
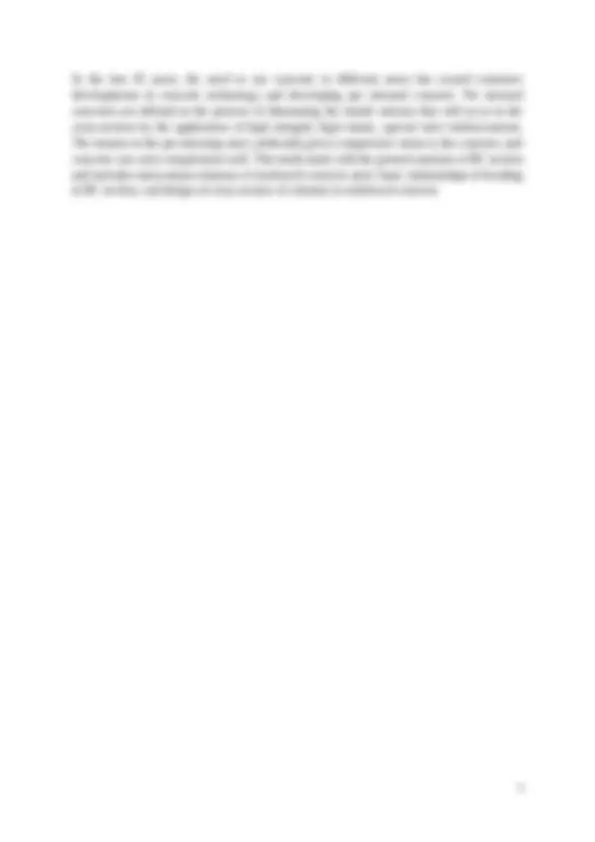
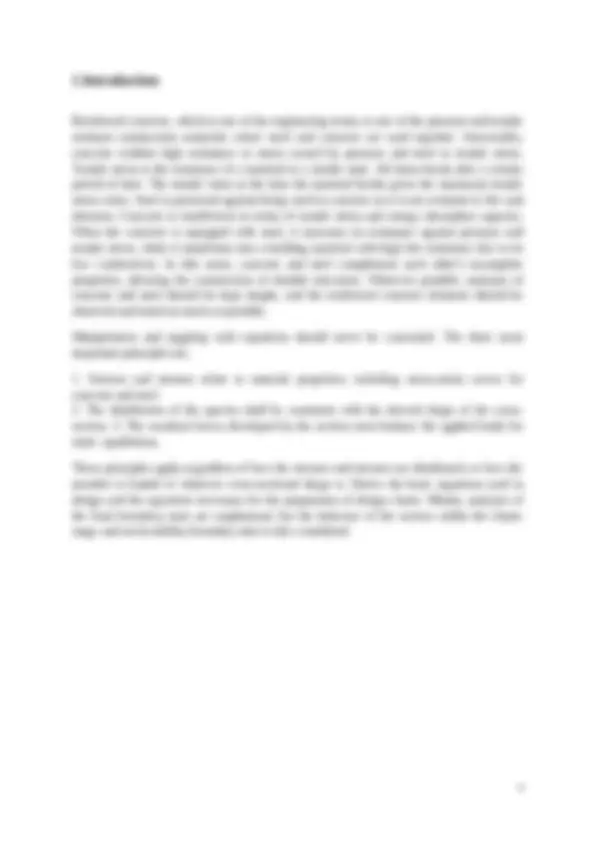

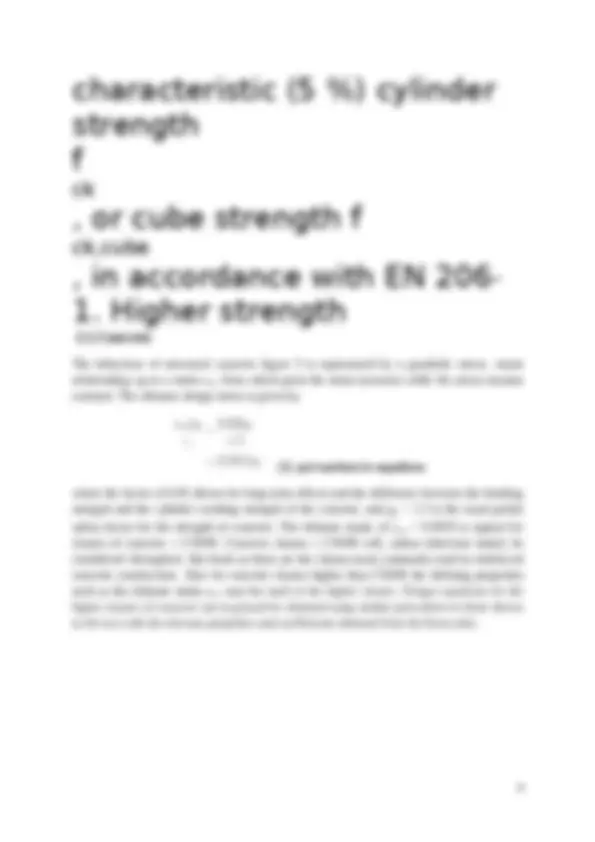
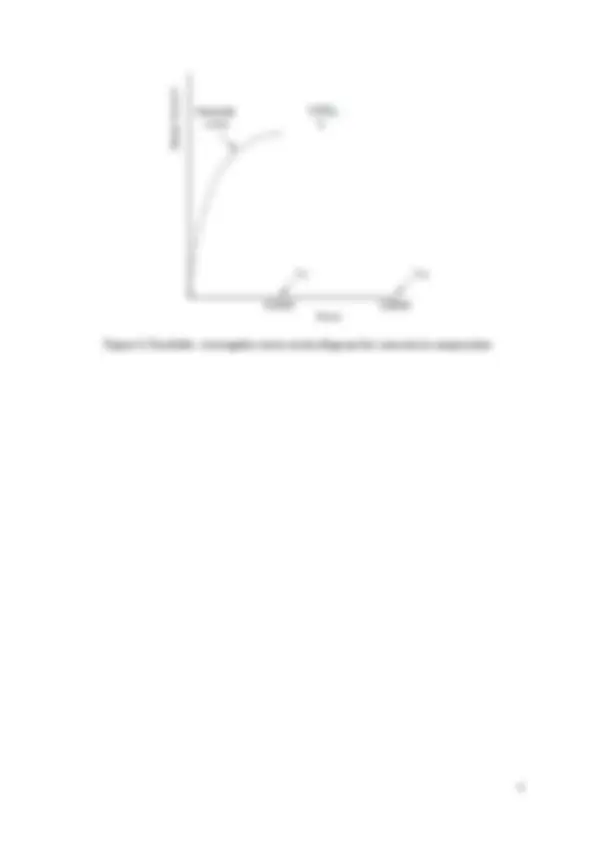
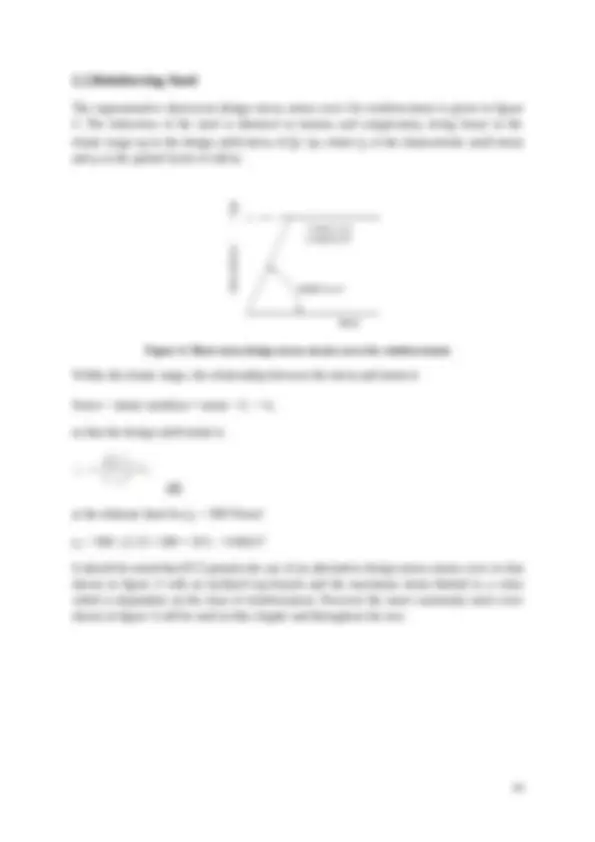
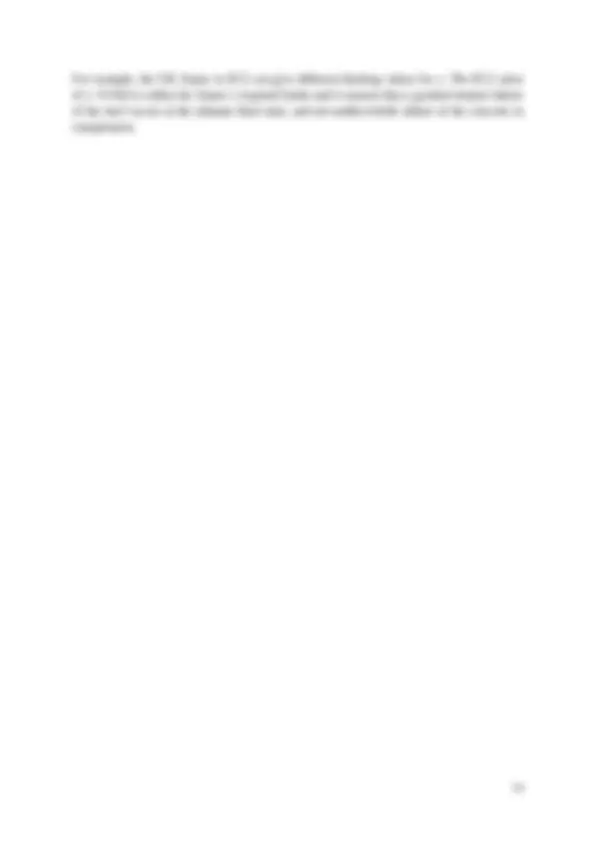
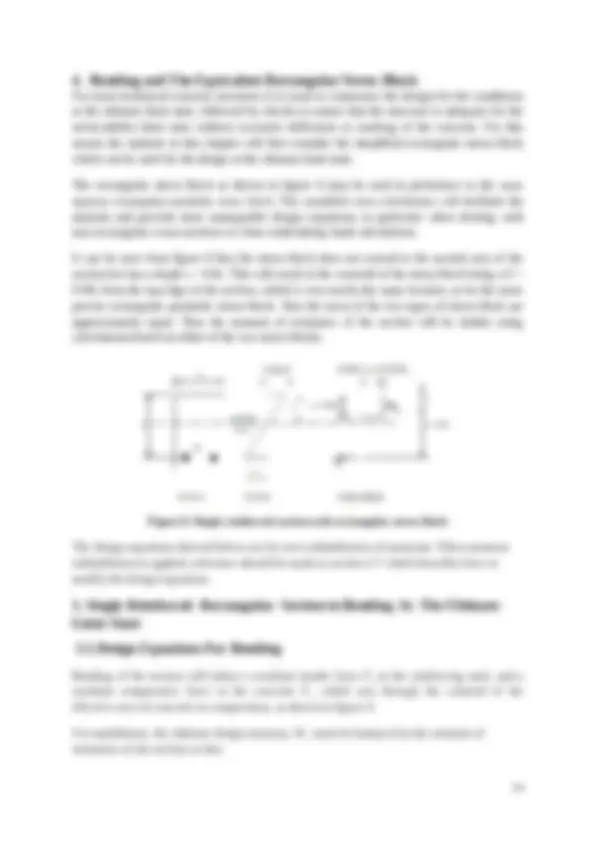
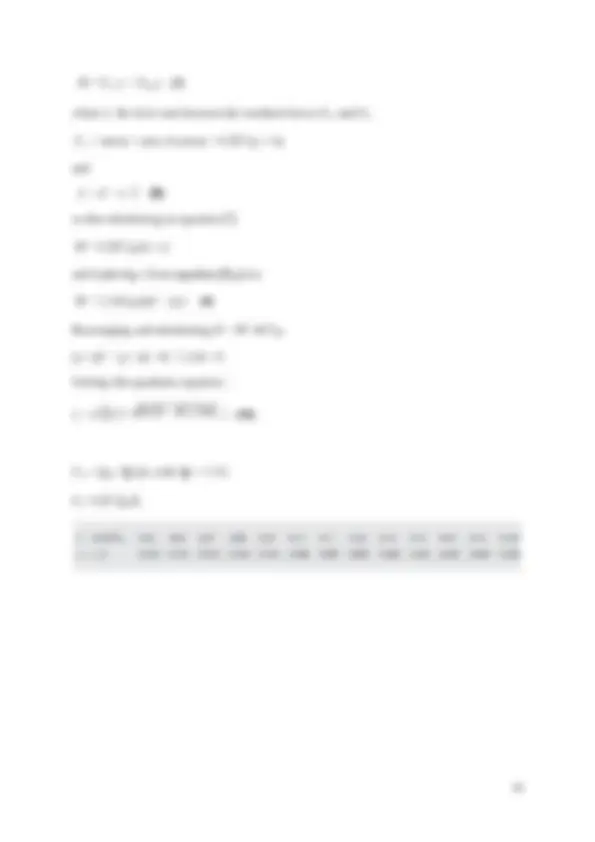
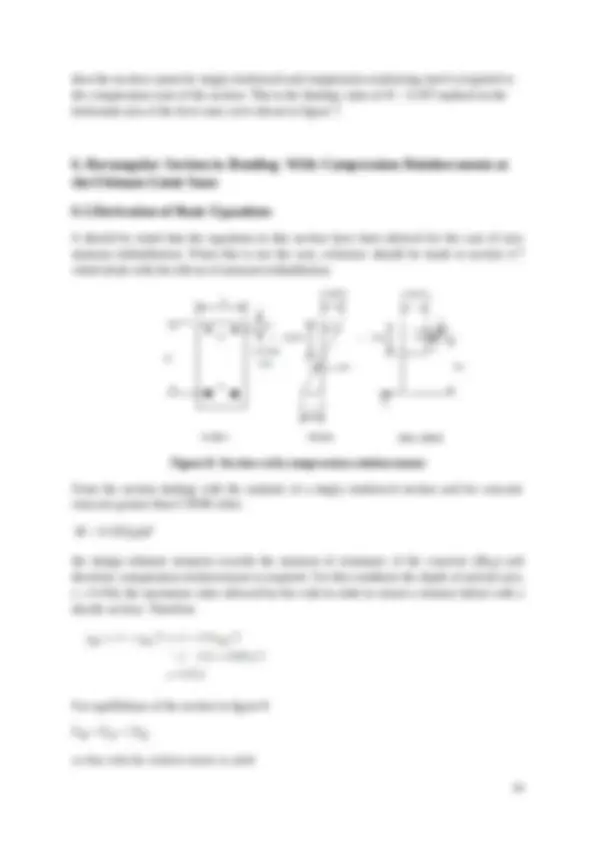
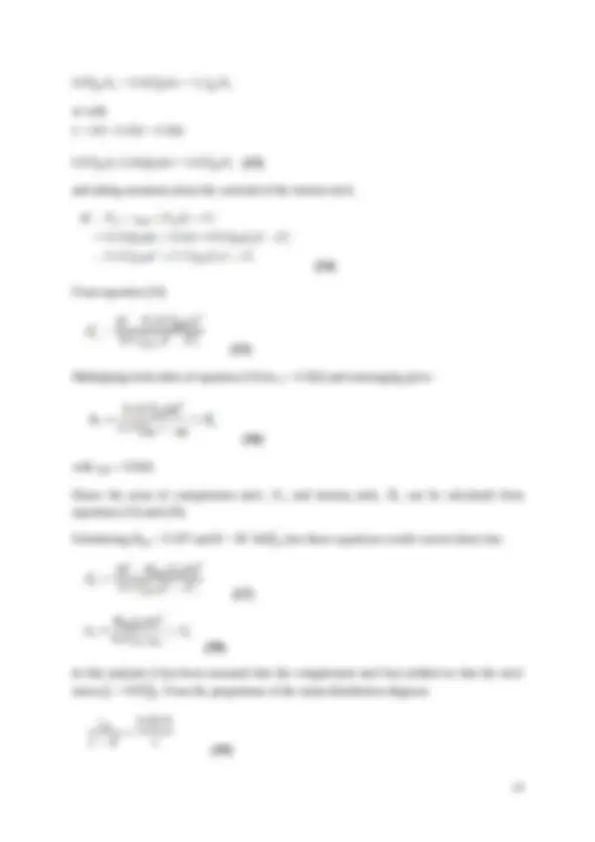
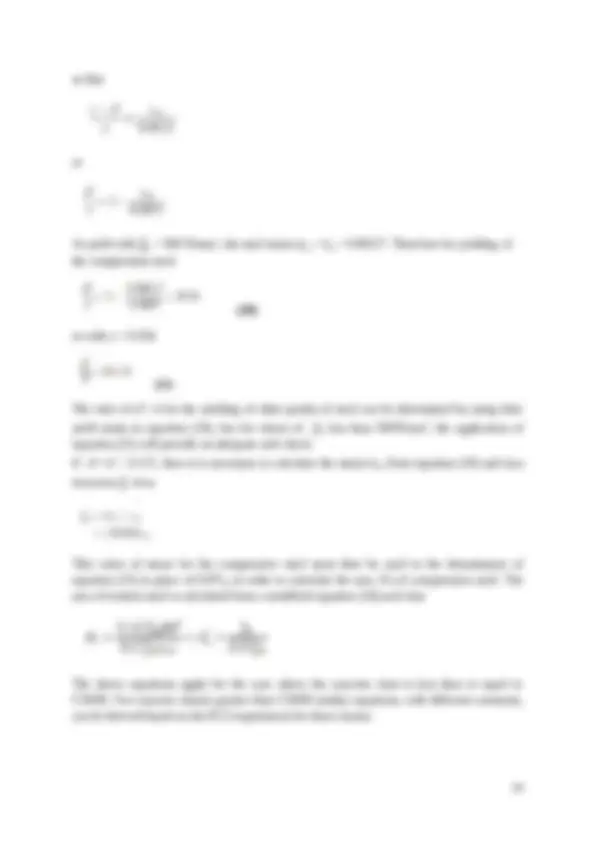

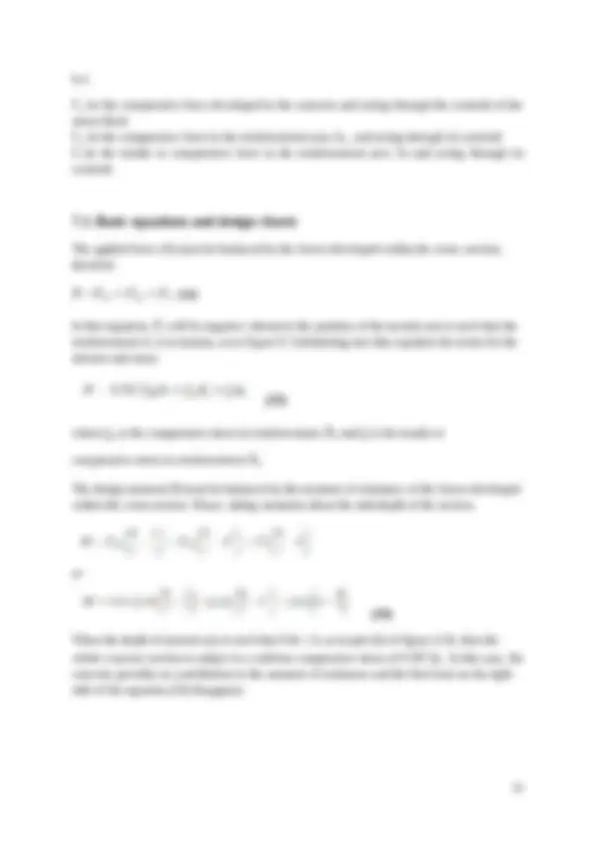
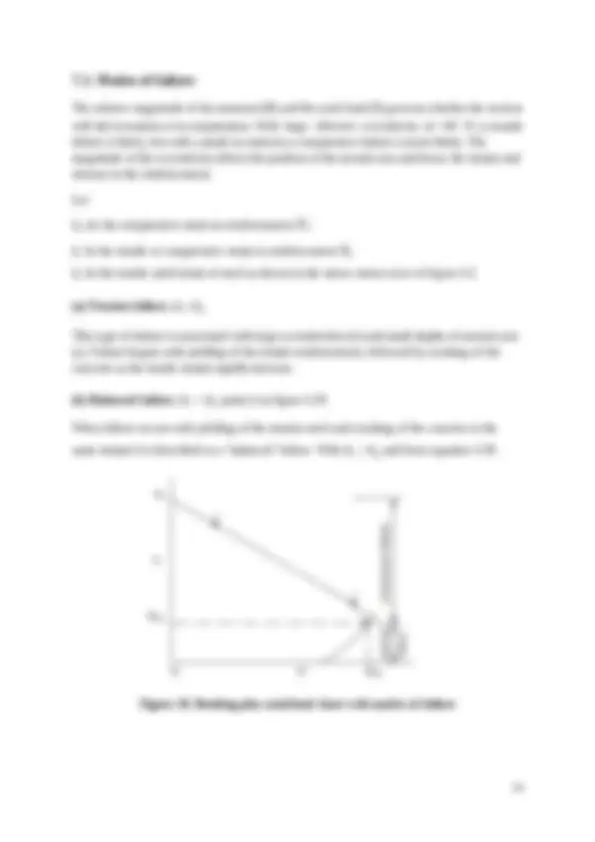
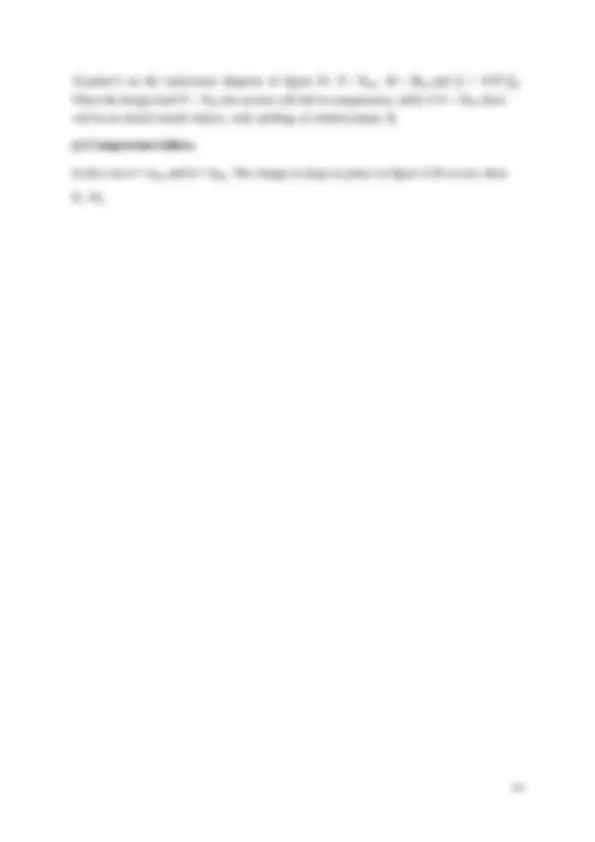
