
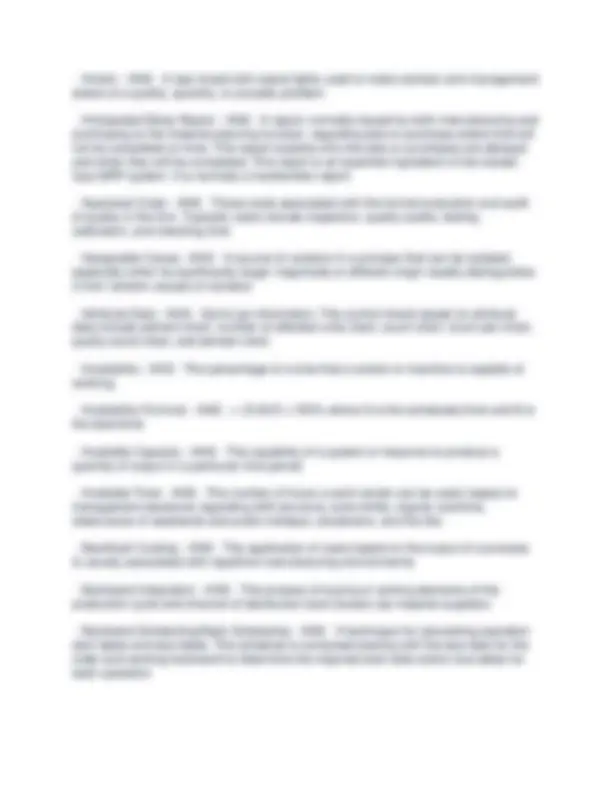
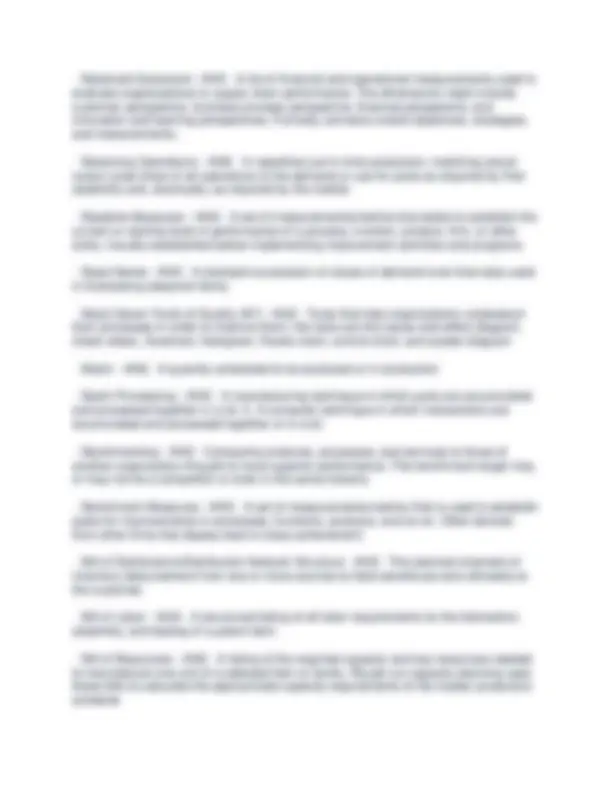
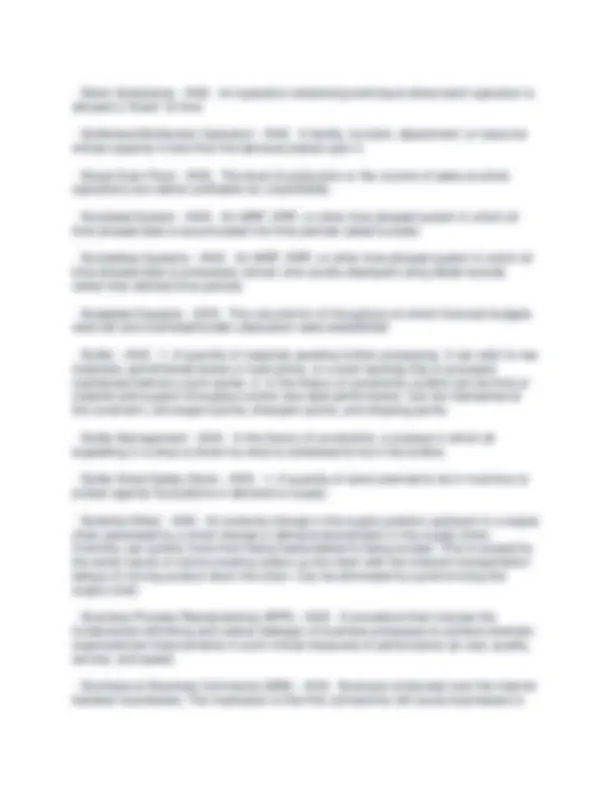
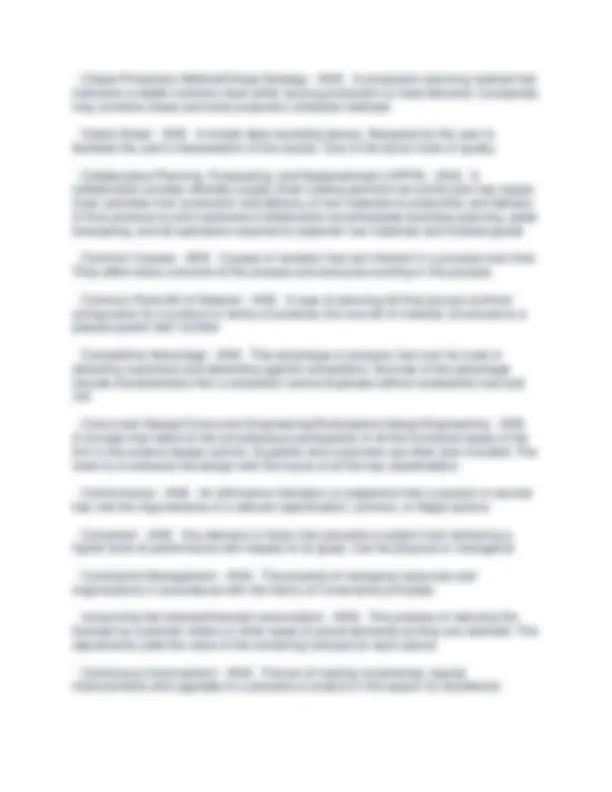
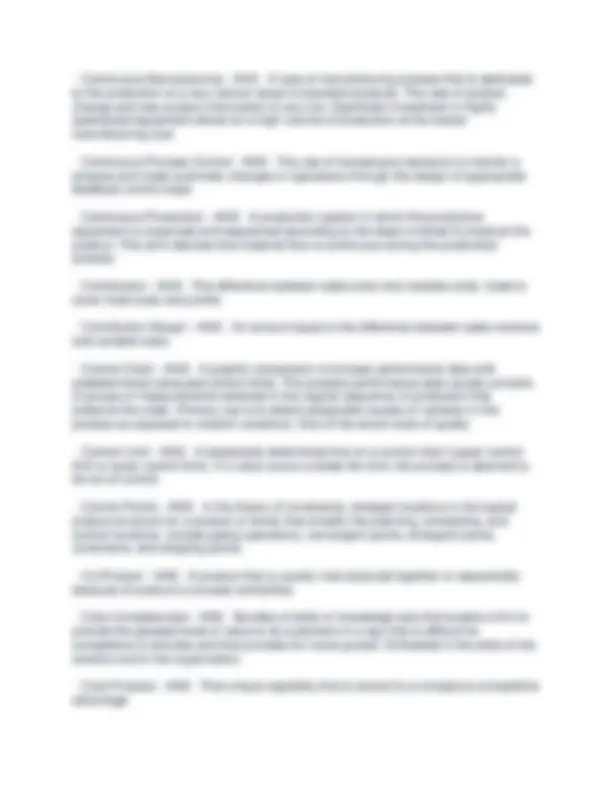
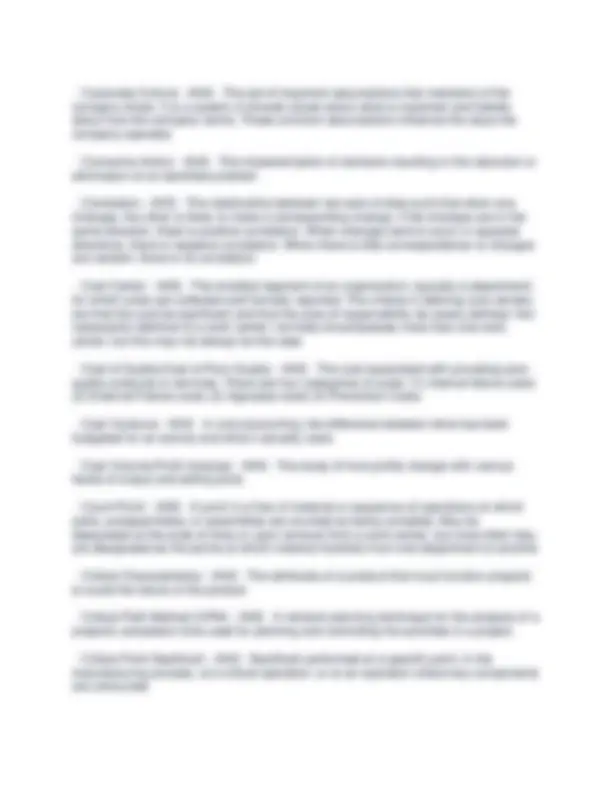
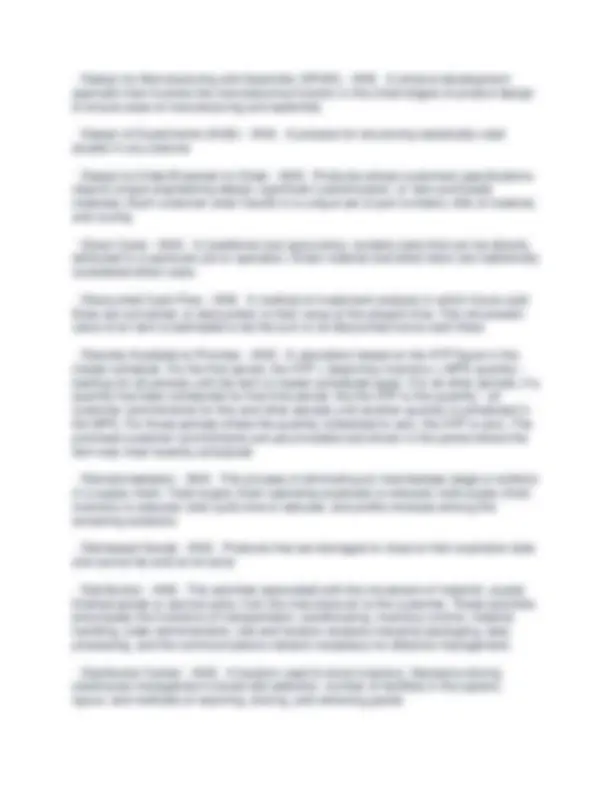
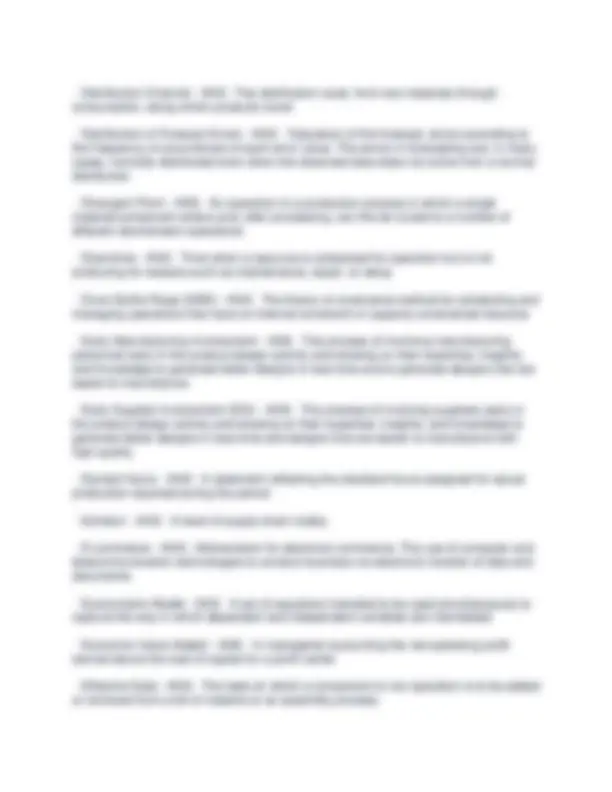
