
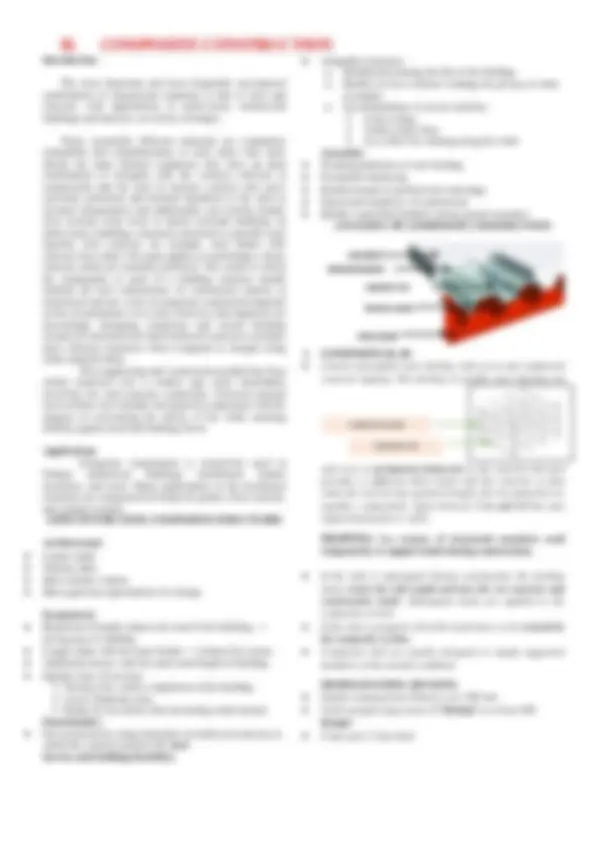
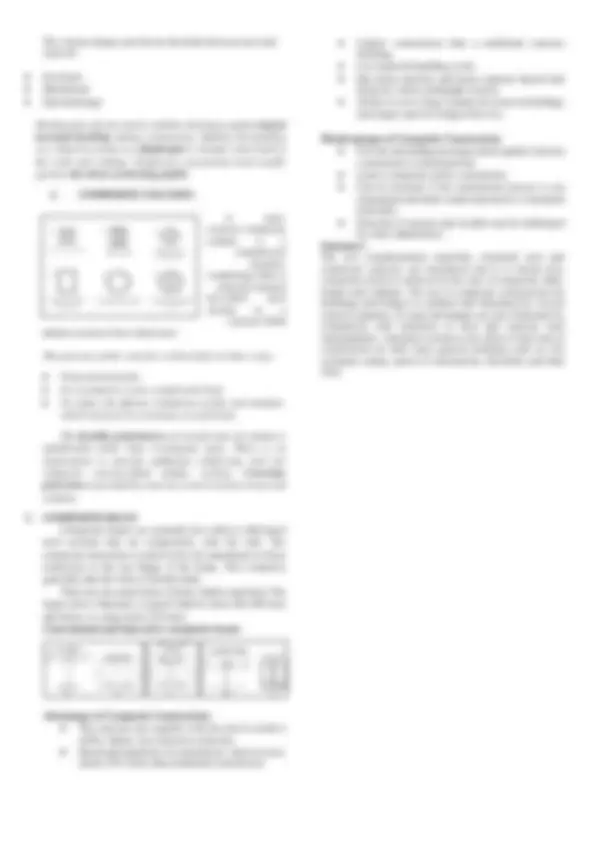
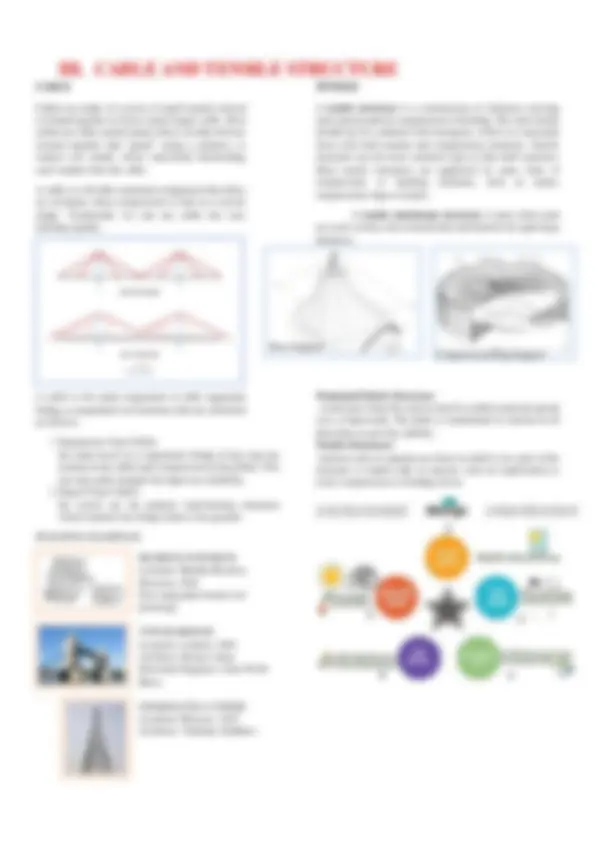
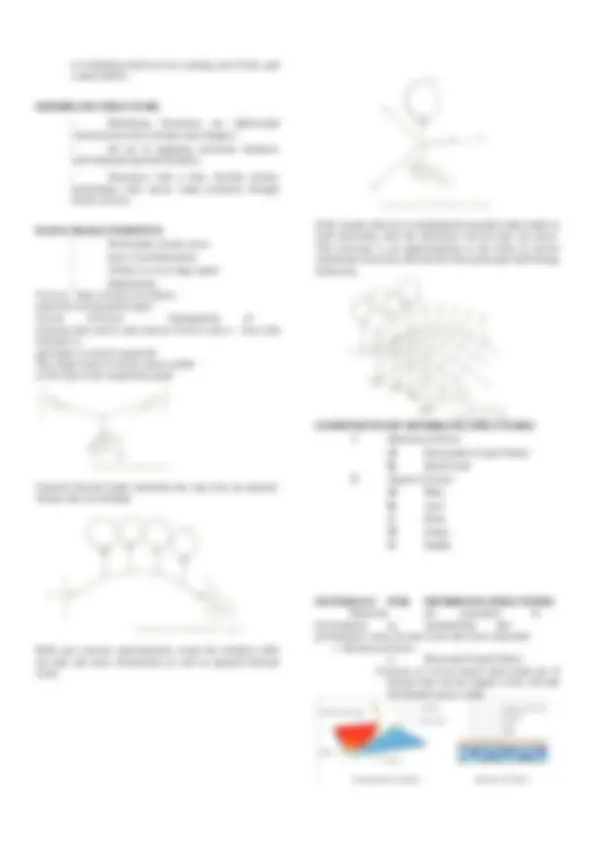
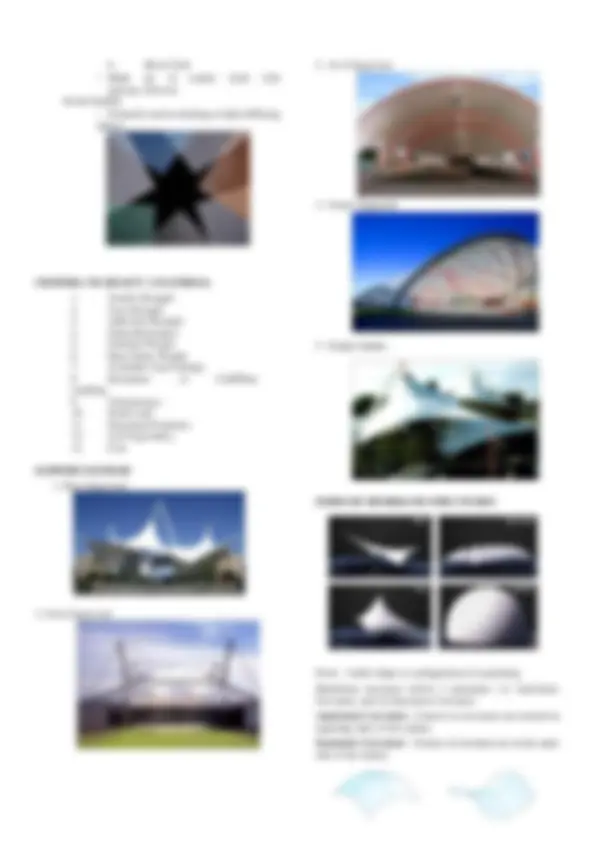
