
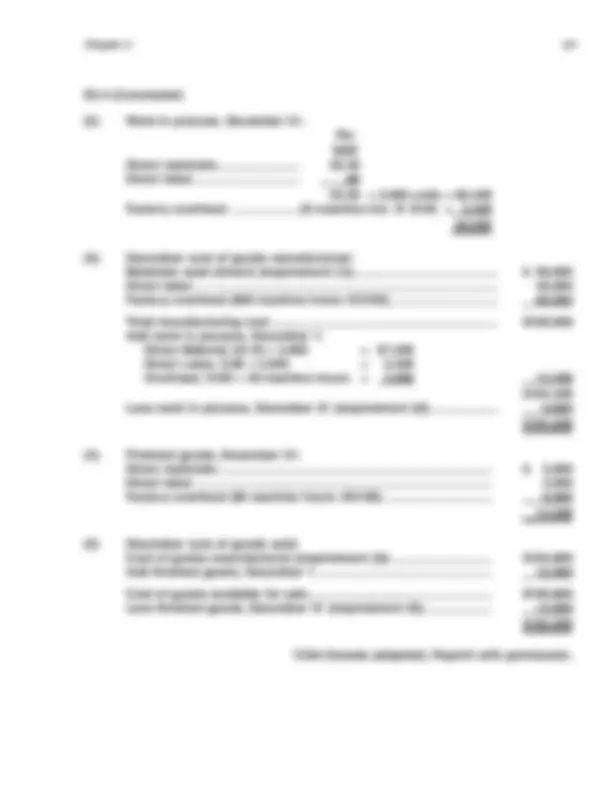
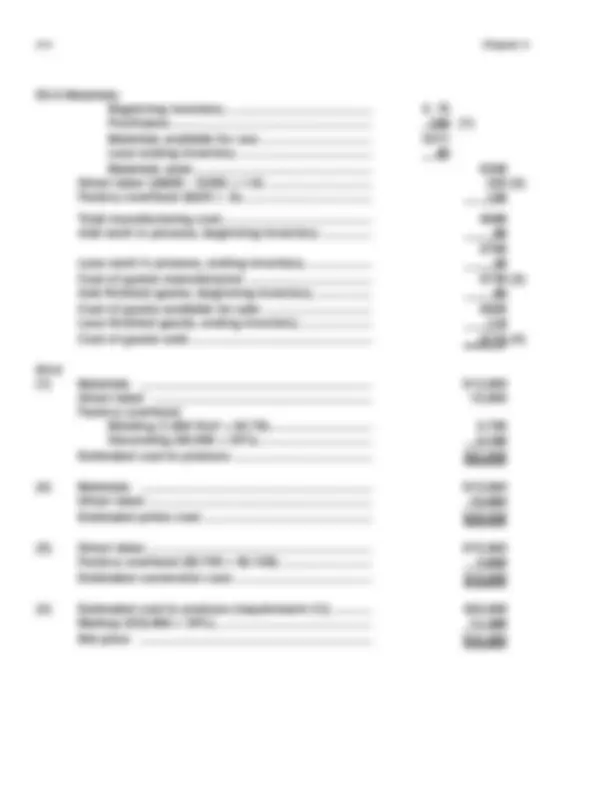
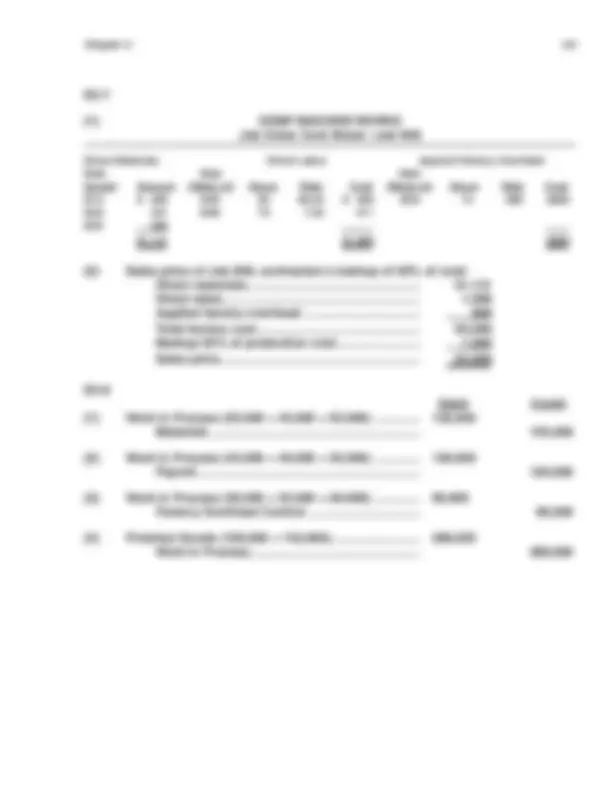
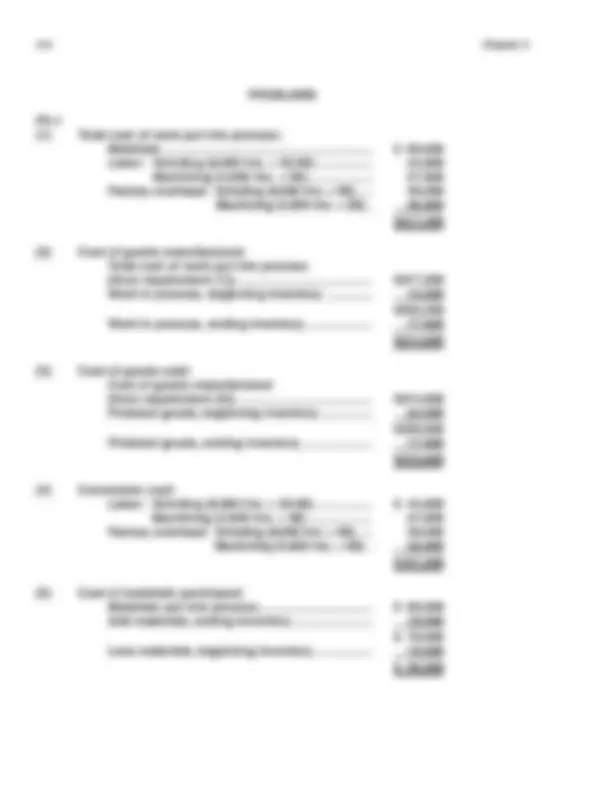
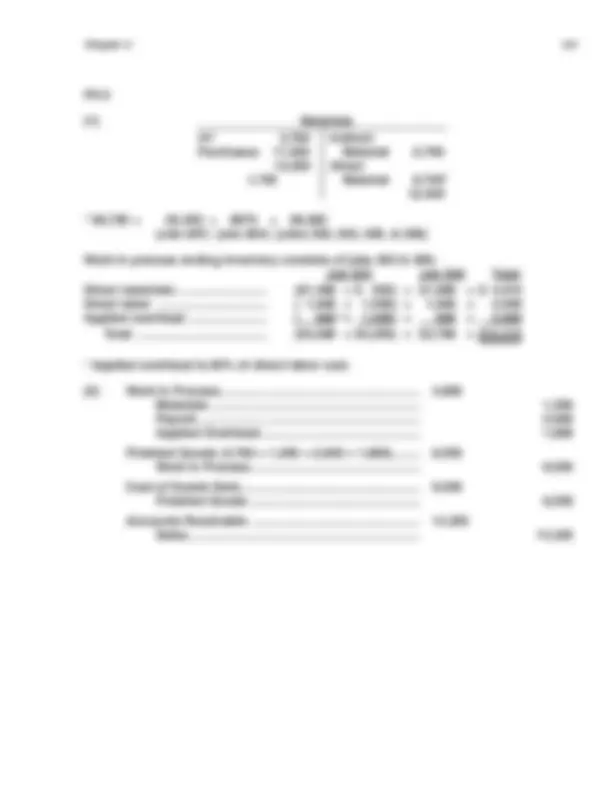

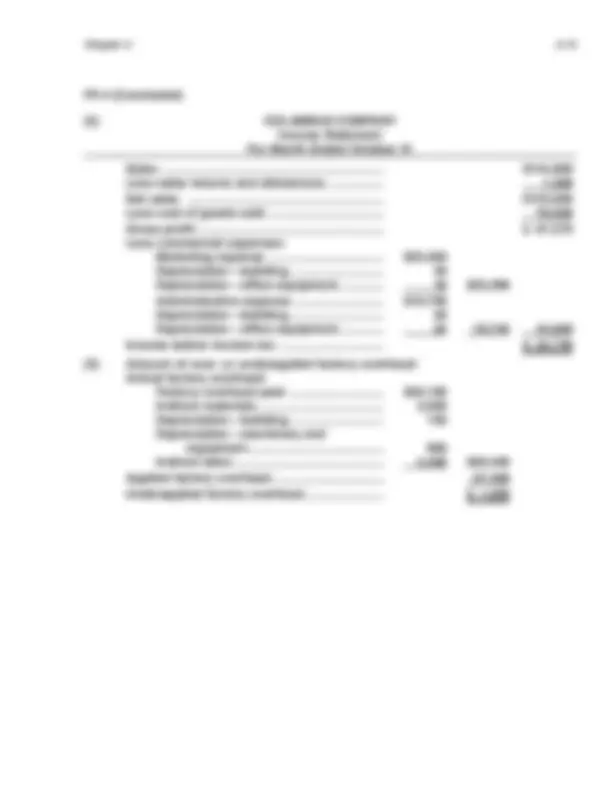
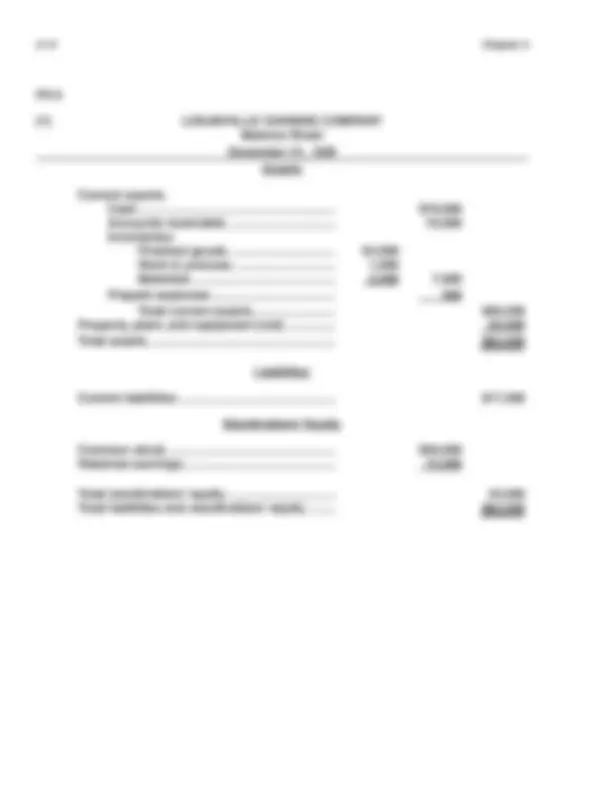
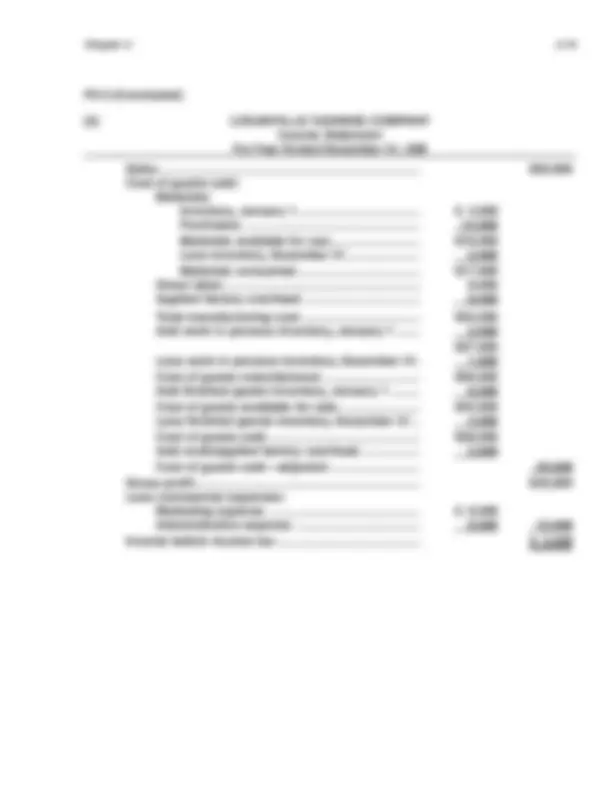