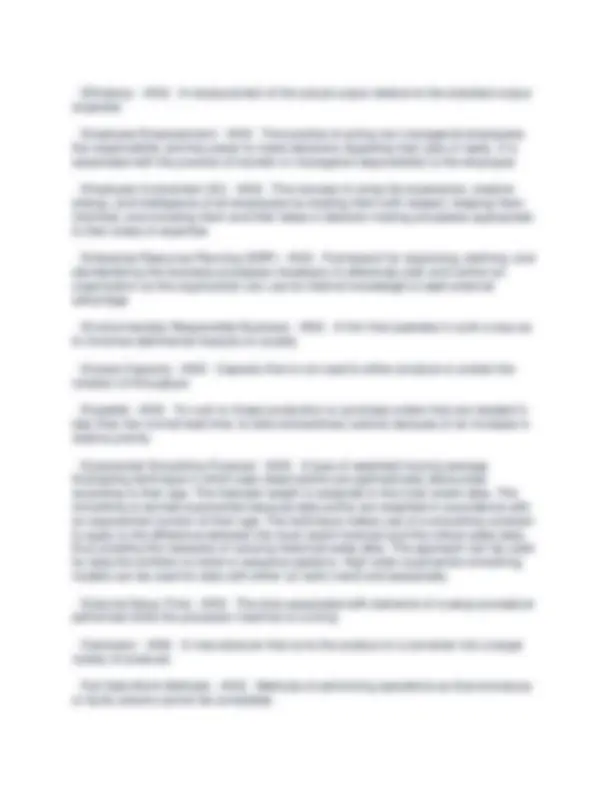
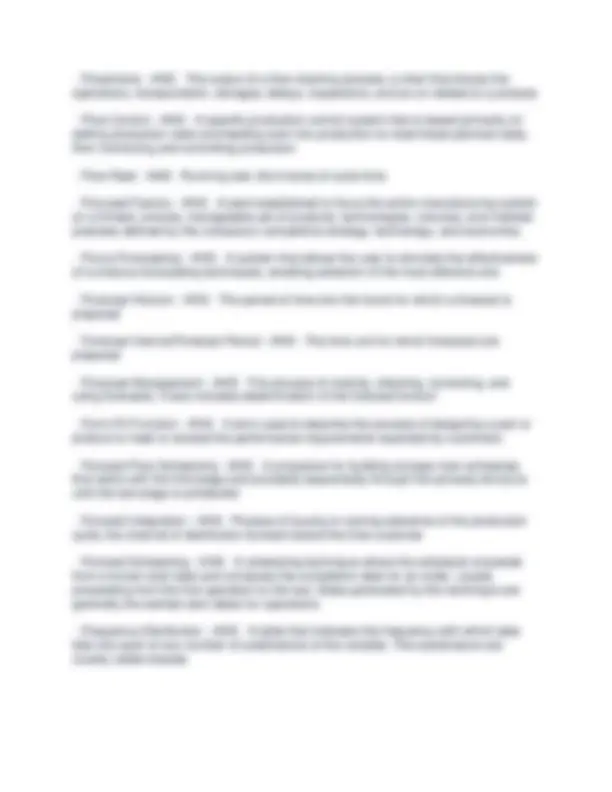
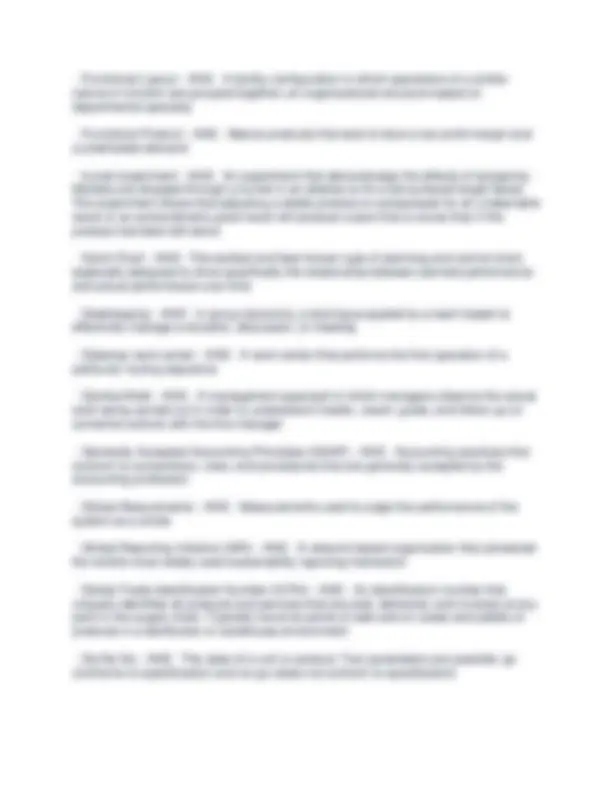
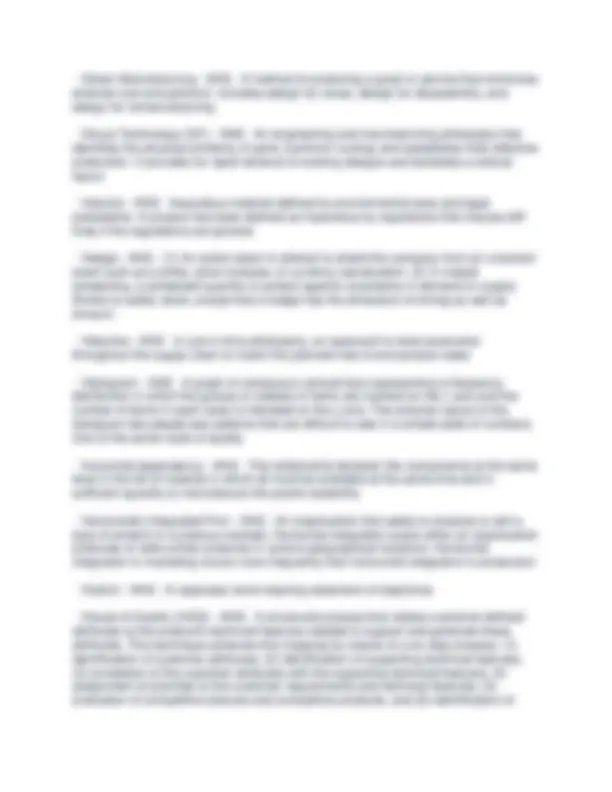
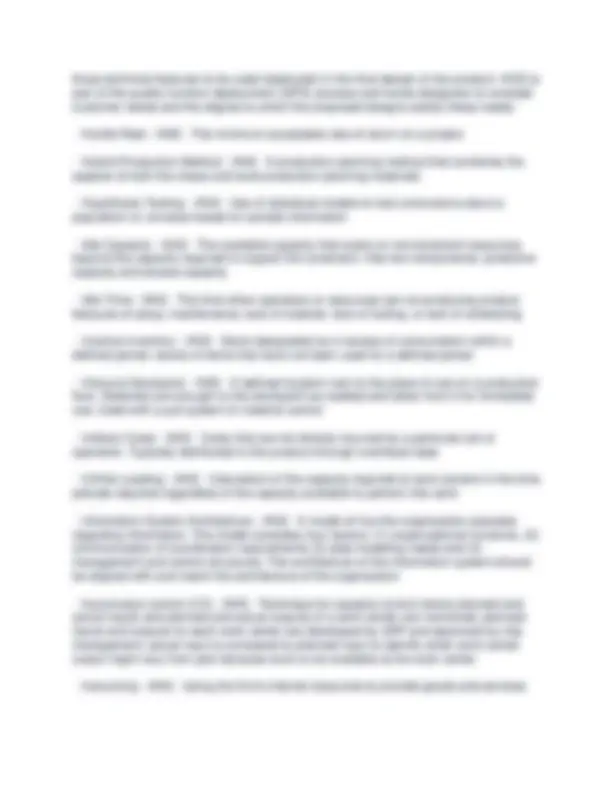
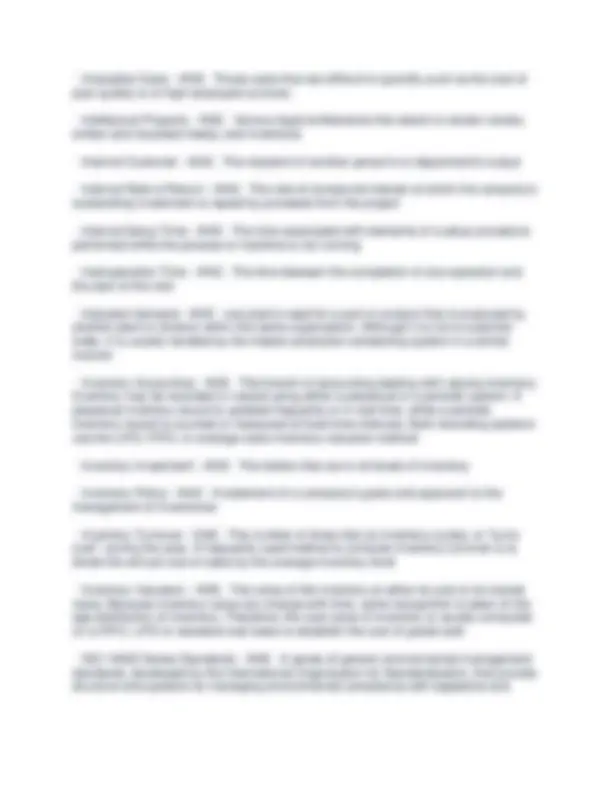
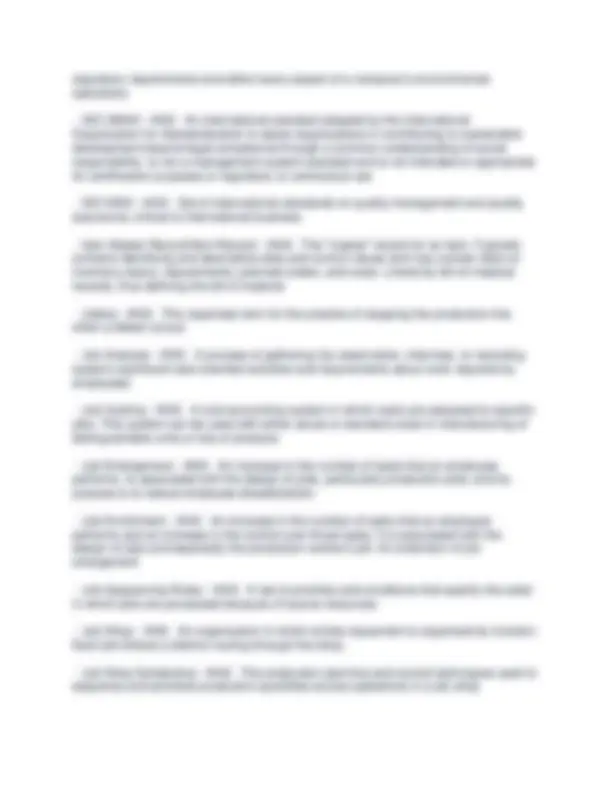
