
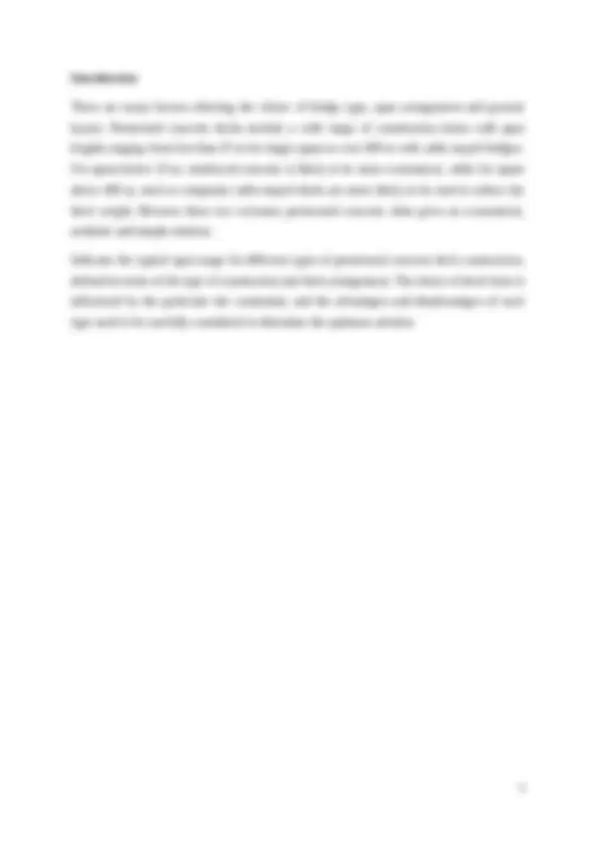
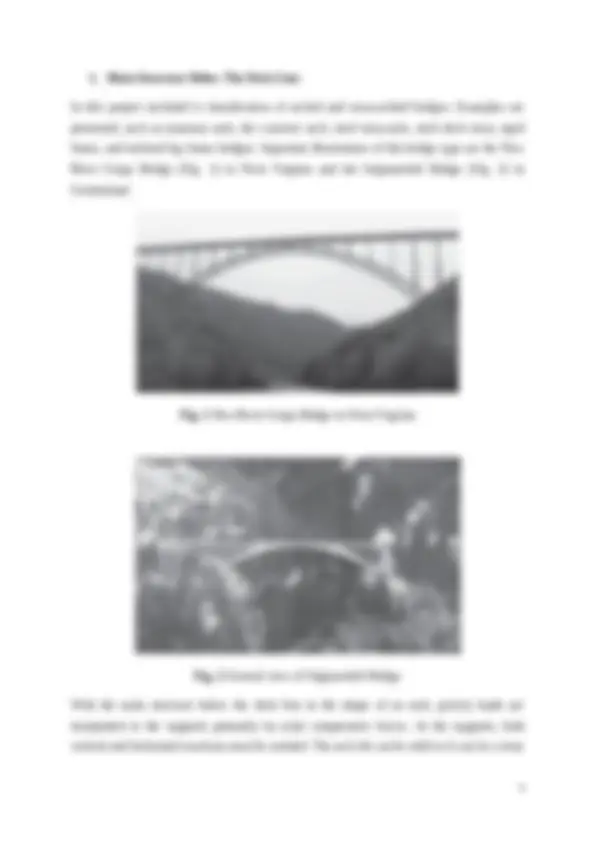
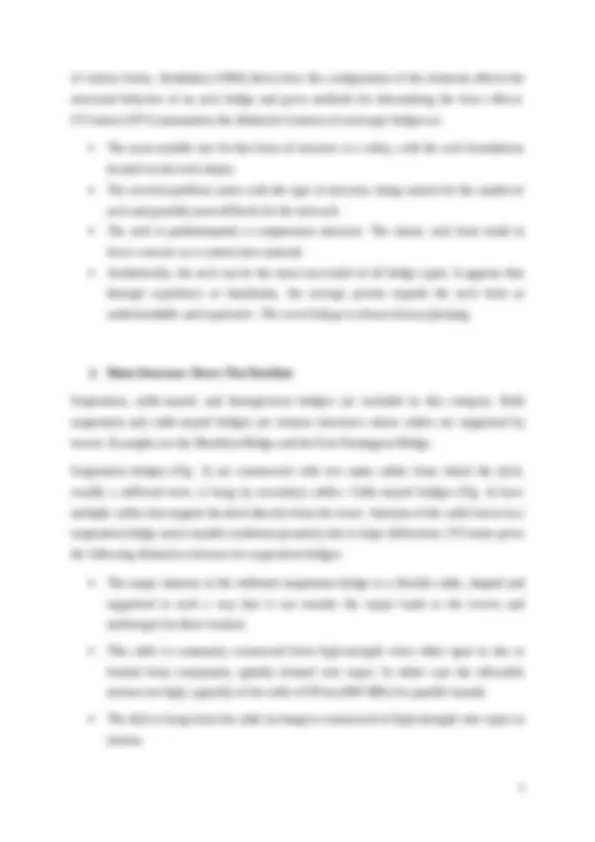
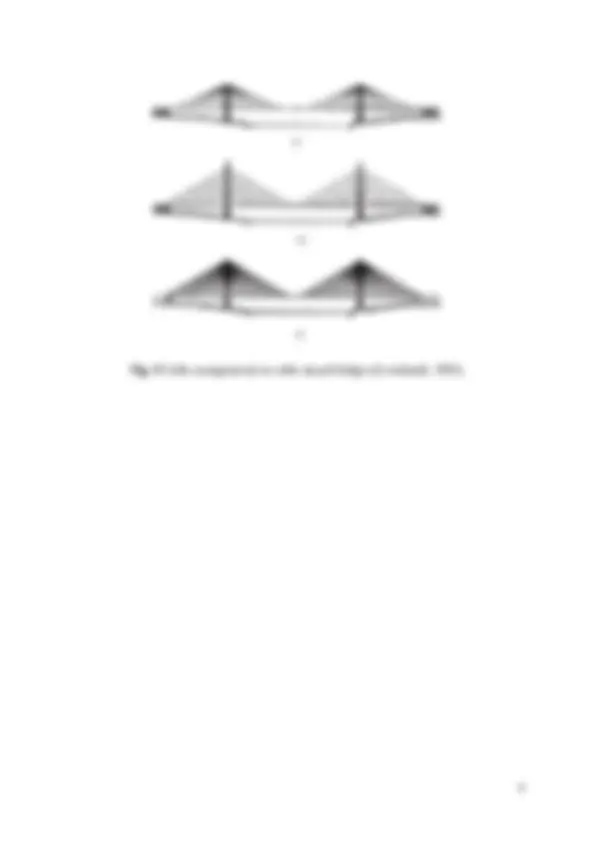
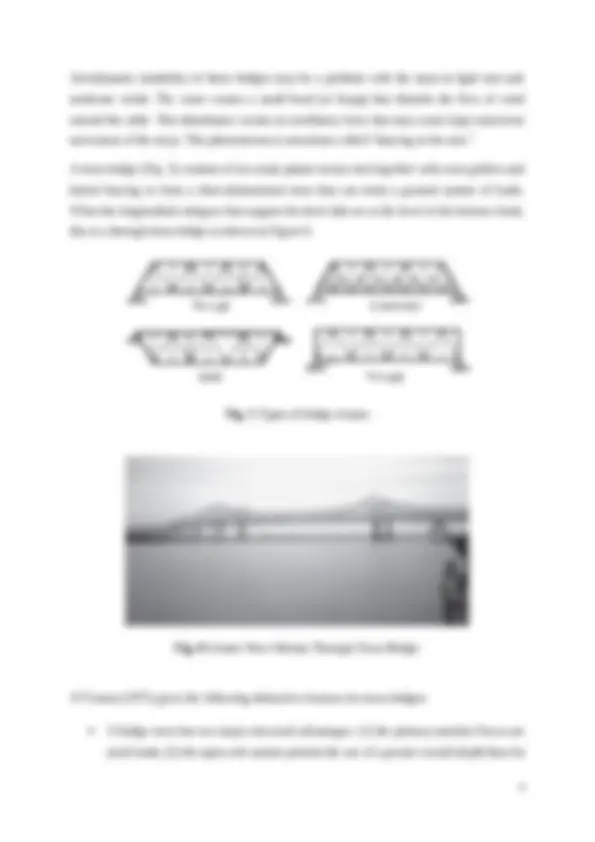
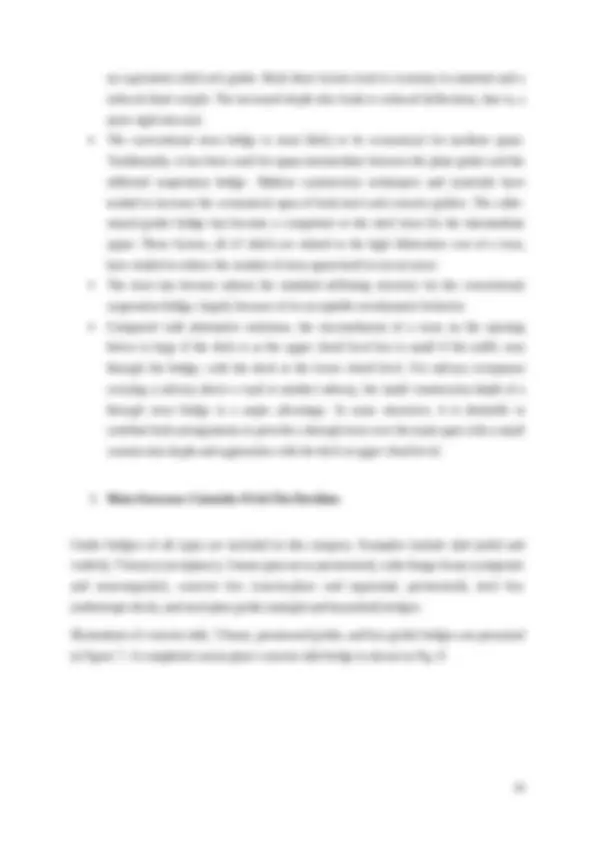
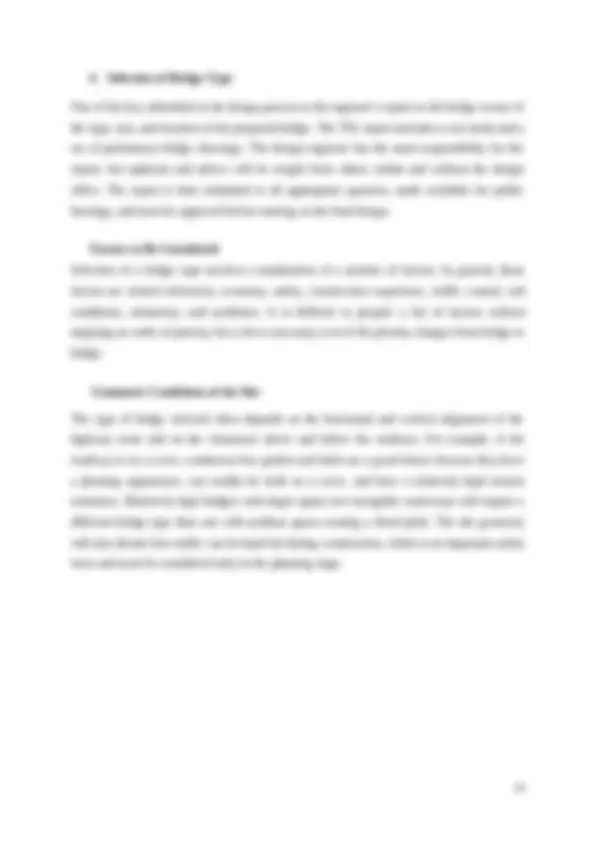
