management strategies, and thesis advice from Docsity tutors
A comprehensive overview of distributed control systems (dcs) and programmable logic controllers (plcs) in industrial process control. It explains the layout and functioning of a typical dcs, including its major components like transmitters, i/o cards, controllers, and the operator interface unit. The document also delves into the operation of plcs, covering their components, ladder logic diagrams, and their role in scada systems. It is a valuable resource for students and professionals seeking to understand the principles and applications of dcs and plc technology in industrial automation.
Typology: Summaries
1 / 17
This page cannot be seen from the preview
Don't miss anything!
Explain the general purpose, design, components and operation of distributed and programmable logic control systems.
You will specifically be able to complete the following tasks:
Explain distributed control and describe the layout and functioning of a typical distributed control system. Explain the function of each major component of the system.
Distributed Control Systems (DCS) currently control many production facilities. Distributed control allows the control of process parameters from one central location. A Distributed Control System is instrumentation used for industrial process control. The components making up a DCS are installed in two different work areas of processing installations and are separated by function. The operator interface unit allows the operator to monitor process conditions and manipulate set points of the process operation. The operator interface unit is located in a central control room. From this location the operator can:
monitor
The measurement and control components of the system are distributed at locations throughout the process area and perform two functions at each location:
Early centralized control systems had separate sets of wires connected from each controller to its field transmitters and control valves. The control panels were large, having to have space for each controller, recording chart and switch. This type of panel is illustrated in Fig. 1. It also has a computer, which controls some of the critical control loops. In newer systems the panel boards and consoles of an older analog system are eliminated and the communications are over a shared cable. The shared cable arrangement is called a data highway. The data highway minimizes the quantity of wiring while allowing for unlimited reconfiguration flexibility (see Fig. 2). No change is required to the wiring when process modifications result in additions to the control system. Figure 1 Analog Control System
Figure 3 DCS System The I/O cards both receive and transmit signals to and from the field. Input and output signals can be both analog and digital. I/O cards may perform analog to digital conversion (ADC) and digital to analog conversion (DAC) to interface with the electrical signals generated by the transmitters or required by the FCEs. Controllers read the input signal use the programmed algorithms to calculate the corrective output signal. These programmed algorithms are called function blocks and include proportional, integral, and derivative functionality. The OP/CON allows the operator to monitor the process and manipulate the setpoint or the desired output of the process manually. The network is the communication path provided to carry signals from the field to the control room. The communication path is either a point-to-point twisted pair wire from each remote location to the central station as in Fig. 1, or a single cable interfacing all the remote stations as in Fig 2.
Identify and explain the functions of the major components of the operator interface unit (OIU), including controller interfaces, displays, alarms and shutdown.
The operator interface unit allows operating personnel and process control engineers to alter the setpoint at which the process is controlled. For example, an operator can increase boiler pressure by changing the setpoint on the boiler master from the control console without having to go to an individual boiler. An operator interface unit has input and output devices, which enable an operator or engineer to alter plant-operating conditions. The principle components of the operator station are a video monitor, keyboard, and mouse/trackball. The video monitor, or CRT, is a means of providing plant information or output to the operator. The operator of a DCS depends on the video monitor to scroll through a variety of displays pertinent to the process. There are four types of process displays common to many suppliers’ systems. These include the: Graphic display, Detail display, Trend Display, and Alarm display. GRAPHIC DISPLAYS Graphic displays allow the operator to view a process in the form of a picture or animation. The various parameters associated with the process (temperatures, pressures, and levels) dynamically change as real time information changes. This provides the operator with all the information necessary to make informed decisions. For example, a tank will fill with color when the level rises. In Fig. 4, the graphic image of the level in the drum D-505 will change as its level changes in the process. From this display, a power engineer may have the ability to start or stop a boiler, change the setpoint of the boiler master or drum level, and place any loop in manual or automatic mode. Graphic displays are generally organized so the operator has access to the next or previous process in the controlled system. The number of graphic displays depends upon the complexity of the plant and the processes.
Figure 5 Digital Controller Display Trend Displays Trend displays are the DCS equivalents of chart recorders. Often an operator wishes to follow or track several process parameters to see what is happening to the process. Dynamic trending allows an operator to select many process parameters and plot the points on a graph. Fig. 6 shows a trend display on a CRT screen. The graph produced on the video monitor is the equivalent of a strip chart recorder, but allows an infinite number of custom selections through the selection (programming) process. For example, trend lines T1 and T2 on the display in Fig. 6 show superheater and low-pressure and high temperature heater temperatures from 16:00 on the 21st to the 12:00 on the 22nd. The graphs illustrate the link between the two temperatures. The lines go up and down together, following the same pattern. The two temperatures are closely linked or on the same system. Temperatures of the superheated steam T3 and the low-pressure steam T4 are not as closely related. Lines on the graph for these two variables move in
different patterns. Figure 6 Trend Display ALARM DISPLAYS As alarm conditions arise, they are immediately brought to the attention of the operator by audible and visual means. It is the responsibility of the operator to acknowledge the alarm, and decide on the appropriate course of action. All alarms, whether active, acknowledged, or cleared, are stored in memory. A report of the daily alarms is available through this display function. SHUTDOWN A variable that is above the high alarm can go high enough to reach the high-high alarm. The high-high alarm can also be connected to initiate an equipment shutdown. Similarly, a low-low alarm indicates a variable that is running below the low alarm level. It also may initiate equipment shutdown. Shutdown status can remove control from the operator starting an automatic sequential shutdown. The automatic shutdown is controlled by the central computer system or by a programmable logic controller. Input Devices An operator or engineer enters information into the DCS through a keyboard, similar to that of a computer.