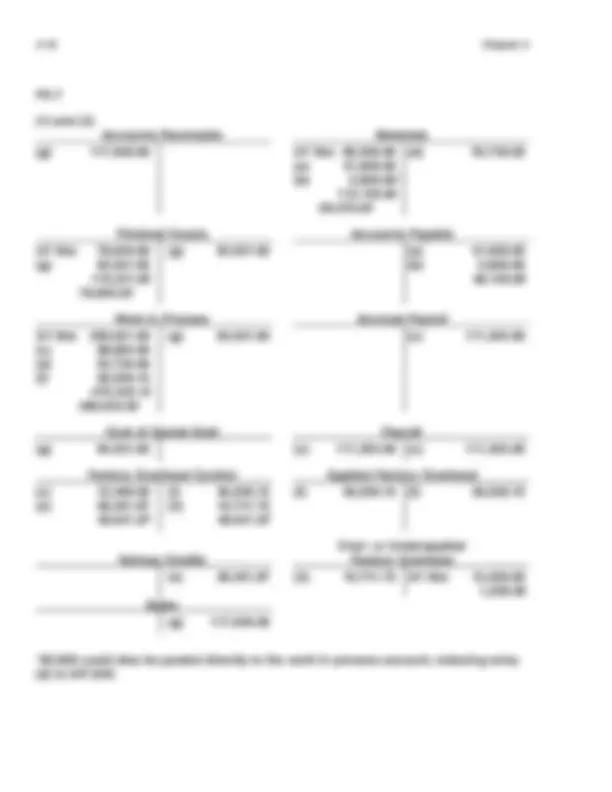
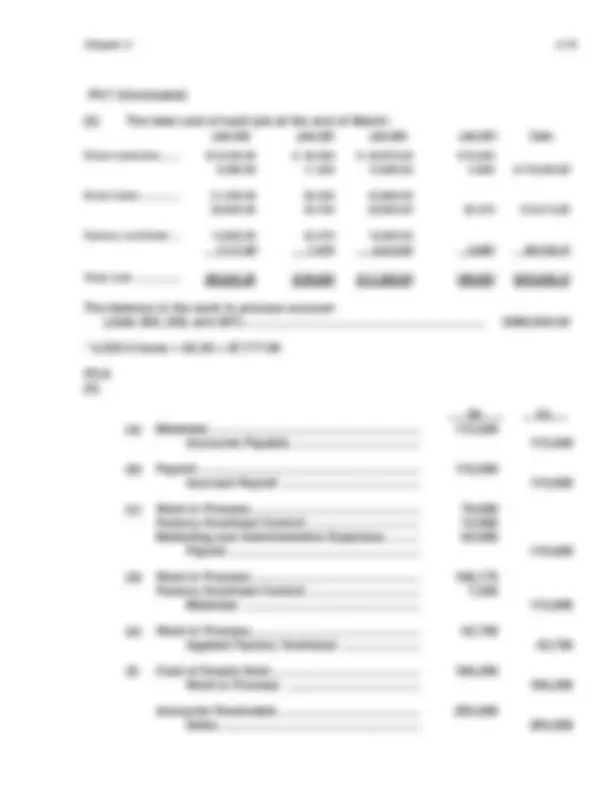
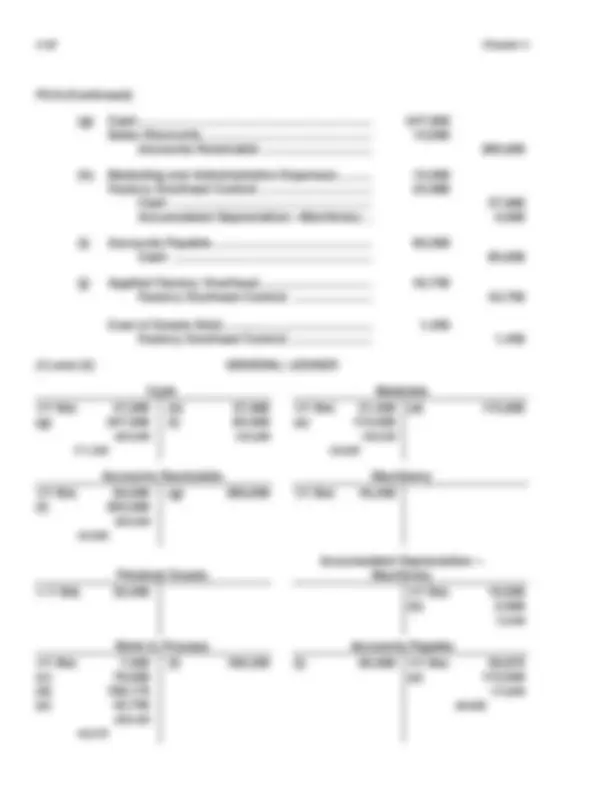
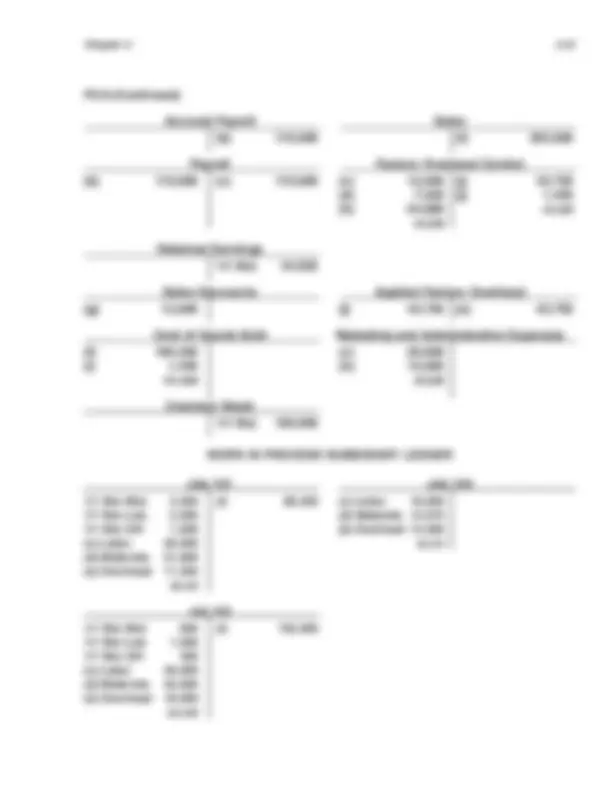
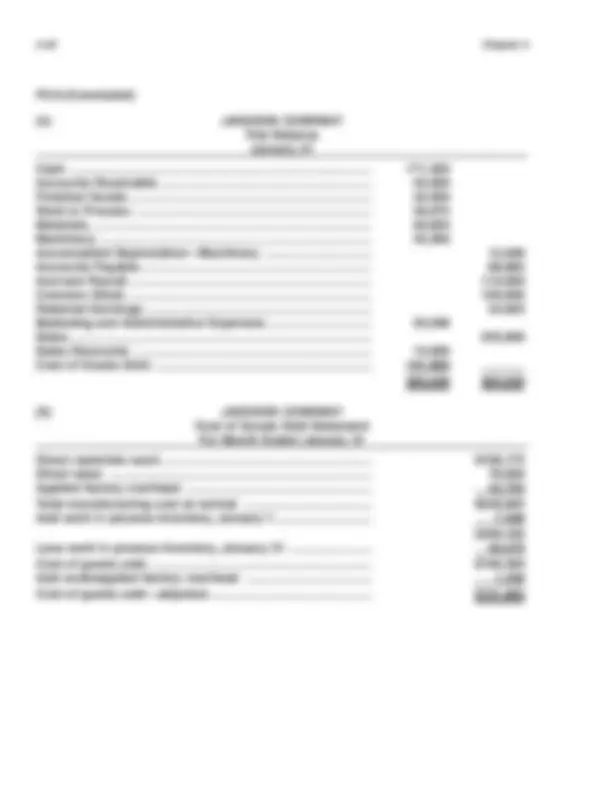
Study with the several resources on Docsity
Earn points by helping other students or get them with a premium plan
Prepare for your exams
Study with the several resources on Docsity
Earn points to download
Earn points by helping other students or get them with a premium plan
Community
Ask the community for help and clear up your study doubts
Discover the best universities in your country according to Docsity users
Free resources
Download our free guides on studying techniques, anxiety management strategies, and thesis advice from Docsity tutors
This document delves into the intricacies of job order costing, a method used to track and allocate costs for specific orders or contracts. It explains the process of accumulating costs for materials, labor, and factory overhead, highlighting the importance of cost control and comparison of actual costs to estimates. The document also discusses the use of job order cost sheets for tracking costs and comparing them to budgets, emphasizing the control function they serve. It provides a clear understanding of the principles and applications of job order costing, making it a valuable resource for students and professionals in accounting and finance.