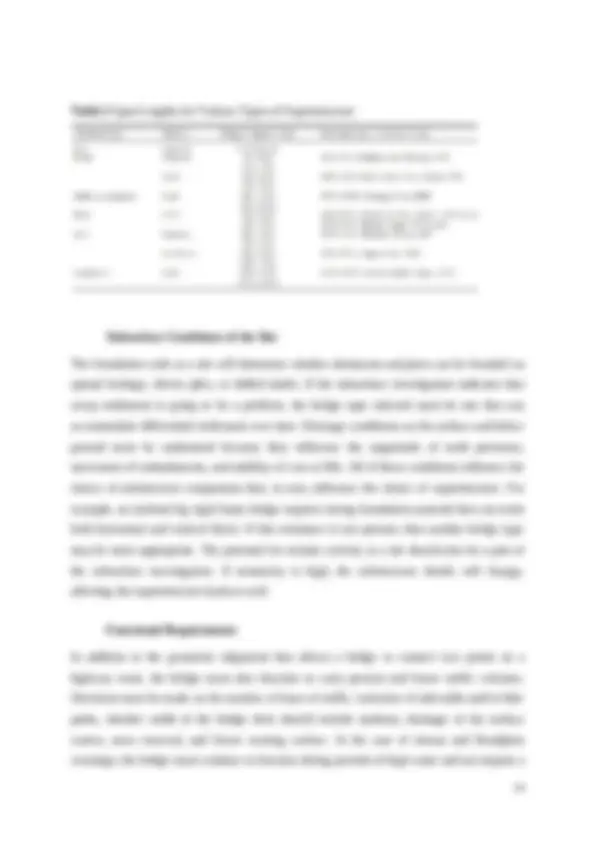
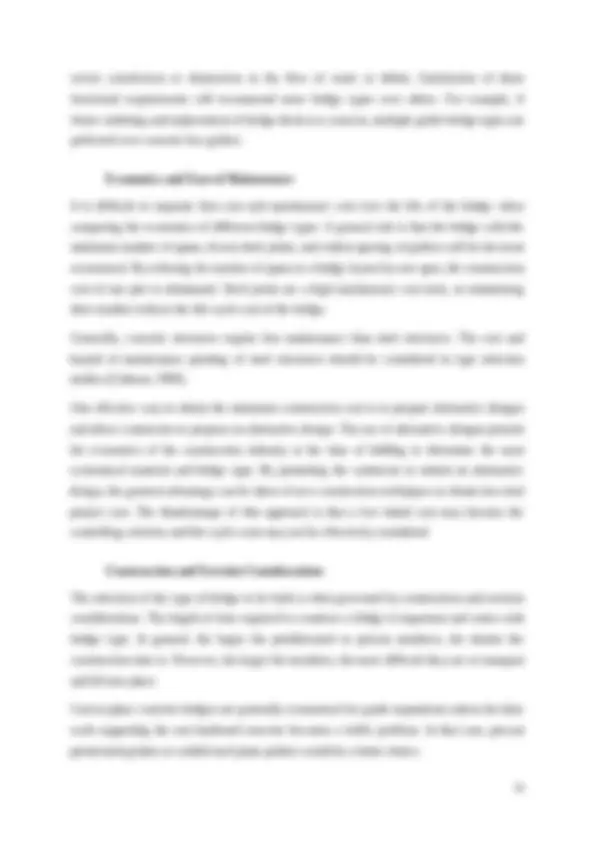
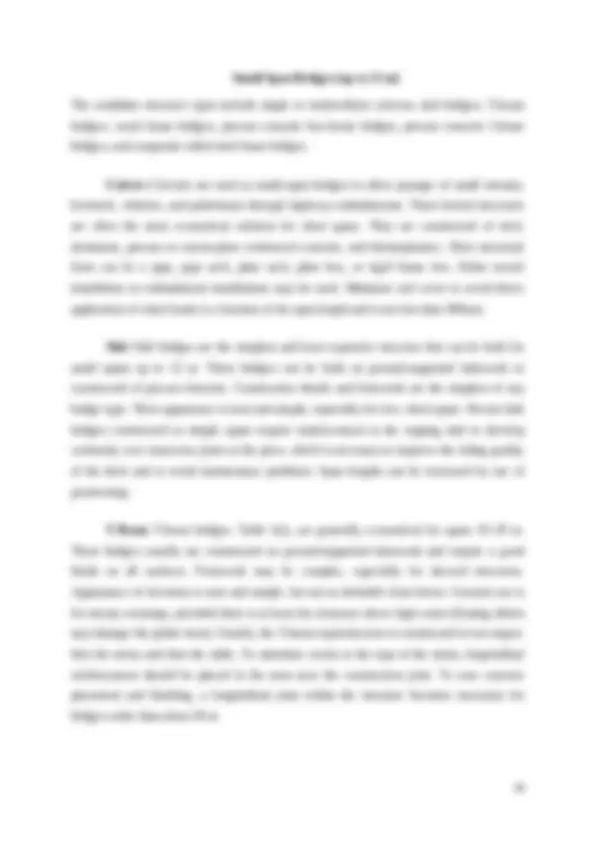
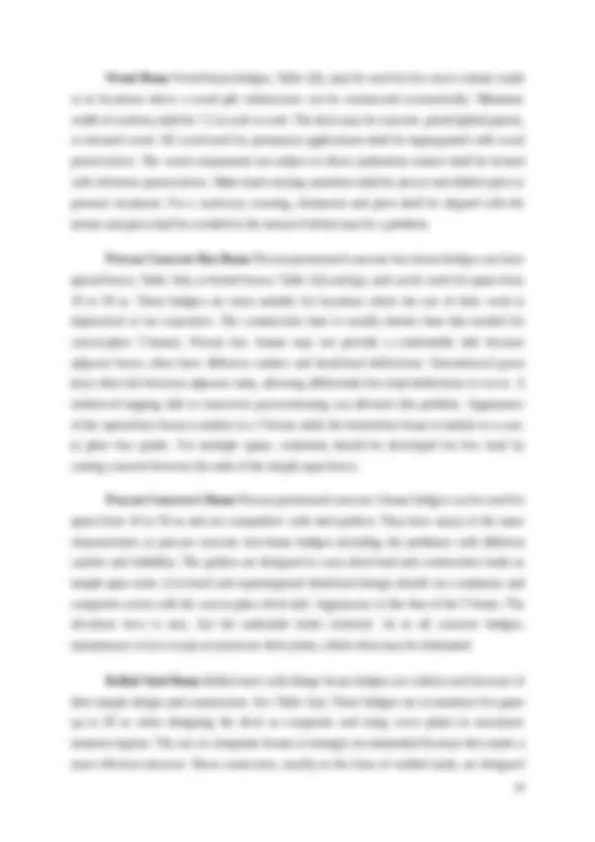
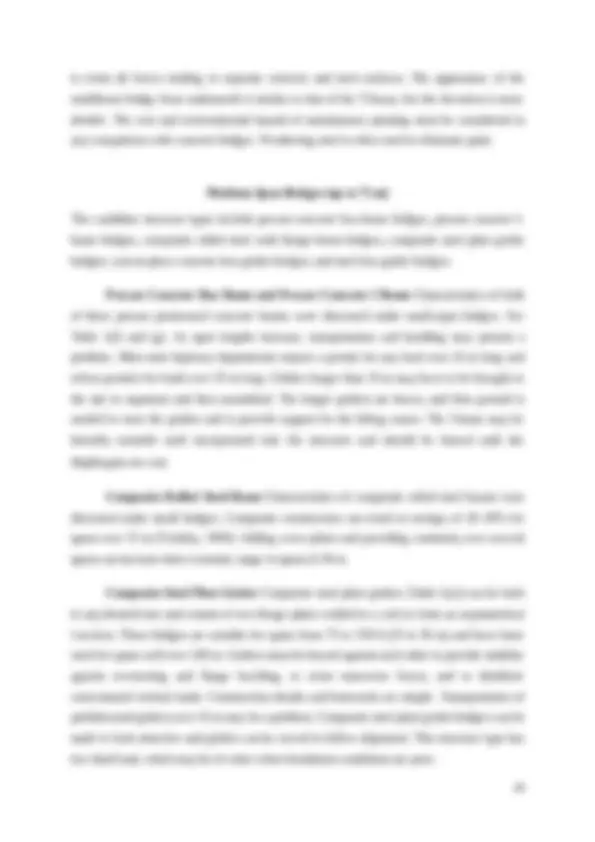
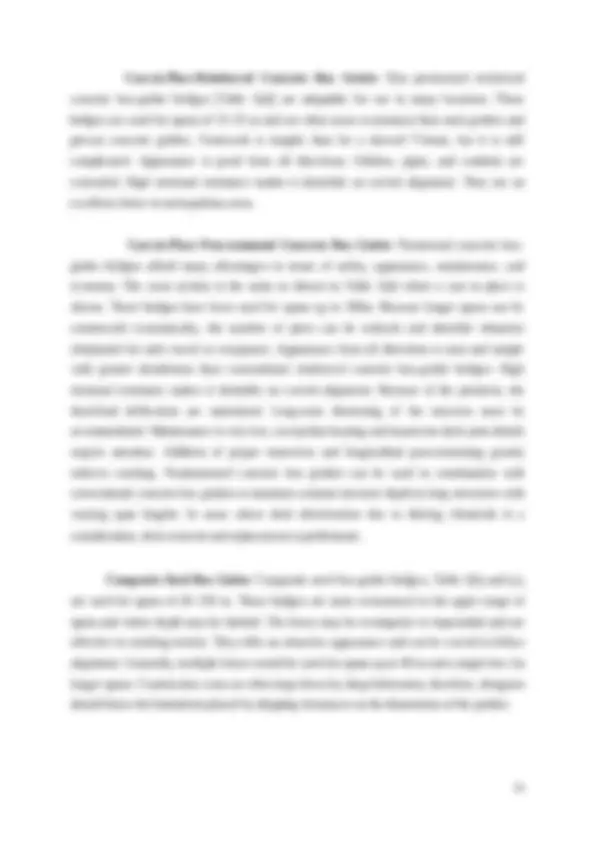
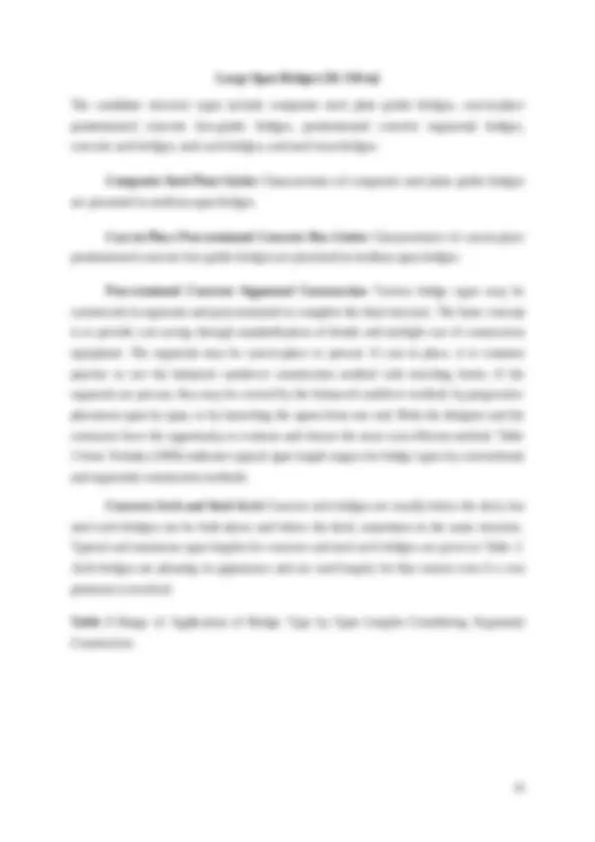