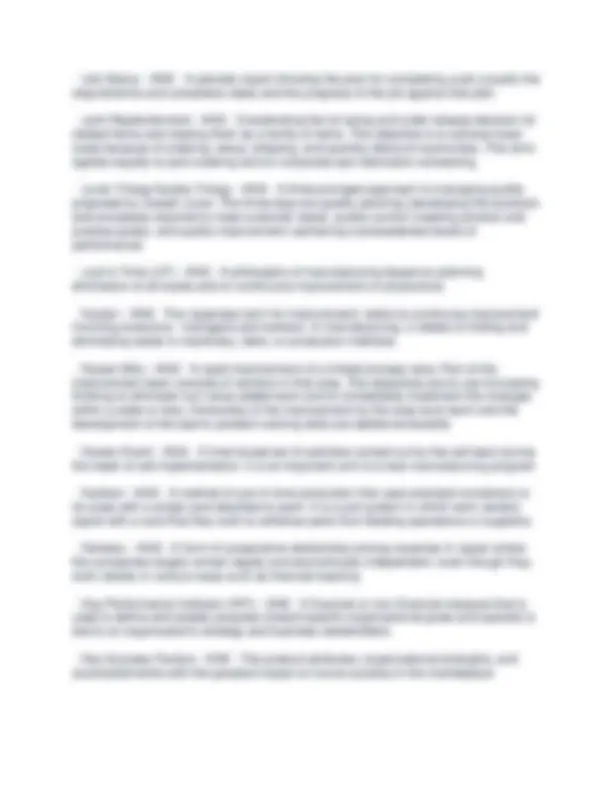
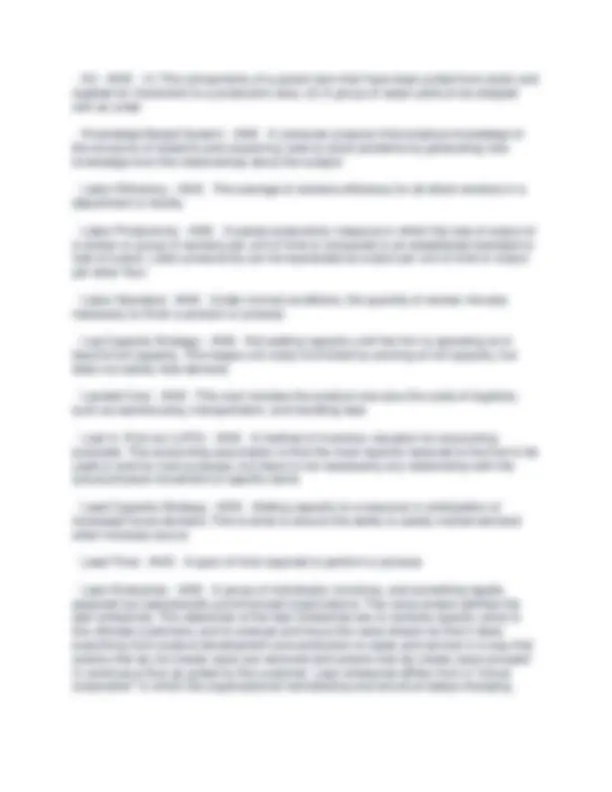
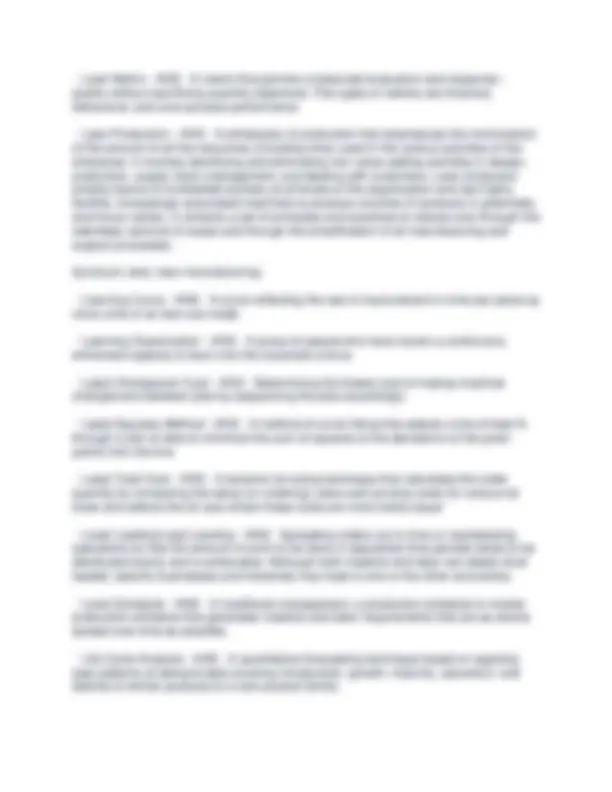
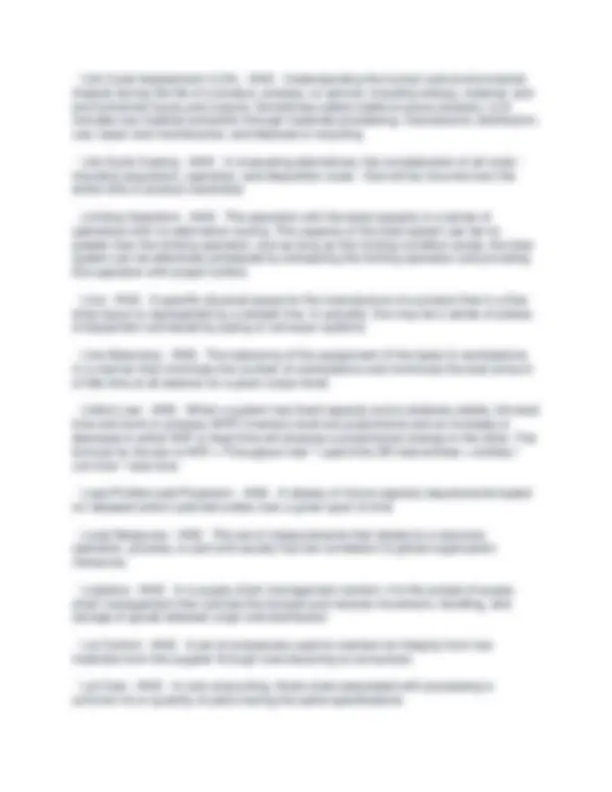
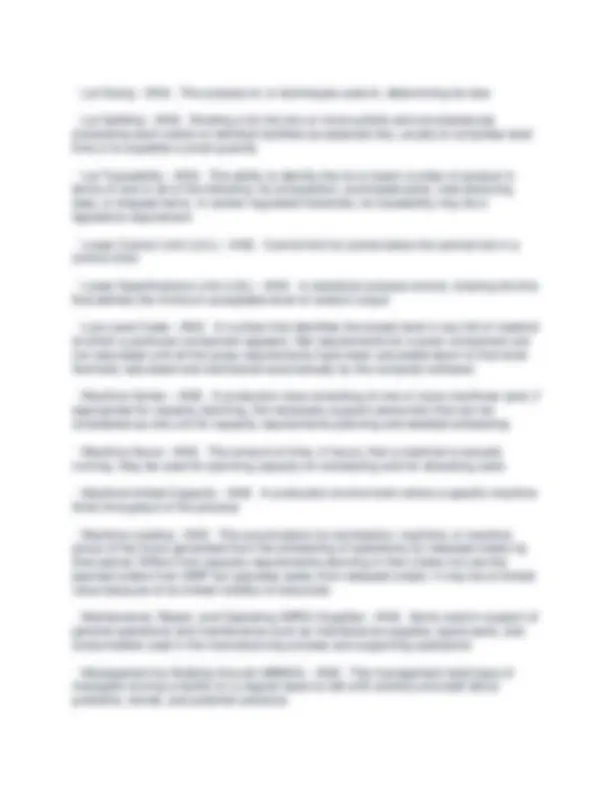
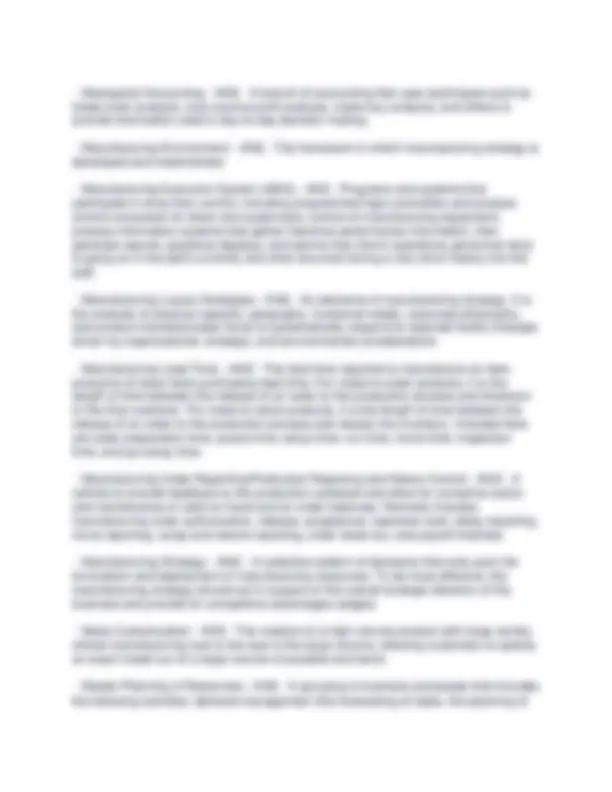
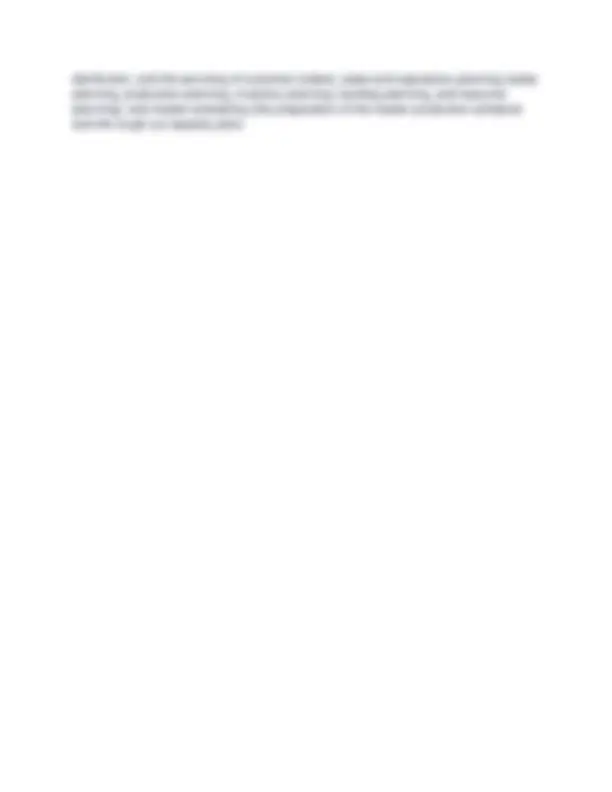
Study with the several resources on Docsity
Earn points by helping other students or get them with a premium plan
Prepare for your exams
Study with the several resources on Docsity
Earn points to download
Earn points by helping other students or get them with a premium plan
Community
Ask the community for help and clear up your study doubts
Discover the best universities in your country according to Docsity users
Free resources
Download our free guides on studying techniques, anxiety management strategies, and thesis advice from Docsity tutors
APICS CPIM Part 2 exam 2024-2025
Typology: Exams
1 / 30
This page cannot be seen from the preview
Don't miss anything!