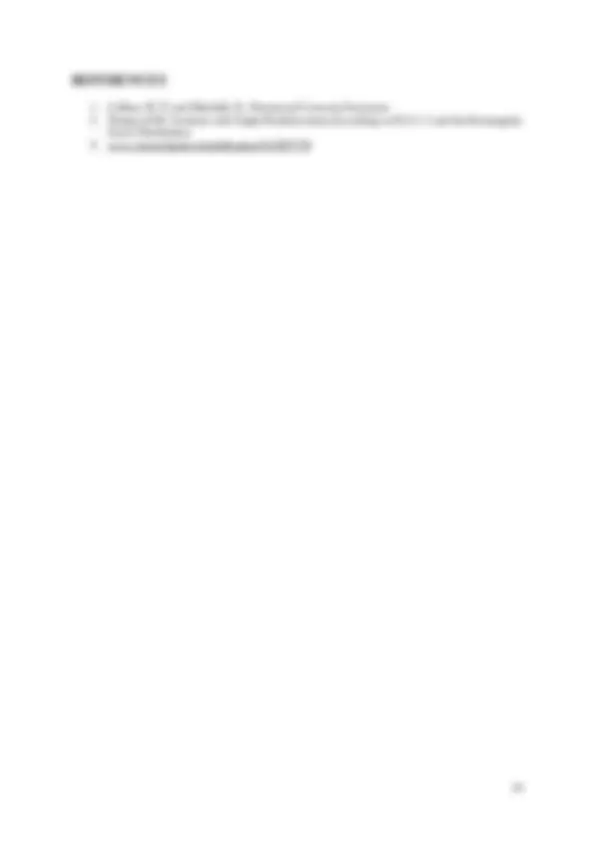
Study with the several resources on Docsity
Earn points by helping other students or get them with a premium plan
Prepare for your exams
Study with the several resources on Docsity
Earn points to download
Earn points by helping other students or get them with a premium plan
Community
Ask the community for help and clear up your study doubts
Discover the best universities in your country according to Docsity users
Free resources
Download our free guides on studying techniques, anxiety management strategies, and thesis advice from Docsity tutors