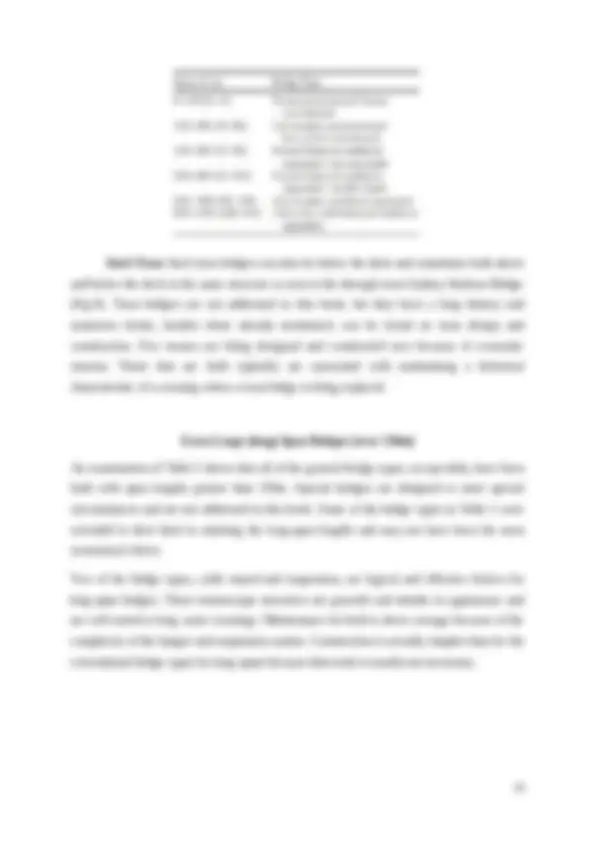
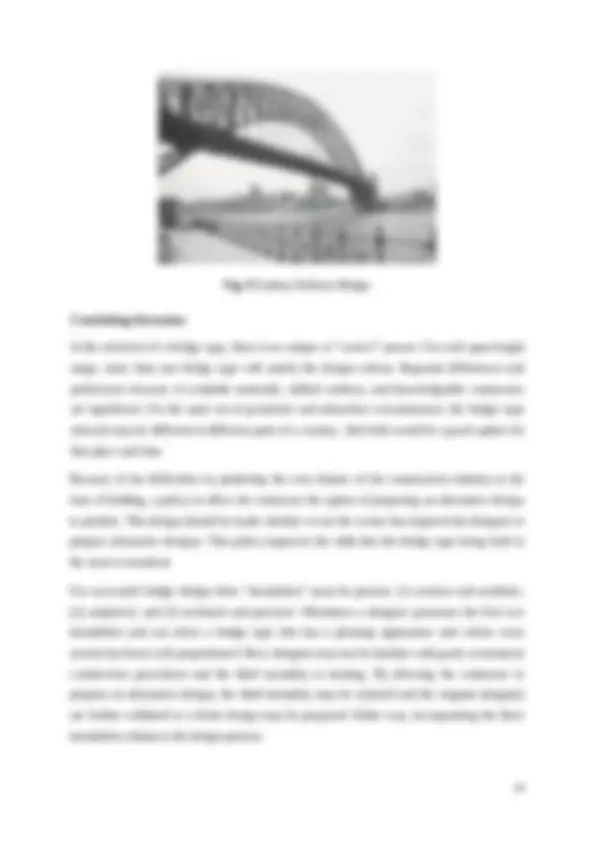
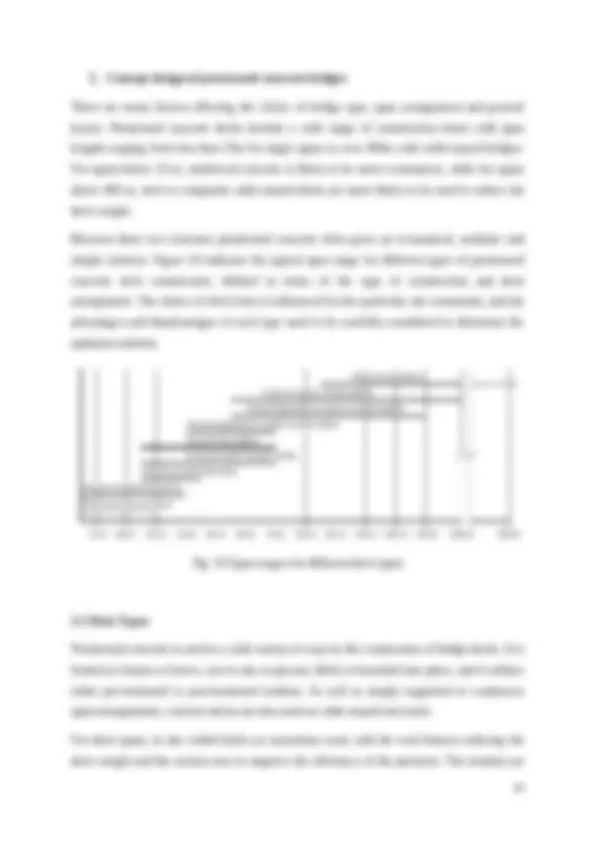
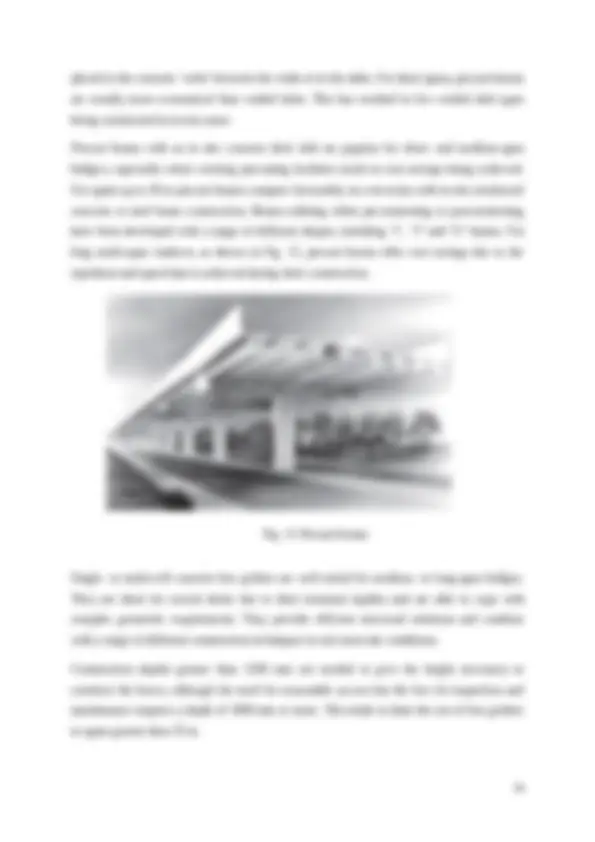
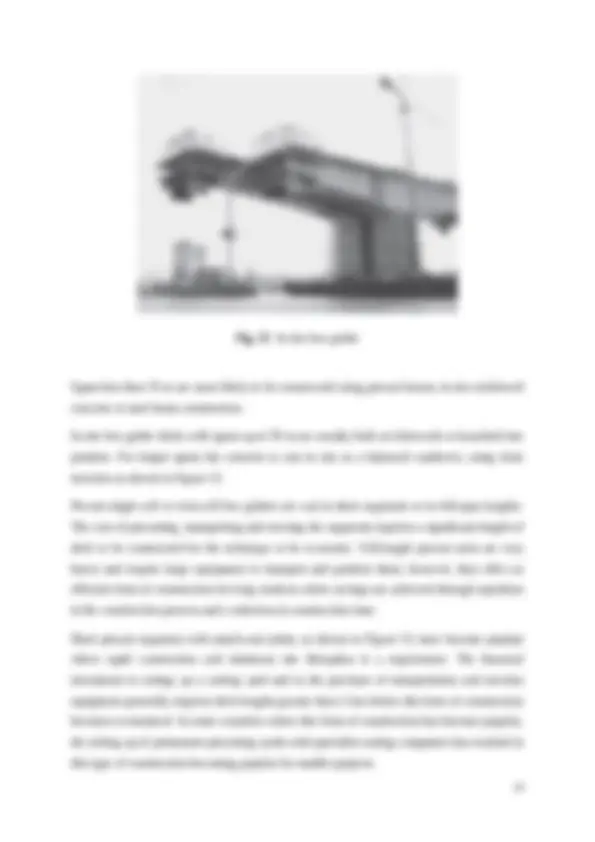
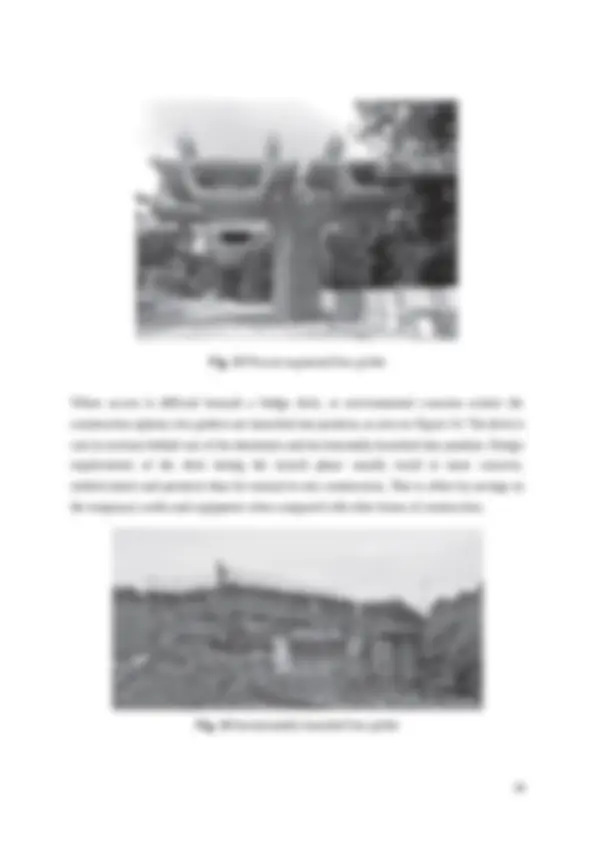
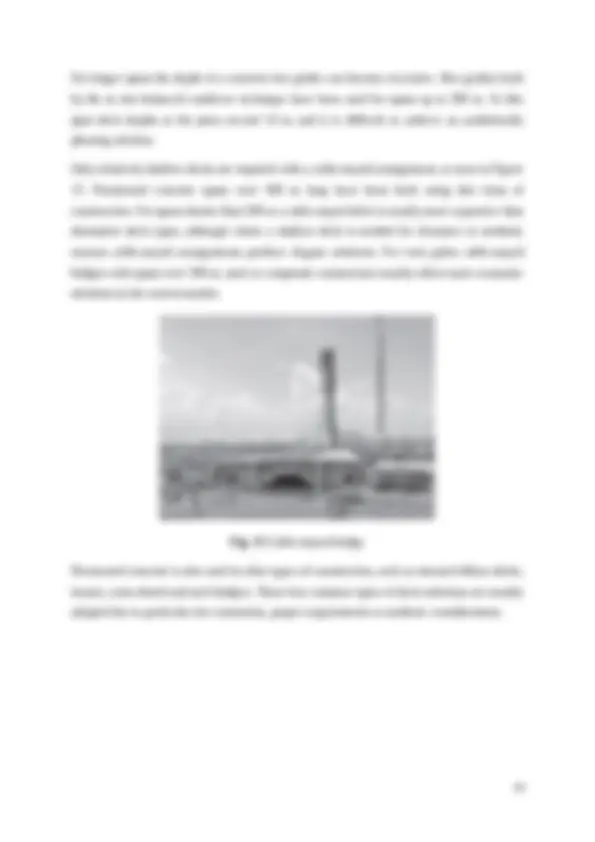