14 Points - ANS W. Edwards Deming's 14 management practices to help companies increase their quality and productivity A3 Method - ANS A means of compactly describing a business process Abnormal Demand - ANS Demand in any period that is outside the limits established by management policy Absorption Costing - ANS An approach to inventory valuation in which variable costs and a portion of fixed costs are assigned to each unit production. Acceptable Quality Level (AQL) - ANS When a continuing series of lots is considered, a quality level that, for the purposes of sampling inspection, is the limit of a satisfactory process average Acceptance Sampling - ANS the process of sampling a portion of goods for inspection rather than examining the entire lot Action Message - ANS An output of a system that identifies the need for, and the type of action to be taken to correct, a current or potential problem. Activation - ANS Putting a resource to work Activity-Based Cost Accounting - ANS A cost accounting system that accumulates costs based on activities performed and then uses cost drivers to allocate these costs to products or other bases such as customers, markets, or projects. It attempts to allocate overhead costs on a more realistic basis than by using direct labor or machine hours Activity-Based Management (ABM) - ANS The use of activity-based costing information about cost pools and drivers, activity analysis, and business processes to identify business strategies; improve design, manufacturing, and distribution; and remove waste from operations Actual Costs - ANS The labor, material, and associated overhead costs that are charged against a job as it moves through the production process Actual Demand - ANS Composed of customer orders (and often allocation of items, ingredients or raw materials to production or distribution). Nets against or chosen over a time horizon. Adaptive Smoothing - ANS A form of exponential smoothing in which the smoothing constant is automatically adjusted as a function of forecast error measurement
Adjustable Capacity - ANS Capacity, such as labor or tools, that can be changed in the short term Advanced planning and scheduling (APS)/Advanced Planning Systems (APS) - ANS Techniques that deal with analysis and planning of logistics and manufacturing during short, intermediate, and long-term time periods. Aggregate Forecast - ANS An estimate of sales, often time-phrased, for a grouping of products or product families produced by a facility or firm. Stated in terms of units, dollars, or both, the aggregate forecast is used for sales and production planning purposes Aggregate Plan - ANS A plan that includes budgeted levels of finished goods, inventory, production backlogs, and changes in the workforce to support the production strategy. Aggregated information rather than product information is used Agility - ANS The ability to quickly plan, source, make, and deliver to adapt and respond to changes in the competitive environment. It is a SCOR performance attribute that includes product or service flexibility (speedy introduction of new products and services), mix flexibility (ability to quickly change products or services offered), volume flexibility (ability to service large order quantities), and delivery flexibility (ability to quickly change delivery dates to meet new requirements) Allocation - ANS The classification of resources or items quantities that have been assigned to specific orders but have not yet been released from the stockroom to production. It is an "uncashed" stockroom requisition. 2. A process used to distribute material in short supply Alpha Factor/Smoothing Constant - ANS In exponential smoothing, the weighting factor that is applied to the most recent demand, observation, or error Alternate Operation - ANS Replacement for a normal step in the manufacturing process Alternate Routing - ANS A routing that is usually less preferred than the primary routing but results in an identical item. Alternate routings may be maintained in the computer or off-line via manual methods, but the computer software must be able to accept alternate routings for specific jobs Analysis of Variance (ANOVA) - ANS A statistical analysis system that estimates what portion of variation in a dependent variable is caused by variation in one or more independent variables. It also produces a number used to infer whether any or all of the independent-dependent variable relationships have statistical significance
Balanced Scorecard - ANS A list of financial and operational measurements used to evaluate organizational or supply chain performance. The dimensions might include customer perspective, business process perspective, financial perspective, and innovation and learning perspectives. Formally connects overall objectives, strategies, and measurements. Balancing Operations - ANS In repetitive just-in-time production, matching actual output cycle times of all operations to the demand or use for parts as required by final assembly and, eventually, as required by the market Baseline Measures - ANS A set of measurements/metrics that seeks to establish the current or starting level of performance of a process, function, product, firm, or other entity. Usually established before implementing improvement activities and programs Base Series - ANS A standard succession of values of demand-over-time data used in forecasting seasonal items. Basic Seven Tools of Quality (B7) - ANS Tools that help organizations understand their processes in order to improve them. the tools are the cause-and-effect diagram, check sheet., flowchart, histogram, Pareto chart, control chart, and scatter diagram Batch - ANS A quantity scheduled to be produced or in production Batch Processing - ANS A manufacturing technique in which parts are accumulated and processed together in a lot. 2. A computer technique in which transactions are accumulated and processed together or in a lot Benchmarking - ANS Comparing products, processes, and services to those of another organization thought to have superior performance. The benchmark target may or may not be a competitor or even in the same industry Benchmark Measures - ANS A set of measurements/metrics that is used to establish goals for improvements in processes, functions, products, and so on. Often derived from other firms that display best-in-class achievement Bill of Distributions/Distribution Network Structure - ANS The planned channels of inventory disbursement from one or more sources to field warehouse and ultimately to the customer. Bill of Labor - ANS A structured listing of all labor requirements for the fabrication, assembly, and testing of a parent item. Bill of Resources - ANS A listing of the required capacity and key resources needed to manufacture one unit of a selected item or family. Rough-cut capacity planning uses these bills to calculate the approximate capacity requirements of the master production schedule
Block Scheduling - ANS An operation scheduling technique where each operation is allowed a "block" of time Bottleneck/Bottleneck Operation - ANS A facility, function, department, or resource whose capacity is less than the demand placed upon it Break-Even Point - ANS The level of production or the volume of sales at which operations are neither profitable nor unprofitable. Bucketed System - ANS An MRP, DRP, or other time-phased system in which all time-phased data is accumulated into time periods called buckets Bucketless Systems - ANS An MRP, DRP, or other time-phased system in which all time-phased data is processed, stored, and usually displayed using dated records rather than defined time periods Budgeted Capacity - ANS The volume/mix of throughput on which financial budgets were set and overhead/burden absorption rates established Buffer - ANS 1. A quantity of materials awaiting further processing. It can refer to raw materials, semifinished stores or hold points, or a work backlog that is purposely maintained behind a work center. 2. In the theory of constraints, buffers can be time or material and support throughput and/or due date performance. Can be maintained at the constraint, convergent points, divergent points, and shipping points Buffer Management - ANS In the theory of constraints, a process in which all expediting in a shop is driven by what is scheduled to be in the buffers Buffer Stock/Safety Stock - ANS 1. A quantity of stock planned to be in inventory to protect against fluctuations in demand or supply. Bullwhip Effect - ANS An extreme change in the supply position upstream in a supply chain generated by a small change in demand downstream in the supply chain. Inventory can quickly move from being backordered to being excess. This is caused by the serial nature of communicating orders up the chain with the inherent transportation delays of moving product down the chain. Can be eliminated by synchronizing the supply chain Business Process Reengineering (BPR) - ANS A procedure that involves the fundamental rethinking and radical redesign of business processes to achieve dramatic organizational improvements in such critical measures of performance as cost, quality, service, and speed. Business-to-Business Commerce (B2B) - ANS Business conducted over the internet between businesses. The implication is that this connectivity will cause businesses to
Capacity Utilization - ANS Goods produced, or customers served, divided by total output capacity Cash conversion Cycle - ANS 1. In retailing, the length of time between the sale of products and the cash payments for a company's resources. 2. In manufacturing, the length of time from the purchase of raw materials to the collection of accounts receivable from customers for the sale of products or services Cash-to-Cash Cycle Time - ANS An indicator of how efficiently a company manages its assets to improve cash flow. Cash-to-Cash Cycle Time Equation - ANS Inventory days + accounts receivable days - accounts payable days Cause-and-Effect Diagram/Ishikawa Diagram - ANS A tool for analyzing process dispersion. Illustrates the main causes and subcauses leading to an effect Cell - ANS A manufacturing or service unit consisting of a number of workstations and the materials transport mechanisms and storage buffers that interconnect them Cellular Manufacturing - ANS A manufacturing process that produces families of parts within a single line or cell of machines controlled by operators who work only within the line or cell Central Point Scheduling - ANS A variant of scheduling that employs both forward and backward scheduling, starting from the scheduled start date of a particular operation Certificate of Compliance - ANS A supplier's certification that the supplies or services in question meet specified requirements Certification Audits - ANS Audits occurring within registration processes Certified Supplier - ANS A status awarded to a supplier that consistently meets predetermined quality, cost, delivery, financial, and count objectives Changeover/Setup - ANS The work required to change a specific machine, resource, work center, or line from making the last good piece of item A to making the first good piece of item B Changeover Costs/Setup Costs - ANS Costs such as scrap costs, calibration costs, downtime costs, and lost sales associated with preparing the resource for the next product