Typology: Assignments
1 / 22
This page cannot be seen from the preview
Don't miss anything!
5-
Q5-1. The cost attached to a product is an amount assigned by the costing methods used—an amount controlled by the circumstances, assumptions, and limitations of the method under which it was compiled. Product costs are composites of historical outlay that have, perhaps, been modified by estimates or stan- dards, by processes assigning or prorating expenditures to periods, or by tracing the direct costs and allocating the indirect costs to particular products so that the total period outlay is spread over the aggregate output. Despite these shortcomings, product costs are useful in costing inventories, comparing prices and total unit cost, measuring current profit or loss, and indicating the minimum cost below which a sales price cannot go in the long run. Some confusion will result at times in using cost information in making manage- ment decisions unless information relevant only to the decision is used. Q5-2. The primary objective in job order costing is to determine the cost of materials, labor, and factory overhead used to produce a specific order or contract. Cost estimates are made when the order is taken, and the job order procedures are designed to reveal costs as the order goes through production, thereby giving an opportunity to control costs. Q5-3. The type of cost accumulation method used by a company will be determined by the type of manufacturing operations performed. A manufacturing company should use process cost accumulation for product costing pur- poses when like units are continuously mass produced; when custom-made or unique goods are produced, job order costing would be more appropriate. Process costing is often used in industries such as chemicals, food processing, oil, mining, rubber, and electrical appliances. With a continuous mass produc- tion of like units, the center of attention is the individual process (usually a department).
The unit costs by cost category as well as total unit cost for each process (department) are necessary for product costing purposes. Q5-4. A job order cost sheet is used: (a) to keep track of the direct materials and direct labor used on a job plus an appro- priate share of factory overhead; (b) to compare actual costs to estimated costs; (c) as a subsidiary ledger for the work in process account. Q5-5. The work in process account is a control account in the general ledger, reflecting total costs assigned or applied to jobs. The individ- ual job cost sheets form the work in process account’s subsidiary ledger, indicating the direct materials, direct labor, and factory over- head charged to each job. Q5-6. Job order cost sheets serve a control func- tion. Comparisons are made between esti- mates of job costs and costs actually accumulated for the job. In addition, cost con- trol is enhanced by accumulating direct mate- rials and labor as well as factory overhead costs by cost centers or departments, and by comparing the actual costs to cost center budgets. Q5-7. Actual factory overhead consists of the day- by-day costs that are actually experienced and incurred by the company. Applied factory overhead is the overhead charged to jobs based on the predetermined factory overhead rate. This rate is created by dividing total esti- mated overhead by total estimated number of units (or any other appropriate base). The dif- ference between actual and applied factory overhead is the over- or underapplied factory overhead. Q5-8. The characteristic of a service business that makes likely the use of job order costing is that all jobs are not alike and cost information for each job is desired.
E5-1 Job 5575 Direct material............................................................... $24, Direct labor.................................................................... 22, Applied overhead ......................................................... 10, Total job cost ....................................................... $56,
E5-2 Job 5576 Direct material............................................................... $ 4, Direct labor.................................................................... 2, Applied overhead ......................................................... 2, Cost to date.......................................................... $ 9,
(1) The amount of direct labor in finished goods: Finished goods ............................................................. $37, Materials included in finished goods ($15,500 – $3,200) 12, Direct labor and factory overhead in finished goods $25,
Let X = direct labor in finished goods 1.8X = $25,200 direct labor and factory overhead in finished goods X = $14,000 direct labor in finished goods
(2) The amount of factory overhead in finished goods: X = $14, .8X = .8($14,000) .8X = $11,200 factory overhead in finished goods
E5- (1) December materials used: Materials inventory, December 1............... $ 8, Materials purchased ................................... $87, Freight-in .................................................... 1,500 88,
Materials available ...................................... $96, Materials inventory, December 31............. 6, $90,
Factory overhead charged to work in process Direct labor charged to woork in process
5-2 Chapter 5
Direct Materials Direct Labor Applied Factory Overhead Date Date Date
(2) Cost of goods manufactured:
(3) Cost of goods sold:
P5-2 (Concluded)