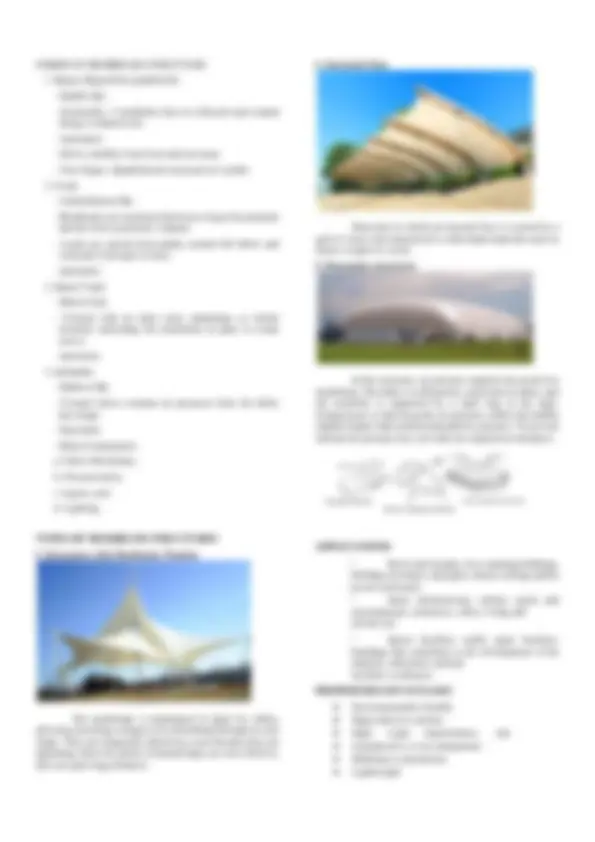
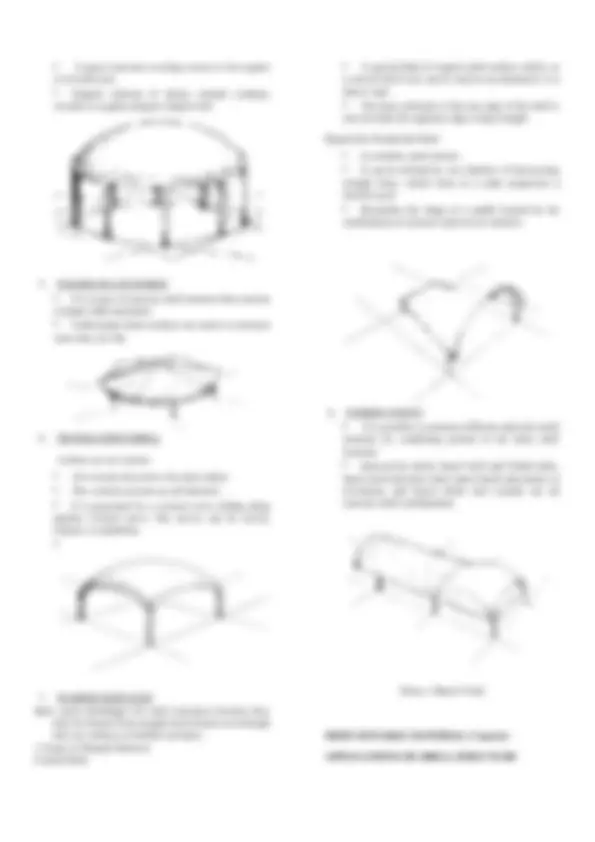
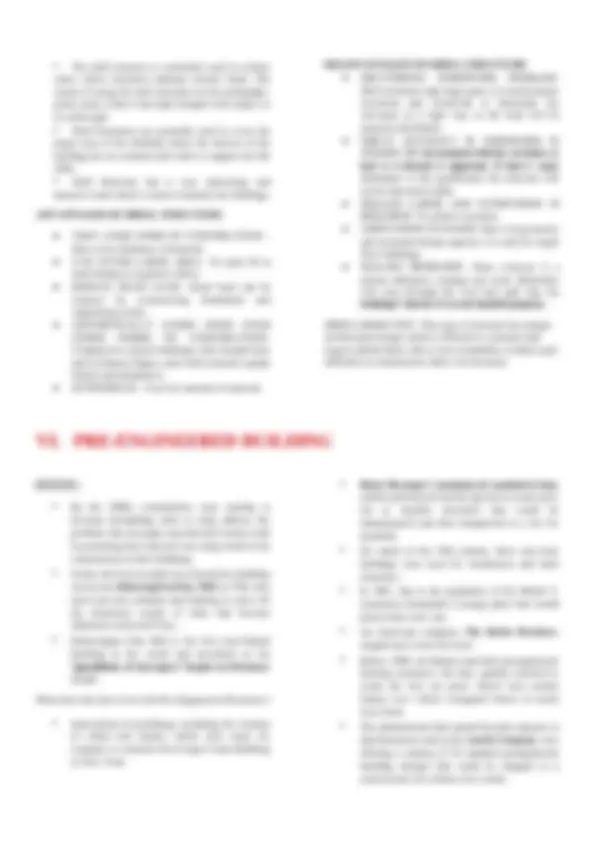
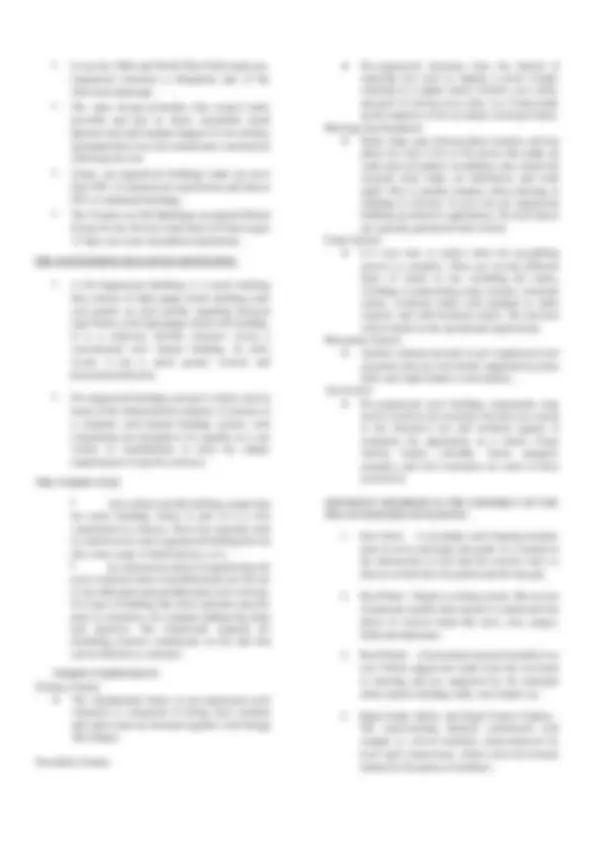
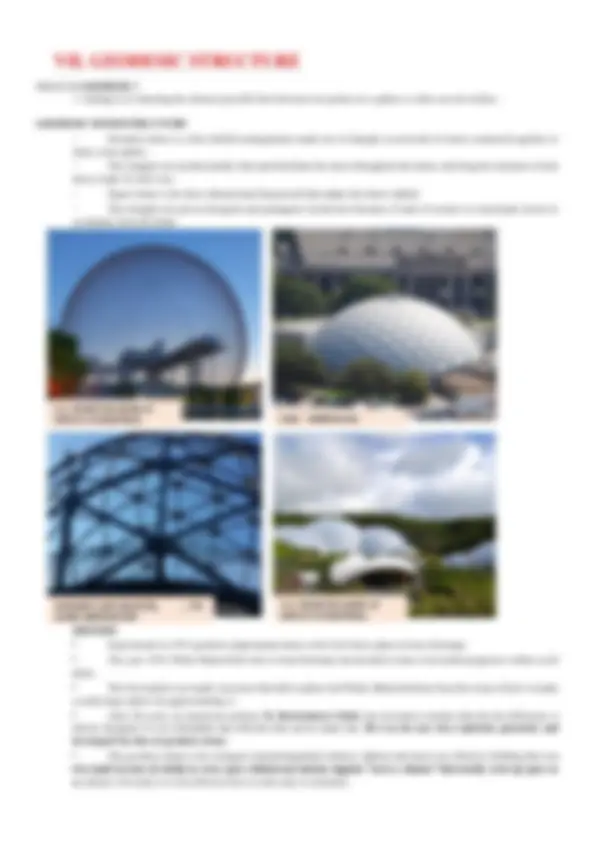