Chase Production Method/Chase Strategy - ANS A production planning method that maintains a stable inventory level while varying production to meet demand. Companies may combine chase and level production schedule methods Check Sheet - ANS A simple data-recording device. Designed by the user to facilitate the user's interpretation of the results. One of the seven tools of quality. Collaborative Planning, Forecasting, and Replenishment (CPFR) - ANS A collaboration process whereby supply chain trading partners can jointly plan key supply chain activities from production and delivery of raw materials to production and delivery of final products to end customers.Collaboration encompasses business planning, sales forecasting, and all operations required to replenish raw materials and finished goods Common Causes - ANS Causes of variation that are inherent in a process over time. They affect every outcome of the process and everyone working in the process Common Parts Bill of Material - ANS A type of planning bill that groups common components for a product or family of products into one bill of material, structured to a pseudo-parent item number Competitive Advantage - ANS The advantage a company has over its rivals in attracting customers and defending against competitors. Sources of the advantage include characteristics that a competitor cannot duplicate without substantial cost and risk Concurrent Design/Concurrent Engineering/Participative Design/Engineering - ANS A concept that refers to the simultaneous participation of all the functional areas of the firm in the product design activity. Suppliers and customers are often also included. The intent is to enhance the design with the inputs of all the key stakeholders. Conformance - ANS An affirmative indication or judgement that a product or service has met the requirements of a relevant specification, contract, or illegal actions Constraint - ANS Any element or factor that prevents a system from achieving a higher level of performance with respect to its goals. Can be physical or managerial Constraints Management - ANS The practice of managing resources and organizations in accordance with the theory of Constraints principles consuming the forecast/forecast consumption - ANS The process of reducing the forecast by customer orders or other types of actual demands as they are received. The adjustments yield the value of the remaining forecast for each period Continuous Improvement - ANS The act of making incremental, regular improvements and upgrades to a process or product in the search for excellence
Corporate Culture - ANS The set of important assumptions that members of the company share. It is a system of shared values about what is important and beliefs about how the company works. These common assumptions influence the ways the company operates Corrective Action - ANS The implementation of solutions resulting in the reduction or elimination of an identified problem Correlation - ANS The relationship between two sets of data such that when one changes, the other is likely to make a corresponding change. if the changes are in the same direction, there is positive correlation. When changes tend to occur in opposite directions, there is negative correlation. When there is little correspondence or changes are random, there is no correlation Cost Center - ANS The smallest segment of an organization, typically a department, for which costs are collected and formally reported. The criteria in defining cost centers are that the cost be significant and that the area of responsibility be clearly defined. Not necessarily identical to a work center; normally encompasses more than one work center, but this may not always be the case Cost of Quality/Cost of Poor Quality - ANS The cost associated with providing poor- quality products or services. There are four categories of costs: (1) internal failure costs (2) External Failure costs (3) Appraisal costs (4) Prevention Costs Cost Variance - ANS In cost accounting, the difference between what has been budgeted for an activity and what it actually costs Cost-Volume-Profit Analysis - ANS The study of how profits change with various levels of output and selling price Count Point - ANS A point in a flow of material or sequence of operations at which parts, subassemblies, or assemblies are counted as being complete. May be designated at the ends of lines or upon removal from a work center, but most often they are designated as the points at which material transfers from one department to another Critical Characteristics - ANS The attributes of a product that must function properly to avoid the failure of the product Critical Path Method (CPM) - ANS A network planning technique for the analysis of a project's completion time used for planning and controlling the activities in a project. Critical Point Backflush - ANS Backflush performed at a specific point, in the manufacturing process, at a critical operation, or at an operation where key components are consumed
Critical Ratio - ANS A dispatching rule that calculates a priority index number by dividing the time to due date remaining by the expected elapsed time to finish the job Critical Ratio Equation - ANS = Time Remaining/work remaining Critical-To-Quality Characteristics (CTQs) - ANS The important and measurable traits of a product or process whose performance targets must be met to satisfy the customer. They adjust improvement efforts to meet consumer requirements Cumulative Available-to-Promise - ANS A calculation based on the ATP figure in the master schedule. Current Ratio - ANS Current assets divided by current liabilites Curve Fitting - ANS An approach to forecasting based on a straight line, polynomial, or other curve that describes some historical time series data Customer Relationship Management (CRM) - ANS A marketing philosophy based on putting the customer first. Involves the collection and analysis of information designed for sales and marketing decision support to understand and support existing and potential customer needs. Customer Service Level/Customer Service Ratio - ANS A measure of delivery performance of finished goods or other cargo, usually expressed as a percentage. Customer-Supplier Partnership - ANS A long-term relationship between a buyer and a supplier characterized by teamwork and mutual confidence. Decision Matrix - ANS A matrix used by teams to evaluate problems or possible solutions Decision Support System (DSS) - ANS A computer system designed to assist managers in selecting and evaluating courses of action by providing a logical analysis of the relevant factors Decomposition - ANS A method of forecasting where time series data is separated into up t three components - trend, seasonal, and cyclical - where trend includes the general horizontal upward of downward movement over time Decoupling - ANS Creating independence between supply and use of material. Commonly denotes allocating inventory between operations so that fluctuations in the production rate of the supplying operation do not constrain the production or use rates of the next operation Dedicated Capacity - ANS A work center that is designated to produce a single item or a limited number of similar items. Equipment that is dedicated may be special
Design for Manufacturing and Assembly (DFMA) - ANS A product development approach that involves the manufacturing function in the initial stages of product design to ensure ease of manufacturing and assembly Design of Experiments (DOE) - ANS A process for structuring statistically valid studies in any science Design-to-Order/Engineer-to-Order - ANS Products whose customers specifications require unique engineering design, significant customization, or new purchased materials. Each customer order results in a unique set of part numbers, bills of material, and routing Direct Costs - ANS In traditional cost accounting, variable costs that can be directly attributed to a particular job or operation. Direct material and direct labor are traditionally considered direct costs Discounted Cash Flow - ANS A method of investment analysis in which future cash flows are converted, or discounted, to their value at the present time. The net present value of an item is estimated to be the sum or all discounted future cash flows Discrete Available-to-Promise - ANS A calculation based on the ATP figure in the master schedule. For the first period, the ATP = beginning inventory + MPS quantity - backlog for all periods until the item is master scheduled again. For all other periods, if a quantity has been scheduled for that time period, the the ATP is this quantity - all customer commitments for this and other periods until another quantity is scheduled in the MPS. For those periods where the quantity scheduled is zero, the ATP is zero. The promised customer commitments are accumulated and shown in the period where the item was most recently scheduled Disintermediation - ANS The process of eliminating an intermediate stage or echelon in a supply chain. Total supply chain operating expenses is reduced, total supply chain inventory is reduced, total cycle time is reduced, and profits increase among the remaining echelons Distressed Goods - ANS Products that are damaged or close to their expiration date and cannot be sold at full price Distribution - ANS The activities associated with the movement of material, usually finished goods or service parts, from the manufacturer to the customer. These activities encompass the functions of transportation, warehousing, inventory control, material handling, order administration, site and location analysis industrial packaging, data processing, and the communications network necessary for effective management. Distribution Center - ANS A location used to store inventory. Decisions driving warehouse management include site selection, number of facilities in the system, layout, and methods of receiving, storing, and retrieving goods
Distribution Channel - ANS The distribution route, from raw materials through consumption, along which products travel Distribution of Forecast Errors - ANS Tabulation of the forecast, errors according to the frequency of occurrences of each error value. The errors in forecasting are, in many cases, normally distributed even when the observed data does not come from a normal distribution Divergent Point - ANS An operation in a production process in which a single material/component enters and, after processing, can the be routed to a number of different downstream operations Downtime - ANS Time when a resource is scheduled for operation but is not producing for reasons such as maintenance, repair, or setup Drum-Buffer-Rope (DBR) - ANS The theory of constraints method for scheduling and managing operations that have an internal constraint or capacity-constrained resource Early Manufacturing Involvement - ANS The process of involving manufacturing personnel early in the product design activity and drawing on their expertise, insights, and knowledge to generate better designs in less time and to generate designs that are easier to manufacture. Early Supplier Involvement (ESI) - ANS The process of involving suppliers early in the product design activity and drawing on their expertise, insights, and knowledge to generate better designs in less time and designs that are easier to manufacture with high quality Earned Hours - ANS A statement reflecting the standard hours assigned for actual production reported during the period Echelon - ANS A level of supply chain nodes. E-commerce - ANS Abbreviation for electronic commerce. The use of computer and telecommunication technologies to conduct business via electronic transfer of data and documents Econometric Model - ANS A set of equations intended to be used simultaneously to capture the way in which dependent and independent variables are interrelated Economic Value Added - ANS In managerial accounting the net operating profit earned above the cost of capital for a profit center Effective Date - ANS The date on which a component or ran operation is to be added or removed from a bill of material or an assembly process.
