
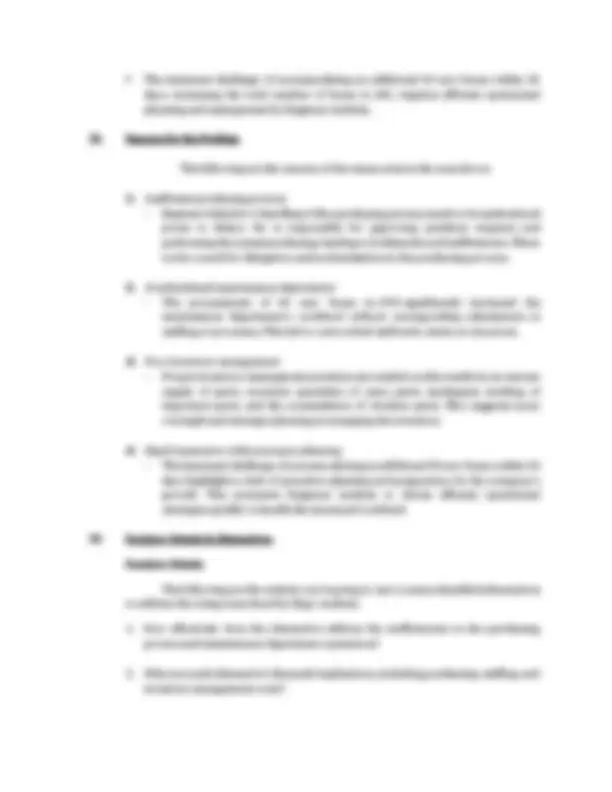
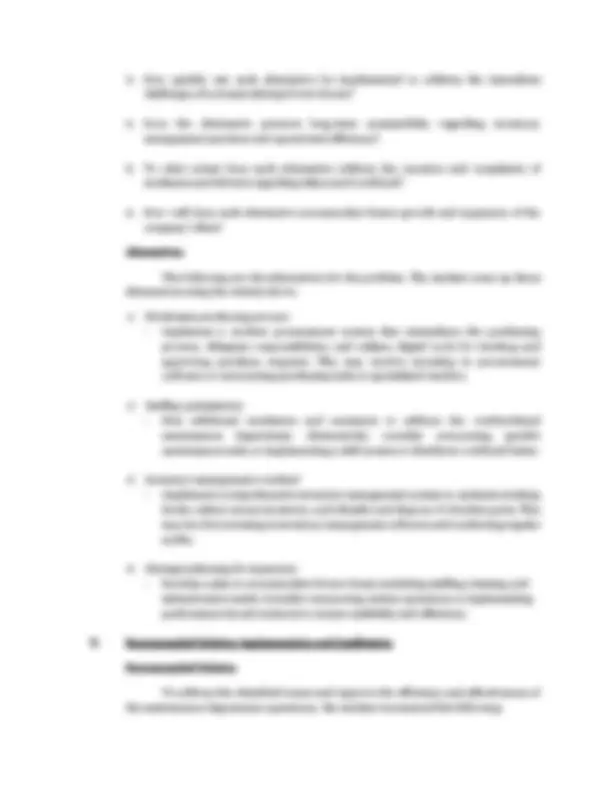
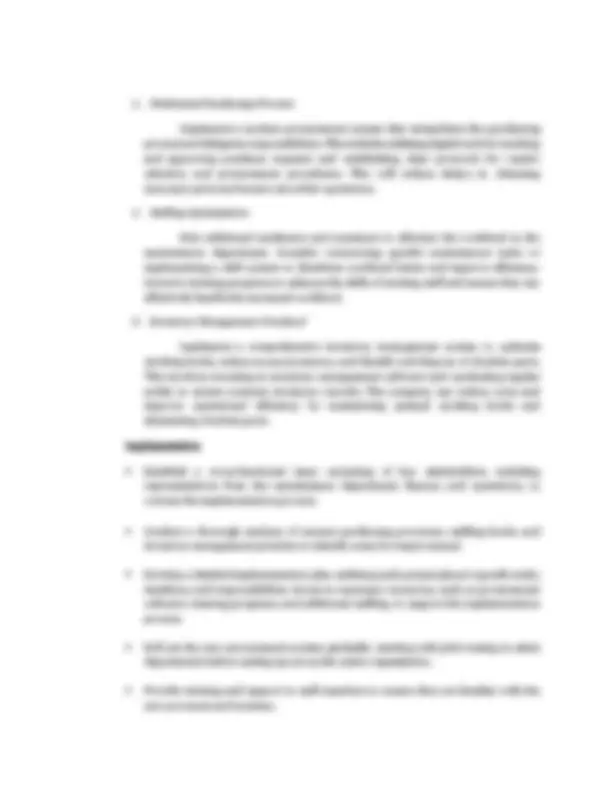
Study with the several resources on Docsity
Earn points by helping other students or get them with a premium plan
Prepare for your exams
Study with the several resources on Docsity
Earn points to download
Earn points by helping other students or get them with a premium plan
Community
Ask the community for help and clear up your study doubts
Discover the best universities in your country according to Docsity users
Free resources
Download our free guides on studying techniques, anxiety management strategies, and thesis advice from Docsity tutors
Declaration of the Issues The following are the identified issues in the case of MOTORBUS COMPANY: Que Sera Sera: The inefficient purchasing process for maintenance parts leads to delays and complaints from mechanics and drivers. Overburdened maintenance department due to increased workload from procuring 40 new buses in 1993. Lack of proper inventory management results in an uneven supply of parts, excessive quantities of some parts, inadequate stocking of essential parts, and accumulation of obsolete parts.
Typology: Assignments
1 / 6
This page cannot be seen from the preview
Don't miss anything!
CASE 3: MOTORBUS COMPANY: Que Sera Sera Engineer Hermogenes Ancheta as a Mechanical Engineering Graduate he then work in a Motorbus Company as Assistant Manager of Maintenance Department. By the year 1993 when he joined the Motorbus Company, he passed the Board Examination for Mechanical Engineering course. He then informed his former class mate from University of Santo Tomas by year 1995 as he promoted Assistant Manager for Maintenance. The former Manager of the Department Engineer Gaudencio Inductivo, joined the company since it started the operations in 1989. A total of ten buses began plying the Manila-Isabela route. A maintenance unit was put up the Manila in Sampaloc. Another unit serves the Ilagan, Isabela terminal. Each unit has a full-time mechanic and one assistant. When a company bus comes in for repair, the mechanic diagnoses the various automotive systems in the bus and later produces a list of parts needing replacement. The mechanic