Concrete and The pre-stressed concrete technology created
Typology: Thesis
1 / 25
This page cannot be seen from the preview
Don't miss anything!
Skopje, 2020
Abstract 3
1.Introduction 4
2.Stress – Strain Relations of Concrete and Reinforced 5
2.1.Concrete 6
2.2.Reinforcing Steel 7
3.Distribution of Strains and Stresses Across a Section in Bending 8
4.Bending and The Equivalent Rectangular Stress Block 9
5.Singly Reinforced Rectangular Section in Bending at The Ultimate Limit State 10
5.1.Design Equations For Bending 10
5.2.The Balanced Section 12
6.Rectangular Section in Bending With Compression Reinforcement at the
Ultimate Limit State
6.1.Derivation of Basic Equations 14
7.Bending Plus Axial Load at the Ultimate Limit State 17
7.1.Basic Equations and Design Charts 18
7.2.Modes of Failure 19
Refence 21
In order to make our modern world more reliable and convenient to live, the studies towards
the safer structures and high durable materials in the field of engineering have reduced the
cross-sectional dimensions and reduced the structure. A big part of these structures is the
weight of the elements. From this point of view, because large stresses ask for too large
cross-sections of reinforced concrete elements, and the weight of the elements gets too big,
the invention of pre-stressed concrete became solution for those cases. Nowadays, one of the
structural composite materials used in the structural system is pre stressed concrete;
increasing research has evolved with advancing technologies and has become one of the most
efficient load bearing system materials. Today it is used in many structures. The pre-stressed
concrete technology created by the pre-tension forces given to the concrete, whether before
the concrete is cast or after the concrete casting, benefits from the advantages of economic
transition, removal of many of the normal apertures and extending the life of the structural
system and is also more economical, more aesthetic and safer. It offers a wide range of
application such as building structures, industrial halls and bridges.
Reinforced concrete, which is one of the engineering terms, is one of the pressure and tensile
resistant construction materials where steel and concrete are used together. Structurally,
concrete exhibits high resistance to stress caused by pressure and steel to tensile stress.