Failure Mode Effects Analysis (FMEA) - ANS A procedure in which each potential failure mode in every sub-item of an item is analyzed to determine its effect on other sub-items and on the required function of the item Feature - ANS A distinctive characteristic of a good or service. The characteristic is provided by an option, accessory, or attachment Feedback - ANS The flow of information back into the control system so that actual performance can be compared with planned performance Feeder Workstations - ANS An area of manufacture whose products feed a subsequent work area Fill Rate/Customer Service Ratio - ANS A measure of delivery performance of finished goods or other cargo, usually expressed as a percentage. In a make-to-stock company, this percentage usually represents the numbers of items or dollars that were shipped on schedule for a specific time period, compared to the total that were supposed to be shipped in that time period Final Assembly Schedule (FAS) - ANS A schedule of end items to finish the product for specific customers' orders in a make-to-order or assemble-to-order environment. It is also referred to as the finishing schedule because it may involve operations other than the final assembly; also, it may not involve assembly Finishing Lead Time - ANS The time that is necessary to finish manufacturing a good after receipt of a customer order. (2) The time allowed for completing the good based on the final assembly schedule Finite Forward Scheduling - ANS An equipment scheduling technique that builds a schedule by proceeding sequentially from the initial period to the final period while observing capacity limits. Finite Loading/Finite Scheduling - ANS Assigning no more work to a work center than the work center can be expected to execute in a given time period First-Article Inspection - ANS A quality check on the first component run after a new setup has been completed First In, First Out (FIFO) - ANS A method of inventory valuation for accounting purposes. The accounting assumption is that the oldest inventory (first in) is the first to be used (first out), but there is no necessary relationship with the actual physical movement of specific items
First-Order Smoothing - ANS A single exponential smoothing; a weighted moving average approach that is applied to forecasting problems where the data does not exhibit significant trend or seasonal patterns First Pass Yield - ANS The ratio of products that conform to specifications without rework or modification to total input Fishbone Analysis - ANS A technique to organize the elements of a problem or situation to aid in the determination of the causes of the problem or situation. The analysis relates the effect of the environment to the several possible sources of the problem Fitness For Use - ANS A term used to indicate that a good or service fits the customer's defined purpose for that good or service Five-Forces Model of Competition - ANS A methodology for analyzing competitive pressures in a market and assessing the strength and importance of each of those pressures Five Ss - ANS Five terms beginning with "S" used to create a workplace suitable for lean production: Sort, simplify, scrub, standardize, and sustain. Sort - ANS To separate needed items from unneeded ones and remove the latter Simplify - ANS To neatly arrange items for use Scrub - ANS To clean up the work area Standardize - ANS To sort, simplify, and scrub daily Sustain - ANS To always follow the first four Ss Fixed Cost - ANS An expenditure that does not vary with the production volume Flexibility - ANS The ability of the manufacturing system to respond quickly, in terms of range and time, to external or internal changes. Six different categories of flexibility can be considered: mix flexibility, design changeover flexibility, modification flexibility, volume flexibility, rerouting flexibility, and material flexibility. Flexible Workforce - ANS A workforce whose members are cross-trained and whose work rules permit assignment of individual workers to different tasks Floor Stocks - ANS Stocks of inexpensive production parts held in the factory, from which production workers can draw without requisitions
Functional Layout - ANS A facility configuration in which operations of a similar nature or function are grouped together; an organizational structure based on departmental specialty Functional Product - ANS Mature products that tend to have a low profit margin and a predictable demand funnel experiment - ANS An experiment that demonstrates the effects of tampering. Marbles are dropped through a funnel in an attempt to hit a flat-surfaced target below. The experiment shows that adjusting a stable process to compensate for an undesirable result or an extraordinarily good result will produce output that is worse than if the process had been left alone Gantt Chart - ANS The earliest and best-known type of planning and control chart, especially designed to show graphically the relationship between planned performance and actual performance over time Gatekeeping - ANS In group dynamics, a technique applied by a team leader to effectively manage a situation, discussion, or meeting Gateway work center - ANS A work center that performs the first operation of a particular routing sequence Gemba Walk - ANS A management approach in which managers observe the actual work being carried out in order to understand it better, coach, guide, and follow up on corrective actions with the line manager Generally Accepted Accounting Principles (GAAP) - ANS Accounting practices that conform to conventions, rules, and procedures that are generally accepted by the accounting profession Global Meaurements - ANS Measurements used to judge the performance of the system as a whole Global Reporting Initiative (GRI) - ANS A network-based organization that pioneered the world's most widely used sustainability reporting framework Global Trade Identification Number (GTIN) - ANS An identification number that uniquely identifies all products and services that are sold, delivered, and invoices at any point in the supply chain. Typically found at points of sale and on cases and pallets of products in a distribution or warehouse environment Go/No Go - ANS The state of a unit or product. Two parameters are possible: go (conforms to specification) and no-go (does not conform to specification)
Green Manufacturing - ANS A method of producing a good or service that minimizes external cost and pollution. Includes design for reuse, design for disassembly, and design for remanufacturing Group Technology (GT) - ANS An engineering and manufacturing philosophy that identifies the physical similarity of parts (common routing) and establishes their effective production. It provides for rapid retrieval of existing designs and facilitates a cellular layout Hazmat - ANS Hazardous material defined by environmental laws and legal precedents. A product has been defined as hazardous by regulations that impose stiff fines if the regulations are ignored Hedge - ANS (1) An action taken in attempt to shield the company from an uncertain event such as a strike, price increase, or currency reevaluation. (2) In master scheduling, a scheduled quantity to protect against uncertainty in demand or supply. Similar to safety stock, except that a hedge has the dimension of timing as well as amount. Heijunka - ANS In just-in-time philosophy, an approach to level production throughout the supply chain to match the planned rate of end product sales Histogram - ANS A graph of contiguous vertical bars representing a frequency distribution in which the groups or classes of items are marked on the x axis and the number of items in each class is indicated on the y axis. The pictorial nature of the histogram lets people see patterns that are difficult to see in a simple table of numbers. One of the seven tools of quality horizontal dependency - ANS The relationship between the components at the same level in the bill of material in which all must be available at the same time and in sufficient quantity to manufacture the parent assembly Horizontally Integrated Firm - ANS An organization that seeks to produce or sell a type of product in numerous markets. Horizontal integration exists when an organization produces or sells similar products in various geographical locations. Horizontal integration in marketing occurs more frequently than horizontal integration in production Hoshin - ANS A Japanese word meaning statement of objectives House of Quality (HOQ) - ANS A structured process that relates customer-defined attributes to the product's technical features needed to support and generate these attributes. This technique achieves this mapping by means of a six step process: (1) identification of customer attributes; (2) identification of supporting technical features; (3) correlation of the customer attributes with the supporting technical features; (4) assignment of priorities to the customer requirements and technical features; (5) evaluation of competitive stances and competitive products, and (6) identification of