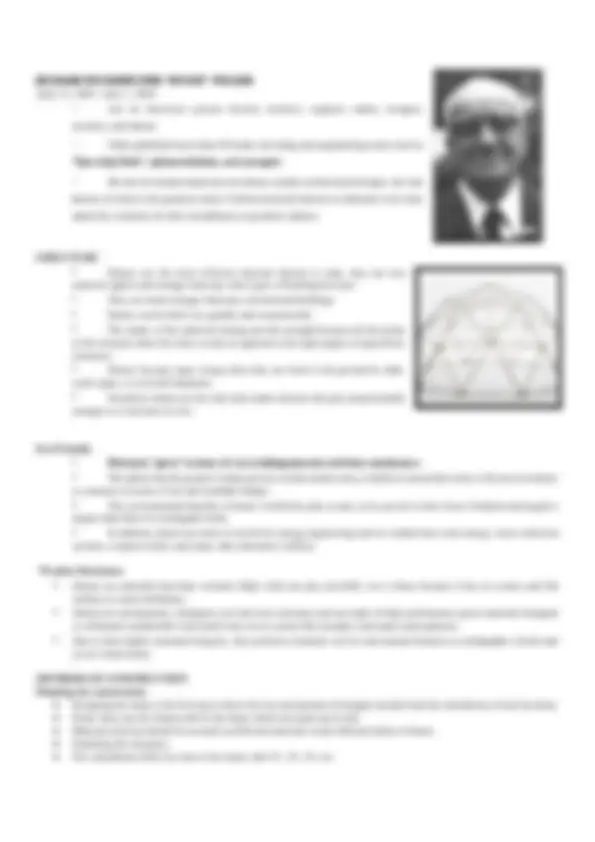
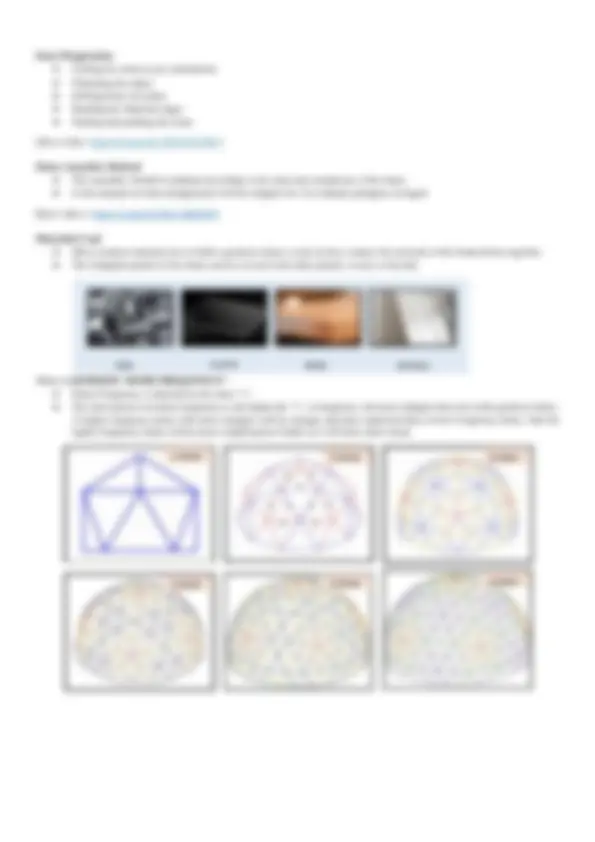
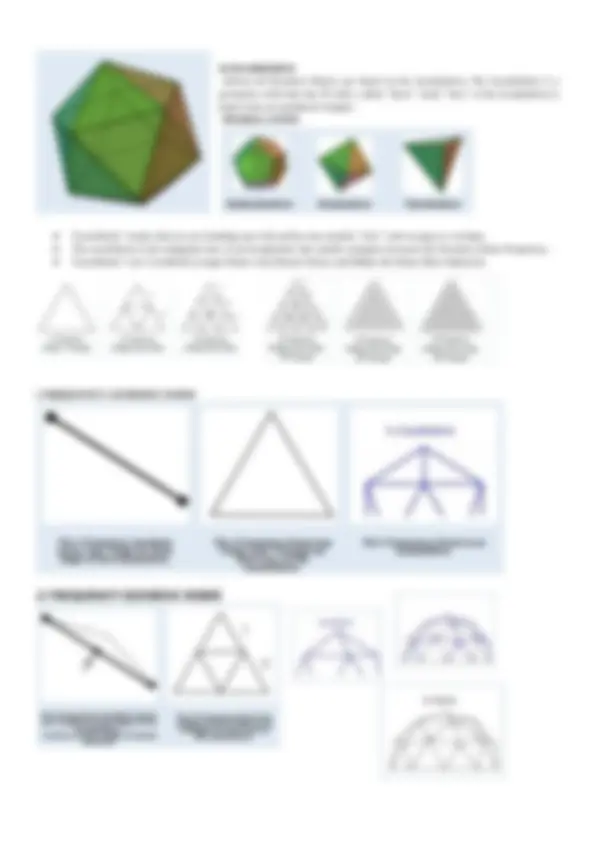
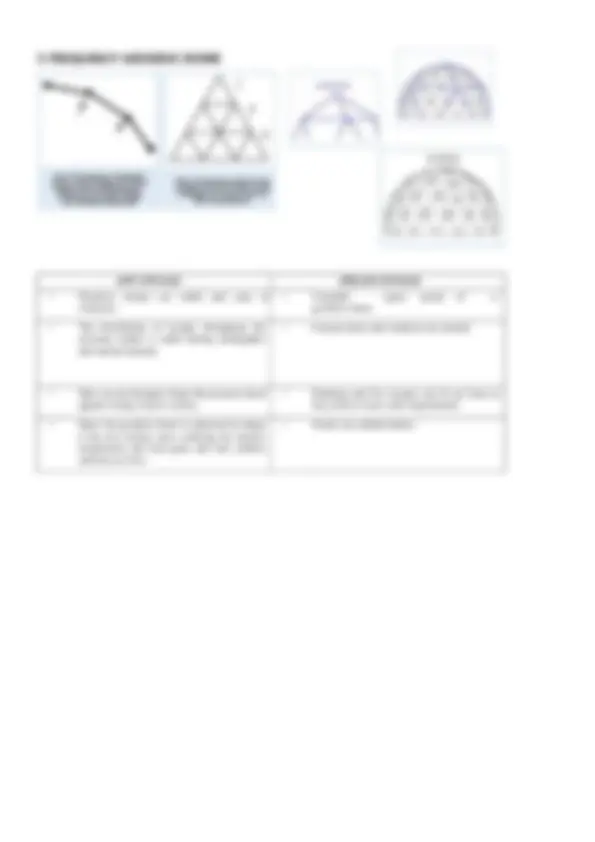
Study with the several resources on Docsity
Earn points by helping other students or get them with a premium plan
Prepare for your exams
Study with the several resources on Docsity
Earn points to download
Earn points by helping other students or get them with a premium plan
Community
Ask the community for help and clear up your study doubts
Discover the best universities in your country according to Docsity users
Free resources
Download our free guides on studying techniques, anxiety management strategies, and thesis advice from Docsity tutors
Building Technology 5- Alternative Building Construction Systems
Typology: Summaries
1 / 22
This page cannot be seen from the preview
Don't miss anything!