Tensile stress is the resistance of a material to a tensile state. All items break after a certain
period of time. The tensile value at the time the material breaks gives the maximum tensile
stress value. Steel is protected against being used in concrete as it is not resistant to fire and
abrasion. Concrete is insufficient in terms of tensile stress and energy absorption capacity.
When the concrete is equipped with steel, it increases its resistance against pressure and
tensile stress, while it transforms into a building material with high fire resistance due to its
low conductivity. In this sense, concrete and steel complement each other's incomplete
properties, allowing the construction of durable structures. Wherever possible, analyzes of
concrete and steel should be kept simple, and the reinforced concrete elements should be
observed and tested as much as possible.
Manipulation and juggling with equations should never be concealed. The three most
important principles are;
concrete and steel.
section. 3. The resultant forces developed by the section must balance the applied loads for
static equilibrium.
These principles apply regardless of how the stresses and stresses are distributed, or how the
member is loaded or whatever cross-sectional shape is. Derive the basic equations used in
design and the equations necessary for the preparation of design charts. Mostly, analyzes of
the final boundary state are emphasized, but the behavior of the section within the elastic
range and serviceability boundary state is also considered.
Short-term stress–strain curves for concrete and steel are presented in EC2. These curves are
in an idealised form which can be used in the analysis of member sections.
Figure 1. Stress-strain relationship for ordinary concrete
Figure 2. Complete stress-strain curve including post-peak response
characteristic (5 %) cylinder
strength
f
ck
, or cube strength f
ck,cube
, in accordance with EN 206-
The behaviour of structural concrete figure 3 is represented by a parabolic stress– strain
relationship, up to a strain ɛ c
, from which point the strain increases while the stress remains
constant. The ultimate design stress is given by
(1) put numbers in equations
where the factor of 0.85 allows for long-term effects and the difference between the bending
strength and the cylinder crushing strength of the concrete, and μ
c
= 1_._ 5 is the usual partial
safety factor for the strength of concrete. The ultimate strain of ɛ cu
= 0 : 0035 is typical for
classes of concrete ≤ C50/60. Concrete classes ≤ C50/60 will, unless otherwise stated, be
considered throughout this book as these are the classes most commonly used in reinforced
concrete construction. Also for concrete classes higher than C50/60 the defining properties
such as the ultimate strain ɛ cu
vary for each of the higher classes. Design equations for the
higher classes of concrete can in general be obtained using similar procedures to those shown
in the text with the relevant properties and coefficients obtained from the Eurocodes.
The representative short-term design stress–strain curve for reinforcement is given in figure
yk
s
where f yk
is the characteristic yield stress
and μ s
is the partial factor of safety.
Figure 4. Short-term design stress-strain curve for reinforcement
Within the elastic range, the relationship between the stress and strain is
Stress = elastic modulus × strain = E s
× ɛ s
so that the design yield strain is
at the ultimate limit for f yk
= 500 N/mm
2
y
3
It should be noted that EC2 permits the use of an alternative design stress–strain curve to that
shown in figure 4 with an inclined top branch and the maximum strain limited to a value
which is dependent on the class of reinforcement. However the more commonly used curve
shown in figure 4 will be used in this chapter and throughout the text.
The theory of bending for reinforced concrete assumes that the concrete will crack in the
regions of tensile strains and that, after cracking, all the tension is carried by the
reinforcement. It is also assumed that plane sections of a structural member remain plane
after straining, so that across the section there must be a linear distribution of strains.
Figure 5. Section with strain diagram and stress blocks
Figure 5 shows the cross-section of a member subjected to bending, and the resultant strain
diagram, together with three different types of stress distribution in the concrete:
1. The triangular stress distribution applies when the stresses are very nearly proportional to
the strains, which generally occurs at the loading levels encountered under working
conditions and is, therefore, used at the serviceability limit state.
2. The rectangular–parabolic stress block represents the distribution at failure when the
compressive strains are within the plastic range, and it is associated with the design for
the ultimate limit state.
3. The equivalent rectangular stress block is a simplified alternative to the rectangular–
parabolic distribution.
As there is compatibility of strains between the reinforcement and the adjacent concrete, the
steel strains ɛ st
in tension and ɛ sc
in compression can be determined from the strain diagram.
The relationships between the depth of neutral axis ( x ) and the maximum concrete strain ( ɛ cu
and the steel strains are given by
and
For example, the UK Annex to EC2 can give different limiting values for x. The EC2 value
of x =0_._ 45 d is within the Annex’s required limits and it ensures that a gradual tension failure
of the steel occurs at the ultimate limit state, and not sudden brittle failure of the concrete in
compression.