sends the list to Engineer Inductivo, who, in turn, forwards the same to the company accountant for approval of the purchase request. Often times, Engineer Inductivo performs the actual purchasing himself. Later, he sends the purchased items to the mechanic who made the request. The maintenance units were operating normally until 40 new buses were procured by the company in 1993. Since then, every maintenance was so busy that they threatened to quit their jobs unless additional mechanics and assistants were recruited. By the end of 1993, each unit has a personnel complement of 5 mechanics and 5 assistants. But with current developments, the old method of purchasing was not improved. Purchase request started to embroiled, the file endorsed becomes discreet. Mechanic and drivers began complaining to the VP for Operations about the delays in the delivery of needed parts. The VP (Vice-President) for Operations immediately sent a note to Engineer Inductivo ordering that the problem should be resolved immediately. Engineer Inductivo was hard pressed and he could not offer an immediate solution. The next day, Engineer Inductivo informed the VP for Operations that he is requesting for the approval of his application for retirement as he is already 62 years old. The VP forwarded the request to the President with an endorsement justifying the request. On the same day, the request for retirement was approved. The next day, Engineer Ancheta received his appointment papers promoting him to Manager. During his first appointment as a Manager the first thing Engineer Ancheta did was to inspect the storage room for parts. He found out that the room was full of uneven supply of parts. Some parts were of excessive quantities, while some important ones were inadequately stocked. A corner of the room contains a big volume of obsolete parts. At the end of the day, Engineer Ancheta was informed by the VP that the company will be fielding an additional 50 new buses within 30 days. This will mean that by next month about 100 buses will be servicing the various routes assigned to Motorbus Company. Engineer Ancheta is now mulling over how he will make the operations of his department as efficient and effective as possible.