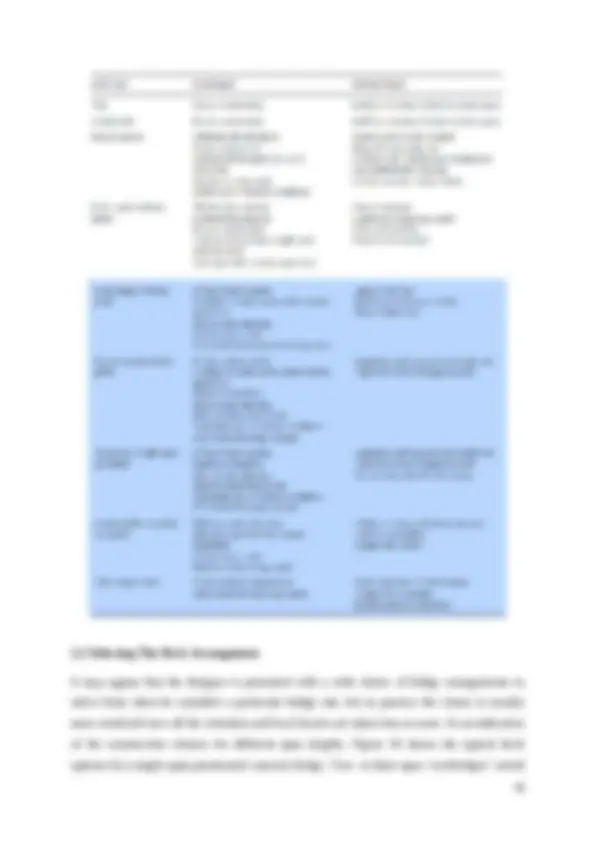
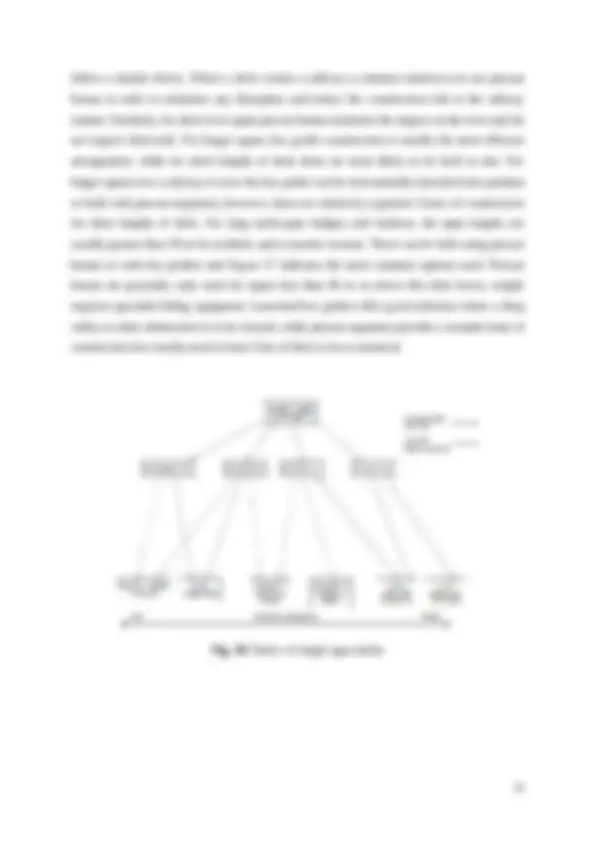
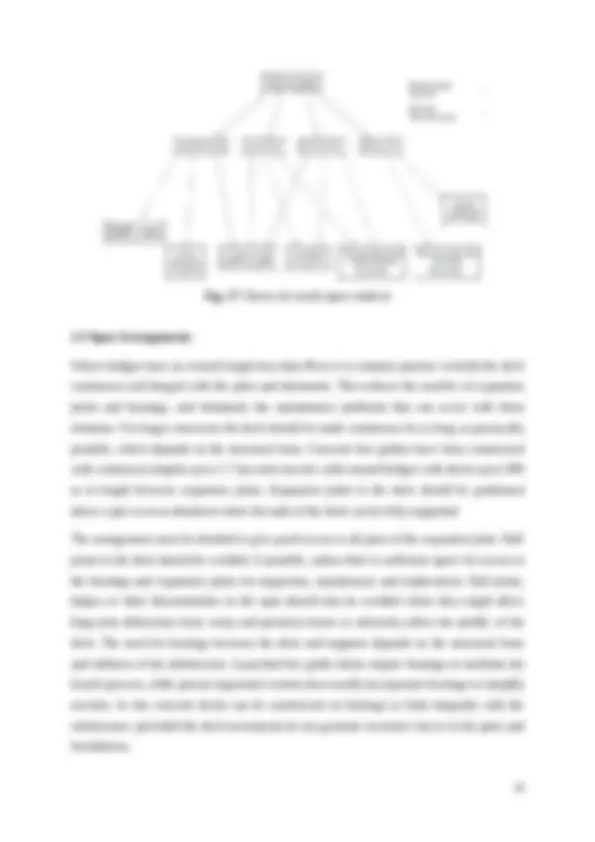
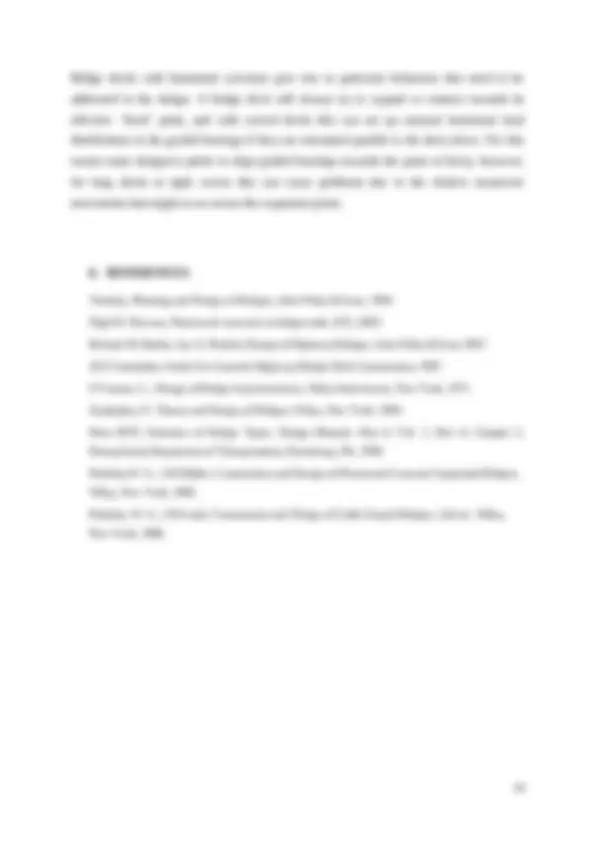
Study with the several resources on Docsity
Earn points by helping other students or get them with a premium plan
Prepare for your exams
Study with the several resources on Docsity
Earn points to download
Earn points by helping other students or get them with a premium plan
Community
Ask the community for help and clear up your study doubts
Discover the best universities in your country according to Docsity users
Free resources
Download our free guides on studying techniques, anxiety management strategies, and thesis advice from Docsity tutors
RC section and includes stress-strain relations of reinforced concrete steel
Typology: Thesis
1 / 33
This page cannot be seen from the preview
Don't miss anything!