For most reinforced concrete structures it is usual to commence the design for the conditions
at the ultimate limit state, followed by checks to ensure that the structure is adequate for the
serviceability limit state without excessive deflection or cracking of the concrete. For this
reason the analysis in this chapter will first consider the simplified rectangular stress block
which can be used for the design at the ultimate limit state.
The rectangular stress block as shown in figure 6 may be used in preference to the more
rigorous rectangular–parabolic stress block. This simplified stress distribution will facilitate the
analysis and provide more manageable design equations, in particular when dealing with
non-rectangular cross-sections or when undertaking hand calculations.
It can be seen from figure 6 that the stress block does not extend to the neutral axis of the
section but has a depth s = 0_._ 8 x. This will result in the centroid of the stress block being s/ 2 =
0_._ 40 x from the top edge of the section, which is very nearly the same location as for the more
precise rectangular–parabolic stress block. Also the areas of the two types of stress block are
approximately equal. Thus the moment of resistance of the section will be similar using
calculations based on either of the two stress blocks.
Figure 6. Singly reinforced section with rectangular stress block
The design equations derived below are for zero redistribution of moments. When moment
redistribution is applied, reference should be made to section 4.7 which describes how to
modify the design equations.
Bending of the section will induce a resultant tensile force F st
in the reinforcing steel, and a
resultant compressive force in the concrete F cc
which acts through the centroid of the
effective area of concrete in compression, as shown in figure 6.
For equilibrium, the ultimate design moment, M , must be balanced by the moment of
resistance of the section so that
Figure 7. Lever arm curve
Hence (11)
Equations 7 and 9 can be used to design the area of tension reinforcement in a singly
reinforced concrete section to resist an ultimate moment, M.
Equation 10 for the lever arm Ɀ can also be used to set up a table and draw a lever- arm
curve as shown in figure 7. This curve may be used to determine the lever arm, Ɀ instead of
solving equation 10.
The lower limit of Ɀ = 0_._ 82 d in figure 7 occurs when the depth of the neutral axis equals
0_._ 45 d. This is the maximum value allowed by EC2 for a singly reinforced section with
concrete class less than or equal to C50/60 in order to provide a ductile section that will have
a gradual tension type failure.
The concrete section with the depth of neutral axis at the specified maximum depth of 0 : 45 d
is often referred to as the balanced section because at the ultimate limit state the concrete and
tension steel reach their ultimate strains at the same time. This occurs at the maximum
moment of resistance for a singly reinforced section, that is a section with no compression
steel. So for this section with
bal
= 0_._ 45 d
the depth of the stress block is
bal
= 0_._ 8 × 0_._ 45 d = 0_._ 36 d
The force in the concrete stress block is
ccbal
ck
ck
bd
ccbal
stbal
in the
steel. So that
stbal
= 0 : 87 f yk
sbal
ccbal
= 0_._ 204 f ck
bd
Therefore
sbal
ck
yk
So that
which is the steel percentage for a balanced section which should not be exceeded for a
ductile singly reinforced section_._
Thus, for example, with f ck
= 25 N/mm
2
yk
= 500 N/mm
2
bal
ccbal
bal
where
bal
= d — s / 2 = 0_._ 82 d
Substituting for F ccbal
and Ɀ
bal
bal
ck
bd
2
and
When the design moment M d
is such that
s
yk
s
ck
yk
0
s
or with
s = 0.8 × 0.45 d = 0.36 d
yk
s
ck
yk
0
s
and taking moments about the centroid of the tension steel,
From equation (14)
Multiplying both sides of equation (13) by Ɀ
= 0_._ 82 d and rearranging gives
with Ɀ bal
= 0_._ 82 d.
s
s
, can be calculated from
equations (15) and (16).
Substituting K bal
= 0.167 and K = M / bd 2 f ck
into these equations would convert them into:
In this analysis it has been assumed that the compression steel has yielded so that the steel
sc
yk
. From the proportions of the strain distribution diagram:
so that
or
yk
= 500 N/mm
2
, the steel strain ɛ
sc
= ɛ
y
= 0.00217. Therefore for yielding of
the compression steel
or with x = 0_._ 45 d
(21)
The ratio of dꞌ / d for the yielding of other grades of steel can be determined by using their
yk
less than 500N/mm
2
, the application of
equation (21) will provide an adequate safe check.
If dꞌ / d > 0_._ 171, then it is necessary to calculate the strain ɛ sc
from equation (19) and then
sc
from
This value of stress for the compressive steel must then be used in the denominator of
equation (15) in place of 0.87f yk
in order to calculate the area Aꞌs of compression steel. The
area of tension steel is calculated from a modified equation (16) such that
The above equations apply for the case where the concrete class is less than or equal to
C50/60. For concrete classes greater than C50/60 similar equations, with different constants,
can be derived based on the EC2 requirement for these classes.