PLCs retrieve information from a process, and based upon the information at a particular point in time, generate a control signal. Fig. 7 shows a block diagram of the inputs/outputs (I/O) of a typical PLC. Figure 7 Inputs/Out puts of a Typical PLC The following terms are commonly used in the industry:
value between its upper and lower range.
to turn a pump on or off.
of a valve to perhaps 30% flow, or some other value between its upper and lower range. It should be noted that the remainder of this module concentrates on the use of DIs and DOs. Other I/Os such as thermocouples and RTDs are also available on some PLCs, but the I/Os summarized in Fig. 7 make up the majority of PLC input points. Processor Card Most of today’s PLCs are built around microprocessors. A microprocessor is an integrated circuit that fits on a single chip. It contains an arithmetic unit, control circuitry, and memory registers. The processor contains the computing power of the PLC. Operator Interface
Fig. 8 shows the connection of a PLC programmer to a PLC. A PLC programmer connects to the PLC so that an operator or instrument technician can enter the ladder logic directly into the PLC. The ladder logic controls the sequence of events. The operator interface allows the operator to make changes to the PLC logic and to observe the condition of any portion of the process it controls. Figure 8 Connection of a PLC Programm er to a PLC A physical device must be used to configure or program the PLC to carry out the proper sequence of events. The sequence can be altered any time a PLC programmer is connected. After the ladder logic has been entered, the PLC programmer is disconnected and the PLC becomes a dedicated controller. Under normal conditions, the PLC operates the process from the I/O points. PLCs are not limited to controlling a single process and can control several processes at a time.
Figure 10 Ladder Logic Diagram
State the purpose and explain the general functioning of a communication and data acquisition system (eg. SCADA) as it relates to process control.
Since the early years of the oil industry, it has been extremely important to monitor well and pipeline flow. The information gathered from monitoring points can indicate if pumps and/or compressors are working properly, whether there is a leak in the pipeline, and the current production rate. To complete this task, people were once employed to check each pumping station, wellhead, and points along the pipeline. This task was time consuming, expensive, and resulted in environmental damage because of time delays in locating leaks. The need to solve these problems led to the development of a system that could be monitored continuously from a remote location. The SCADA System SCADA, or Supervisory Control And Data Acquisition system allows continuous process monitoring and simple loop control. It is accomplished from a distant location by local phone system or radio transmission. The system consists of a Remote Terminal Unit (RTU), a Master Terminal Unit (MTU), and modems or other data communication equipment (DCE) compatible with the method of communication chosen. Remote Terminal Unit A Remote Terminal Unit (RTU) is used to monitor and execute simple control of a process. The RTU consists of a microprocessor, memory, input/output terminals, and a power supply. Measurement instruments send either an analog or digital signal to the input/output terminals. If an analog signal is sent, analog to digital converters (ADC) convert the signal to a binary signal that the
Figure 11 Simplified SCADA System Running dedicated lines from the central computer to the RTU is extremely costly. The number of wire pairs installed, plus the cost of installation and operation, generally makes this type of communication impractical. The advantage of this type of system, however, is uninterrupted contact with the RTU. Communicating with the remote site via the local phone system is a practical and cost effective method of communication with the RTU. A dial-up modem must be installed at each end of the system, which converts the serial signal used by the phone system to a signal that can be recognized by the computer. A dedicated phone line is run from each site to the local phone system, and each site can then be dialed up from the central computer system and accessed accordingly. The disadvantage of this type of communication is that it relies upon the local phone system as the main link between the central computer and the remote site. The phone system may not be as reliable as dedicated lines. Radio and microwave transmission are popular media used to communicate with RTU’s. A transmitter/receiver is placed at the remote site along with antennae or microwave dishes. Signals are then sent to the main computer and received by similar transmitter/receiver equipment. Very high frequency (VHF) and ultra high frequency (UHF) radio signals have a greater range than microwave signals, and are not affected as severely by land-bound obstacles. Antennas can be placed on towers to transmit over top of obstacles.
Microwave signals are sent from one site to another in a series of “hops”. Microwave transmission equipment can carry large volumes of high-speed data, but it may require greater maintenance than UHF or VHF radio equipment. Microwave dishes are adversely affected by frost and ice, and may have to be occasionally realigned by service companies. Microwave signals can be affected by different reflective properties, such as snow on the ground. Therefore, microwave is a more costly communication medium than VHF or UHF radio unless very high-speed data, or many voice channels, are required.