(3) Cost of goods manufactured = cost of jobs finished in April. Job 205: Direct material ............................ $ 2, Direct labor ................................. 2,100 (105 direct labor hours × $20) Applied overhead ....................... 1,680 (105 direct labor hours × $16) Total Job 205........................... $ 6,
Job 202 ................................................. 9,550 (see requirement (2)) Job 204 ................................................. 6, Job 207 ................................................. 5, Total ......................................... $28,
(4) Actual overhead (1,375 + 2,500 + 2,700 + 2,790) ....... $9, Applied overhead: Jobs 202, 203, 205, 206 (330* hours × $16) ....... $ 5, Job 207 ................................................................. 1, Job 204 ($1,760 – $960) ...................................... 800 Total applied overhead............................... 7, Underapplied................................................................. $1, *100 + 75 + 105 + 50
(5) Jobs 201, 202, and 205 were sold. Their costs are $8,450 + $9,550 + $6,280 = $24,280. Sales ($24,280 × 1.5) .................................................... $36, Cost of goods sold....................................................... (24,280) Underapplied overhead................................................ (1,765) Gross profit for April .................................................... $10,
Finished Goods Work in Process
Bal. 80,000 360,000 Bal. 20,000 (i) 320, (i) 320,000 (c) 150, 400,000 (e) 80, 40,000 100,000 * 350, 30,
*$330,000 – $80,000 = $250,000 direct labor and factory overhead. Factory overhead is 150% of direct labor, therefore, direct labor is $100,
5-10 Chapter 5
P5-3 (Concluded)
Materials Cost of Goods Sold
Bal. 15,000 (e) 80,000 360, (b) 100,000 12, 115,000 92, 23,
Factory Overhead Control Applied Factory Overhead
(d) 60,000 (c) 150, 12, 75, 147,
Accounts Payable Accrued Payroll
(f) 102,000 Bal. 7,000 (j) 172,000 Bal. 11, 100,000 175, 107,000 186, 5,000 14,
Accounts Receivable Sales
Bal. 45,000 (h) 480,000 (a) 500,000** (a) 500, 545, 65,
**Cost of goods sold is 72% of sales (100% – 28%).
(1) Materials purchased—$100, (2) Cost of goods sold—$360, (3) Finished goods ending inventory—$40, (4) Work in process ending inventory—$30, (5) Direct labor cost—$100, (6) Applied factory overhead—$150, (7) Over or underapplied factory overhead—$3,000 overapplied (8) Closed out to the cost of goods sold account
CGA-Canada (adapted). Reprint with permission.
Chapter 5 5-
P5-4 (Concluded)
(2) COLUMBUS COMPANY Income Statement For Month Ended October 31 Sales ................................................................... $144, Less sales returns and allowances ................. 1, Net sales ........................................................... $143, Less cost of goods sold ................................... 76, Gross profit ........................................................ $ 67, Less commercial expenses: Marketing expense ................................... $25, Depreciation—building............................. 30 Depreciation—office equipment.............. 16 $25, Administrative expense ........................... $19, Depreciation—building............................. 20 Depreciation—office equipment.............. 24 19,744 44, Income before income tax ................................ $ 22,
(3) Amount of over- or underapplied factory overhead: Actual factory overhead: Factory overhead paid ............................. $20, Indirect materials ...................................... 3, Depreciation—building............................. 150 Depreciation—machinery and equipment......................................... 800 Indirect labor ............................................. 4,400 $29, Applied factory overhead.................................. 27, Underapplied factory overhead........................ $ 1,
Chapter 5 5-
Balance Sheet December 31, 20B Assets
Current assets: Cash ........................................................... $19, Accounts receivable ................................. 10, Inventories: Finished goods ................................ $4, Work in process ............................... 1, Materials ........................................... 2,000 7, Prepaid expenses ..................................... 500 Total current assets......................... $36, Property, plant, and equipment (net) ............... 26, Total assets ........................................................ $62,
Liabilities
Current liabilities ............................................... $17,
Stockholders’ Equity
Common stock................................................... $30, Retained earnings.............................................. 15,
Total stockholders’ equity................................. 45, Total liabilities and stockholders’ equity......... $62,
5-14 Chapter 5
(1) and (2) JUAREZ INC. Job Order Cost Sheets To Post Beginning Inventory Data
(j) Completed and transferred Completed and trans- Still in to warehouse ferred to warehouse process
P5-6 (Concluded)
(2) The total cost of each job at the end of March:
(1) and (3) GENERAL LEDGER Accumulated Depreciation—
- Beginning inventory $ - Materials available for use.................................. $ Purchases............................................................. 336 (1) - Less ending inventory - Materials used...................................................... $