Faculty of Engineering Department of Civil Engineering
Graduation Project 2 Mentor: Candidate: Assist. Prof. Dr. Jelena Ristic Emre Gök Skopje, 2019
1. Main Structure Below The Deck Line In this project included is classification of arched and truss-arched bridges. Examples are presented, such as masonry arch, the concrete arch, steel truss-arch, steel deck truss, rigid frame, and inclined leg frame bridges. Important illustrations of this bridge type are the New River Gorge Bridge (Fig. 1) in West Virginia and the Salginatobel Bridge (Fig. 2) in Switzerland. Fig. 1 New River Gorge Bridge in West Virginia Fig. 2 General view of Salginatobel Bridge With the main structure below the deck line in the shape of an arch, gravity loads are transmitted to the supports primarily by axial compressive forces. At the supports, both vertical and horizontal reactions must be resisted. The arch rib can be solid or it can be a truss
of various forms. Xanthakos (1994) shows how the configuration of the elements affects the structural behavior of an arch bridge and gives methods for determining the force effects. O’Connor (1971) summarizes the distinctive features of arch-type bridges as: The most suitable site for this form of structure is a valley, with the arch foundations located on dry rock slopes. The erection problem varies with the type of structure, being easiest for the cantilever arch and possibly most difficult for the tied arch. The arch is predominantly a compression structure. The classic arch form tends to favor concrete as a construction material. Aesthetically, the arch can be the most successful of all bridge types. It appears that through experience or familiarity, the average person regards the arch form as understandable and expressive. The curved shape is almost always pleasing.
2. Main Structure Above The Deckline Suspension, cable-stayed, and through-truss bridges are included in this category. Both suspension and cable-stayed bridges are tension structures whose cables are supported by towers. Examples are the Brooklyn Bridge and the East Huntington Bridge. Suspension bridges (Fig. 3) are constructed with two main cables from which the deck, usually a stiffened truss, is hung by secondary cables. Cable-stayed bridges (Fig. 4) have multiple cables that support the deck directly from the tower. Analysis of the cable forces in a suspension bridge must consider nonlinear geometry due to large deflections. O’Connor gives the following distinctive features for suspension bridges: The major element of the stiffened suspension bridge is a flexible cable, shaped and supported in such a way that it can transfer the major loads to the towers and anchorages by direct tension. This cable is commonly constructed from high-strength wires either spun in situ or formed from component, spirally formed wire ropes. In either case the allowable stresses are high, typically of the order of 90 ksi (600 MPa) for parallel strands. The deck is hung from the cable by hangers constructed of high-strength wire ropes in tension.
Fig. 3 Typical suspension bridge
Fig. 4 Cable arrangements in cable-stayed bridges (Leonhardt, 1991).
an equivalent solid-web girder. Both these factors lead to economy in material and a reduced dead weight. The increased depth also leads to reduced deflections, that is, a more rigid structure. The conventional truss bridge is most likely to be economical for medium spans. Traditionally, it has been used for spans intermediate between the plate girder and the stiffened suspension bridge. Modern construction techniques and materials have tended to increase the economical span of both steel and concrete girders. The cable- stayed girder bridge has become a competitor to the steel truss for the intermediate spans. These factors, all of which are related to the high fabrication cost of a truss, have tended to reduce the number of truss spans built in recent years. The truss has become almost the standard stiffening structure for the conventional suspension bridge, largely because of its acceptable aerodynamic behavior. Compared with alternative solutions, the encroachment of a truss on the opening below is large if the deck is at the upper chord level but is small if the traffic runs through the bridge, with the deck at the lower chord level. For railway overpasses carrying a railway above a road or another railway, the small construction depth of a through truss bridge is a major advantage. In some structures, it is desirable to combine both arrangements to provide a through truss over the main span with a small construction depth and approaches with the deck at upper chord level.
Fig. 7 Types of concrete bridges. Fig. 8 Cast-in-place posttensioned voided slab bridge (Dorton, 1991) Girder-type bridges carry loads primarily in shear and flexural bending. This action is relatively inefficient when compared to axial compression in arches and to tensile forces in suspension structures. A girder must develop both compressive and tensile forces within its own depth. A lever arm sufficient to provide the internal resisting moment separates these internal forces. Because the extreme fibers are the only portion of the cross section fully stressed, it is difficult to obtain an efficient distribution of material in a girder cross section. Additionally, stability concerns further limit the stresses and associated economy from a material utilization perspective. But from total economic perspective slab–girder bridges provide an economical and long-lasting solution for the vast majority of bridges.
4. Selection of Bridge Type One of the key submittals in the design process is the engineer’s report to the bridge owner of the type, size, and location of the proposed bridge. The TSL report includes a cost study and a set of preliminary bridge drawings. The design engineer has the main responsibility for the report, but opinions and advice will be sought from others within and without the design office. The report is then submitted to all appropriate agencies, made available for public hearings, and must be approved before starting on the final design. Factors to Be Considered Selection of a bridge type involves consideration of a number of factors. In general, these factors are related tofunction, economy, safety, construction experience, traffic control, soil conditions, seismicity, and aesthetics. It is difficult to prepare a list of factors without implying an order of priority, but a list is necessary even if the priority changes from bridge to bridge. Geometric Conditions of the Site The type of bridge selected often depends on the horizontal and vertical alignment of the highway route and on the clearances above and below the roadway. For example, if the roadway is on a curve, continuous box girders and slabs are a good choice because they have a pleasing appearance, can readily be built on a curve, and have a relatively high torsion resistance. Relatively high bridges with larger spans over navigable waterways will require a different bridge type than one with medium spans crossing a flood plain. The site geometry will also dictate how traffic can be hand led during construction, which is an important safety issue and must be considered early in the planning stage.