Name: Charlene V. Sebron Date : April 12, 2024 Course: BSEnE 4B Instructor: Dr. Allen Rhay B. Bayantong CASE 3: MOTORBUS COMPANY: Que Sera Sera I. Executive Summary Engineer Hermogenes Ancheta, a Mechanical Engineering Graduate, rose through the ranks of a Motorbus Company to become the Manager of the Maintenance Department. Joining the company in 1993 , he witnessed its growth from ten buses servicing the Manila-Isabela route to procuring 40 new buses by the same year and an additional 50 buses by 1995. However, with this expansion came challenges in maintenance efficiency, highlighted by delays in parts procurement and complaints from mechanics and drivers. When faced with the impending retirement of the former Manager, Engineer Ancheta stepped up to the challenge, inheriting a department with unevenly stocked parts and the imminent task of managing a fleet of 100 buses. As Engineer Ancheta assumes his new role, his foremost concern is optimizing the department's operations to meet the demands of an expanding fleet. Upon discovering the disarray in the parts storage room, he recognizes the urgent need for an inventory management overhaul. With 100 buses soon to be in service, Engineer Ancheta is tasked with streamlining procurement processes, ensuring adequate stock levels, and minimizing waste. His strategic decisions in the coming days will shape the efficiency and effectiveness of the Maintenance Department, positioning the Motorbus Company for continued success in the competitive transportation industry. II. Declaration of the Issues The following are the identified issues in the case of MOTORBUS COMPANY: Que Sera Sera: The inefficient purchasing process for maintenance parts leads to delays and complaints from mechanics and drivers. Overburdened maintenance department due to increased workload from procuring 40 new buses in 1993. Lack of proper inventory management results in an uneven supply of parts, excessive quantities of some parts, inadequate stocking of essential parts, and accumulation of obsolete parts.
Implement a modern procurement system that streamlines the purchasing process and delegates responsibilities. This includes utilizing digital tools for tracking and approving purchase requests and establishing clear protocols for vendor selection and procurement procedures. This will reduce delays in obtaining necessary parts and ensure smoother operations.
Hire additional mechanics and assistants to alleviate the workload in the maintenance department. Consider outsourcing specific maintenance tasks or implementing a shift system to distribute workload better and improve efficiency. Invest in training programs to enhance the skills of existing staff and ensure they can effectively handle the increased workload.
Implement a comprehensive inventory management system to optimize stocking levels, reduce excess inventory, and identify and dispose of obsolete parts. This involves investing in inventory management software and conducting regular audits to ensure accurate inventory records. The company can reduce costs and improve operational efficiency by maintaining optimal stocking levels and eliminating obsolete parts. Implementation Establish a cross-functional team consisting of key stakeholders, including representatives from the maintenance department, finance, and operations, to oversee the implementation process. Conduct a thorough analysis of current purchasing processes, staffing levels, and inventory management practices to identify areas for improvement. Develop a detailed implementation plan outlining each project phase's specific tasks, timelines, and responsibilities. Invest in necessary resources, such as procurement software, training programs, and additional staffing, to support the implementation process. Roll out the new procurement system gradually, starting with pilot testing in select departments before scaling up across the entire organization. Provide training and support to staff members to ensure they are familiar with the new processes and systems.