Pre-stressed concrete is a form of concrete where initial compression is given in the concrete before applying the external load so that stress from external loads is counteracted in the desired way during the service period. This initial compression is introduced by high-strength steel wire or alloys (called ‘tendons’) located in the concrete section. How does Prestressed concrete Work? In the real life, high tensile strength steel wires are inserted into the beam section and they are stretched and anchored, then released. Now the steel tendon wants to gain its original length and tensile stresses are transformed into compressive stress in the concrete. Now after loading there are two kinds of forces on the beam, Internal prestressing force External forces (Dead load, Live load, etc.) WHEN WAS PRE-STRESSED CONCRETE INTRODUCED? In 1929, Eugène Freyssinet (1879-1962) was a skilled craftsman and a prolific bridge builder, who invented prestressed concrete. WHO PATENTED PRE-STESSED CONCRETE? Eugène Freyssinet
Rock /soil Anchors: The use of prestressed anchors avoids the driving of the pile all the way to the rock which is available at very large depth.
The various shapes provide an interlock between steel and concrete:
Cables are made of a series of small strands twisted or bound together to form a much larger cable. Steel cables are either spiral strand, where circular rods are twisted together and "glued" using a polymer, or locked coil strand, where individual interlocking steel strands form the cable. A cable is a flexible structural component that offers no resistance when compressed or bent in a curved shape. Technically we can say cable has zero bending rigidity. A cable is the main component of cable supported bridge or suspended roof structures that are classified as follows:
A tensile structure is a construction of elements carrying only tension and no compression or bending. The term tensile should not be confused with tensegrity, which is a structural form with both tension and compression elements. Tensile structures are the most common type of thin-shell structure. Most tensile structures are supported by some form of compression or bending elements, such as masts, compression rings or beams. A tensile membrane structure is most often used as a roof, as they can economically and attractively span large distances. Tensioned Fabric Structure
been proven and built-in climates ranging from the frigid artic to the scorching desert heat.
Building with textiles is a tradition which goes back thousands of years. From yurts made out of animal skins through to the roman shade structures installed at the Colosseum. Biologically based woven cotton and canvas materials which were used to create the first fabric structures have been replaced by some of the world’s most technical man-made fabrics to achieve lasting permanent fabric architecture. Modern coated fabrics have similar aesthetic properties but offer significant performance advantages (1) Increase strength, (2) ease of cleaning, (3) Printability, (4) Solar Shading, (5) Acoustic characteristics. Modern coated fabrics will also resist the absorption of atmospheric moisture resulting in much longer lifespans and better dimensional stability Historically inspired by some of the first man-made shelters—such as the black tents first developed using camel leather by the nomads of the Sahara Desert, Saudi Arabia, and Iran, as well as the structures used by Native American tribes 1960s - german architect Frei Otto pushed the boundaries of membrane technology and opened people’s eyes to what can be created with tensile fabric Vladimir Shukhov
of a building which we are creating out of foils, and coated fabrics. MEMBRANE STRUCTURE
Materials are constantly in development as sustainability and performance issues become more and more important
1. Membrane/Fabric a. Structural Coated Fabric
Shell structures take huge span, so it needs proper execution and formwork to determine the curvature in a right way so the load will be properly distributed.
Building Length: Whenever possible maintain equal bay lengths throughout the building. When this is not possible make all interior bays equal and make the end bays equal but shorter than the interior bays. Building Width: Whenever possible make building width a multiple of 3m. This is because roof purlins are spaced at 1.5m on centers and 3m is equal to two purlin spacings one on each side of the ridge. TYPICAL PRE-ENGINEERED BUILDING ASSEMBLY:
( July 12, 1 895 – July 1, 1983)
Strut Preparation