Table 2 Span Lengths for Various Types of Superstructure Subsurface Conditions of the Site The foundation soils at a site will determine whether abutments and piers can be founded on spread footings, driven piles, or drilled shafts. If the subsurface investigation indicates that creep settlement is going to be a problem, the bridge type selected must be one that can accommodate differential settlement over time. Drainage conditions on the surface and below ground must be understood because they influence the magnitude of earth pressures, movement of embankments, and stability of cuts or fills. All of these conditions influence the choice of substructure components that, in turn, influence the choice of superstructure. For example, an inclined leg rigid frame bridge requires strong foundation material that can resist both horizontal and vertical thrust. If this resistance is not present, then another bridge type may be more appropriate. The potential for seismic activity at a site should also be a part of the subsurface investigation. If seismicity is high, the substructure details will change, affecting the superstructure loads as well. Functional Requirements In addition to the geometric alignment that allows a bridge to connect two points on a highway route, the bridge must also function to carry present and future traffic volumes. Decisions must be made on the number of lanes of traffic, inclusion of sidewalks and/or bike paths, whether width of the bridge deck should include medians, drainage of the surface waters, snow removal, and future wearing surface. In the case of stream and floodplain crossings, the bridge must continue to function during periods of high water and not impose a
The availability of skilled labor and specified materials also influences the choice of a particular bridge type. For example, if no precast plants for prestressed girders are located within easy transport, a steel fabrication plant is located nearby that could make the steel structure more economical. However, other factors in the construction industry may be at work. The primary way to determine which bridge type is more economical is to bid alternative designs. Designers are often familiar with bid histories and local economics and have significant experience regarding the lowest first cost. Design–Build Option In the early years of bridge building, the design–build option was traditional. An owner would express an interest in having a bridge built at a particular location and solicit proposals from engineers for the design and construction of the bridge. On other occasions an engineer may see the need for a bridge and make presentations to potential owners of the merits of a particular design. Such was the case in the building of the Brooklyn Bridge. John Roebling convinced influential people in Manhattan and Brooklyn to charter the New York Bridge Company to promote and finance his design for a great suspension bridge across the East River. The company hired his son, Washington Roebling, as chief engineer responsible for executing his father’s design, preparing drawings and specifications, and supervising the construction. All services for designing and building the bridge were the responsibility of one entity. This design–build practice of single-source responsibility faded somewhat at the end of the nineteenth century. The conventional approach became the design–bid–build model where an owner commissions an engineer to prepare drawings and specifications and separately selects a construction contractor by competitive bidding. The objective of the design–bid–build approach is to obtain the quality product defined by the drawings and specifications at a reasonable price. The approach works well with the checks and balances between the engineer and contractor when the separate parties work well together. Difficulties can occur when things go wrong on the job site or in the design office. There can be a lot of “finger pointing” that the other entity was responsible for the problem. This adversarial situation can increase the financial risk for all involved. To alleviate some of the problems of unclear lines of responsibility, there has been a trend in recent years toward a return to the design–build option. One company is selected by the owner to prepare the engineering design and to be the construction contractor. This approach almost
assures that the design group will possess the three essential mentalities: creative, analytical, and knowledge of construction techniques. If there is a question about the quality of the work or there are construction delays, only one entity is responsible. One objection to the design– build option is the absence of checks and balances because the same party that supplies a product approves it. It is important that the owner has staff people who are knowledgeable and can make independent judgments about the quality of the work provided. Legal Considerations One of the components of the model of the bridge design process is the constraint put on the design procedure by regulations. These regulations are usually beyond the control of the engineer, but they are real and must be considered. Examples of regulations that will determine what bridge type can be built and where it can be located include: Permits over Navigable Waterways, National Environmental Policy Act, Department of Transportation Act, National Historic Preservation Act, Clean Air Act, Noise Control Act, Fish and Wildlife Coordination Act, Endangered Species Act, Water Bank Act, Wild and Scenic Rivers Act, Prime and Unique Farmlands, and Executive Orders on Floodplain Management and Protection of Wetlands. Engineers who are not conscious of the effect the design of a bridge has on the environment will soon become conscious once they begin preparing the environmental documentation required by these acts. In addition to the environmental laws and acts defining national policy, local and regional politics are also of concern. Commitments to officials or promises made to communities often must be honored and may preclude other nonpolitical issues. 4.1 Bridge Types Used for Different Span Lengths Once a preliminary span length has been chosen, comparative studies are conducted to find the bridge type best suited to the site. For each group of bridge spans (small, medium, and large), experience has shown that certain bridge types are more appropriate than others. This experience can be found in design aids prepared by associations, state agencies, and consulting firms. The comments that follow on common bridge types used for different span lengths are based on the experience of American entities, ACI-ASCE Committee 343 (1988), Caltrans (1990), and Penn DOT (1993).
Wood Beam Wood beam bridges, Table 1(l), may be used for low truck volume roads or in locations where a wood pile substructure can be constructed economically. Minimum width of roadway shall be 7.2 m curb to curb. The deck may be concrete, glued/spiked panels, or stressed wood. All wood used for permanent applications shall be impregnated with wood preservatives. The wood components not subject to direct pedestrian contact shall be treated with oil-borne preservatives. Main load-carrying members shall be precut and drilled prior to pressure treatment. For a waterway crossing, abutments and piers shall be aligned with the stream and piers shall be avoided in the stream if debris may be a problem. Precast Concrete Box Beam Precast prestressed concrete box-beam bridges can have spread boxes, Table 1(b), or butted boxes, Table 1(f) and (g), and can be used for spans from 10 to 50 m. These bridges are most suitable for locations where the use of false work is impractical or too expensive. The construction time is usually shorter than that needed for cast-in-place T-beams. Precast box beams may not provide a comfortable ride because adjacent boxes often have different camber and dead-load deflections. Unreinforced grout keys often fail between adjacent units, allowing differential live-load deflections to occur. A reinforced topping slab or transverse post-tensioning can alleviate this problem. Appearance of the spread-box beam is similar to a T-beam while the butted-box beam is similar to a cast- in place box girder. For multiple spans, continuity should be developed for live load by casting concrete between the ends of the simple-span boxes. Precast Concrete I-Beam Precast prestressed concrete I-beam bridges can be used for spans from 10 to 50 m and are competitive with steel girders. They have many of the same characteristics as precast concrete box-beam bridges including the problems with different camber and ridability. The girders are designed to carry dead load and construction loads as simple-span units. Live-load and superimposed dead-load design should use continuity and composite action with the cast-in-place deck slab. Appearance is like that of the T-beam: The elevation view is nice, but the underside looks cluttered. As in all concrete bridges, maintenance is low except at transverse deck joints, which often may be eliminated. Rolled Steel Beam Rolled steel wide-flange beam bridges are widely used because of their simple design and construction. See Table 1(a). These bridges are economical for spans up to 30 m when designing the deck as composite and using cover plates in maximum moment regions. The use of composite beams is strongly recommended because they make a more efficient structure. Shear connectors, usually in the form of welded studs, are designed
to resist all forces tending to separate concrete and steel surfaces. The appearance of the multibeam bridge from underneath is similar to that of the T-beam, but the elevation is more slender. The cost and environmental hazard of maintenance painting must be considered in any comparison with concrete bridges. Weathering steel is often used to eliminate paint. Medium-Span Bridges [up to 75 m] The candidate structure types include precast concrete box-beam bridges, precast concrete I- beam bridges, composite rolled steel wide flange beam bridges, composite steel plate girder bridges, cast-in-place concrete box-girder bridges, and steel box-girder bridges. Precast Concrete Box Beam and Precast Concrete I Beam Characteristics of both of these precast prestressed concrete beams were discussed under small-span bridges. See Table 1(f) and (g). As span lengths increase, transportation and handling may present a problem. Most state highway departments require a permit for any load over 24 m long and refuse permits for loads over 35 m long. Girders longer than 35 m may have to be brought to the site in segments and then assembled. The longer girders are heavy, and firm ground is needed to store the girders and to provide support for the lifting cranes. The I-beam may be laterally unstable until incorporated into the structure and should be braced until the diaphragms are cast. Composite Rolled Steel Beam Characteristics of composite rolled steel beams were discussed under small bridges. Composite construction can result in savings of 20–30% for spans over 15 m (Troitsky, 1994). Adding cover plates and providing continuity over several spans can increase their economic range to spans of 30 m. Composite Steel Plate Girder Composite steel plate girders [Table 1(a)] can be built to any desired size and consist of two flange plates welded to a web to form an asymmetrical I-section. These bridges are suitable for spans from 75 to 150 ft (25 to 50 m) and have been used for spans well over 100 m. Girders must be braced against each other to provide stability against overturning and flange buckling, to resist transverse forces, and to distribute concentrated vertical loads. Construction details and formwork are simple. Transportation of prefabricated girders over 35 m may be a problem. Composite steel plate girder bridges can be made to look attractive and girders can be curved to follow alignment. This structure type has low dead load, which may be of value when foundation conditions are poor.